For the first time in history, a pathway for ALD-enhanced materials to be rapidly developed and transitioned from lab-scale to commercial production is available for nearly any application.
Until recently, atomic level surface engineering on powders and porous materials has not been possible at high throughputs. Now a well-defined development pathway from R&D-scale (milligram to kilogram samples) to commercial-scale production (thousands of tons per year and beyond) is facilitating the power of sub-nano surface coatings and bulk material property control for nearly any application.
Atomic layer deposition (ALD) has been used to demonstrate surface property enhancement across hundreds of applications over the past sixty years. Commercial ALD processes exist for wafer technologies in the semiconductor industry that rely on costly ultra-high purity precursors. But innovative applications on three-dimensional and porous materials (i.e. higher surface area materials) had lagged in commercial development due to the perceived costs of ALD coatings requiring these expensive precursors. This perception delayed innovations around manufacturing and scaling particle ALD products. As such, the application of ALD on particles and porous structures has historically been relegated to lab-scale demonstrations, typically in academic environments. Forge Nano recognized the criticality of enabling ALD for commercial applications, and through rigorous design and engineering efforts developed and patented a method and apparatus for high-throughput (spatial) ALD for high surface area substrates. For the first time in history, a pathway for ALD-enhanced materials to be rapidly transitioned from lab-scale demonstration to commercial presentation is available for new product development.
Researchers around the globe have proven real advantages of ALD coatings on particles for markets including batteries, catalysts, barrier coatings, pigments, cosmetics, healthcare, and filtration. Atomic layer deposition enables changing surface properties without changing bulk characteristics, which facilitates “drop-in ready” solutions to overcome commercial material challenges. High fidelity surface engineering modifications using ALD can enhance properties and/or reduce the amount of modifying material required to achieve functional properties. New opportunities are emerging for talented researchers to develop and demonstrate commercially-viable materials at the lab scale; these technologies can rapidly be converted to commercial products by leveraging Forge Nano’s scaling experience and world leading ALD coating capabilities.
.jpg)
Atomic layer deposition is performed by sequentially dosing reactants and inert purge to build up material in a layer-by-layer process one atom layer per cycle.
Why should you care about particle ALD or surface engineering?
A: Mechanical and physical properties of any powder can be tuned for the optimal economic performance of an end-product by adjusting the surface properties of the base particle. Without changing the bulk properties, adjusting surface properties influences the performance of mixing, settling, stability, degradation, corrosion, and many other industrially relevant material handling steps in production. Adjusting these properties can result in significant process cost and time savings without bulk property change to the final product. Additionally, industrial powders can be protected from environmental damage without changing the bulk properties by adding sub-nano surfaces using ALD.
.jpg)
A wide range of surface properties can be enhanced or diminished without changing bulk properties using atomic layer deposition. Adjusting these properties can result in significant process cost and time savings.
Why should you Spend Your Time and Intelligence Building Your Own R&D System for Particle ALD?
A: You shouldn’t! Forge Nano offers a series of R&D systems for particle ALD and a world-class support team with the expertise to help you innovate new materials and scale your technology to commercial production levels. The Prometheus R&D tools come in an assortment of reactor volumes and process configuration options that are adjustable to meet your current needs quickly, yet adaptable enough to support your ongoing needs and ideas as they evolve. The systems are reliable for years of operation and designed with swappable componentry to expand future capabilities. Prometheus tools leverage the decades of experience that our team has in building and operating particle ALD systems so you can start cutting edge research immediately. The academic lite option is a cost-effective model for academic researchers looking to enter the particle ALD field or upgrade their current equipment. The robust full capability option allows complete versatility for feasibility testing up to small production capacity. Transition packages are also available to upgrade qualifying academic entry models to expand capabilities overtime.
Why Should a Particle ALD Tool be Used for Particles Instead of a Modified Wafer ALD Tool?
A: From a practical perspective, most wafer ALD tools are installed in clean room environments, which are incompatible with processing particles. Beyond this, since a properly functioning wafer ALD tool is designed to minimize particle generation and/or retention, the process equipment and software may not be backward compatible to facilitate the processing of powders. For example, there are typically orders of magnitude higher surface area to be coated in a given unit volume of powder than on a wafer, and precursor storage and delivery is just one of many aspects where incompatibilities have been identified.
