Reid vapor pressure (RVP) and true vapor pressure (TVP) of crude oil should be tested when dealing with both its production and storage.
The vapor pressure reflects the level of performance of the crude oil at the time of handling. It also underlines conditions under which bubbles may probably form and shows where pressure build-ups of escaping light ends are likely to happen. The measurement of vapor pressure eliminates costly damage to vessels or pipelines that transport crude oil. In addition, it provides guidance on how transportation facilities should be constructed to withstand a worst-case situation.
Prior to transporting crude to a distribution point, pipeline operators usually determine bubble point and TVP. Wellhead crude gas needs to be removed to fulfill tanker, pipeline, and storage specifications. Surplus amounts of gas can be either flared or separated to control the vapor pressure and avoid any damage to the transportation medium.
However, two major safety issues can occur if the vapor pressure of the crude case is very high. The first issue is pumping cavitation at the time of transfer operations, while the second is the presence of vapor pressure in a vessel or pipeline, which may increase as a result of changes in temperature. After exposing the transportation medium to direct sunlight, the crude oil’s vapor pressure increases and, in the worst-case situation, causes damage. Therefore, operators are advised to use a vapor pressure analyzer that can prevent costly damage and also offer proof that the released crude is transported in accordance with specifications.
TVP Measurement and Bubble Point Determination
Within the engineering community, the accurate definition of bubble point and TVP is an extensively debatable topic. Here, the term “bubble point vapor pressure” refers to pressure, while the term “bubble point” refers to temperature.
The bubble point pressure (BPP) and TVP are equal as per the International Maritime Organization. “The TVP or bubble point vapor pressure is the equilibrium vapor pressure of a mixture when the gas/liquid ratio is effectively zero. It is the highest vapor pressure which is possible at any specified temperature. As the temperature of a petroleum mixture increases, its TVP also increases. If the TVP exceeds atmospheric pressure, the liquid commences to boil” (IMO, 2006, p140).
In the above definition, TVP is typically the total vapor pressure (Ptot) of the crude oil minus the dissolved gases in the sample (Pgas) and the vapor pressure of air. The ensuing value is the absolute vapor pressure (Pabs or Pliquid) of the liquid, often known as TVP, as determined by ASTM D2879 (US EPA, 2006). It is recommended that the ASTM D2879 technique is only used for single-component substances. Crude oil is generally a multi-component liquid and needs a different kind of analysis.
The equation TVP = BPP at a vapor-to-liquid ratio (V/L ratio) of 0/1 tackles the usual practical issues related to the transportation of crude oil. The roof is directly placed on the liquid crude oil in the case of floating roof tanks, whereas the liquid crude oil is pressurized in pipelines. In both these cases, the V/L ratio is effectively zero and the measurement of the TVP provides an accurate indication of the bubble point pressure at a given temperature.
However, the equation is not sufficient in certain cases. In multi-component mixtures, bubbles are likely to form whenever the liquid’s vapor pressure goes beyond the environmental pressure (IMO, 2006), regardless of whether the V/L ratio is 100/1 or 0/1. As such, there are three factors that have an impact on the bubble point—temperature, volume, and pressure. A more precise definition considers different V/L ratios and temperatures when establishing the bubble point. In a multi-component mixture, the bubble point is the temperature at which the initial bubbles emerge at a fixed V/L ratio.
Pumping Cavitation
Pumping cavitation is regarded as a major risk during the transportation of crude oil. Cavitation is said to occur when the bubble point vapor pressure or TVP at a V/L ratio close to 0/1 is reached and it often has catastrophic effects. The crude oil is normally accelerated in a pumping system, producing low-pressure areas. If the surrounding pressure happens to be lower than the crude oil’s vapor pressure, bubbles will form, grow, and finally collapse, creating high temperatures and high pressure at the surface of the bubble.
Furthermore, the collapse of the cavitation bubble close to a fixed surface, for example, in a pumping system, will create a shockwave that is directed to a neighboring surface, and this causes damage to the pump or the transportation system.
