In this interview, AZoM talks to Christine Desplat, an R&D engineer at Master Bond Inc., about the testing Master Bond does to discover an epoxy's resistance to bases.
What variables should be considered to determine if an adhesive is chemically resistant?
Typically, adhesives have potential chemical vulnerabilities that can result in a loss of physical performance properties. There are so many variables to consider such as what substrates, adhesives, and chemical agents are involved in an application. The possible combinations are endless. In addition, the type of exposure involved and other operating conditions must be taken into account.
What are the different types of chemical exposures?
Exposures should be characterized by the intensity of contact with a chemical agent. Low-intensity exposures are best thought of as a splash. Higher intensity exposures would involve immersion that could be intermittent or continuous. Chemical exposures should also be considered in the context of the application’s thermal and mechanical loads. Many adhesives can experience an incremental loss of chemical resistance at elevated temperatures—especially above the Tg. High stresses also exacerbate any adverse effects that a chemical agent has on adhesive or cohesive strength.
What tests measure chemical resistance?
There are dozens of ASTM and industry-specific tests that attempt to capture chemical interactions. Keep in mind that testing can only approximate real-world conditions. Also, many accelerated test regimens may even be more aggressive than real-world applications. Some military tests for example subject adhesives to immersion in fuels and hydraulic fluid for one week and to high-humidity conditions for 30 days. Such aging tests may be conducted despite there being limited to no exposure to such conditions, but it gives engineers the peace of mind to be able to design a more robust device, capable of lasting many years in the field.
How does Master Bond test adhesives?
Master Bond relies on its own unique database of long-term exposure data. Some of this chemical exposure data comes from immersion tests that have even lasted for years. Our long-term data covers many combinations of adhesives and chemicals—including many organic and inorganic acids, alcohols, chlorinated compounds, hydrocarbons, solvents, and more.
A common way of testing chemical resistance of an epoxy is immersing a sample in a chemical and measuring its change in weight over time. A significant loss or gain in weight would indicate a decreased ability of a material to stand up to chemical exposure. These tests allow us to more accurately recommend the right adhesive based on specific application requirements.
What bases did Master Bond use to test their epoxies’ resistance?
50% Sodium hydroxide (NaOH) and 45% Potassium hydroxide (KOH), two of the most common base solutions, were used to test Master Bond epoxies EP62-1HT, EP42HT-2, EP39MAOHT, and EP42HT-2AO-1 Black. A few thin castings, roughly 2 inches in diameter and around 0.125 inches thick were made for each product and cured in accordance with their specifications. Most epoxies selected here needed a moderate amount of heat ~ 60-100 C to be added during the curing/post-curing process. Once the cured samples were created and the initial weight was recorded, they were submerged in NaOH and KOH for 37 weeks. Weekly weight measurements were recorded to see the percentage of weight change over time. These epoxies were measured against a casting of a standard/off the shelf two-component room temperature curable epoxy that was not formulated for chemical resistance, under the same conditions.
What were the results?
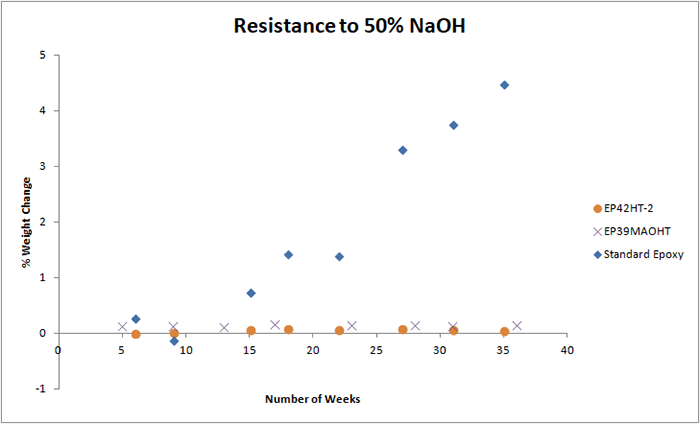
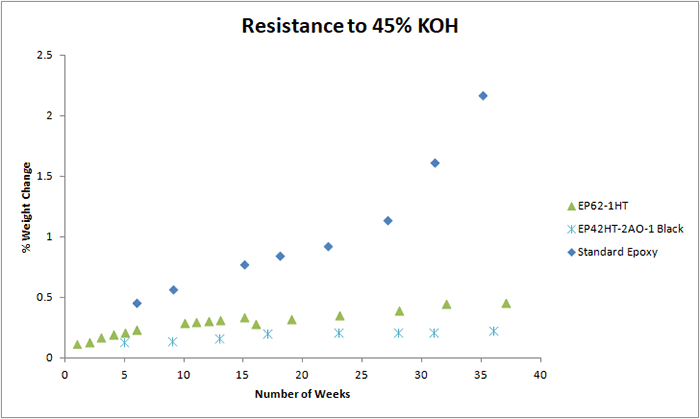
As depicted in the graphs, the standard epoxy was not as resistant to the bases as the other epoxies tested, considering that it demonstrated a significantly higher weight gain over time. In general, a swelling of less than 1% can be considered excellent, especially since this test may be more rigorous compared to actual service conditions. It is also worth noting that in the context of a bonded joint or a potted assembly the exposure to bases might not be as severe or direct, as in the above test conditions.
About Christine Desplat
Christine Desplat is an R&D Engineer at Master Bond where she analyzes application-oriented issues and provides product solutions for companies in the aerospace, electronics, medical, optical, and oil/chemical industries. She received a Bachelor's Degree in Chemical Engineering from Rensselaer Polytechnic Institute.
Disclaimer: The views expressed here are those of the interviewee and do not necessarily represent the views of AZoM.com Limited (T/A) AZoNetwork, the owner and operator of this website. This disclaimer forms part of the Terms and Conditions of use of this website.