During the last five to ten years, there has been a dramatic increase in the number and range of rapid prototyping and rapid tooling techniques. Traditional tooling methods take up a significant amount of time in the manufacturing development process and, if the ‘hard’ financial aspects of launching a product are fully examined, the key issue is the lead time of the hard tooling in the pre-production process. In the plastics injection industry, tools are generally machined from a solid block of steel, while in the polyurethane (PU) moulding industry they are often cast in aluminium. In both cases there are now several alternatives to these processes on the market. Sprayforming One of the most promising methods to cut the lead times of tool production is a method known as sprayforming. Sprayforming works by spraying molten steel onto a reverse ceramic replica of the required part. Once a design for a part has been completed - invariably via CAD/CAM - a three dimensional model is taken and machined in modelling board. Then a ceramic cast is taken of the modelling board replica and pre-heated, prior to spraying with molten steel from metal arc spray guns. This creates a hard net shape shell of the working surface of the tool. The ceramic is removed and the tool shell readied for finishing and, where appropriate, assembly in a bolster block. Spraying During the spraying process the tool steel undergoes shear transformation to produce a mixture of martensite and lower bainite phases. These shear transformation products experience a net volume expansion of 4.2%, which counteracts the thermal shrinkage as the tool steel cools from its melting point to the process operating temperature, a range of 200-350°C. In this way, residual stresses in the tool steel shells are minimised and normal tolerances - to within ±0.127mm - are achieved. Under certain circumstances these tolerances are improved still further to ±0.065mm. 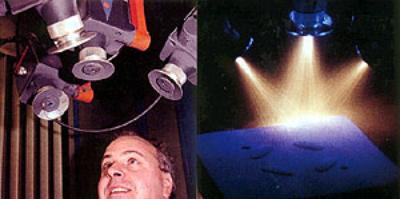 | Figure 1. The spray guns (left) and the sprayforming process in action (right) | Lead Times The lead time from receipt of the CAD file to production of the fully-hardened tool steel shells can be as little as ten working days. However, if a model or facsimile of the tool is available, this can be reduced to seven days. In addition, depending on the complexity of the tool, finishing, bolstering and packing can be finished in as little as two and a half weeks and completed at a competitive cost, compared to conventionally manufactured tools. Advantages of the Sprayforming Process The advantages of sprayforming technology are of most use to the manufacturing industries, from the automotive to the brown and white goods industries. The significant reduction in lead time which can be up to 75% - results in a product brought to market far more quickly than if conventional tooling methods were used, in turn giving a faster rate of return for investors. Size Limitations of Sprayforming Currently, the only limit to the sprayforming process is size. Novarc is currently developing the process in conjunction with Oxford University, and is increasing the thermal spray capacity of the Oxford cell from four to six SmartArc guns. The aim is to produce tools with a surface area exceeding 1m2. At this size, sprayformed tools are of particular interest to both the automotive and industrial sectors as the system can be used to manufacture full-sized body panels for cars and white goods. Sprayforming and the Polymers Industry However, sprayforming has yet to be used to its full extent in the polymer processing industry. Until now, the choices open to a company in this area, in terms of how it makes the tools that will be used in injection or PU moulding, have been extremely limited. Generally, injection moulding tools are machined from solid blocks of steel, with any heating or cooling channels ‘rifle bored’ into the tool after the machining process. However, as these can only be drilled in straight lines, the heating and cooling channels are at times very close to the tool working surface and at others far away. Moulds for Polyurethane
With polyurethane moulding, ‘soft’ aluminium tools are often used, with cooling channels cast into the aluminium shell of the tool. However, because of its softness, aluminium tools are easily damaged, either during the moulding process itself or through operators using abrasive cleaning techniques or knives to clean `flash lines'. Refurbishing tools and recurring flashlines adds to costs and loses production time. Sprayforming of Injection Moulding Tools Many of the answers to the challenges of creating polymer processing tools lie with sprayforming. For injection moulding tools, the spraying process can be interrupted to allow heating or cooling lines to be laid onto the surface of the sprayformed shell. This usually takes place after between four and six millimetres of steel have been sprayed. Either copper or stainless steel lines can be used, with connections left for water cooling or heating lines. Spraying is then continued until the appropriate tool thickness is reached. Cooling Channels and Ejectors Alternatively, these lines can be made using lead section, which is melted out after the sprayforming process to leave an integral channel. Obviously, it is essential that the cooling lines are strategically placed, in order not to interfere with mould ‘furniture’ such as ejectors. Using the above process, the heating or cooling channels can be placed at a constant offset to the tool working surface, giving ‘conformal’ cooling channels. Such heating and cooling lines can reduce mould cycle times by up to 30%. Hardness of Sprayformed Tools Sprayformed tools are particularly advantageous where the injection moulding of filled polymers is concerned. Conventional tools used to mould such polymers experience short lives because of the abrasive nature of these materials. However, with sprayforming, the sprayed steel is a multi-phase structure consisting of a transformed steel matrix containing a fine distribution of iron oxides. This microstructure has unusually high abrasion resistance and ceramic-coated or ceramic-tipped cutting tools are essential to machine the sprayed steel. Economics of Sprayformed Moulds Sprayforming also carries a number of benefits for polyurethane. Polyurethane tools are often used in multiple sets of up to 40, ideal for a technology such as sprayforming that uses a model of the tool as a master to create the ceramic refractory patterns. The cost of the master is shared across a number of tools, making the amortised cost per tool negligible. Instead of a soft aluminium tool, a hard tool is produced, with a high abrasion resistance that allows for operator ‘wear and tear’ and will last the lifetime of the product cycle without needing expensive refurbishment. Advantages of Using Sprayformed Moulds Another advantage to the use of spray-forming for polurethane moulding tools is that the steel shells produced are thin and relatively light in comparison to cast aluminium tools. This not only makes the unit cost lower but also enables the units to be managed by hand. Sprayforming also allows for the units to be textured easily, which is a bonus in tools where this is needed, such as those for use in creating automotive interiors, where a mock leather appearance may be desired, for example, on a dashboard moulding. Alternatives to Sprayforming However, sprayforming, is not the only new process around. During the past ten years there has been a dramatic increase in the number and range of rapid prototyping techniques, all of which promise to cut lead times. Processes such as stereo lithography, selective laser sintering, laminated object manufacture and three dimensional printing are techniques that have enabled designers and manufacturers to better visualise prototypes and to improve the ergonomic, tactile and functional aspects of a product. Press Stamping However, Novarc believes that sprayforming will come to play a vital role, not only in the production of polymer processing tools, but also in a wider context. If press stamping tools are used as an example, current processes can produce tools with a footprint of 850mm x 850mm. As the company, in conjunction with its colleagues at Oxford University and Ford, continues to develop the process, the size capability of the process will grow. Commercial Acceptance of Sprayformed Moulds Presently the automotive sector - both OEM and tier 1 - has embraced sprayforming technology. Production and development tools are being commissioned for a variety of end uses including metal stamping, plastic injection and other moulding processes. In the UK, tooling and pressings specialist Airflow Streamlines has used the technology to produce a stamping tool for the production of body-in-white panels. Under trial press conditions, the tool has shown a high degree of wear resistance, due in the main to the robust physical properties of the steel shell generated by the process. Summary Time-to-market is one of the key drivers for industry, especially as many industries move towards an increasingly globalised, one-market type structure. With toolmaking taking up a large element of the pre-production process, sprayforming and the discipline of rapid tooling will come to play an increasingly important role. The commercial advantage of quicker lead times is not an ‘added value’. It is fundamental to the future success of any manufacturing organisation. |