With this summer’s temperature reaching record levels in many areas, people around the globe are looking for ways to cool down. What better way than to have a refreshing drink?
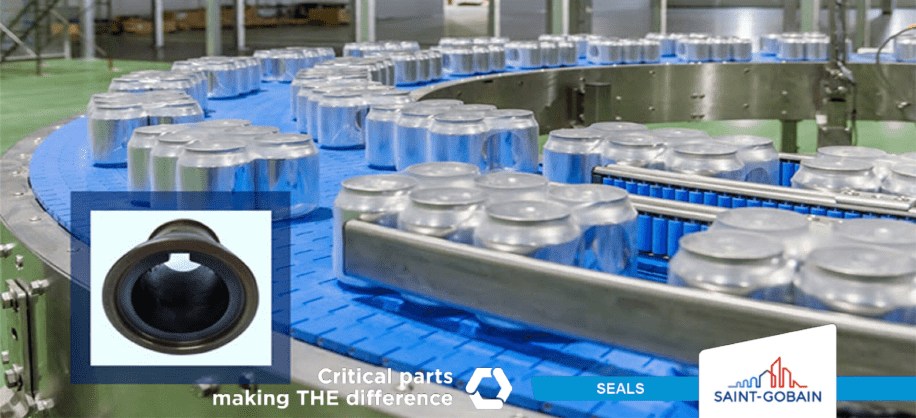
Nearly all of our favorite drinks come from cans. Each year, we use approximately 200 billion aluminum cans from consuming beer and soda. This amounts to 6,700 cans every second - enough to circle the planet every seventeen hours.
Have you ever considered how these aluminum and steel containers are manufactured? The process is intriguing with many steps, including forming, trimming, cleaning, decorating, necking and inspection. However, as with any precision manufacturing, problems can arise. Utilizing the proper parts, like composites, in canning applications can help.
What Are Major Challenges for Manufacturers?
In 1963, the Reynolds Metals company developed technology that became today’s standard for the all-aluminum cans we use (Reynolds later expanded into non-aluminum products such as precious metals and plastics, with the introduction of Reynolds Plastic Wrap in 1982). The initial companies that started using this new can were Coors and Hamms Brewery with Coca-Cola and PepsiCo following in 1967. The amount of aluminum cans shipped in the U.S. grew from half a billion in 1965 to 8.5 billion in 1972.
Ever since, the number continued to grow as aluminum became the almost universal choice for carbonated drinks because it was not just lighter than old steel or steel-and-aluminum can, it did not rust, cools quickly, is easy to imprint, lengthens shelf life and is not difficult to recycle. Presently, the leaders in can manufacturing in the U.S. include, Crown Holdings, Inc., Ardagh Group and Ball Corporation. At least a quarter of the world’s total production, more than 40 billion cans, is manufactured by Ball.
Portability, greater convenience, infinitely recyclable and the move away from carcinogenic materials (for example BPAs) in packaging is resulting in growth in the metal cans market. Appetite for healthy drinks, carbonated drinks and juices also makes a large contribution to this growing industry, which has an estimated value of about $48 billion USD in 2018, and is expected to surpass $58 billion by 2024. According to Modor Intelligence, Asia Pacific is the fastest growing market and the US is the biggest.
Major can manufacturers frequently run day and night to produce cans to strict tolerances. It is not unheard of for multiple machines to produce the same or various size cans at different stages with outputs of three to four million cans per line per day.
With this kind of high production speed, these plants cannot afford even a few minutes of downtime as it can dramatically reduce productivity and increase expenses. It is for this reason they invest in equipment and parts that are not prone to failure. Bushings, bearings and other parts in canning machines play a critical role as they are subject to long run times, high-velocities, extended wear and vibration.
Canning applications frequently use metal and bronze bushings and bearings due to their softer materials, which behave as a sacrificial element to break down before mating parts do on big, costly machinery and help to leave equipment intact.
A drawback of metallic bearings and bushings is they need a significant amount of oil or grease to keep them lubricated. This lubricant, which is automated to flow through lines to machinery, can make equipment, surfaces, and cans slippery and present a number of issues.
It can be problematic to simply ensure the functionality of the automated lubrication system. Manufacturers consistently check the following to prevent equipment from freezing up and leading to downstream issues:
- The appropriate amount of grease
- Functionality of the pump mechanism
- Appropriate flow of the lubricant, with the possibility for machinery to break itself and lead to outages if this is inadequate
Not enough grease is a challenge, and too much is also a problem. Issues that can occur include:
- Safety risks – Grease getting into moving parts and onto products can lead to hazardous working conditions. Too much grease creates a risk of trips and slips and runs in contrast to the 5S methodology to efficiently and safely manage workspaces.
- Increased scrap – Sophisticated vision systems, photographically examining cans for quality, may automatically eject those with grease from assembly lines. Often, when one can is ejected several others will follow, leading to increased scrap and assembly expenses.
- Reduced life and increased downtime – Greater and faster wear to bronze and metal bearings and bushings creates a maintenance problem. This is compounded by the fact that a lot of these parts are used in hard to reach areas or in hot, hostile, environments, where they may be more difficult to access and not be sufficiently lubricated, causing unscheduled downtime.
Critical Composite Parts Can Make the Difference
It is for those reasons, carbon fiber, composite bearings and bushings have risen to the forefront as an alternative to bronze. These highly-performing polymers provide great strength and can tackle high temperatures without the need for lubrication. While carbon fiber is extremely light, it is five-times stronger than steel and twice as stiff, making it ideal for a great number of manufactured material parts.
