Plastic materials have been utilized in diverse products in a broad range of fields in recent years. Some of these include not only automotive parts such as bumpers, but also medical materials, daily commodities, sports products, and packaging.
One vital feature of plastic is the fact that products with a wide range of hardness properties can be created, from hard products like machine parts to soft materials.
As the mechanical properties and physical properties of plastic materials can be measured in a simple and easy manner, hardness testing is effective in both research and development and quality control. On the other hand, the issues below arise in Rockwell hardness tests of plastics.
With thin-film specimens and small specimens the correct measurements are not possible due to the large force. In addition, when the thickness is below 6 mm, depending on the material different scales are utilized and simple comparison by numerical values of hardness is not possible.
In order to address these challenges, ISO/TS 19278 was issued in 2019 as a method for the measurement of the indentation hardness of plastics.
Hardness testing of even small specimens and thin-film specimens is possible as specimens are measured at a low force, and hardness is assessed using the same scale, irrespective of the type of material.
This article introduces hardness testing conforming to the above-mentioned standard (ISO/TS 19278:2019) by the Shimadzu DUH™-210 Dynamic Ultra Micro Hardness Tester for plastics using representative plastic materials.
Introduction of Standard
Under the ISO/TS 19278:2019 standard, a hardness tester conforming to ISO 14577-1 (Metallic Materials – Instrumented indentation test for hardness and materials parameters – Part 1: Test method) is needed.
This is a hardness tester that can measure the indentation depth and force in real time, and can assess the surface properties of the specimen. Using this instrument, indentation hardness is calculated from the results of one load/unload process.
As shown in Figure 1, in the graph of the force and indentation depth at this time, the contact depth is calculated from the maximum depth and the tangent at the start of unloading, and the value is acquired by dividing the force Fmax by the projected area Ap calculated from this contact depth is defined as indentation hardness HIT. The main test conditions of ISO/TS 19278 are shown in Table 1.
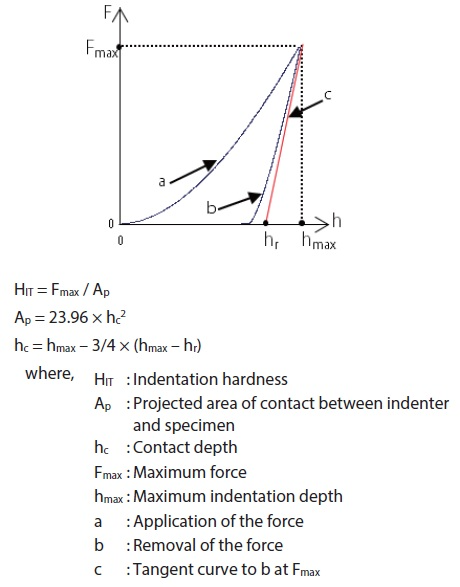
Figure 1. Definition of Indentation Hardness HIT. Image Credit: Shimadzu Scientific Instruments
Table 1. Main Test Conditions of ISO/TS 19278. Source: Shimadzu Scientific Instruments
. |
. |
Maximum force |
500 mN |
Loading time |
30 s |
Unloading time |
30 s |
Holding time at maximum force |
40 s |
No. of test cycles |
Min. 5 |
Samples and Test Conditions
The specimen information utilized in the measurements can be observed in Table 2. PP, HDPE, ABS/PMMA, and PS were chosen as representative plastics. The test conditions are shown in Table 3, and Fig. 2 shows the appearance of the DUH-210 Dynamic Ultra Micro Hardness Tester for plastics.
