Unstable and uncontrolled processes account for most financial drains in the injection molding process. Between 60 and 70% of all molding errors can be traced back to the tempering of the injection mold, with these being responsible for unacceptably long cycle times and inadequate quality.
Employing a combination of compact Optris infrared cameras and an IR-ThermoControl online quality control system (explicitly developed for plastics processing Plexpert GmbH and GTT Willi Steinko GmbH) ensures that thermal errors occurring in the injection molding process may be detected at source or “inline”.
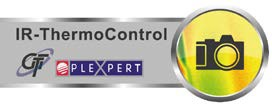
Data transfer to IR-ThermoControl is made possible thanks to the PI Connect software. This central element allows the process technician, fitter, and quality leader to manufacture quality components in a safe, rapid, and target-oriented fashion while ensuring the shortest possible cycle times.
If targeted measures are to be taken effectively, it is essential to be aware of where the causes of problems tend to be found.
Common Thermal Problems and Their Causes
Appearance |
Thermal problem classification |
Most common cause |
Dimensional problems, poor mechanical performance |
Excessive temperature deviations in the mold wall |
Asymmetrical cooling channel layout, insufficient heat dissipation, bridging of cooling channels |
Molding warpage |
Excessive temperature deviations in the mold wall, partially or over the entire molding |
Asymmetrical cooling channel layout, insufficient heat dissipation, bridging of cooling channels |
Surface markings in the form of shiny and matt patches, feathering |
Thermal moldings of inserts and ejector pins, mandrels, retainers, ribbing and apertures |
Insufficient heat dissipation, inadequate isolation of hot runner systems and hot runner nozzles, untempered molding lots |
Excessively long cooling times/cycle
times |
Poorly configured tool tempering, significant pressure losses within the tempering system, hotspots on the molding |
Blocked cooling channels, the inadequate technical condition of tempering and cooling equipment, aggressive condition of water, untreated or insufficiently treated water |
The IR-ThermoControl system provides information on potential problems, even showing intermittent effects and trends such as a slight temperature increase occurring during serial production. This system is easy to install on any injection molding machine and can be fitted in under 5 minutes, allowing for unmatched availability and flexibility.
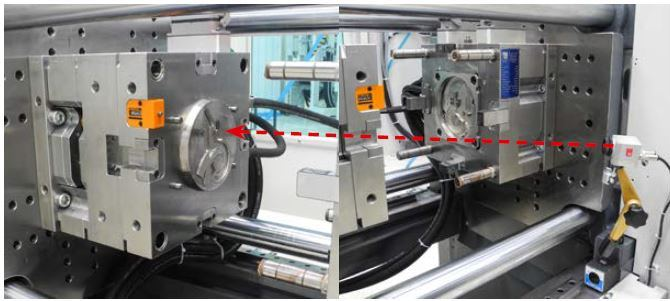
Positioning the infrared camera in the tool installing area.
The user guidance is process-oriented, allowing control limits to be defined and automatically providing information on temperature deviations via a reference image system. This approach allows for any differences that occur to be seen instantly.
Initially, the IR-ThermoControl quality module generates an image of the molding in every cycle. Next, a reference image is created of the first good part. Each subsequent recording is then compared with this reference image, and if a deviation is detected at any point then an alarm will be sounded. This technology is employed in both 2K injection molding, and combined foam/compact injection molding (Krallmann Pilot Werkzeug GmbH).
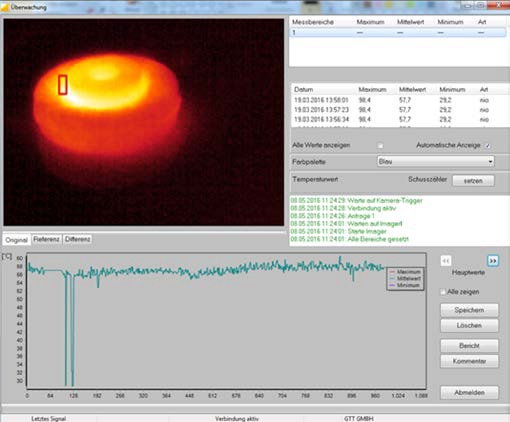
Analysis mask with IR-ThermoControl temperature graphic.
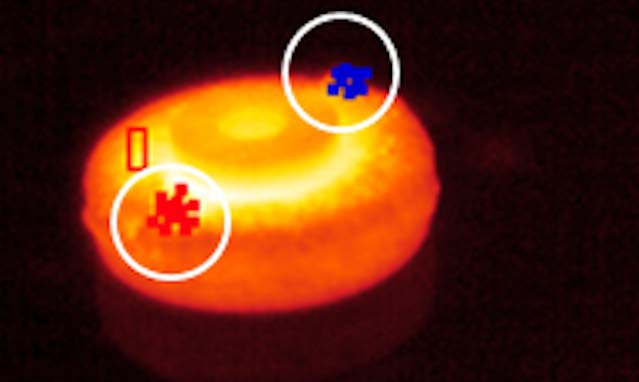
Red zones indicate an exceedance of the threshold value, blue zones indicate a shortfall.
In this particular application in the automotive sector, any errors in the process are visible immediately. The application outlined below displays a thermal weak point that occurs during production. The zone shown on the left displays a lower surface temperature than the zone on the right.
Here, the length of the manufactured component was approximately 2.5 mm shorter than specified, and the dimensional deviation resulted from the required dwell pressure not being reached. The tool tempering was adjusted in this zone to optimize the process.
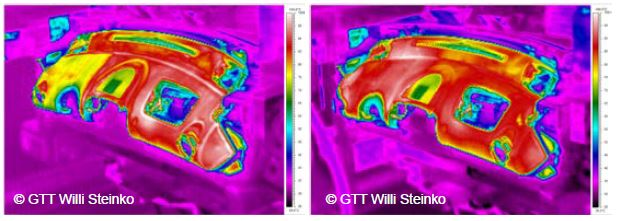
Before: clearly identifiable thermal weak points. After: thermally optimized component.
A Look Into the Thermal Future
The IR-ThermoControl’s “Plug and Work” system reveals thermal deficiencies more effectively than any other technical instrument; for example, temperature differences on injection molded components and tools which are found to be too high are displayed in a clear and concise fashion.
The staff that are responsible for production must be mindful of price and quality, and continuous use of IR-ThermoControl will enable them to monitor and control processes both economically and efficiently.
Finally, there is no need to put staff at risk by touching the surface of the component or tool by hand in order to locate warm, hot or cold zones.
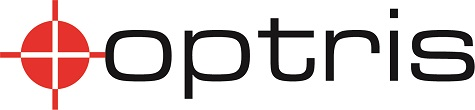
This information has been sourced, reviewed and adapted from materials provided by Optris GmbH.
For more information on this source, please visit Optris GmbH.