A large concrete and construction company based in the Midwest of the United States had an issue with limited visibility of inventory control at their primary dispatch.
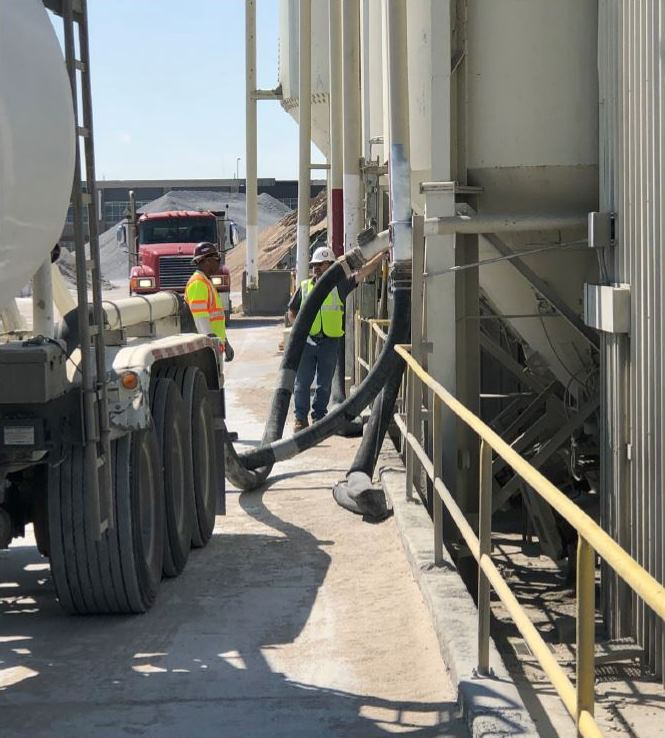
Image Credit: BinMaster
Constant silo climbing and dropping of tape measures led to a time-consuming and inaccurate process that had to be managed by the concrete suppliers’ workers, even before considering the potential safety hazards posed by this approach.
Centralized Monitoring was Needed
Dispatch required real-time inventory oversight of ten local plants and a number of other remote plant locations, in order to meet the demand for fly ash and cement powder. Improving logistics between the cement plant itself and the batch plants was vital if all locations were to run efficiently.
The two full-time members of staff were overwhelmed, as it was their job to schedule and route all the trucks for the ten local plants located around the metropolitan area, as well as the trucks for the remote plants. BinMaster was ready for this challenge, and was able to work with the company to help it manage this complex logistical issue.
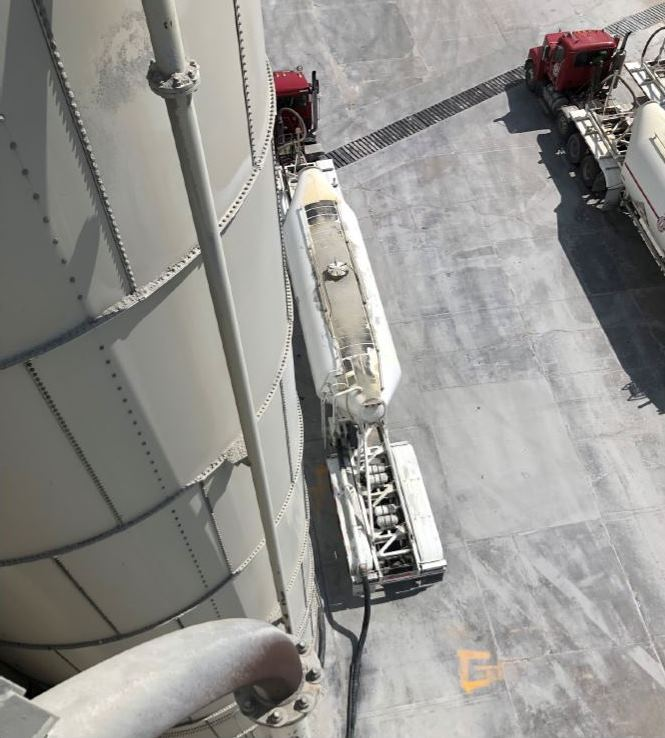
Image Credit: BinMaster
Logistical Challenges
Each of the batch plant locations managed between five and eight silos of Type I cement powder, fly ash and IPF, and each had to be filled with these raw materials. The fly ash for the series of ten plants was primarily provided by a nearby power plant, while the Type I cement powder and IPF were ordered from a single cement plant.
The company’s trucks held approximately 32 tons of material per load. It was imperative that all of the material could fit into the silos when the trucks made a delivery, so staff had to ensure that there was sufficient space for the truck’s entire contents to empty into the silo.
Effective coordination of all of these variables was critical in order to prevent the company from losing both money and time.
Non-Contact Radar Relief
To allow continuous measurement of silo levels with no need for climbing, BinMaster’s Nathan Grube recommended using 80 GHz non-contact radar level sensors. Maintenance staff at the plants were able to pre-wire the silos themselves, so these were ready to accommodate sensor installation.
BinMaster technical services could complete the commissioned work in a day or two per location, and over time, NCR-80 sensors were successfully fitted in 58 silos along with the rotary level indicators that were to be employed as redundant high-level alerts.
