This article examines the various uses of presses in research and manufacturing, while exploring some of the different industries in which they are used. Omnipresent in both industry manufacturing and laboratory environments, presses find use in a diverse range of processes, including transfer molding, compression molding, and vacuum press applications.
Machine presses – simply referred to as ‘presses’ – are common-place in nearly every niche of manufacturing. Techniques associated with presses are wide-ranging and vary almost as much as their applications and they all share one thing in common: presses enable the manufacturing of components via the application of pressure. In processes such as laminating, molding, overmolding, and extrusion, presses can be put to use to form a range of materials, primarily rubber and plastics.
The high-throughput production of a huge number and variety of common items including pc boards, aerospace parts, oil seals, molded cable ends and test plaques are made possible because presses possess an unparalleled versatility as a manufacturing tool. Furthermore, as well as producing finished products in a single process, presses are typically used to perform crucial steps in multi-stage manufacturing processes; such as coil encapsulation.
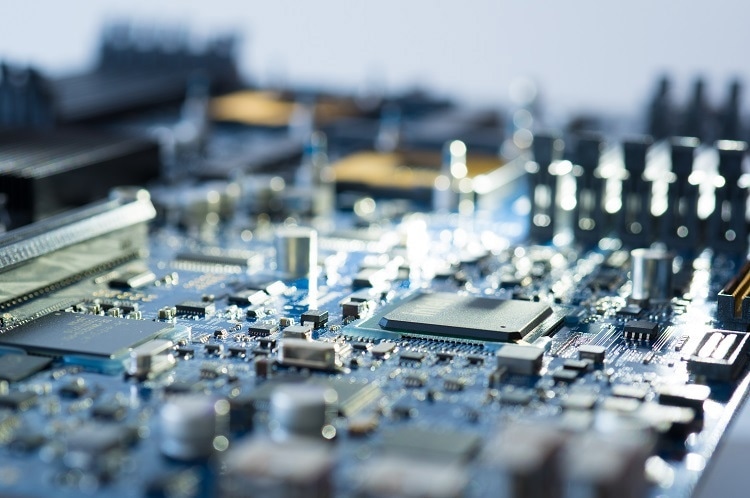
Image Credit: glitterstudio/shutterstock.com
While manufacturing and industry depend on colossal labor heavy presses, customized precision hydraulic and pneumatic presses are often found in the laboratory too. Lead frames used to mount microchips, for example, require the use of presses with sub-micron accuracy for their production. The manufacturing of next-generation aerospace components from carbon-fiber-reinforced plastics is also made possible because of heated presses.1 What’s more, is that presses have even made their way into tissue engineering processes, where they have provided an effective way of producing cellular scaffolds on which to grow tissues for transplantation.2
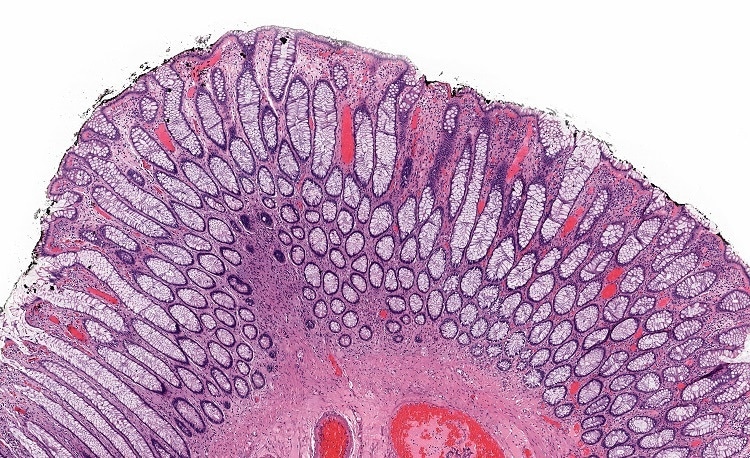
Image Credit: MriMan/shutterstock.com
Today’s presses are usually either floor standing or benchtop devices and can be assembled to meet a vast range of specifications of force and precision. While standard presses meet the needs of most manufacturing applications, there are cases and instances that necessitate a more demanding use, often requiring a customized press solution that can apply exceptionally high forces or can move over extremely small and precise increments.
To gain more insight, three of the most common types of processes, which are performed by presses, will be assessed: compression molding, transfer molding, and vacuum press applications.
Compression Molding
This is one of the most basic and fundamental molding techniques, given its name because a bulk material is positioned into a mold cavity, and compressed so that it packs the mold in a press. Depending on the material, it is possible for the workpiece to be preheated prior to pressing, or even heated during pressing using heated platens.
Compression molding provides numerous advantages and not least due to it being one of the cheapest molding processes to carry out. This technique can be used to produce relatively large and fairly sophisticated components. Compression molding can be used to mold plastics, fiberglass and metals, and finds common usage in the production of moderately curved or flat components.
