Plating on plastic is one of the largest markets growing within the plating industry. Manufacturers are cutting costs by utilizing plastic for a wide variety of parts, from washing machines to car logos. These parts are then plated with a chrome or nickel finish for decoration to increase the attractiveness of the product.
The paying consumer doesn’t seem to mind; by 2024, the plating on plastic market is estimated to reach 750 million dollars. In this article, Matt Kreiner, coatings analysis expert at Hitachi-High Tech, outlines why the industry should be prepared for this increasing demand and why XRF technology should become a part of any quality control toolkit.
Huge Trend in Consumer Facing Markets
Two major consumer-facing markets are driving the demand for plating on plastic, these are automotive and home appliances.
In the automotive industry, the prevalence of plated plastic components is mostly due to two reasons. Firstly, to decrease the vehicle weight to increase the efficiency of the fuel, and secondly to limit costs of production.
It is more financially viable to manufacture complicated shapes from plastic and then plate them with chrome and nickel for an attractive finish. Plastic components are also less likely to be impacted by wear and corrosion. In the manufacturing of cars, plating on plastic can be utilized for wheel covers, trims, door handles, grilles, dashboards, and several other components.
The automotive section of the plating on plastic market is estimated to increase by over 6.5% (CAGR) between now and 2024.
The global home appliance industry is estimated to increase from 174 to 203 billion dollars in 2023. In this industry, plating on plastic is utilized to keep manufacturing costs low. Chrome and nickel plating is a cheap alternative to stainless steel.
By simply changing the finish, manufacturers can provide what looks like a different and unique product with no significant changes in design. This finds its application in a wide range of products, from large fridge-freezers to toasters.
Nickel and chrome are the two key decorative finishes; nickel is employed under the chrome layer, or as a complete finish. The plating technology utilized is chrome electroplating and electroless nickel plating. Several plastic materials can be utilized, and frequently used substrate types include: polycarbonate, ABS, liquid crystal polymers and polyethylenes.
XRF Best Practice For Plating on Plastic
In plating for decoration, it’s all about quality. Disappointed consumers and damage to the supplier’s reputation can be the result of a poor quality finish. Providing high quality components is critical as a provider of metal finishes on plastic.
XRF analysis is the ideal thickness measurement method for decorative finishes as it is non-harmful, accurate and efficient. Although, when chrome and nickel is layered over plastic, some XRF equipment can find it difficult to verify and measure the different materials. This is due to the elements in decorative plating being very close together on the X-ray analysis spectrum.
Ensuring XRF equipment has the correct kind of detector is a great way to overcome this challenge. The detector type most suited to this application is a silicon drift detector, or SDD detector. The SDD detector has higher resolution than a traditional proportional counter, enabling peaks from the different metal layers to be easily seen.
This makes it more convenient to ensure the right plating thickness is used, which is critical for maintaining a high quality finish over the component’s lifetime.
Plating on plastic is a tangible growth opportunity for providers of metal finishes, particularly if a supplier already works with automotive and home appliance manufacturers.
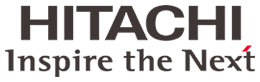
This information has been sourced, reviewed and adapted from materials provided by Hitachi High-Tech Analytical Science.
For more information on this source, please visit Hitachi High-Tech Analytical Science.