Because the silos rapidly fill up in as little as four to five hours, DPM-100 digital panel meters were installed to report headspace levels. A BinCloud® gateway allowed data to be communicated from the sensors to the panel meters with no need for extensive wiring.
Custom cabinets now house several digital panel meters, allowing access to silo data from a central location.
Now, the two main truck drivers, or indeed anyone working at the plant, can check silo headspace at any time. This allows drivers to confidently load silos and empty trucks, assured that the material will fit.
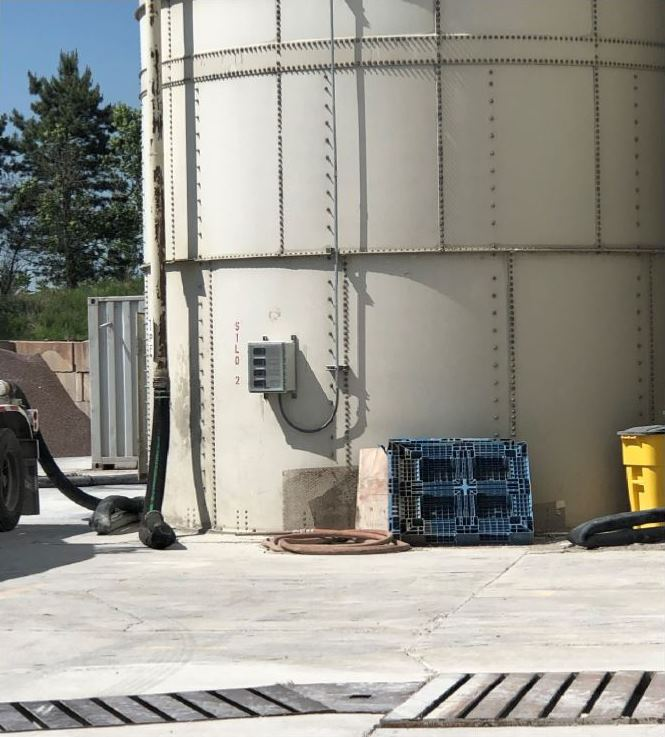
Image Credit: BinMaster
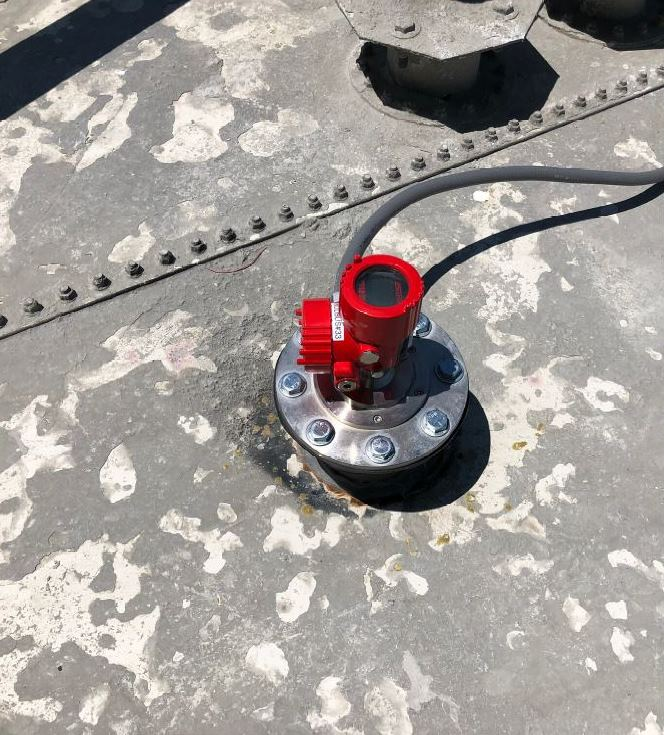
Image Credit: BinMaster
Software Takes the Solution Full Circle
Real-time views of inventory levels at each individual batch plant were vital to keep pace with the rapidly changing silo levels. The corporate headquarters dispatch location was provided with access to a BinView® remote monitoring website, and this was also made available at each of the plants.
With all staff viewing the same data, inventory discrepancies became a thing of the past. Drivers, dispatchers, and plant managers can now set priorities while reducing out-of-stocks and delivery emergencies - issues that waste time, adversely affecting profits and schedules.
The BinView® software lets dispatchers monitor and order materials for several locations, while plant managers now have easy access to inventory information for their location as required. Users can view and sort bins by material, as well as being able to set automated alerts, examine trends, and generate detailed usage reports.
