The age of the battery is well underway. For instance, lithium-ion batteries have so far transformed our everyday lives ranging from smart mobile devices to emission-free electric cars and smart power management solutions. In the future, the provision of an economical solution for mass energy storage and complement renewable energy resources for power grid applications could be possible.
Although battery technology has proven to be successful in many areas, some gaps still remain, both with regards to safety and performance. Additionally, for their mass-scale adoption in applications such as electric transportation, large reductions in cost will be required.
Undeniably, with increasingly stringent regulators and more demanding consumers, these main issues are encouraging research into new battery materials, as well as enhancements in the efficiency of production to lessen manufacture costs. It is essential for manufacturers to have the ability to guarantee total quality and performance every time when success is defined by such small margins nowadays.
Malvern Panalytical has over six decades of experience within the design, production, and supply of analytical instruments to provide a comprehensive range of laboratory and online analytical solutions. These solutions are aimed at a wide variety of businesses, from a battery component manufacturer searching for improved process efficiency and enhanced quality control, to a researcher with the aim of determining the performance parameters of novel battery materials. Malvern Panalytical can provide new levels of insight and control that is required to power the manufacture of superior quality batteries.
Monitoring and Optimization at Each Stage
It is important that manufacturers of battery components not only provide consistent overall quality, but it is necessary that they provide it throughout the production process. The continual manufacturing process results in the accumulation of errors or impurities at an early stage, leading to much greater consequences further down the line of production.
Quality must be monitored at each stage, from raw materials through to cell assembly, in order to sustain the efficiency of production and minimize waste. Similarly, research into new battery materials must ensure all the essential parameters that are possible to affect battery performance throughout the whole production process.
Malvern Panalytical has developed a variety of research and quality control solutions to assist manufacturers in monitoring and optimizing each stage of the battery manufacturing process. They provide a unique set of physical, chemical and structural analysis opportunities offered by successful technologies that can be employed across numerous stages of battery component production.
They can enable the development and manufacture of batteries with superior performance, from enhancing the quality of electrode material to speeding up the successful development of new high-performance battery materials.
Table 1. Battery materials and analytical solutions along the battery value chain. Source: Malvern Panalytical
Battery materials |
Critical Parameters |
Analytical techniques |
Product and solutions |
Cathode precursor and electrode materials |
Particle size
Particle shape
Chemical composition
Crystal phase |
Laser diffraction
Automated Imaging
X-ray fluorescence
X-ray diffraction |
Mastersizer 3000
Morphologi 4
Epsilon 4 / Zetium XRF
Aeris compact XRD |
Battery slurry |
Particle size
Particle shape |
Laser diffraction
Automated Imaging |
Mastersizer 3000
Morphologi 4 |
Electrode coating |
Coat weight
Coating thickness |
Photon sensor
Micro caliper thickness sensor |
Photon and Micro caliper
sensors from NDC technologies |
Battery cell |
Degradation mechanism during cycling |
In operando XRD |
Empyrean XRD |
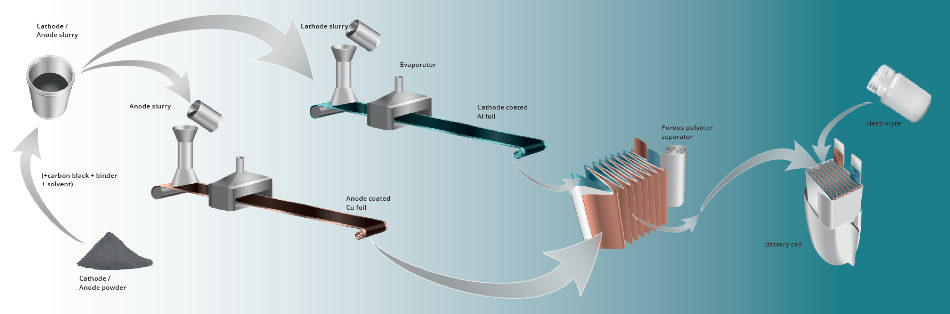
Image Credit: Malvern Panalytical
Cathode Material Optimization
The manufacture of cathode material is just one example of how Malvern Panalytical solutions empower quality at each stage of the production process. Quality control is one of the primary stages of battery production, and it is particularly important to cathode manufacturing. Battery manufacturers need to implement it all in addition to reducing costs.