Omniseal Solutions HyComp’s FibreComp® product is a high-temperature resin polymer, milled carbon fiber and graphite bulk molding compound that is specifically designed for medium loads, higher speeds, and lower impact. To improve canning plant operating efficiency, this unique self-lubricating resin system is blended with carbon fiber to enable superior wear, brilliant dimensional stability and vibration dampening. It can be compression or transfer molded to operate in 600° Fahrenheit (315° Celsius) conditions continuously. Limited wear between moving elements also means improved process control and better quality.
Given its advantages, the FibreComp® product is used by the previously mentioned three major can manufacturers as well as OEMs such as Belvac, Carnaud and Stolle. From shell press, to body making and trimming, it is used in bearings, bushings and other parts in machinery in all stages of can development, IC spray decorating and necking.
Specific benefits of FibreComp® composite bushings above traditionally used high pressure, hydrostatic, bronze bushings include:
- Dry running – Grease lines, line pumps, and chambers can be taken away, dramatically reducing safety and productivity risks and increasing can throughput. Composite bearings can frequently run entirely dry, or with minimal manually applied grease.
- Reworks are limited – A decent example of this is at a Crown Cork and Seal site where standard Necker Ram Housing reworks with FibreComp® composite bushings run six to eight years, which is notably more efficient than the two to four years for OEM product runs. Rework expenses are, in general, cheaper for FibreComp® composite bushings than with OEM components.
- Reduced tool/die wear and longer life – The stable material in FibreComp® composite bushings ensures good wear life as a result of a microscopic resin transfer that gets into the mating surface finish when being broken in to limit the amount of abrasion on devices.
- Improved productivity and alignment – With vision systems for quality detection very sensitive, misalignment of even a tiny fraction on canning machines due to wear can present a significant downstream risk to metal cans. As FibreComp® bearings wear significantly less over time in comparison to copper or metal bearings, they can maintain alignment longer to help ensure quality.
As discussed, one specific application where Omniseal Solutions HyComp’s FibreComp® bearings and bushings are valuable is in the necking machine. The neck, where you would drink from the aluminum beverage can, is formed in 14 steps using a tool that extends and retracts on the tip of a shaft through a housing to gradually develop the thin aluminum wall to avert cracking.
A huge bottleneck, the necking machine runs around 3,000 cans per minute. Each housing rotates on a turret with a shaft in each chamber. A tool on the end of the chamber extends out, perfectly timed with a can as it passes by to put a little bit of the neck on each time. Usually, the OEM housing/shaft is a metal on metal wear interface and requires lubrication pumped in. With as many as 24 housings and 14 turrets all getting grease, the lubricant can become very messy, covering the machine cabinet’s insides and occasionally getting onto cans being formed, resulting in more scrap.
Omniseal Solutions HyComp’s team developed a solution to get rid of the need for grease in this application. As housing on this machinery can be removed, their team bore out the housing ID where it press-fits in FibreComp® bushings. This transformed into the new, longer-wearing surface for the shaft. With FibreComp® bushings being dry running, the requirement for grease is drastically reduced and the housing system life is extended from two to three years with the majority of OEM systems to six to eight with the FibreComp® bearings.
Additional specific applications for FibreComp® bearings and bushings include:
- Body makers - Substituting traditional high pressure, hydrostatic, bronze bushings for tighter running clearances and improved vibration dampening protection of the ram. The result is beverage cans with improved appearances, reduced tool pack wear and reducing oil consumption, leading to improved processing efficiency.
- Vacuum manifolds - Providing stability and drastically limiting wear to extend service life, reduce downtime, and extend productivity in this sealing equipment.
- Shell presses – Offering as much as 20 times longer life than products that are nylon and teflon-based. FibreComp® composites also do not creep to help keep critical separation between moving parts.
The Right Experts also Make the Difference
Production of aluminum beverage cans is growing worldwide by billions of cans a year. With this increase in demand, the future of the beverage is dependent upon designs capable of saving costs and materials. Can manufacturers have to work with the right partners and the right parts.
With longer life, a reduction in wear and dry running capabilities, Omniseal Solutions HyComp’s FibreComp® bushings can help canning companies reach critical tolerances for less scrap and longer service. Their team of experts share many years of experience overcoming issues and innovating custom solutions.
Omniseal Solutions HyComp, founded in 1986 and based in Cleveland, Ohio, is an exemplary supplier of composite parts made of injection and compression molded engineered thermoplastic and thermoset materials. In March 2018, it was acquired by Omniseal Solutions, complementing its high-performance sealing and polymer offerings for high temperature and high load materials.
At first, Omniseal Solutions HyComp’s solutions were designed for wide-scale aerospace and niche areas worldwide. This included use in aggressive space applications for NASA that can run continuously at 600 °F (316 °C), with no lubrication and with no break downs.
Omniseal Solutions HyComp operates from a fully-accredited ISO 9001 and AS 9100D facility and has put into place a fully-operational test laboratory and quality clinic to make sure optimal standards are met and continually improve. Together with the FibreComp® product, the business also assists the industrial industry with its WearComp® carbon fiber product that is used in rolling mill, extrusion and shear applications.

This information has been sourced, reviewed and adapted from materials provided by Omniseal Solutions.
For more information on this source, please visit Omniseal Solutions.