Silo fires have the potential to, not only be devastating, but to also have a high cost impact. They can cause a complete loss of stored material as well as create a knock-on effect leading to extended production loss by the plant. To mitigate the risk posed by biomass storage fires, Air Products has developed effective solutions which incorporate nitrogen inerting.
For carbon-neutral, renewable electricity generation from power plants, Biomass is a popular fuel. The largest global exporter of densified biomass is the United States, exporting primarily to the European Union. Very large silos house these wood pellets from production before their exportation, which leaves them at risk of unique operational and fire safety hazards.
The potential for a silo fire is one of the largest issues with wood-pellet storage. Typically, a fire of this kind ignites deep inside the silo’s center and is not easily detected until the majority of the biomass inside has been engulfed by flame. Unfortunately, once the fire has begun, most attempts to control a silo fire and save the structure prove futile.
Ways to Detect and Prevent Silo Fires
Often, the smoldering throughout caused by biological and chemical activities that produce combustible gases, like methane and carbon monoxide (CO) are the key causes of biomass fires. Heat is produced when the concentrations of these gases build up and ignite in the presence of air. This chemical oxidation is further increased with the temperature rise, as rapid generation of combustible gases spreads the imminent and smoldering fire throughout the silo’s interior. These combustible gases slowly rise to the headspace, influenced by the porosity of biomass and the air ingress into the silo, and subsequently create an explosive atmosphere at the top of the silo. Firefighters are precluded from fighting a silo fire from the top, due to the potential of dangerous exposure to a high concentration of CO and the explosive mix of gases present.
Typically, the method used to detect a developing fire in a storage vessel is monitoring the combustible gas concentration in the headspace. This approach may not be as effective in the case of biomass silo fires, given the aforementioned slow rise of combustible gases through the biomass. It could take some days before a concentration rise is detected in the headspace, depending on the height of biomass in the silo. By the time this occurs, the chemical and biological oxidation will inevitably have spread inside the silo to cover a significantly larger area.1
Applying foam or water from the top of the silo is one approach to a silo fire – though this is not without its hazards. This method holds potential risk due to the buildup of combustible gases in the headspace. The use of water leads to the biomass swelling and bridging, which can cause the collapse of the silo without effectively extinguishing the fire contained within its interior.
Using Nitrogen to Prevent and Suppress Silo Fires
Injecting inert gas such as nitrogen into the silo has proven an extremely effective way to counteract a silo fire. The difficulty with this approach is the location and accessibility of large volumes of nitrogen, which are not always on hand or nearby. Though bulk quantities of nitrogen can be delivered by tanker from nearby production plants, a certain amount of infrastructure is required for injecting nitrogen into a silo. This infrastructure includes piping, injection point location and orientation that needs to be built into the silo itself.
Difficulties of nitrogen delivery include its duration (sufficient nitrogen delivery has the propensity to take days) as well as its efficiency: depending on the silo size and fire intensity, it can take weeks to months to extinguish a fire on-site. These silo fires can be devastating and costly, affecting the amount of stored material and possibly leading to an extended production loss suffered by the plant.
Fighting a silo fire once it has begun presents multiple challenges, so the preferred measures taken are preventative approaches, such as proactively inerting storage silos with dry nitrogen. The migration of smoldering pellets will be reduced by a continuous inert nitrogen purge, while other actions are deployed. As displacement with nitrogen lowers the oxygen concentration in the storage area, the energy required to start a fire increases significantly. Also, below the limiting oxygen concentration of the biomass, combustion cannot be sustained which, therefore, protects the silo and its contents. A penetrative approach can also include purging with an inert gas during the filling and emptying steps.
Moisture on the surface of the biomass can also be reduced by dry nitrogen gas. This helps to curtail biological activity at the same time as cooling the biomass to lower the chemical oxidation rate. A lower oxygen concentration is created by providing a continuous purge of dry nitrogen gas into the silo, which reduces the risk of an explosive atmosphere forming in the headspace.
