PCD Grades and Characteristics
Grade |
Applications |
Characteristics |
Microstructure |
CMX850 |
Perfect where extreme chip resistance is required, such as in milling and rough cutting of aluminium alloys, and for machining titanium and composites.
|
Sub-micron grain size. The ultra-fine grain structure of CMX850 is ideal for applications that require mirror finishes, thanks to its strong edge sharpness/retention.
|
.jpg) |
CTX002 |
Best for use in thread cutting tools and profile routers. CTX002 can additionally be applied in wear part applications.
|
Average grain size of 2 µm with ease of processing facilitated by increased cobalt. CTX002 is ideal where excessive processing is required, as in complex tools.
|
.jpg) |
CTB004 |
Ideal for aluminium alloy cutting which requires a high surface finish, as well as higher durability.
|
4 µm average grain size. The 4-micron fine grain structure of CTB004 provides an extra facet in delivering the perfect balance between durability against chips and abrasions and optimum tool performance.
|
.jpg) |
CTB010 |
Where roughing and finishing are completed with a single tool, CTB010 is the ideal grade. Best for use with low-to-medium content aluminium alloys.
|
Average grain size of 10 µm. The workhorse PCD grade, CTB010 is widely applicable for tasks requiring a key balance of toughness and durability.
|
.jpg) |
CTH025 |
Ideal in tasks involving the machining of metal matrix composites (MMC), high silicon aluminium alloys, ceramics and tungsten carbide.
|
With a 25 µm average grain size, CTH025 provides maximum wear resistance in harsh machining conditions.
|
.jpg) |
CTM302 |
Application areas CTM302 is designed for include bi-metal applications, MMC, high silicon aluminium alloys and high-strength cast irons, thanks to its strong thermal stability and high abrasion resistance.
|
As a multi-modal PCD, the combination of 2 µm to 30 µm grain sizes in CTM302 provide it with high edge strength and quality, as well as strong wear resistance.
|
.jpg) |
Choosing the Right PCD Grades
PCD Grades for Wider Usage
Thanks to progress in product development capabilities and developments with synthesis techniques, CMX850 and CTM302 possess the properties to overcome many common obstacles in tool performance. CMX850 balances performance with processability, CTM302 is the last word in maximum abrasion resistance, and CTB004 strikes the optimum balance of tool performance and abrasion resistance.
.jpg)
.jpg)
Materials and Machining
The grades offered by Element Six PCD ensure that behavior in application and processing characteristics are perfectly matched to meet the requirements of the grinding operation.
.jpg)
Aero-Dianamics™ - PCD Round Tool Blanks
Grades and Characteristics
Grade |
Applications |
Grain Sizes |
Characteristics |
A3MH HELIX |
Milling |
Fine |
- Lower tool forces and improved chip evacuation thanks to helical geometry
- Reduced adhesion and heat build-up due to high thermal conductivity and low coefficient of friction
- Clean-cut fibers due to the sharpness of PCD edges
|
.jpg) |
A2DS CHEVRON |
Drilling |
Coarse |
- 10x increase in tool lifespan against carbide drills
- Available in half round disks formats
- Custom-cut EDM segments available
|
.jpg) |
A3DP PLANAR |
Drilling |
Fine |
- Limitless flexibility in drill point geometry
- Tenfold increase in tool life against tungsten carbide drills
- Lower tool forces possible through large rake angles
|
.jpg) |
Setting Tool Design Free
Tool designers are now being provided with the opportunity to break into new territory with the Aero-Dianamics™ range of round tool blanks, which offers the chance to create completely new PCD tool geometries, with:
- Multiple flutes
- Freedom of design in flute profiles
- Almost infinite flute angles and orientations
Aero-DianamicsTM – Transforming Composite Tooling
.jpg)
Traditional coated tungsten carbide tools are being replaced by these revolutionary composite tooling solutions, which facilitate the fabrication of composite components.
Revolutionary AD-M3 Blanks for Milling Tools
The milling range offered by Aero-Dianamics™ provides a vast increase in productivity as compared to coated tungsten carbide tools:
- Machining speeds of between 3-12 x faster
- Reduced cutting forces
- Better tool evacuation
Unique AD-D3 Blanks for Compound Drill Geometries
Compared to coated tungsten carbide tools, the Aero-Dianamics™ drilling range offers a significant productivity increase:
- Significant increase of durability against coated carbide drills
- Tool life increased by 10 x in drilling CFRP
- 2 x speed of drilling CFRP/ Al
- Consistent performance over tool life
- Ameliorated work piece finish
Improving Productivity and Attaining a Superior Edge Quality
Tungsten Carbide:
Hole surface quality on CFRP test piece
.jpg)
AD-M3 Planar:
Provides faster drilling and a consistently clean finish
.jpg)
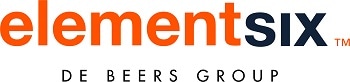
This information has been sourced, reviewed and adapted from materials provided by Element Six.
For more information on this source, please visit Element Six.