Element Six harnesses the unique properties of synthetic diamond and tungsten carbide to deliver supermaterials that improve the efficiency, performance and reliability of industrial tools and technology. 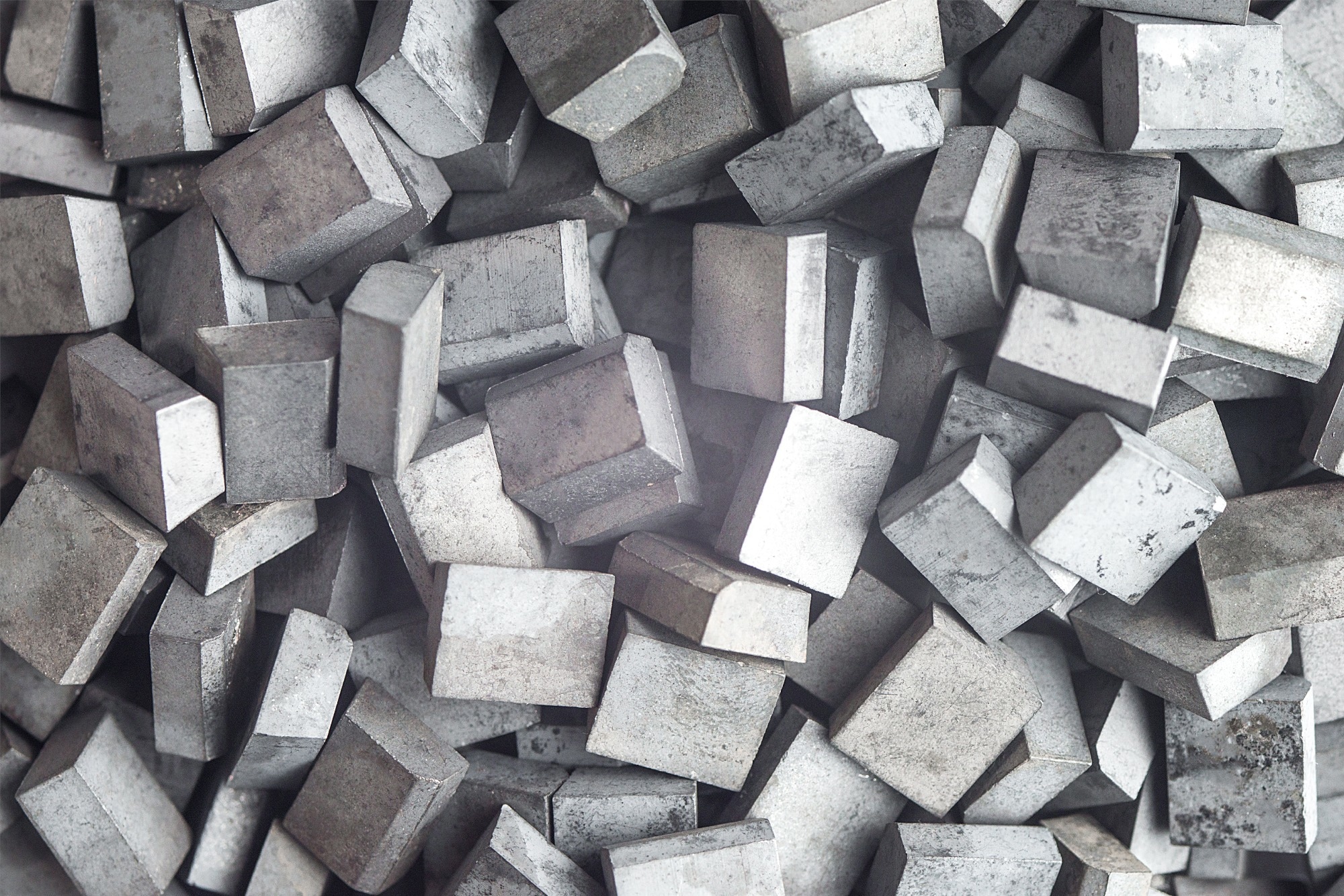
Image Credit: AkulininaOlga/Shutterstock
The primary focus for Element Six is providing supermaterials solutions that optimize the performance, efficiency, and reliability of industrial tools and technology, something that is proving to be vital for the future of the construction and mining applications.
