Crisp packets drink pouches and even dog food packaging is manufactured from numerous polymer layers that have been stuck together with glue to optimize the packaging’s barrier and mechanical properties.
Conventional Lamination Adhesives employed in multi-layered flexible packaging are generally a product of solvent-based or solvent-free two-pot systems that have undergone the reaction below:
Polyol (-OH) + Isocyanate (-N=C=O) → Polyurethane lamination adhesive (-NHCOO-)
Traditionally, the packaging industry has utilized FTIR to screen test the decay rate of isocyanate (NCO) in a freshly applied adhesive. This approach has been vital because unreacted aromatic NCO molecules can migrate through laminated packaging into food. If this happens, these molecules have the potential to react with water molecules, generating carcinogenic primary aromatic amines that can be harmful to both humans and pets.
Obtaining measurements of the reduction of NCO absorbance peak height overtime at ~2270-2250 cm-1 allows this decay to serve as an indication of both adhesive curing speed and food packaging safety. The spectra shown below have been taken over time from a single solvent-free adhesive on a single Arrow slide:
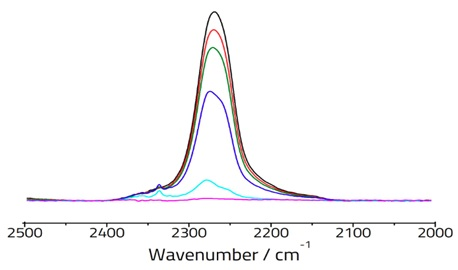
Figure 1. The decay of NCO in absorbance mode over time in a two-pot packaging adhesive at standard mix ratio.
It is also possible to use multiple Arrow Slides to compare the curing speed of different adhesives simultaneously. Adhesive curing speed has numerous variables including OH to NCO mix ratio, relative humidity, curing temperature, the crosslink-ability of starting components, and also the reactivity of the aromatic NCO component.
The curing process can sometimes take days or even weeks, so occupying a single conventional crystal ATR puck for extended periods of time is rarely prudent. High volume batch sampling utilizing Arrow consumable ATR Slides is a far better alternative, saving time, speeding up work, and ultimately making an organization more competitive.
Once the polyurethane product is formed on a crystal, it will likely be challenging to remove. The adhesive is, of course, designed to stick, so this process risks damaging a comparatively more expensive crystal puck.
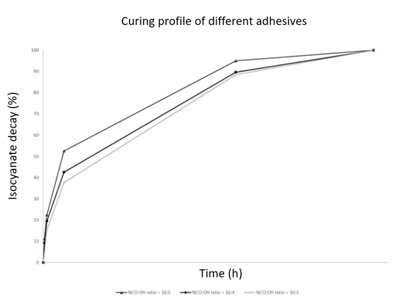
Figure 2. Curing speed of adhesives at different mix ratios.
Overall, the use of Arrow consumable ATR Slides in the analysis of packaging adhesives offers a number of clear advantages. They are ideal when working with irreversible reactions - once a polyurethane thermoset has cured, it will not revert to its original components and will be hard to remove.
There is no need for sample preparation. Conventional FTIR transmission methods necessitate lamination - either by machine or by hand - and these processes are time-consuming while also wasting packaging substrates. Arrow negates the use of hazardous cleaning solvents, as no lamination is required. It also allows multiple samples to be monitored in an inexpensive way.
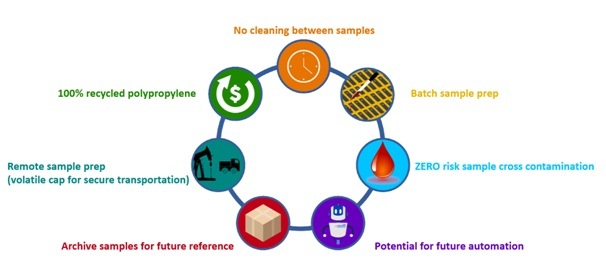
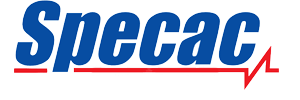
This information has been sourced, reviewed and adapted from materials provided by Specac Ltd.
For more information on this source, please visit Specac Ltd.