Ceramic powder can be heated and formed into a huge variety of shapes, but the pellet or disc is the accepted shape for the testing of these materials.
This shape is favored for many reasons, the main justification being that the cylindrical shape means there are only two edges to perform as stress concentrators.1
This is crucial because if the initial powder lacks a binder, the following green compact can be extremely delicate and may fracture before additional processing.
This phenomenon can also be found in the heat-processed form as a greater amount of edges can increase the chance of the structure breaking in the densification process.2
A further argument behind the selection of the pellet shape when analyzing these materials is that it can be cut to suit most of the tests that will be applied to it. Some of the common tests that are carried out on engineering ceramics are X-ray fluorescence (XRF) and infrared (IR) spectroscopy.3
A flat cylindrical sample is normally used in these investigations. The ability to test the pellets with no need for additional grinding or cutting is highly beneficial.
Further processing can present issues in the guise of inconsistencies in the final sample’s dimensions, which may then result in measurement errors.
There are also some important characteristics of the pellets to consider now the reasoning behind the shape has been outlined. A pressed disc must adhere to the following quality criteria: solidity to avoid loose particles, a homogeneous composition, storability, and stability.4
When spectroscopy is used, the content of the pellet is analyzed, so it is important to ensure that any binder does not come into contact with the primary powder. It is preferential to have a pellet that has been created without the assistance of a binder.
A flat pellet can be beneficial in additional investigations. X-ray diffraction is more effective with a solid pellet because the concentration of elements across a particular area has a higher density compared to a loose powder.
This results in a higher number of counts during the sample testing time. A smooth surface is also favored instead of a rough one from an optical perspective, as any contrasts are much simpler to observe when applying optical microscopy.
The equipment utilized to press pellets for analysis must be accurately engineered to create pellets that adhere to the previously mentioned criteria.
Carver Inc. has been formulating and producing laboratory standard presses for more than 100 years and is proud to provide a complete product range to meet various testing requirements.5
It is every researcher’s goal to verify that their pellets have been created with uniformity and consistency, but not all research environments can facilitate an identical press.
Carver Inc. responds to this need by offering a range of presses that are tailored to industry or research, whether a large run of the same powder or the production of single pellets one at a time is required.
A benchtop press should be considered for laboratories with space restrictions. They provide the same customization options and high quality as alternative presses that are larger while having a smaller footprint.
The benchtop press range from Carver has both automatic and hand-operated models, with a variety of optional features for greater customization to the task at hand.
The standard model on the manual side is available in 12, 25 and 30-ton capacities. It can be employed for tasks such as pelletizing, fluid extraction, pressure forming, destructive testing, and much more.
For the creation of pellets, which is particularly beneficial in the case of XRF or IR spectroscopy, Carver provides a selection of dies in 12, 13, 25, 31 and 40 mm sample sizes. For processing involving heat such as laminating and molding, models with heated platens that are temperature controlled are also available.
Certain tests demand a large number of samples with homogeneous shapes. Automation is a more desirable option than manual completion which can be time-consuming and tedious.
Carver additionally provides a solution for this issue, with both the standard Auto Series Plus and AutoPellet automatic laboratory presses. These models will easily sit on a laboratory benchtop, but scaled up versions are also available.
The Auto Series Plus General Purpose Presses include a large 7” color touch screen for user input. The AutoPellet is the more attractive option if a large number of pellets need to be created.
This model can be outfitted with dies of 6, 12, 13, 25, 31, and 40 mm similar to the manual version, and is available in both 25 and 40-ton varieties, with a hydraulic system that is electrically powered to control the 5" diameter platen.
The construction of the slab side is extremely rigid to ensure accurate alignment, with space for a vacuum line to be connected to the pellet die.
The AutoPellet presses have programmable decompression rates along with a programmable control system with 10-recipe storage capacity. This can modify the temperature of the platen, along with providing ramp heating capabilities, auto-tuning, and the live output of temperature and force.
Up to 250 recipes can be stored and modified with system features such as remote access to data through Wi-Fi and a seven-day timer to automatically heat platens. There is a range of Auto Series Plus press models on offer with clamping forces of 15 to 48 tons and platen sizes of 6" x 6" to 19” x 19”.
References and Further Reading
- Barsoum, M. . Fundamentals of Ceramics. (2002).
- Johnson, D. L. Fundamentals of the Sintering of Ceramics. Mater Sci Res 11, 137– 149 (1978).
- Dent, G. Preparation of Samples for IR Spectroscopy as KBr Disk. Available at: https://www.irdg.org
- Eads, A. & Miller, G. Pressing Ceramic Sample Discs. 34–35 (2019).
- Carver Inc. Products. Available at: https://www.carverpress.com/products.
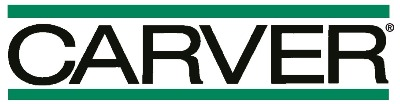
This information has been sourced, reviewed and adapted from materials provided by Carver, Inc.
For more information on this source, please visit Carver, Inc.