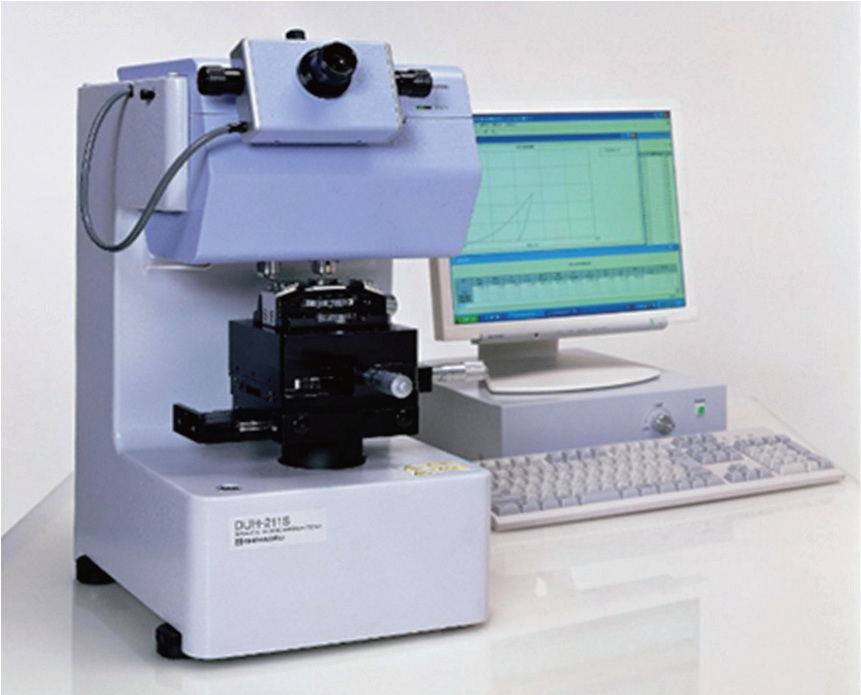
Figure 2. Appearance of Plastic Hardness Analyzer (Dynamic Ultra Micro Hardness Tester for Plastics DUH™-210). Image Credit: Shimadzu Scientific Instruments
Table 2. Specimen Information. Source: Shimadzu Scientific Instruments
. |
. |
Sample name |
PP, HDPE, ABS/PMMA, and PS |
Sample geometry |
Rectangular solid, 20 mm × 10 mm × 3 mm |
Table 3. Test Conditions. Source: Shimadzu Scientific Instruments
. |
. |
Instrument |
Plastic hardness analyzer
(Dynamic Ultra Micro Hardness Tester for plastics DUH-210) |
Room temperature (°C) |
23 ± 2 |
Humidity (%) |
50 ± 10 |
Upper pressure indenter |
Berkovich indenter (diamond) |
Test mode |
Load/unload test |
Test force (mN) |
500 |
Loading/unloading time (s) |
30 |
Holding time (s) |
40 |
No. of test cycles |
5 |
Test Results
Figure 3 shows the hardness test results (average values) and error ranges, Table 4 shows the hardness test results (average values), and Figure 4 shows the force-depth curves.
