On-line particle size analysis during the production of alumina has enhanced throughput by 50% and achieved return-on-investment within 12 months by eliminating the requirement to reprocess ‘out of spec’ material identified during post-treatment analysis.
Small, gradual enhancements in process efficiency are often highly beneficial for high-tonnage processes. This article discusses the impact of using on-line particle analysis on the efficiency of aluminum production.
The role that particle size distribution performs within this the process is outlined and the advantages that can be gained by enhancing particle size control are demonstrated. A case study is also presented which details the experience of an aluminum producer changing from off- to on-line analysis.
Bauxite Refining
As with a number of metals, aluminum is extracted from its ore by initially concentrating the ore mineral utilizing a process that involves mechanical size reduction with a chemical treatment afterwards (Figure 1).
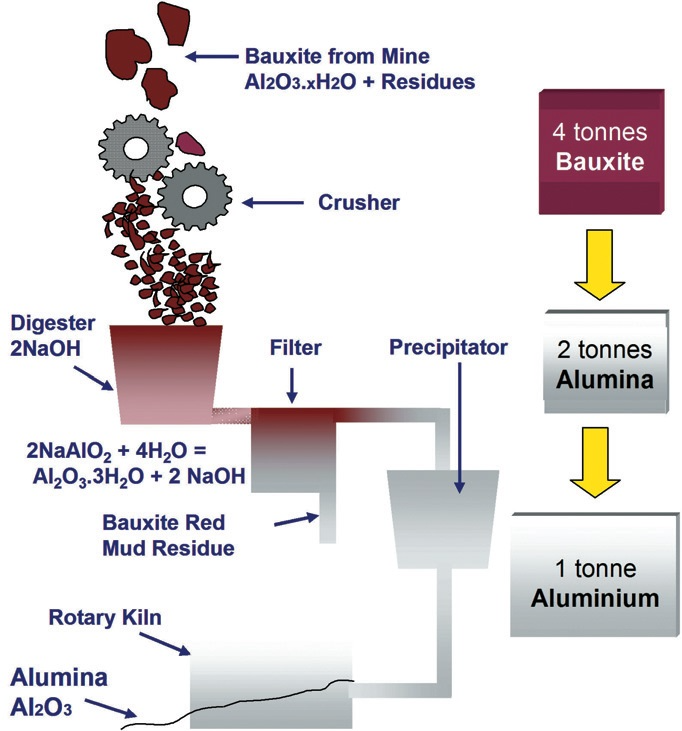
Figure 1. Refining alumina from bauxite ore. Image Credit: Malvern Panalytical
The bauxite ore is first crushed and ground into fine particles which are then combined in autoclaves with a caustic soda solution. Aluminum oxide dissolves while impurities within the ore remain in a solid state in the autoclaves, which function at temperatures in the range of 200 to 240 ºC and at pressures of up to 30 bar.
The insoluble impurities are removed and discarded after additional pressure filtration and scrubbing steps which leaves a relatively pure solution for further processing. Precipitator tanks seeded with pure alumina trihydrate are then used to house the aluminate solution.
Agitation and cooling moves the dissolved material out of solution and settling and vacuum filtration steps are used to separate the subsequent trihydrate solids from the caustic soda.
Long rotating furnaces operating at a temperature of approximately 1000 ºC to are used to calcine the recovered crystals to exclude all water, which creates a white powder (calcined alumina) that is formed into aluminum metal during the process of smelting.
The Hall-Heroult electrolytic system is employed to create aluminum from the calcined alumina. A bath of molten cryolite (sodium aluminum fluoride) is used to dissolve the alumina, through which a high electric current is passed (normally 150 000-350 000 ampere).
Consisting of petroleum coke and pitch, a carbon anode is fixed in the pot and the cathode is a thick graphite or carbon lining of the vessel. At the base of the vessel, molten aluminum is deposited and periodically siphoned off to a holding furnace for future casting.
Download the Full Whitepaper
Acknowledgments
Produced from materials originally authored by David Pugh from Malvern Panalytical Ltd.
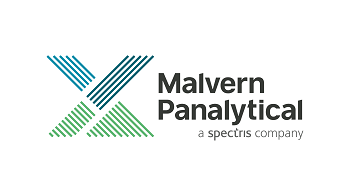
This information has been sourced, reviewed and adapted from materials provided by Malvern Panalytical.
For more information on this source, please visit Malvern Panalytical.