Numerous process variables can influence the true commercial scalability of an ALD technology: deposition uniformity, thermal stability, temperature uniformity, consistency of precursor delivery, surface blocking, and full precursor utilization to name a few. A particle specific reactor incorporates the precursor flow and particle agitation needed to ensure uniform deposition temperatures and reliable gas-solid mixing. Forge Nano’s scale-up pathway translates the feasibility knowledge learned in a temporal ALD system (batch system) to our commercial production scale spatial ALD systems. Particle specific ALD R&D systems lower the scale-up risk and increase the value of your R&D-scale development work and avoid misleading results caused by non-uniform deposition.
Research and Development in Atomic Layer Deposition for Particles and Powders
Developing ALD processes requires careful attention to even trivial tasks, which is why we are offering our Prometheus R&D tools that eliminate the largest pain point we’ve heard from our customers: inconsistent results derived from poorly-adapted wafer ALD tools. This product line represents a reliable R&D tool, where conditions can be mapped to Forge Nano’s larger manufacturing tools with proven scalability. Process conditions and reactor control are critical to producing reliable and repeatable end materials. Analytical integration is a valuable tool to elucidate if the desired reactions are proceeding. Forge Nano has successfully navigated the development pathway from R&D to commercial production for several products. We now offer the ability for others to do the same with our Prometheus R&D Series tools. Control and safety are paramount in our systems, allowing researchers at any skill level to focus their analytical and innovation skills to develop new products rather than troubleshot reactor issues.
Capabilities of an R&D Series Particle ALD Tool
Systems range in price point from the academic-lite version to the full capability systems including: up to 8 precursor source delivery options, ozone precursor capability, air-free glovebox handling reactor, gas-solid mixing aid, and integrated mass spectrometer or any combination of these features. Air-free operations are valuable for specialty materials and deposition chemistries. Reactor production size range from milligram to kilogram batch size for in-house production scale-up or object coating capabilities.
Scale Up Process Using Experts in the Field
Material handling at scale, precursor delivery and stability, as well as safety of reactants and by-products are critical to successful commercialization. Facilitate your R&D technology success by affiliating your development with an engineering and production team capable of scaling your process design to meet market-based production goals. Together we elucidate new opportunities toward a manufacturable, viable and cost-effective market solution.
.png)
Forge Nano’s in-house ALD process capabilities facilitates the development pathway from R&D to commercial opportunity of sub-nano surface coatings.
Speed of Development for First to Publish, First to Patent, and First to Market
Utilizing the best tools and partnerships increases the pace of R&D for rapid evaluation of new chemistries and associated applications. System downtime and operational inefficiencies are costly; Prometheus Series tools have been designed for performance with long operating life and optimized for R&D success. Precursor quarantine maintains cleanliness of process lines while, specially designed valves minimize downtime during maintenance. Prescribed safe operating boundaries reduce risk while automated control operation and emergency stop logic improve safety. Customized recipe building enables faster innovation with inherent safety allowing for autonomous operation without human intervention. These benefits allow researchers to focus their valuable time on new material development and product characterization instead of building and troubleshooting a do-it-yourself lab-system.
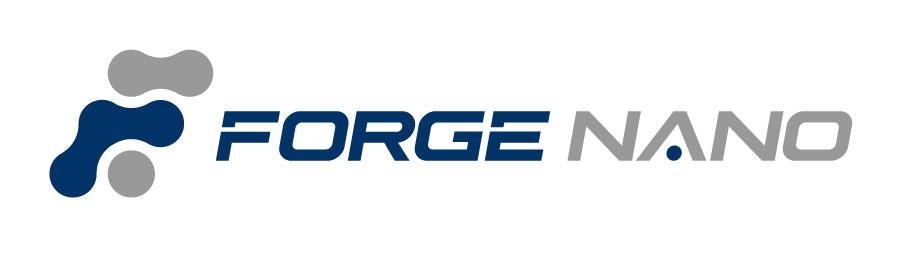
This information has been sourced, reviewed and adapted from materials provided by Forge Nano.
For more information on this source, please visit Forge Nano.