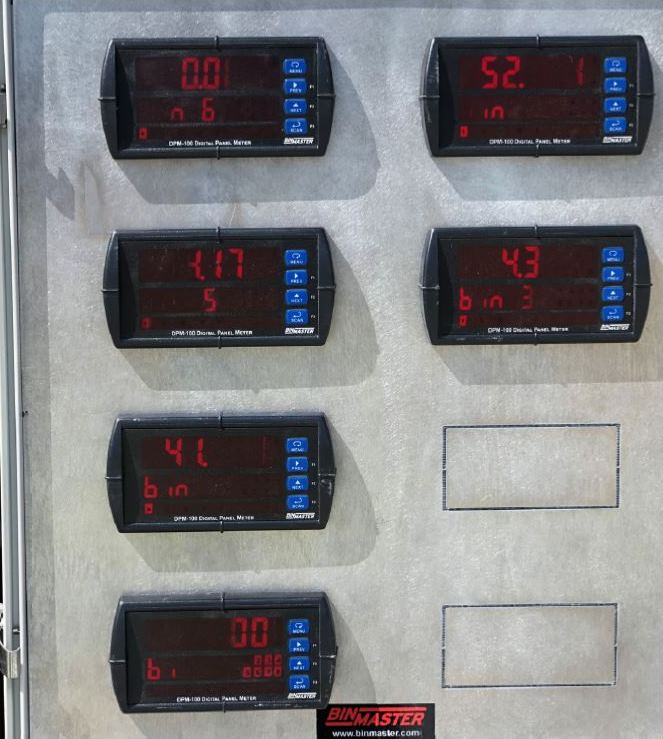
Image Credit: BinMaster
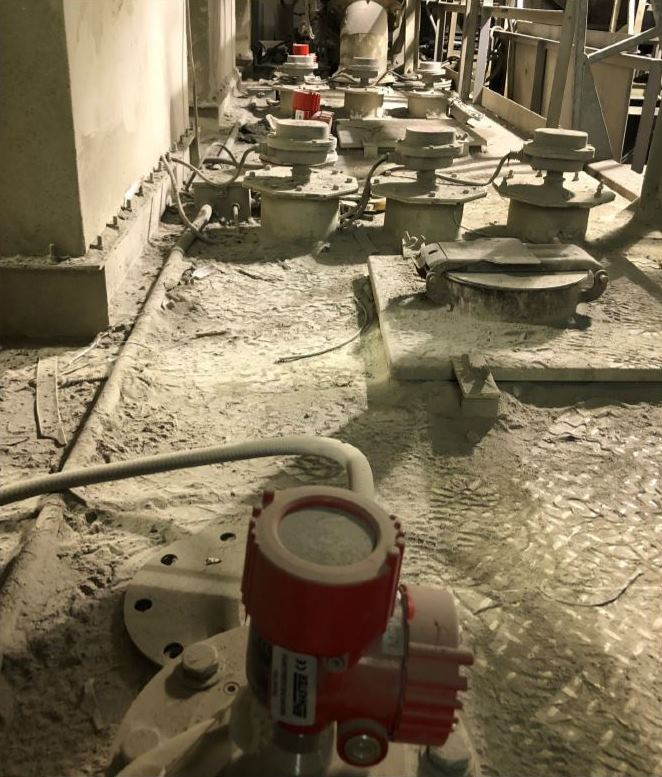
Image Credit: BinMaster
Rock Solid Results
The concrete company had said that they, “couldn’t afford to run out or risk messy overfills.” Thanks to BinMaster’s products, staff no longer have to manage the risk of climbing outdoors, in weather that can be very hot, cold or windy in a location like the Midwest. Staff at the cement supplier also said that they “really like the visualization of what’s going on.”
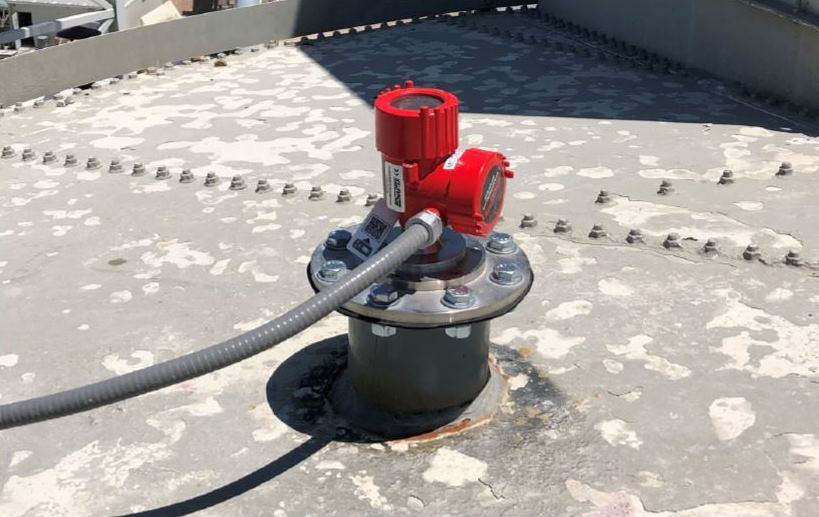
Image Credit: BinMaster
They can look at data for all locations, just one location, or just bins that need to be filled. And since the plants are so active, they get updates every 10 minutes. Younger people recognize the value of technology, while plants are faced with trying to do more work with fewer people.
Nathan Grube, Binmaster
Acknowledgments
Produced from materials originally authored by Nathan Grube from BinMaster.

This information has been sourced, reviewed and adapted from materials provided by BinMaster.
For more information on this source, please visit BinMaster.