The international welding scenario in both industry and academia has been overwhelmed in recent years by a profusion of new versions of arc welding processes. Developments in electronics and software, as well as new concepts in mechanical design and mechanisms, have made innovations possible.
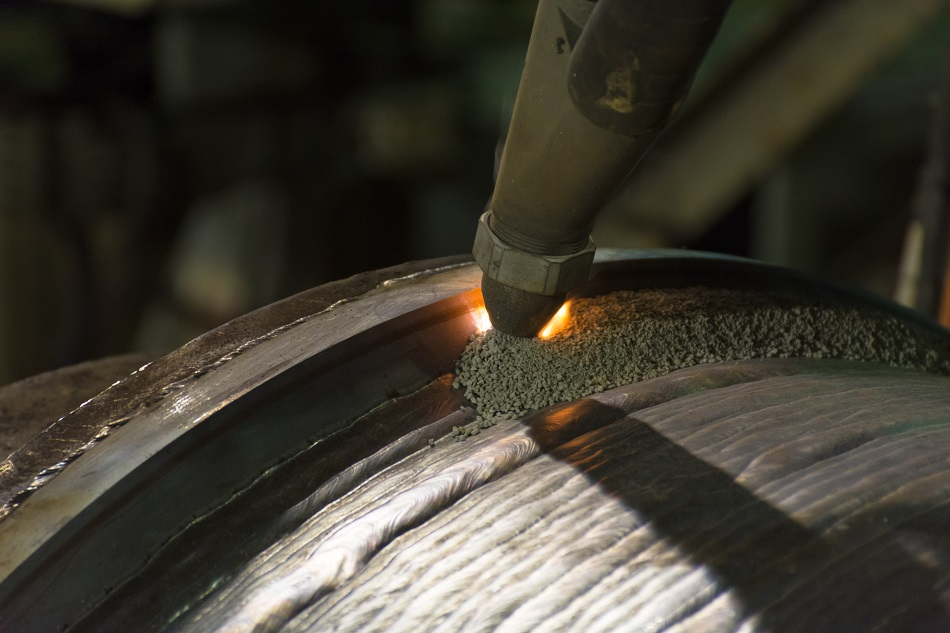
Image Credit: GajokFilm/Shutterstock.com
Dynamic Feed (Wire Oscillation) is just one example when it comes to the TIG process. In comparison to other arc welding processes, one disadvantage often attributed to conventional TIG is low productivity.
A forward and backward wire oscillation movement has been implemented in TIG systems to manage this drawback and to better deal with hard wetting materials (Ni-Cr alloys for example). This implementation has been well received in the industry and has had a great interest within the scientific community.
The technique may also provide a further benefit of reducing porosity. In terms of observation and stability evaluation of the metal fusion and transfer, arc behavior and weld pool behavior, high-speed filming has been a powerful tool in the study and development of such techniques. The main purposes of such studies are the scientific investigation into the influence of parameters over the resulting physical phenomena and the development of parameterization for different welding conditions (position of wire feeding, torch geometry, wire dynamics).
Dynamic feed TIG Welding – CAVILUX illumination laser – Cavitar Ltd
Video 1. Dynamic Feed TIG Welding imaged at 1.000 fps. Video Credit: Cavitar
In terms of MIG/MAG welding, new technologies are designed to support the development of adaptive control methods, innovative current waveforms and mechanization techniques to improve arc stability, metal transfer regularity, process reliability and expansion of the application range.
The rotary arc and the pulsed arc mode are examples of this, both of which show promise in achieving outstanding results for cladding and thick-walled narrow gap joints. In such scenarios, high-speed filming is applied for metal transfer phenomena observation, arc movement patterns and respective influences over the weld pool, arc geometry and generation of the weld bead. Furthermore, to evaluate consumables and peripherals (such as wire-electrodes, contact tips and wire feeders), high-speed filming has been applied.
Rotary arc pulsed MIG/MAG welding - CAVILUX illumination laser – Cavitar Ltd
Video 2. Rotary Arc Pulsed MIG/MAG Welding imaged at 5.000 fps. Video Credit: Cavitar
MIG/MAG welding - CAVILUX illumination laser – Cavitar Ltd
Video 3. MIG/MAG Welding with forward/backward movement of the wire electrode imaged at 4.166 fps. Video Credit: Cavitar
A CMOS, 1-megapixel array size color camera was applied in the videos above with 105 mm and 180 mm macro lenses. A Data Acquisition System was used to adjust acquisition rates in synchronization with electric welding data monitoring.
CAVILUX HF has been intensively applied to these investigations and developments. The arc intensity of the produced high-speed images can be finely adjusted using the laser illumination system. This enables specific welding process features (wire, arc, droplet, pool, etc.) to be selected and isolated.
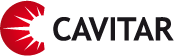
This information has been sourced, reviewed and adapted from materials provided by Cavitar.
For more information on this source, please visit Cavitar.