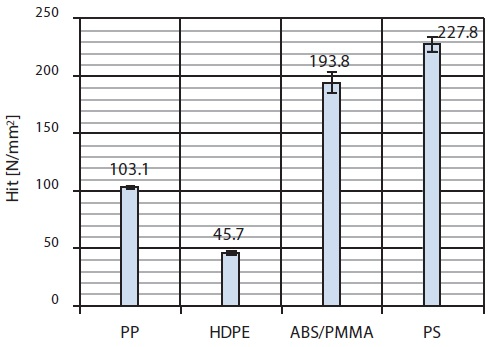
Figure 3. Hardness Test Results (Average Values) and Error Ranges. Image Credit: Shimadzu Scientific Instruments
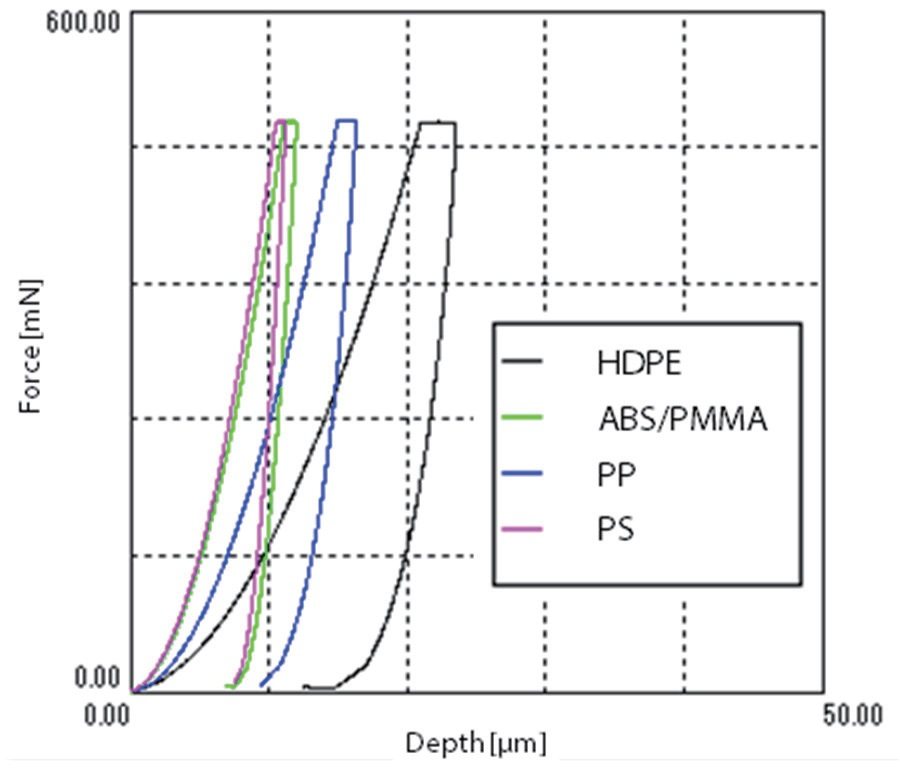
Figure 4. Force-Depth Curves. Image Credit: Shimadzu Scientific Instruments
Table 4. Hardness Test Results (Average Values). Source: Shimadzu Scientific Instruments
Sample |
Force
[mN] |
Depth
[μm] |
Indentation hardness HIT
[N/mm2] |
Standard deviation |
PP |
502.3 |
16.4 |
103.1 |
1.59 |
HDPE |
502.2 |
23.5 |
045.7 |
0.87 |
ABS/PMMA |
502.1 |
12.1 |
193.8 |
8.74 |
PS |
502.2 |
11.2 |
227.8 |
6.15 |
The indentation ranged from 11.2 μm to 23.5 μm at a load of around 500 mN, and results showing hardness values of 45.7 to 227.8 were gathered with these sample materials. As for the order of hardness, the results demonstrated that the hardest material was PS and the softest material was HDPE.
Conclusion
A standard for hardness testing as a method for the easy measurement of the physical and mechanical properties of plastic materials was introduced in this article.
Through deliberations with the related countries based on a Japanese proposal, this standard was established in 2019, and it is suitable for hardness assessments of plastics from the following viewpoints:
- Measuring specimens with thickness < 6 mm without overlaying.
- Measuring micro specimens smaller than those with conventional methods.
- Work related to the alteration in conditions is not necessary.
Wide utilization is possible based on the above-mentioned features, from the selection of resin materials in product development, to evaluation of resins for quality control purposes and evaluation of developed materials.
The plastic hardness analyzer (Dynamic Ultra Micro Hardness Tester for plastics DUH-210) employed in this experiment allows simple measurements that conform to ISO/TS 19278.
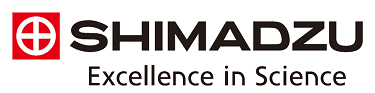
This information has been sourced, reviewed and adapted from materials provided by Shimadzu Scientific Instruments.
For more information on this source, please visit Shimadzu Scientific Instruments.