Transfer Molding
Transfer molding, also known as ‘compression transfer molding’, is the application of pressure by a press which forces the material into the mold. By forcing bulk material into the mold higher dimensional tolerances can be achieved, but this requires much higher pressures than compression molding.3
The conditions needed for the material to flow into the mold means that transfer molding is usually reserved for the generation of components from resins, to form thermoset products. Transfer molding is adaptable enough for a diverse range of applications that includes industries such as construction, electronics, aerospace and even the manufacture sports equipment.4
Vacuum Press Applications
‘Vacuum press’ refers to any kind of machine press where during pressing the workpiece is held in an evacuated environment. Pressing in a vacuum can lead to faster production, yield higher quality results and reduce waste materials. Removing heated gases and trapped air from the equation, the application of a vacuum can minimize the type of defects that can occur with compression or transfer molding. For this reason, vacuum presses are most commonly used for the manufacturing of products where a particular level of high-quality precision is required.
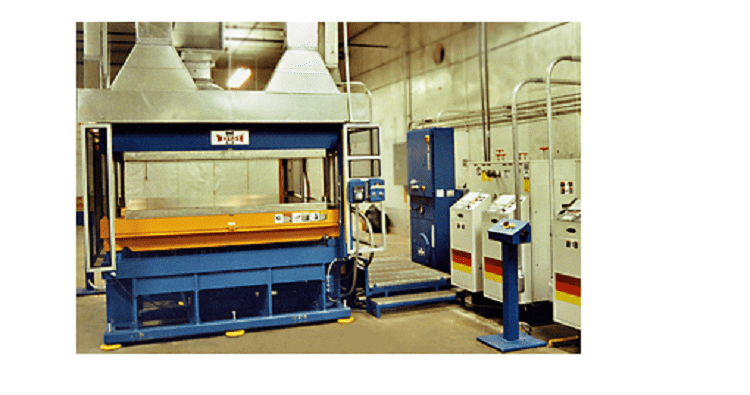
Image Credit: Wabash MPI Carver
Hydraulic and Pneumatic Presses for Manufacturing and Laboratory Work
Wabash MPI is a manufacturer and global distributor of industry standard and customized pneumatic and hydraulic presses for the medical, aerospace, energy, and automotive industries, among many others. Producing a full range of presses to suit any application in manufacturing, Wabash MPI provides presses for compression molding, transfer molding and vacuum press applications.
A wide-range of accessories can modify the capacity and facilities of Wabash MPI presses, including large, heated platens and vacuum shrouds. Furthermore, capable of providing a range of field services, Wabash MPI is on hand to assist with start-up, calibration, and preventative maintenance of new equipment.
Their sister company,Carver, provides hydraulic and pneumatic presses developed with rigor and precision exclusively for the laboratory. With experience in the manufacturing and production of presses for over 100 years, their range of floor-standing and benchtop presses are designed with accuracy at the forefront. They are also cutting-edge world-leaders in the design and production of custom presses and produce accessories that can meet the demands of the most complex of applications.
References and Further Reading
- Wulfsberg, J. et al. Combination of carbon fibre sheet moulding compound and prepreg compression moulding in aerospace industry. in Procedia Engineering 81, 1601–1607 (Elsevier Ltd, 2014).
- Hou, Q., Grijpma, D. W. & Feijen, J. Porous polymeric structures for tissue engineering prepared by a coagulation, compression moulding and salt leaching technique. Biomaterials 24, 1937–1947 (2003).
- Ornaghi, H. L., Bolner, A. S., Fiorio, R., Zattera, A. J. & Amico, S. C. Mechanical and dynamic mechanical analysis of hybrid composites molded by resin transfer molding. J. Appl. Polym. Sci. 118, 887–896 (2010).
- Resin Transfer Moulding - K. Potter - Google Books. Available at: https://books.google.co.uk/books?hl=en&lr=&id=JmDxCAAAQBAJ&oi=fnd&pg=PR7&dq=+transfer+moulding+&ots=9e8iVSgvVo&sig=CqvqVT37MgVwLXm9NI0kWwMgF10&redir_esc=y#v=onepage&q=transfer moulding&f=false. (Accessed: 1st November 2019)
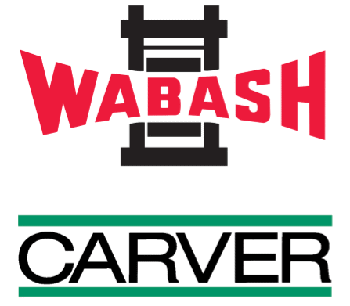
This information has been sourced, reviewed and adapted from materials provided by Carver, Inc.
For more information on this source, please visit Carver, Inc.