Carbon-based fuels, like kerosene and gasoline, have primarily powered aircraft for over one hundred years. Fuels like these hold a lot of energy for their weight, rendering them able to power the largest aircrafts.
As we all know, however, the future of conventional fuel sources for aviation looks uncertain, as carbon-based fuels are a major contributor to CO2 emissions. With decreasing oil resources, the industry is dependent on finding an alternative power source.
The switch to electric propulsion in aircraft is one such area of investigation. For instance, the E-Fan X is a hybrid-electric aircraft, which is currently under joint development between Airbus, Rolls Royce, and Siemens. Its developers hope to boost power for take-off and climb as well as creating an electric-only descent by replacing one of the turbofans used in a regular aircraft with a 2 MW liquid-cooled electric motor - this which would significantly lessen fuel burn and decrease local atmospheric emissions. However, there are yet more advantages of electrification within aviation than reduced emissions.
Transforming How We Travel
Possibilities of aviation electrification include such radical alterations as a vertical take-off and landing, and a much quieter electric aircraft. It seems likely that with this reduction in sound pollution, and less need for lengthy airport runways, there will be an increase in inner-city airports, as well as with less flying restrictions.
Electric planes hold the potential to transform the way we travel, work and live. For instance, there are those who want to live in rural areas, but find themselves prohibited by a lack of opportunities in countryside employment.
Electrification of aircraft would therefore allow an air commute to local cities for work. Within cities themselves, short journeys offer possibilities too, such as in 4-6 seat taxi planes which enable travel from North to South London, or from Palo Alto to San Francisco, for example.
This is not without huge commercial opportunities - electrification stands to make short-haul air travel extremely cost-effective for its providers, with urban travel and longer flying hours providing additional revenue.
Are there any obstacles in the way of this air travel revolution?
Excess Weight Caused by High Power Batteries and Motors
One of the main obstacles to this electric revolution is the power to weight ratio of the batteries and motors which are needed to supplant a conventional kerosene-powered engine. The potential avenues of various battery chemistries are being explored, with Li-O2 currently sitting in front, but a fully electric system needs batteries with a far greater energy density than those currently on the market, to match power requirements without adding excess weight to the aircraft.
According to NASA, a single-aisle 737 class aircraft, even in a hybrid electric configuration, would require a battery specific energy of 1,000 Wh/kg or higher. However, current commercial batteries are only able to offer around 170 Wh/kg of battery specific energy. In order to achieve this kind of power, new battery chemistries are necessary, as are new battery pack designs which feature enhanced thermal management and greater integration.
Electric motors are another obstacle in this revolution. In order to convert the electrical energy provided by batteries into the thrust for take-off and flight, high power density electric motors are essential. Siemens has already begun development of a new 50 kg electric motor which is able to deliver a continuous output of around 260 kW using a hybrid-electric propulsion system. However, when we consider the fact that a commercial aircraft may require a power between two to fifty megawatts, innovation still feels some distance away.
Over-Heating as a Result of Increased Operating Voltages
Another challenge with the goal of adopting more-electric and ultimately all-electric propulsion technologies is the imminent significant elevation of operating voltages. This will prompt a rise in system temperatures. A system of five to ten-megawatts generates hundreds of kilowatts of heat from multiple sources, like motors, power electronics, batteries, and cabling. There is a pressing need to improve heat dissipation in these higher temperature systems in order to prevent overheating and component failure.
Cooling technologies will have an effect, but appropriate thermally-conductive insulation materials will also have a major role to play.
Lack of Availability of Thermally-Conductive Insulation Solutions
Insulation solutions which can support the extremely high voltages that are required to power fully-electric or hybrid-electric aircraft, do not currently exist. Unscreened cable is currently the norm in power transmission and cabling systems. Insulation thicknesses are chosen to minimize the electric field to a point below which incites partial discharge.
This phenomenon is common in equipment with a high electrical field, and generates a short-duration plasma burst. This plasma burst then causes rapid localized spikes in temperature– all of which, of course, would be undesirable in an electric aircraft.
If the industry were to continue to use unscreened cable, this would lead to prohibitively large insulation thicknesses at high voltages. It may well be necessary to move to screened cables with an earthed outer layer, to eliminate partial discharge between wires.
The need to maximize power density in motors and machines also contradicts the need for robust, partial discharge-free insulation. At voltages above 690 V, systems used at ground level are created to tolerate insignificant amounts of partial discharge, but at altitude, this voltage level will be lower.
It may be that a combination of pressurization, insulation, and separation is required to avoid the corona effect of high altitude and high voltage arcing.
This research into new thermally-conductive insulation technologies is vital, in large part because insulation will be subject to different environmental conditions at altitude. These conditions include lower pressures, lower temperatures, higher levels of ozone, and regular variations in humidity.
High-Performance PEEK Insulation can Facilitate Vital Advances
In collaboration with major players in electric propulsion, Zeus has begun to develop an enhanced and single layer PEEK insulated wire. PEEK is a lightweight, high temperature polymer with a high dielectric breakdown strength, which makes it an ideal replacement for the Polyimide (Kapton®), film wrapping, and enamel coated wire which is often used in civil and military aircraft insulated wire applications.
PEEK can also be used in much thinner insulations, thanks to its high strength-to-weight ratio, which can see it replacing thicker, heavier materials but without compromising performance.
High-performance PEEK insulation has offered manifold benefits in its work with leading aerospace industry partners, providing robust performance and reduced errors which contribute to overall cost savings. In electric motor technology, for example, the possibility of using PEEK in a thin layer offers a significant advantage.
A thinner PEEK layer permits for more copper around the stator. The efficiency is thereby increased, which permits the motor to deliver the same output with less energy, or to deliver the same energy with an increased output.
A thin, single-layer solution offers yet more benefits. Less potential failures from reduced delamination become a factor, as do longer product lifespans. Warranty costs too will be reduced with fewer field failures. Cost savings are generated in multiple ways: for instance, the PEEK insulated wire is a 100% defect-free product.
To compare to the fact that that magnet wire typically has no more than 3 defects per 5 m, this offers a significant reduction in inspection costs. Optimization of manufacturing with abrasion resistant solution leads to lower conversion costs and lower yield loss, given that PEEK does not chip, crack, or flake.
Zeus has 25 years of experience of working with PEEK, and the company feels strongly that its high-performance polymer will be able to facilitate vital advances in the next generation of aerospace design.
Electric Planes: The Future of Flying
It seems clear that aircraft electrification is the future of aviation. Though commercial travel on an all-electric aircraft may be some way in the distance, there are myriad market opportunities for the development of electrifying air travel. It’s safe to say that when it comes to electric air travel, the entire Zeus aerospace team – and the rest of the world – are aiming for the stars.
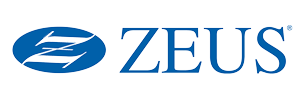
This information has been sourced, reviewed and adapted from materials provided by Zeus Industrial Products, Inc.
For more information on this source, please visit Zeus Industrial Products, Inc.