Metal forging is a molding process where a press machine or hammer is used to apply strong pressure to a metallic material.
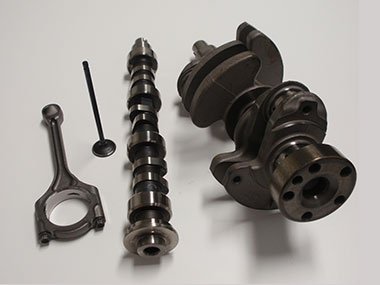
Various forged products used in vehicles. Image Credit: Evident Corporation - Industrial Microscopy
Metal forging is commonly used for products that need to be strong, because forged products have a greater strength than products made by cutting, where a metal is ground with cutting equipment, or by casting, where melted metal is poured into a mold.
Forged products include things you might find in your house such as kitchen knives, along with components used in industrial machinery and vehicles like valves, gears, crankshafts, and connecting rods. When pressure is applied to a metal, its crystal structure is crushed and forms a linear shape. This is known as a metal flow (or fiber flow).
In the forging process, since the line of metal flow is formed following the product's shape, processed materials have have high viscosity and resistance to external impacts.
Challenges of Observing Metal Flow Using a Conventional Microscope
Inspectors verify the metal flow of forged products during quality control. The flow must be correct for the product to fulfill the strength requirements.
The metal flow is usually observed using a microscope. To evaluate a wide area, the inspector must observe using a low magnification microscope or stitch multiple high-magnification images together. These techniques pose two critical issues:
- The form of the metal flow is not clearly visible at low magnification because of the lens' low resolution.
- In many cases, stitched images may not be of a high enough quality because of misalignment or uneven colors caused by conventional stitching software.
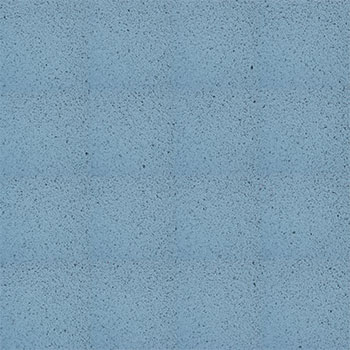
Pasted image with uneven color.
Benefits of Observing Metal Flow Using the DSX1000 Digital Microscope
1. Clearly Observe the Entire Forged Product at Low Magnification
When inspecting a large sample such as a forged product, the user begins by viewing the whole sample at low magnification to determine the observation position.
The DSX1000 digital microscope is equipped with a dedicated low-magnification, long-working distance objective lens so the user can efficiently locate the observation area on a clear image.

SXLOB low-magnification, long-working distance objectives.
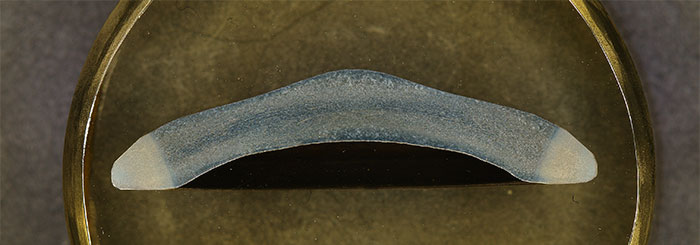
View the entire forged product with a low-magnification objective lens (1X).
2. Using the Auto-Stitching Function, the User can Create a Fully Focused Image of a Forged Part
Using the Auto-Stitching Funcion when observing an edged, resin-embedded sample, the user may capture an image with blur spots at a distance.
This can be casued by the shallow depth of field at high magnification and the difficulty of locating a flat area. The same is true for a stitched image where there are different areas that are in and out of focus.
The DSX1000 digital microscope, provides an auto-stitching function to help users create a fully focused image of a forged part. Just click the all-points AF icon in the softwareto create a stitched image from multiple images that are all captured in focus. The microscope automatically captures images once the user enters the length, number of images, and starting and ending points of the images for stitching. High-precision shading and pattern matching produce high-quality stitched images.
