3DLevelScanners have been performing highly precise volume and level measurements of the demanding materials stored in tanks, silos, and bins for almost a decade.
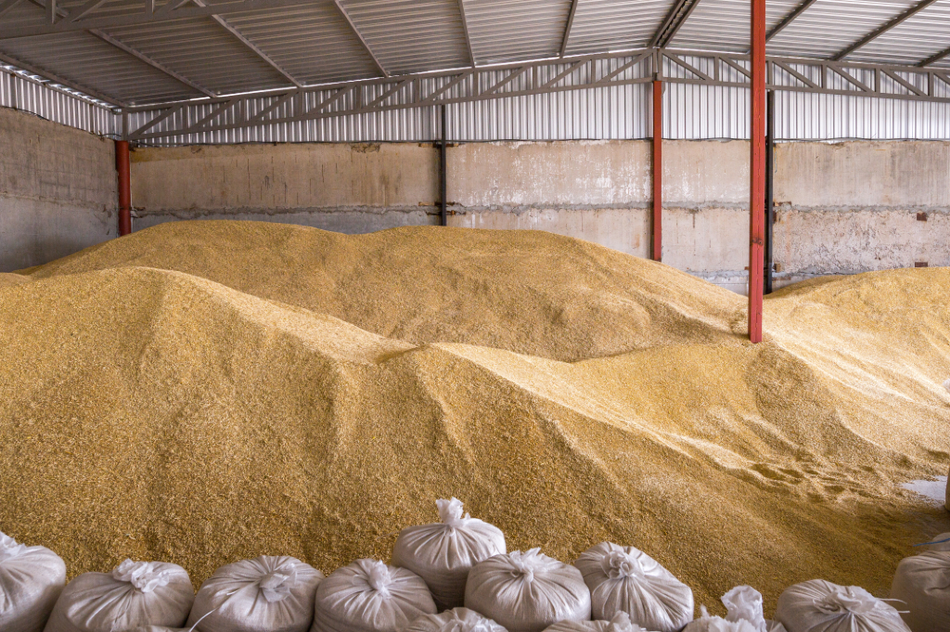
Image Credit: Shutterstock/Sodel Vladyslav
As the only sensor to analyze and map the surface of the material, it generates pulses at a 70 ° beam angle, recording several level measurements and considering uneven surface topography when the volume is calculated.
Every sensor is supplied with 3DVision software that explains the lowest and highest points detected and the average level established on a weighted average of all bin measurements.
For the MVL and the MV models, a colorful graphical display shows where the high and low spots are present in the silo.
3D scanners continue to advance boundaries and solve the challenges of increasingly more complex grain storage operations. This article outlines some of the newest innovations.
View Multiple Silos on a Single Screen
MultiVision Software for Inventory Visibility Across an Organization
Multiple departments across a grain processing or storage operation are affected by inventory management.
Plant employees require a precise understanding of volume to control sales and storage. Those in charge of finance also need an accurate valuation for financial statements.
To create corporate-wide visibility, the optional 3D MultiVision software provides users with the ability to view data for more than one bin in a single window. It is Windows-based, meaning it can be arranged to provide 24/7 access using an organization’s Local Area Network (LAN).
MultiVision software can be utilized with all versions of the dust-penetrating, contactless 3DLevelScanner, including the RL, S, M, MV and MVL models. By selecting a single bin, users can zoom in on complex information for the bin such as average, minimum, and maximum levels.
For the MVL and MV models, users can additionally view the 3D visualization of the contents of the bin. The software lets several users in different locations look at bin volume and level data on a permissions basis.
3D MultiVision software makes the sharing of real-time bin data across the entire organization (or with vendors using VMI) simple to enhance financial management, operational decisions, logistics, and purchasing.
Every user can customize their screen to see all bins or a group of bins and color-code the bins by type of material with user-friendly configuration and intuitive operation. Users can set low and high-level alerts to be told when bins reach key levels.
As the software is installed on the LAN, there are no data access fees or third-party applications (Images 1 and 2).
Detect and Alert to Center of Gravity Danger
Prevent Silo Collapse or Damage Using 3DLevelScanners
Grains are prone to build-up on sidewalls, bridge, pile unevenly, and flow irregularly from storage vessels.
Not only does this make analyzing the material volume within the vessel difficult, but an irregular disbursement of material can also cause wear to the storage vessel itself.
The walls of concrete or steel silos have been known to fail or wear, resulting in bending, buckling, denting, and cracking over time. In the most critical cases, it can create catastrophic silo collapse.
