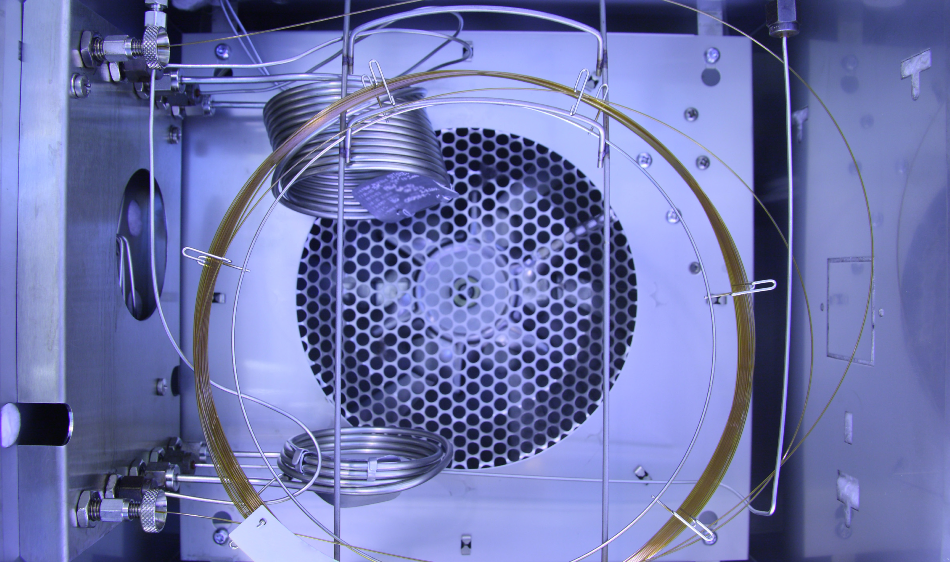
Ultra-Small Diameter (USD) capillary tubing plays a key role in terms of enhancing the performance of liquid chromatography and related microfluidics instrumentation. Industry leaders operating at the boundaries of hi-tech chromatography demand faster productivity and efficiency from the equipment they use, they also require accurate results of the highest caliber.
USD tubing offers competitive advantages due to it being able to withstand high working pressures while maintaining an inside diameter that is both clean and smooth (low surface roughness).
However, unique challenges arise when trying to accomplish these properties as the outer diameter (OD) of the tube drops to USD sizes (less than 0.0625 inches). This article explores these challenges as well as the manufacturing solutions used by HandyTube to control any issues in order to produce high-quality USD tubing.
ID Surface Roughness
Ultra-small diameter tubing installed into laboratory equipment, medical devices, and other applications requiring accuracy and care must have a smooth ID surface finish to guarantee high-purity delivery of chemicals, solvents, gas, and other media. Determining proper ID smoothness is two-fold: firstly, how the tube is first drawn, and secondly, skilled engineering proficiency of the manufacturing supplier.
Throughout the manufacturing process, drawing, which narrows the tube’s dimensions, is one of three main functions that occur. The others are cleaning, to eliminate drawing lubricants, and heat treatment, to reset the mechanical properties and ready the tube for redrawing. There are two main types of drawing operations:
- Floating plug. Tubing is pulled through a conical die with a floating plug in the ID. Importantly, the die and the plug regulate the drawn OD and ID. This form of drawing requires more tooling and lubrication than other methods, but it produces tubing with more accurate dimensions and a smoother surface finish.
- Sink drawing. This method does not utilize internal support, unlike the floating plug drawing. Throughout this process, tubing is pulled through a conical die, lessening the inside and outside diameters. The resulting ID is resolved by multiple factors, including the die angle, drawing stress, and the inner and outer diameters of the stock tube.
Acknowledging the necessity for reduced tubing dimensions and smoother ID surfaces, HandyTube has enhanced proprietary tube drawing processes and developed equipment that can draw stainless steel in coil form. The results are dependable flow rates and rapid sampling cycles in HPLC applications. Supporting the ID in the later stages of the drawing process and holding tooling to strict standards produces surface finishes as smooth as 20 Ra.