The vapor pressure of the crude oil should be known for writing standard operating procedures and for properly dimensioning new pumping systems and pipelines. It must be ensured that the crude’s vapor pressure is lower than the pressure in the transportation system for any anticipated condition. This will prevent the build-up of bubbles and pumping cavitation in an installed transportation system.
Temperature, volume, or pressure must be modified if the vapor pressure happens to be very high. Moreover, the pressure within the transportation system can be increased to surpass the crude oil’s vapor pressure. Burning or separation of excess amounts of gases can also reduce the vapor pressure of the crude oil and this, in turn, lowers the volume. As a third option, the temperature for crude oil transportation and thus the crude oil’s vapor pressure can be reduced.
Lord and Rudeen recommend oil cooling or oil degasification to lower the vapor pressure: “The degasification program removes gas from oil in selected caverns, which reduces its bubble point pressure and gas-oil ratio, which in turn significantly increases the predicted margin of system performance under the safety criteria.”2
Here, a complex problem is often faced by crude oil producers: The extracted crude oil is not homogenous. The crude’s vapor pressure can vary at the time of oil production. In addition, the presence of different amounts of natural gas in the crude alters the V/L ratio significantly and raises the vapor pressure to a large extent. Moreover, highly viscous crude oil has to be delivered at extreme temperatures to ensure a flow both in the pipeline and the pumping system. In turn, changes in temperature have an impact on vapor pressure.
Based on the amount of light ends transported with the crude oil, vapor pressure will be considerably higher for 60 °C when compared to the vapor pressure at 37.8 °C (100 °F).
A majority of the vapor pressure testers can measure crude oil at a V/L ratio of 4/1 and only at 37.8 °C. At times, crudes can be transported at a V/L ratio close to 0/1 and at a temperature of 85 °C.
Therefore, for sufficient risk management regarding the bubble point, the vapor pressure should be measured at a V/L ratio of 0/1 and at different temperatures. A vapor pressure analyzer capable of monitoring vapor pressure at different V/L ratios and temperatures will enable the operators to control their transportation system instantly.
Vapor Pressure Increase in the Transportation Medium
An unexpected pressure increase in the tanker or the pipeline is another potential issue faced during the transportation of crude oil. “Live” crude oil contains volatiles, while “dead” crude oil is mostly uncomplicated when transported. Natural gas and other similar volatiles raise the vapor pressure of the crude case. When a tanker or a pipeline—the transportation medium for live crude—is subjected to direct sunlight and heats up, there will be a significant rise in vapor pressure. When live crude oil is filled at 20 °C, its vapor pressure can increase more than two-fold if the live crude oil’s temperature is increased to 50 °C.
If the live crude oil is transported at an extremely low V/L ratio, the absolute pressure increase from temperature variations will become even higher. In Russia, the vapor pressure of crude oil has to be tested at a V/L ratio of 0.02/1 to replicate the conditions in a pipeline or a tanker. Crude oil generally takes up 98% of a tanker’s volume. The increase in vapor pressure resulting from this is shown in Figure 1.
.jpg)
Figure 1. Vapor pressure of crude oil at different vapor-liquid ratios at 37.8 °C (100 °F).
The testing of vapor pressure at different V/L ratios and temperatures answers several questions arising from the transportation of crude oil:
- Do control personnel need to lower the vapor pressure before storage or shipment?
- Is the vapor pressure sufficiently low to mix in some natural gas before shipment without risking damage?
- What will the level of vapor pressure be if the crude oil at a V/L ratio of 0.02/1 (98% filled with liquid) is delivered at 50 °C instead of 37.8 °C because the tanker is exposed to sunlight?
- Is it essential for certain crude cases containing volatiles to fill up a tanker to just 90% to prevent air pollution or damage to the tanker by excessive outgassing?
Vapor Pressure Analyzer
Continuous monitoring of vapor pressure such as BPP and TVP will help operators to instantly control their transportation system. Grabner Instruments’ Minivap On-line vapor pressure process analyzer is designed to measure BPP or TVP at different temperatures ranging between 20 °C and 60 °C to replicate TVP for even higher temperatures. The instrument also makes it possible to determine a V/L ratio as low as 0.02/1 in a pressure range of 0–1000 kPa.