Designing a Nitrogen Inerting System for Biomass Storage
At both the receiving facility (i.e., power plant) and biomass production facility where the material is stored in silos before shipping proactive inerting is recommended. Utilizing computational modeling of gas flow within the silo, a cost-effective silo inerting process can be designed, which requires the installation of plug-free nitrogen injection nozzles. To ensure uniform nitrogen gas dispersion with optimal nitrogen gas usage, the design must incorporate the ideal number and placement of gas injection nozzles.
To simulate the spatial distribution and generation of combustible gases within a silo, using standard or material-specific reaction models, Computational Fluid Dynamics (CFD) can be used. If nozzle design and placement are inefficient, this can lead to pockets in the silo that have high oxygen and combustible gas concentration, and therefore unsafe conditions are created.
Under transient conditions, CFD can also be used to create oxygen and combustible gas concentration profiles, for example, during start-up or a nitrogen injection surge. This is also true for steady-state operation in a specific silo. It is possible that the inerting system can be designed in such a way as to control a maximum combustible gas concentration in the silo, a maximum oxygen concentration in the silo, or indeed both.
The capacity to inject a large volume of nitrogen in the event of a fire can also be built into the design, along with this prevention approach. To meet a steady inerting requirement, on-site nitrogen storage or generation equipment can be specified, as well as specified to achieve a surge capacity during an emergency event.
Examples of fire prevention and fire suppression systems that have been designed for biomass silos, both at a biomass power station and a biomass production and storage facility, follow on below. In one of these instances, a power station fired by coal decided to convert their primary fuel source to wood. To store the biomass safely, a design was created of a nitrogen injection and delivery system, engineered to prevent the build-up of methane and other flammable gases (thus minimising the risk of a silo fire).
Based on the specific geometry of the silos, extensive CFD simulations were performed to mitigate the methane concentration and to optimize nozzle placement within the silo, all to guarantee the most cost-effective gas distribution (see Figure 1). Additions of a nitrogen gas delivery system (which incorporated nitrogen flow controls linked to gas and heat sensors), as well as proprietary injection nozzles (designed to alleviate plugging with dust particles), were made.
.jpg)
Figure 1. This figure demonstrates how the formation of volatile gases, like methane, and their concentration distribution can be simulated through computational modeling. The methane distribution is shown by this illustration, in a silo with continuous nitrogen inerting under two different operating conditions.
Another instance detailed a storage facility that had experienced a silo fire. This fire subsequently created months of smoldering wood pellets and eventual silo collapse. When it came to rebuilding the facility, the silos were designed to be inerted with nitrogen below the limiting oxygen concentration of the wood pellets when filled, to both prevent and mitigate further potential fires.
To evaluate the nitrogen injection system design, as well as validate the number and placement of the nozzles, CFD studies were used (see Figure 2). Transient simulations which were performed demonstrated, not only the propagation of an inert atmosphere, but also the time needed to dispel oxygen from the silo geometry at a given flow rate. The operation team was then able to fine-tune its operating strategy, as well as validate their design. Also, the team was able to guarantee that adequate nitrogen was available on-site to reduce the oxygen concentration in a silo at any given time.
.jpg)
Figure 2. To design an efficient inert gas delivery system, computational modeling can be used. Nitrogen is injected into the silo at a fixed flow rate, creating the transient oxygen distribution depicted in this illustration.
The instances above demonstrate the vast range of solutions that are in existence for both fire suppression and inerting biomass silos. Designing and engineering these specifications to a storage project is possible, which can incorporate consultation on the existing fire mitigation approach, CFD studies to use a simulation to validate a design, as well as the addition of specific flow control systems or plug-free nozzles and nitrogen supply. In light of the immense risk fire poses in a biomass silo, it is important to implement a fire suppression system which is optimised for a specific operation, to guarantee a safe and lucrative operation.
References and Further Reading
- Persson, H., “Silo Fires: Fire Extinguishing and Preventive and Preparatory Measures,” Swedish Civil Contingencies Agency (MSB) (July 2013).
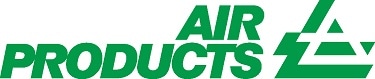
This information has been sourced, reviewed and adapted from materials provided by Air Products PLC.
For more information on this source, please visit Air Products PLC.