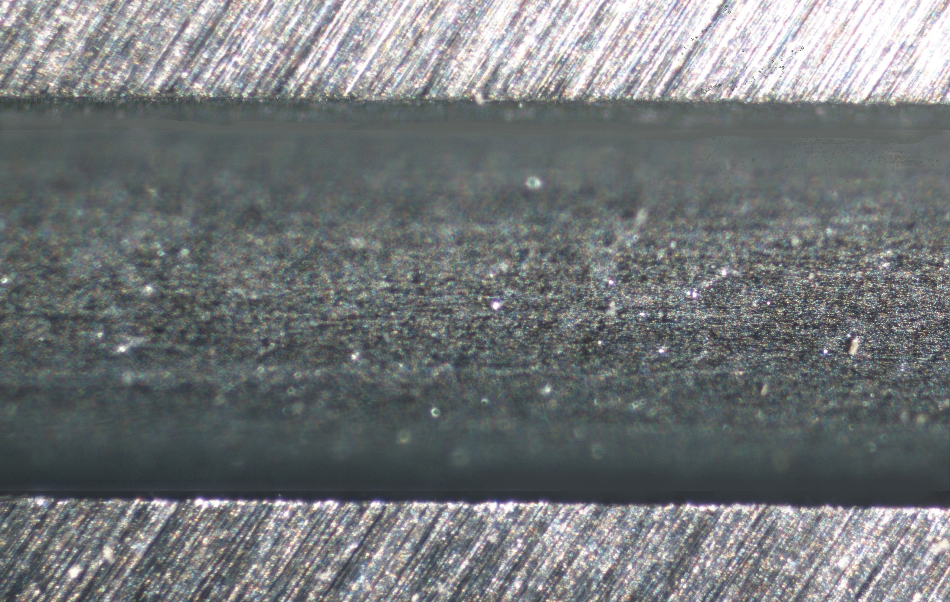
ID Cleanliness
Problems can arise causing impurities in USD tubing, these include a build-up of grease, oil, and other foreign material left over from the manufacturing process which can lead to cross-contamination and imprecise sample readings for the end-user. To mitigate these issues, supplementary cleaning is necessary prior to the installing of conventional tubing.
Determining an effective method to clean long lengths of stainless-steel tubing which has tiny diameters presents a sizeable challenge for most end users. Furthermore, as the tube lengthens and the ID narrows, the pressure necessary to drive any media through the coil tubing greatly increases.
Consequently, ordinary cleaning methods and equipment are not fit for purpose when it comes to cleaning high-precision USD tubes. HandyTube’s exclusive cleaning processes can successfully degrease USD coil tubing several hundred feet in length. Following the drawing of a tube, lubricant on the outer diameters is eliminated by HandyTube’s degreasing process.
The tube is then exposed to high pressures to get rid of ID lubricants. Thus, the processing of small-diameter tubing in long coils is facilitated by specialized cleaning equipment. HandyTube’s capacity to clean in coil form substantially reduces the amount of time required by OEMs and end-users for cleaning, as each length would otherwise require individual flushing.
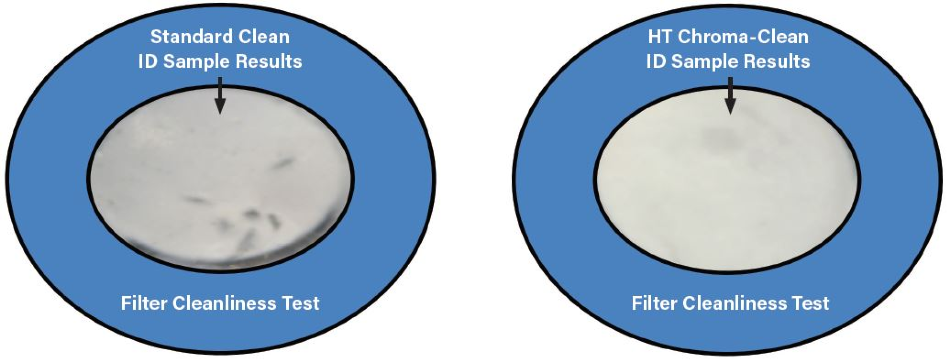
Seamless Advantage
Welded tubing is fabricated from a strip of metal that is rolled into a tube shape and then longitudinally welded. Seamless tubing, however, contains no longitudinal weld seam, as inferred in its name: rather, tubing is expressed from a billet and drawn to finish.