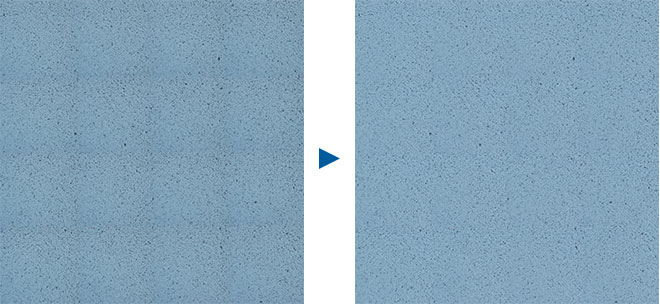
Image Credit: Evident Corporation - Industrial Microscopy
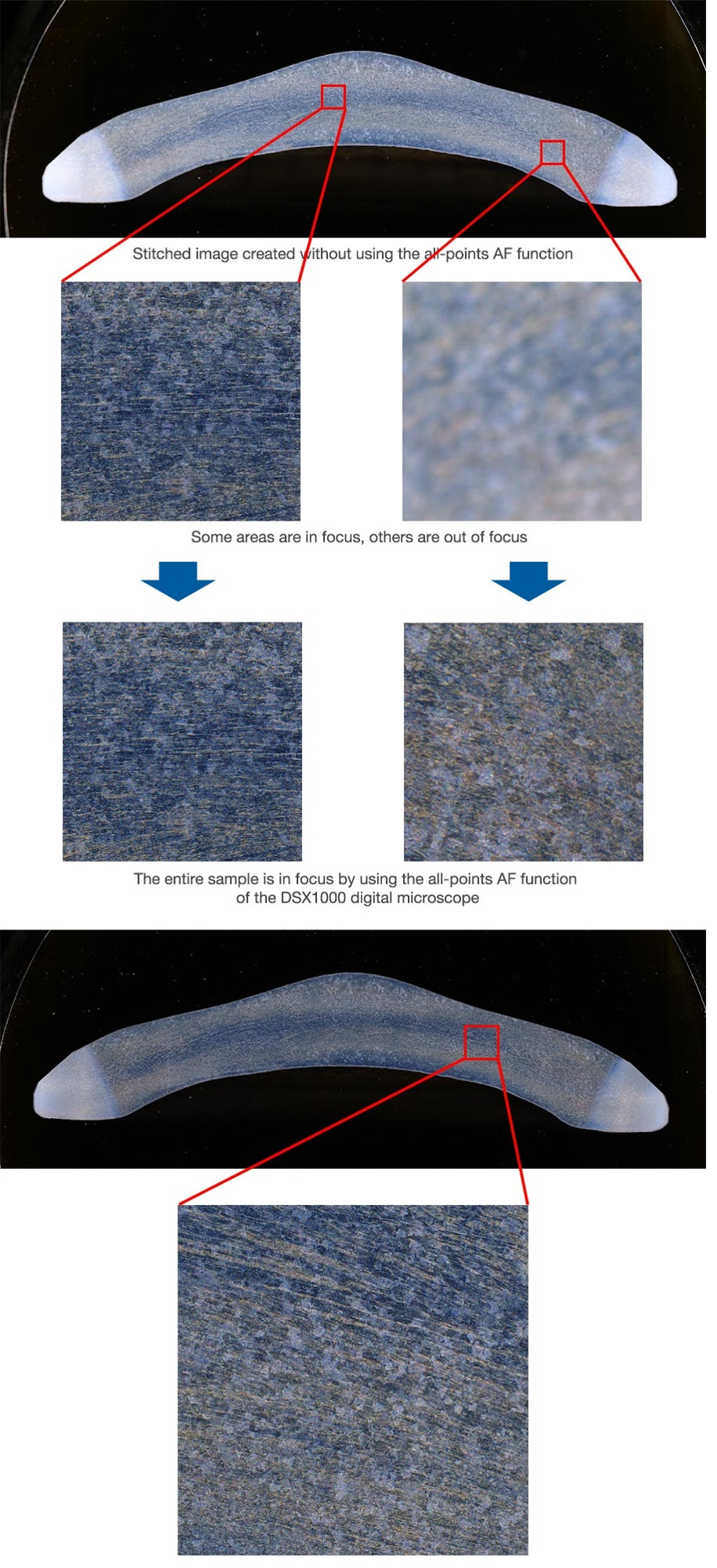
An auto-pasted image of a forged part made from several high-magnification images captured by the DSX1000 digital microscope (140X, 6 images vertically, 17 images horizontally). The image quality is maintained if you cut and magnify a part of it. Image Credit: Evident Corporation - Industrial Microscopy
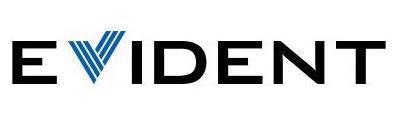
This information has been sourced, reviewed and adapted from materials provided by Evident Corporation - Industrial Microscopy.
For more information on this source, please visit Evident Corporation - Industrial Microscopy