.png)
This has been shown to occur in grain bins across the world, where the walls of large storage vessels are damaged in time by the weight of the built-up grain on one side of the bin.
There is now a software choice that employs 3DLevelScanners to discover the location of the center of gravity, show it graphically, and tell the user when the center of gravity goes outside of a predetermined area. This is suitable for plant operations who would like to discern uneven loading of silos, contributing to structural failures or wear.
A 3DLevelScanner is installed on the roof of the silo in an optimum location to see the material surface in the silo. Level measurements are employed to calculate the X, Y, and Z coordinates of the center of gravity founded on the material topography.
The coordinates are calculated in 3DMultiVision software using a proprietary RS-485 communication protocol. Users can select the alert parameters and the accepted area in which the center of gravity must remain.
A 3D visual will signify where the center of gravity is positioned and will demonstrate if the current center of gravity lies in the preselected area (Image 3).
This unique solution can be employed by operations to decrease structural stress when emptying or loading a silo. It is a useful preventative maintenance tool that can tell the user if there is a need for cleaning or inspection.
The integrity of the silo can be extended over time, and the tool can make the environment safer by alerting the user to possible structural stress as a result of uneven loading (Image 4).
Measure Volume in a Wedge or Pie-Shaped Silo
Accurate Inventory for Ingredients in Segmented Silos (Image 5)
Milling or grain operations often deal with grains at different stages of processing, which can be kept in segmented silos.
Documenting inventory by volume in these spaces that are unevenly-shaped can be complex, particularly for grains or flour that tends to build-up along the outer silo perimeter or the interior walls.
Purchasing or plant operations personnel struggling with the task of managing inventory in pie-shaped segments of silos now have an answer that provides very precise volume data.
.jpg)
The 3DLevelScanner evaluates and models the topography of the material kept in these unusual pie-shaped wedges.
This latest release of 3DVision software update then applies the calculated distances to a 3D model of vessel dimensions and translates it to highly precise volume measurement.
Alternative measurement sensors, for example, weight-and-cable style, non-contact radar, or guided-wave radar sensors measure just one distance in these unevenly shaped segments.
The location of the emptying or filling points or lack of material flow may result in uneven piling of material, which could mean that inventory estimates calculated on a single measurement are inaccurate.
The 3DLevelScanner, in comparison, maps the surface of the material while accounting for any changes or buildup, and also considers the height and radius of the segment being assessed, making the volume accuracy highly precise.
Employing a system that supplies an organization with precise data about the dollar value and amount of material on hand can help to decrease safety stocks, optimize inventory turns, and pay for itself by releasing funds that may be tied up in inventory.
This can be particularly true for expensive grains, oilseeds, and rice being utilized in many organic or contemporary food products.
Any build-up along the interior walls of each segment or on the outer perimeter of the silo segment can be found, accounted for in the inventory, and corrected by maintenance if required.
The same 3DLevel Scanner can be utilized for either round or segmented silos, making it a flexible choice for its long sensor life.
Level Monitoring in Flat Storage Warehouses
Breakthrough Technology Measures Level per Section
With grain production across the world reaching the highest levels yet, there is a shortage of grain storage as special commodities await additional processing.
An initial step to guard grain is through the use of large covered storage buildings where grain is piled employing overhead vehicles or conveyors. Due to irregular piling, it is very hard to predict the amount of grain held in these temporary warehouses.
A further pioneering development not provided with alternative inventory management systems is a new software option that can quantify the level of materials piled within structures.
.jpg)
While MultiVision software categorizes the piled material into virtual sections, multiple sensors measure and map the levels across the surface of the material.
The maximum, minimum, and average levels for each section are calculated for up to 99 distinct sections. The data is gathered to produce a graphical image that demonstrates the topography of the complete storage building (Image 7).
This original solution is utilized to approximate inventory and increase the efficiency of production. Locating high and low areas helps to automate process control and manages the extraction or filling of materials.
Up to 20 3DLevelScanners have been installed in the upper structure of the warehouse roof in proven installations.
The building is essentially separated into sections as small as 1.5 by 1.5 meters with 3D sensors constantly analyzing changes throughout the surface and offering distinctive visual and data reporting of inventory in the huge structure.
This innovative technology is perfect for corn or different grains held in covered warehouses.
3D scanner technology began a revolution in the accurate management of inventory in 2009. This progress keeps solving the unique needs of the industry as the worlds of sensor software and hardware integrate with contemporary solutions.

This information has been sourced, reviewed and adapted from materials provided by BinMaster.
For more information on this source, please visit BinMaster.