Application How adhesives are applied and cured depends on: • whether there is a facility to change the manufacturing process; • whether it is possible to heat cure an adhesive; • the curing mechanism of the adhesive; • time factors in the assembly process. The adhesive can be applied by either an automated robotic system, a bulk dispensing system or a portable hand held dispensing cartridge which allows the system to be mobile. Adhesives can even be applied by hand with a spatula. Which application method is chosen really depends on the volume of adhesive being used. With respect to the two part epoxies and polyurethanes, mixing and metering of exactly the right amount of component parts is vital for optimum performance of the adhesive. Equipment exists which can provide both exact metering and full mixing, as well as dispensing in exactly the right position for manufacturing of the product. In the case of heat curing either one part pastes or film adhesives, platens, autoclaves and vacuum presses may be required. Joint Design When designing an adhesively bonded joint it is not advisable to assume that the joint design should be the same as for traditional fixing methods like welding and brazing. There are characteristics of the adhesives which mean that they perform better in compression, shear and tension than in peel and cleavage. These forces are indicated in figure 1. When designing the joint it is necessary to: • maximise tension, shear and compression forces; • minimise peel and cleavage forces; • optimise the area over which the load is distributed. 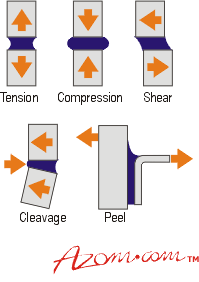 | Figure 1. The types of load experienced by a joint | The strength of a joint is a complex function of the stress concentrations set up by the load. In a simple lap joint made from thin metal sheet there are two sorts of stress: shear and peel. The shear stress varies along the length of the joint with concentrations at the ends. The peel stress acts at right angles to the lap joint and is likewise at a maximum at the ends (Figure 2). The peel stress tends to distort the joint and consequently weakens it. Alternative joint designs are presented in Figure 3. In most of these the stresses are more evenly distributed. The efficiency gained results in joints of greater strength. These joints can be applied to more complex geometries including the stiffening of large thin sheets, strengthening around apertures, bonding of multilayer structures and joints using profiles. 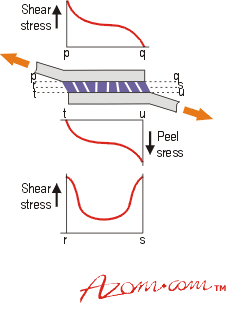 | Figure 2. Stress distributions in a lap shear joint. | 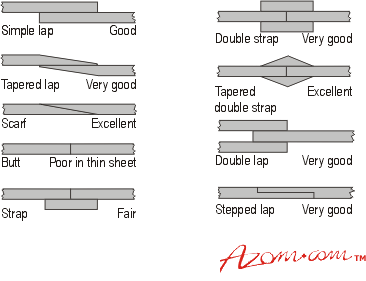 | Figure 3. Basic joint geometries. In practice, two or more may be used in conjunction with one another. | Other Specific Types Of Joints Butt Joints A straight butt joint has poor resistance to cleavage. A recessed butt joint, (figure 3) is a recommended alternative. Corner Joints Corner joints can be assembled with adhesives by using simple supplementary attachments. Typical designs are right angle butt joints, slip joints and right angle support joints. These joints increase the structure's rigidity. With this technique, thin gauge metals or sandwich panels can be easily formed. When larger gauge materials are to be joined, end lap joints are the simplest design type although they require machining. Mortise and tenon joints are excellent from a design stand point but may also require machining if a standard section is not available. A mitred joint with spline is the best if members are hollow extrusions, in this case a void filling adhesive is recommended. |