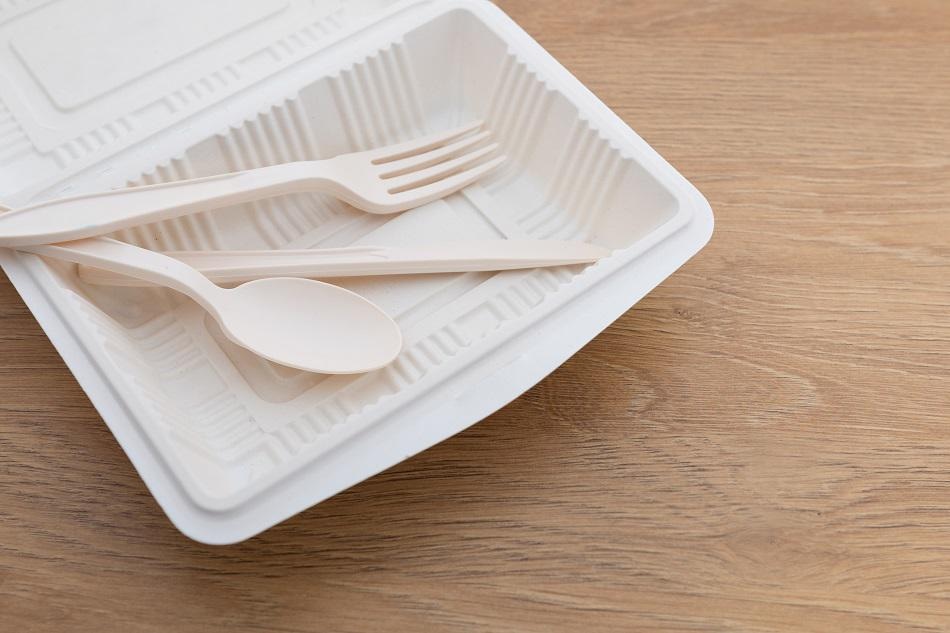
Image Credit: Pawarun Chitchirachan/Shutterstock.com
The increasing amount of synthetic plastic waste is a huge problem that could potentially be solved with bioplastics. Despite increasing efforts to recycle, approximately 53% of waste in the US is still sent to landfill and plastic waste makes up about 19% of that1. While evidence suggests that people are becoming more aware of the damage that plastic waste can cause to the environment, it is still extremely prevalent in daily lives, from packaging to clothing.
Viable alternatives to synthetic plastics are biopolymers produced from natural and renewable resources. Economically speaking, they are also abundant, inexpensive, environmentally friendly and biodegradable.
Food is most commonly protected from damage and spoiling using plastic films and, more often than not, this is unavoidable. Many food products could not be stocked in supermarkets without the use of plastic films.
Agricultural by-products make a considerable contribution to bioplastics. They are typically recovered from the co-products that arise when the initial crop is processed into another form. They can come from a range of sources, including soy protein concentrates and isolates from purified soy flour2, potato protein concentrate extracted from potato fruit water3, and legume waste formed from residues when processing peas, beans and lentils4. The protein extracts are not themselves suitable as plastics. The intramolecular forces linking different parts of the protein chain reduce the mobility and formability of the material, so a plasticizer may be added in order to improve the material properties5.
There are a number of ways to form the final plastic material, among them casting and hot-pressing. The results of hot-pressing depend on accurate control of the temperature and applied pressure. The elevated temperature causes denaturation of the proteins. This means that ordered alpha-helical and beta-sheet structures in the polymer chains give way to more randomly organized coils and loops which allow the material to behave more plastically. These changes are demonstrable in the form of band shifts in the amide region of an infrared spectrum, measurable using, for instance an ATR technique3.
These bioplastics must be tested in other areas to make sure that they can compete with existing synthetic polymers before they can be brought into mass production. Mechanical strength, water sensitivity, and cost are the three main areas for testing. For testing, it is common to produce small-scale samples for the laboratory by pressing the protein between two heated plates at a constant pressure. Samples of a constant thickness can be produced fairly quickly with this method without expensive equipment.
Specac offers a range of tools for producing, testing, and analyzing biopolymers and bioplastics. The Mini-film Maker is ideal for laboratories with limited space6. Its small footprint allows it to be situated alongside other equipment on a worktop and it is ideal for processing proteins into a form ready for analysis by infrared transmission spectroscopy or another analysis method. It has a heating element that is capable of achieving precise temperatures from ambient to 250 °C, making it ideal for hot pressing delicate protein-based polymers, with constant and reproducible thicknesses from 50 to 500 µm and 15 mm diameter.
Specac also offers conversion kits for those who already own one of their presses but would like to produce polymer films7. The Atlas Constant Thickness Film Maker and Atlas Heated Platens can be used with existing Specac presses to form polymer films of highly reproducible thickness, from ambient to 300 °C.
References and Further Reading
- National Overview: Facts and Figures on Materials, Wastes and Recycling. United States Environmental Protection Agency (2015).
- Mercedes Jiménez-Rosado, Victor Perez-Puyana, Felipe Cordobés, Development of superabsorbent soy protein-based bioplastic matrices with incorporated zinc for horticulture. J Sci FoodAgric 99, 4825–4832 (2019).
- Online, V. A. RSC Advances Commercial potato protein concentrate as a novel source for thermoformed bio-based plastic fi lms with unusual polymerisation and tensile properties. 32217–32226 (2015). doi:10.1039/C5RA00662G
- Change, C. & Estanga, E. G. LEGUVAL — Result In Brief. 7–8
- Jerez, A., Partal, P., Martínez, I., Gallegos, C. & Guerrero, A. Protein-based bioplastics: Effect of thermo-mechanical processing. Rheol. Acta 46, 711–720 (2007).
- Specac. Mini-Film Maker | Polymer Film Maker. Available at: https://specac.com/.
- Specac. Constant Thickness Film Maker. Available at: https://specac.com/.
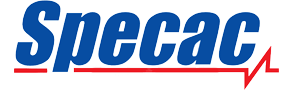
This information has been sourced, reviewed and adapted from materials provided by Specac Ltd.
For more information on this source, please visit Specac Ltd.