The aerospace sector is well known for its safety standards, and the whole sector has progressed to provide equipment and services for testing aircraft and their subsystems.
As airliners take off and land, they are subjected to vast loads from the undercarriage touchdown to the back-thrust of the jet engines when they slow the aircraft on the runway and the wind pressure on the flight control surfaces and flaps when they are lowered to allow air-braking.
Frequently testing the relevant parts and recertifying them as fit for purpose is necessary, as these loads may quickly increase during difficult situations or in an emergency.
Test Rigs from SGN Electrical
SGN Electrical in Sittingbourne, Kent, UK, recently developed two test rigs, one for testing the landing gear and one for testing the flaps on the tailplane. This helps to ensure that the transoceanic-scale airliners can carry hundreds of passengers and can land every flight safely and reliably.
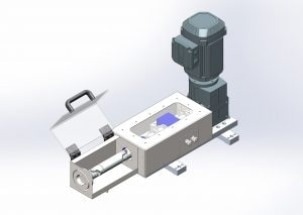
Image Credit: Sensor Technology Ltd
SGN is known for its electrical contracting services to most industries in the southeast, including at the main airports of the region where “right first time and right on time” is the standard regardless of the work challenges.
The companies engineers are highly experienced in testing and inspection, from aerospace field to small installations, hazardous areas, and other specialized fields. Further to their electrical expertise, they are equally knowledgeable in mechanical engineering, so it was a choice by nature to develop the test rigs.
Testing of Ballscrews and Landing Gear Using Test Rigs
One rig carries out the testing of the ballscrews, which are utilized for raising and lowering the flaps of the tailplane. The rig simulates the high-speed airflow over the aircraft while it is in flight by using a hydraulic actuator to exert a measured but changing load to the ballscrews, instead of just performing a function test.
Via the simulation of loads on the main lead screw as the wheels are lowered and touch down, the second rig tests the landing gear. This includes the sudden shock loads which could happen during an emergency landing and the additional loads which could be experienced in bad weather conditions.
Sensor Technology’s TorqSense Transducer
In both of the test rigs, the TorqSense transducer, which was developed by Sensor Technology Ltd in Banbury, is employed as the main element. The TorqSense is much-favored by test rig builders, as it is a non-contact technology that measures the torque in a rotating shaft using reflected radio waves.
During its operation, two piezoelectric combs are fixed to the test shaft at right angles to each other. Their purpose is to reflect radio waves targeted at the shaft by the TorqSense. Since they get distorted proportional to the torque in the shaft (one compressing, and the other expanding), they distort the reflected waves.
How much the waves get distorted is in proportion to the comb distortion, which reflects the shaft deformation and so, the level of torque that it is subjected to.
There is no need to spend time setting up fiddly slip rings every time you use the rig. You just point the sensing head at the test piece and real-time data is collected. We run this through a standard Sensor Technology controller and the results are both displayed on a digital screen and stored for later analysis.
Scott Nicholson, SGN Electrical
Using TorqSense makes it easy to build a test rig, but far more importantly it makes the tests much, much quicker and easier. Therefore more tests can be done in a given time, which means results can be checked, double-checked and checked again—which is pretty much the operating procedure required for aircraft safety.
Scott Nicholson, SGN Electrical
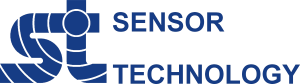
This information has been sourced, reviewed and adapted from materials provided by Sensor Technology Ltd.
For more information on this source, please visit Sensor Technology Ltd.