The vapor pressure process analyzer includes the ASTM D6377 method, which is considered the latest standard for determining the vapor pressure of crude oil without any need for sample preparation. Replacing the 80-year-old plus ASTM D323 method, the ASTM D6377 technique is used for determining BPP or TVP in the analyzer.
The sample conditioning system of the vapor pressure process analyzer allows the pressurized crude oil to be directly transferred to the measuring chamber and the vapor pressure is eventually determined against a vacuum through a single expansion of an integrated piston. Next, a three-point expansion sequence is carried out at varied V/L ratios, and a curve fit is conducted for evaluating the TVP at a V/L ratio of 0/1 (also refer Lord & Rudeen, 2010).
In addition, the Minivap On-line vapor pressure process analyzer includes the triple expansion technique for measuring vapor pressure in accordance with the ASTM D6378 method, making it possible to directly measure the total vapor pressure (Ptot) of the sample, and also the vapor pressure of both the gases (Pgas) and liquid (Pabs or Pliquid) in the sample (see Figure 2).
.jpg)
Figure 2. Vapor pressure measurement using the triple expansion method
Considering the fact that the liquids’ vapor pressure stays constant and that all components like dissolved air obey the ideal gas equation, (p*V)/T = constant, an expansion is therefore carried out in three steps at a steady temperature. First, three total pressure values are established, and from these, the solubility factor of the liquid, the partial pressure of the air, and the absolute vapor pressure of the liquid are computed. Results for the pressure of the gas (Pgas), the pressure of the liquid (Pabs or Pliquid), and the TVP (Ptot) of the sample are available every 5 to 7 minutes. The accuracy of this measurement has been established according to the ASTM Round Robin method and is considerably better than that of the traditional vapor pressure test methods.
Crude Blending
An analyzer that can be utilized for measuring both RVPE and TVP will repay its cost in a short period of time. Most often, refiners and suppliers agree over the highest vapor pressure limits of crude oil transported to a terminal or plant. This practice is important to guarantee safety for both storage and transportation and to ensure that the refiner obtains a specific quality of crude. In this process, crude oil blending provides a method for facilitating crude oil processing or raising the sales price.
The price valuation of crudes can be increased considerably by mixing with higher-grade crude oil or natural gas with lower-grade crude oil to reach, but not surpass, target specifications. Profits can be earned if target specifications are reached by mixing low-cost hydrocarbons with the minimum amount of high-grade crude oil. The maximum RVP tends to limit the addition of these hydrocarbons. Based on the RVP before blending, usual ratios of 1%–5% hydrocarbons are mixed into the crude. The ultimate objective of all blending facilities is to achieve the highest precision in vapor pressure tests according to standards, since this raises the potential blending ratio.
The accuracy of the Minivap On-line vapor pressure process analyzer enables C4 blending close to RVP limits, thus translating to maximum revenue generation. A measurement method that fully conforms to the rigorous IP, ASTM, and EN standards, and also US EPA regulations for vapor pressure testing of LPG, gasoline, and crude oil, eliminates the need for additional testing in the laboratory to certify the measurement accuracy.
References and Further Reading
1. Specialized Training for Oil Tankers, International Maritime Organisation, Model Course 1.02, Edition (TB102E), London, 2006.
2. Lord D L, Rudeen D K, Strategic Petroleum Reserve Crude Oil Equation of State Model Development—Current Performance Against Measured Data, Research Report, Sandia National Laboratories, Albuquerque, NM & Livermore, CA, 2010.
3. Organic Liquid Storage Tanks, Compilation of Air Pollutant Emission Factors, Emission Factor Documentation for AP-42, 5th ed, I, 7.1, Office of Air Quality Planning and Standards Office of Air and Radiation, US EPA, Durham, NC, 2006.
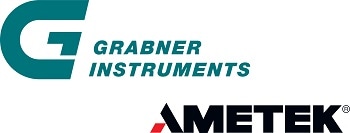
This information has been sourced, reviewed and adapted from materials provided by Grabner Instruments.
For more information on this source, please visit Grabner Instruments.