Element Six is celebrating 60 years of synthetic diamond innovation. Since 1959, they have been working to continuously develop and optimize their solutions to meet the ever-changing demands in the industries they serve. The extreme properties of synthetic diamond are used to open up possibilities in a range of areas such as thermal management and quantum optics, manufacturing for the automotive and consumer electronics industries, and cutting and drilling applications for oil and gas.
Unique In-House Manufacturing Capabilities
With primary manufacturing sites located in the UK, Ireland, South Africa, Germany, and the US, Element Six is in a unique position as it possesses the in-house capabilities to manage the end-to-end production process.
Their German facility has a wide scope of capabilities such as polishing, grinding, steel machining, EDM cutting, welding and brazing, that sets it apart from other manufacturers. Element Six is able to both work alongside its customers throughout the entire process, and to offer them customized solutions that are tailored around their specific challenges.
To gather a deeper understanding of the challenges they are facing and the problems they want to overcome, Element Six works collaboratively with leading OEMs and end-users. Starting with their initial brief, Element Six helps the customer choose the most appropriate design and material for their tool or application, working to develop and deliver a high quality, tailored solution.
Boosting Mine Productivity
Element Six is part of Anglo American plc and De Beers Group, so they are in a unique position when it comes to gathering valuable insights into the current demands of the mining industry. They can access first-hand information that comes directly from mining companies, giving them a strategic advantage over other key carbide and synthetic diamond manufacturers. Element Six can focus on developing solutions that will solve real-time challenges and ensure the needs of mining companies are taken into account when designing parts.
The manufacture of components for mineral processing equipment is one of their core mining businesses. Components are developed firstly for use in equipment that will extract materials and bring them up to the surface, and secondly for use in crushing or milling applications that perform the operation of processing the materials.
Element Six mining components aim to enhance the lifetime of tools and applications to limit time loss for mining companies. Wear resistance is an essential element in achieving longer tool life and through close collaboration with leading OEMs, Elemnet Six has been able to develop special carbide grades to enhance operations such as mineral processing.
Increasing the wear resistance of components increases tool life, and delivers cost savings to enable better time efficiency for project completion.
Global Sales Director, Mining, Road and Wear Parts at Element Six, Markus Bening, commented, “As companies look to embrace forward-thinking concepts like smart drilling and smart mining, longer-lasting tools are at the forefront of their minds. Our specially developed carbide grades enable continuous improvement of application lifetimes and increase the ease at which mining companies can run applications for processes like crushing or milling.”
Synthetic Diamond Solutions to Shape the Future
In addition to tungsten carbide, Element Six is continually developing materials that utilise the properties of synthetic diamond. Their polycrystalline diamond (PCD) material is of particular relevance to mining, a material that is employed in their range of drill bits for roof bolting applications.
Element Six uses two methods to grow synthetic diamond; Chemical vapor deposition (CVD) and High-pressure, high-temperature (HPHT).
The CVD method occurs at a low pressure using a plasma reactor, whereas the HPHT method, used to produce diamond for Element Six's mining solutions, mimics the conditions under which diamond naturally forms. The HPHT method uses a temperature of 1,500°C and a pressure of 55,000 atmospheres – that’s the same as 5,000 saloon cars stacked on top of a jar of peanut butter!
PCD tools provide a range of advantages to the end-user, with one key benefit being the potential for some applications to extend tool life by over 40 times compared to standard tungsten carbide tools.
“Feedback from end-users in Sweden, where synthetic diamond is today’s standard for road milling, consistently demonstrates the game-changing benefits delivered to our customers,” said Bening.
Bening continued, “There is presently a great deal of testing and fine tuning taking place, and in the next five to ten years I envisage the commercialisation of hard rock cutting throughout the mining industry, where Element Six PCD technology could play a pivotal role. E6 synthetic diamond tools can deliver advantages such as extended tool life, increased cutting and drilling speeds, and reduced machining time, all of which are paramount to mining industry success in the future.”
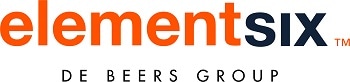
This information has been sourced, reviewed and adapted from materials provided by Element Six.
For more information on this source, please visit Element Six.