Malvern Panalytical solutions can be used as cathode characterization tools at many stages of the cathode production process, from co-precipitation and precursor quality control, to enhancing calcination and the final material. By offering manufacturers morphological, structural, and elemental insights, these solutions can help them to optimize process parameters accordingly to guarantee the best cathode quality.
Cathode materials of recent interest, like NCA and NMC, are manufactured through co-precipitation of a transition metal hydroxide precursor, followed by calcination (lithiation and oxidation) with a lithium compound. Morphological, structural and elemental insights at Malvern Panalytical can help to optimize process parameters, guarantee constant quality and decrease production costs.

Image Credit: Malvern Panalytical
Characterization Tools
Particle Size
- Consistent cathode-material particle size begins with the precursor. Malvern Panalytical offers an Insitec online tool, so manufacturers can analyze particle size in real time at the precursor or milling stage.
- The quality of the electrode coating depends on the fine control over particle size distribution. The Mastersizer 3000 allows manufacturers to analyze particle size with accuracy and ease.
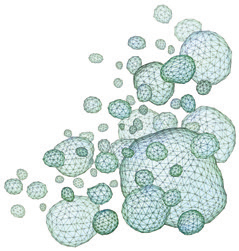
Image Credit: Malvern Panalytical
Particle Shape
- Particle shape has an effect on essential parameters like electrode slurry rheology and packing density. Morphologi 4 imaging can be used to analyze particle size and shape at the precursor stage. It is the automatic analysis of thousands of particles with highly accurate statistical outcomes.
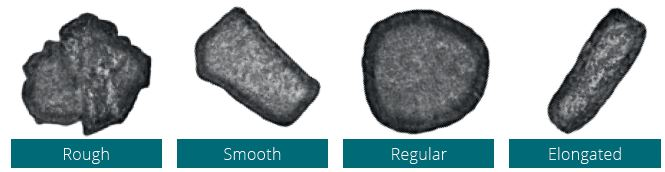
Image Credit: Malvern Panalytical
Elemental Composition
- The Epsilon 4 benchtop X-ray fluorescence (XRF) spectrometer or high-end Zetium spectrometer can simplify the chemical composition and elemental impurity analysis of electrode materials when combined with fusion sample preparation recipes.
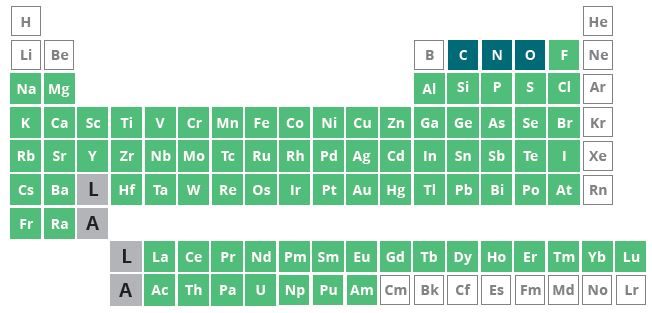
Image Credit: Malvern Panalytical
Crystalline Phase
- Crystalline phase, in addition to crystallite size are the main characteristics defining the quality of electrode materials. The Aeris compact X-ray diffractometer by Malvern Panalytical sets the benchmark in this industry for crystalline phase composition analysis. This can be utilized to optimize the calcination process.
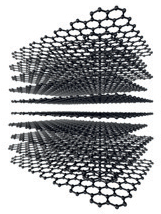
Image Credit: Malvern Panalytical
Zeta Potential
- It is possible to use zeta potential to optimize process parameters such as pH and concentration to control slurry stability, agglomeration, and sedimentation behavior. The Zetasizer can be used to analyze zeta potential of a dispersion and, as well as the size and agglomerate state of nanosized materials.
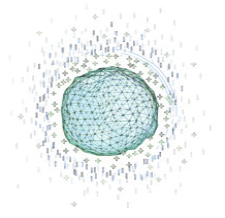
Image Credit: Malvern Panalytical
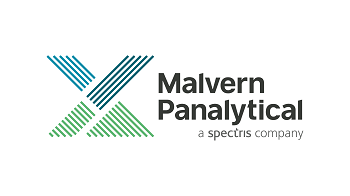
This information has been sourced, reviewed and adapted from materials provided by Malvern Panalytical.
For more information on this source, please visit Malvern Panalytical.