Across a range of industries, including producers of medical devices and processing equipment, require seamless small-diameter tubing, which typically has outer diameters between 0.018 and 0.0625 inches, for manufacturing processes. Seamless tubes remove all the possible risks relative to weld seams including; off-seam welds; stress concentrators in high-pressure applications; inclusions; and contamination of the weld.
Therefore, industry standards regard seamless tubes at a higher working pressure than welded tubes of the same size. Over time, this high-pressure capability proves to be indispensable as end-users require smaller ID sizes, increasing the amount of pressure needed for media to flow.
Measurement Quality
Physical gaging can often be problematic when measuring the inside diameter (ID) size due to the small dimensions of USD tubing. The ID becomes increasingly starburst-shaped as the tubing is drawn to smaller sizes. This distinct geometry leads to unreliable results when pinned with circular gauge pins to measure ID size. HandyTube utilizes a wide range of proprietary measuring techniques to make sure that these variations in geometry are accounted for.
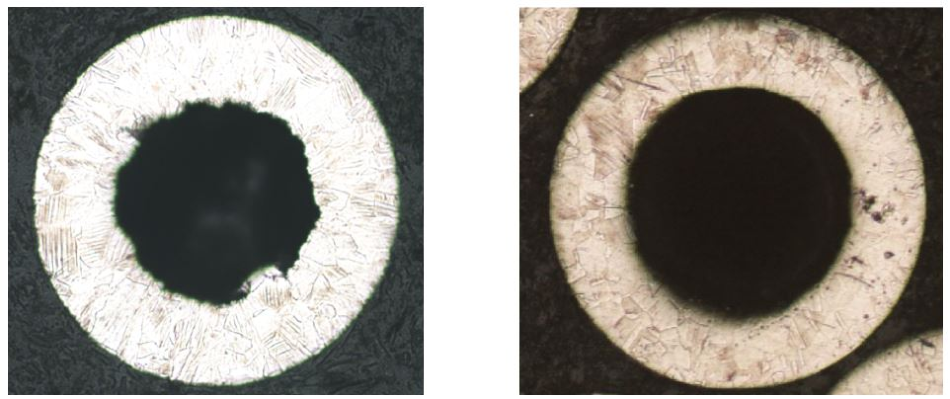
Alloys
Relative to small-diameter tubing, the most widely used stainless-steel alloys are the 300 series, available in an array of corrosion-resistant types and sizes. These alloys are composed of nickel, chromium, titanium, and molybdenum and are the perfect choice for seamless coil-tubing applications. They are capable of standing up to high pressures and temperatures. Some specific types include:
- Type 304/304L. Corrosion-resistant and non-magnetic, this alloy is the most popular of all the stainless steels. It has supreme weldability and forming characteristics and can withstand fairly aggressive organic acids, including acetic acid and reducing acids.
- Type 316/316L. More resistant to chemical attack and intergranular corrosion (IGC) than 304. This alloy has increased corrosion resistance due to the addition of 2-3% molybdenum and is especially effective in high chloride/saline environments.
- Type 321. While this alloy is similar to 304, in terms of chemical composition, it holds at least six times the amount of titanium equal to the combined Carbon and Nitrogen content. The introduction of titanium makes alloy 321 perfect for operating at temperatures greater than 800 °F.
- Type 347. This alloy offers better corrosion resistance than type 321 in strongly oxidizing environments because of the additions of columbium and tantalum. Even when exposed to environments between 800 ºF (427 ºC) and 1,650 ºF (899 ºC), 347 maintains its enhanced corrosion resistance.
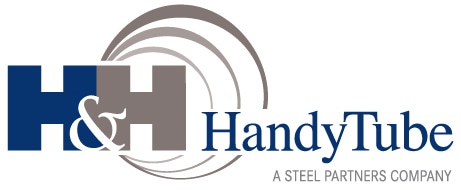
This information has been sourced, reviewed and adapted from materials provided by HandyTube.
For more information on this source, please visit HandyTube.