Ensuring parts meet specification is crucial and so it helps to have confidence in your measurement system. Parts that don’t meet specification, whether gauging composition or measuring thickness, mean rework, additional scrap, in-field failure and possible reputational damage.
.jpg)
Measurement system analysis (MSA) procedures have been called for by internationally recognized quality management systems (QMS). Now a robust MSA must be in place before you can become certified for international quality standards.
The measurement uncertainty for spectroscopy measurements will be calculated as part of this. In the automotive industry, the IATF 16949 standard is the most widespread standard for quality designed to be implemented in conjunction with ISO 9001. Measurement system analysis is exclusively dealt with through a clause in section 7 of the IATF 16949. Calculating and applying the measurement uncertainty is crucial for laboratories that are accredited according to DIN EN ISO/IEC 17025.
MSA in Spectroscopy
The measurement system in XRF, LIBS and OES analyses includes the following:
- The spectroscopy equipment operators.
Their training and access levels on the instrument are likely included here. For example, more experienced personnel may have access to more features with some analyzers.
- The testing process.
Making sure that the correct procedures are followed. For example, when using the analyzer and including calculations for measurement uncertainty, the correct program must be selected.
- The analyzer (XRF, LIBS or OES) and associated software.
The detection limits as demanded by the final specification need to be met by the analyzer and the instrument needs to be properly maintained.
- Calibration (reference) samples and procedure.
A calibration frequency needs to be set and the suitability of reference samples for the application assessed. For example, the composition of the reference sample and the production samples must be similar.
- The components to be measured.
The condition and preparation of the samples must be consistent.
- Environmental factors.
For example, temperature, pressure and humidity
As with any quality management system, with an MSA you first need to understand what the correct procedures are. These then need to be documented and steps need to be taken to ensure those procedures are met in production. To maintain certification, frequent management review meetings are required to assess whether quality standards are being met and whether any improvements can be made.
A robust measurement system analysis procedure that includes measurement uncertainty is essential for selling into industries that require high-quality standards such as the automotive industry. Once the new MSA procedures are implemented into operations, they soon become second nature. For example, correctly implemented spectroscopy instruments can carry out the relevant statistical analysis calculations.
Measurement Uncertainty in Detail
In spectroscopy, accurately calculating the margin of error in measurements is a fundamental part of an MSA procedure. There are several methods for this, including the ISO-recognized GUM method, which requires a calibrated reference sample. Or, if a reference sample is not available, the margin of error can be estimated using a different method.
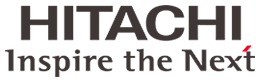
This information has been sourced, reviewed and adapted from materials provided by Hitachi High-Tech Analytical Science.
For more information on this source, please visit Hitachi High-Tech Analytical Science.