In this interview, AZoM talks to Ed Bullard and Martin Lewis, CEO and Principal Engineer at Scintacor respectively, about Scintacor, the company's products, capabilities, and vision for the future.
Ed, can you tell us a bit about your role at the company and how long you've been with Scintacor?
Ed Bullard: I joined Scintacor three years ago, in the autumn of 2017, as the chief executive.
When did you move into your newest facility and what are your thoughts on it?
Ed Bullard: Scintacor moved into this facility in the summer of 2017, shortly before I joined the company. I had visited the old facility in Harlow. This new facility is a big step up for the company. It is a larger factory with a much bigger and higher specification clean room, which potentially improves the quality of the product and reduces the risk of contamination or defects.
Martin, you've worked in several different technology companies over the years. What's interesting about your work at Scintacor?
Martin Lewis: There are a lot of challenges, and what is particularly interesting about Scintacor is that you get to work in many different areas. I am heavily involved in inspection and developing inspection techniques. For example, looking at things in a novel way to gain some information and some insight into how CsI materials in particular perform.
We are experts in, X-ray, and scintillation processes. We understand how to get the best out of materials. A lot of our testing equipment is custom made; it cannot be bought off the shelf. It is necessary to modify and add elements to improve functionality. There is chemistry involved, there is an understanding of water systems, cleaning, glass, optics, and more, and that is what I like. I like the variety in it all.
Can you give us a brief overview of some of your main product lines?
Ed Bullard: I will start with the infrared products. We make laser alignment cards, which are used with infrared and ultraviolet lasers to visualize the beam. We also have CamIR, which is a conventional camera with an infrared coating that enables the visualization of short-wavelength infrared radiation at about 1550 nanometers. And it is a nice solution if you need a lower cost camera to image SWIR radiation above 1000 nanometers. It is about 10% of the cost of an InGaAs SWIR camera. It is a great product for users of telecoms lasers and others, and we will be releasing a new version this year.
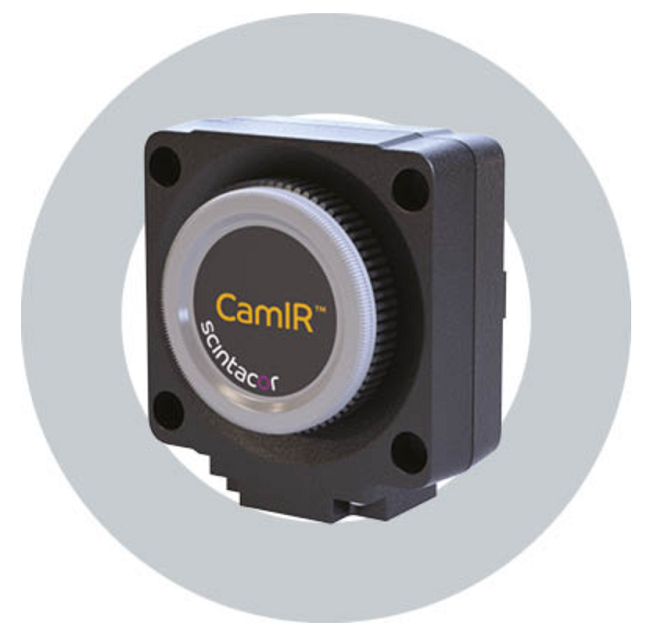
CamIR from Scintacor
Beyond that, we have our neutron glass, which is glass that we make here in our furnaces. It allows the detection of neutrons, for example from radioactive materials. This can be used in a portable radiation monitor, for example, if a first responder is at the scene of an explosion, they may wish to know whether there is any plutonium present or any emission of neutrons. And that can be done with a handheld device using our glass. The same technology can be used in the oil and gas industry to detect whether oil or gas is present in the rock around a drilled oil well. That same GS20 glass is also used in some scientific neutron detection equipment.
In cesium iodide, as I mentioned earlier, we have cesium iodide scintillators for intraoral dental devices, those that go in the mouth, as well as extraoral devices which are larger and are used outside of the head and enable the whole jaw to be imaged. We are one of the world's largest producers of those devices. In the future, we intend to produce larger area screens, cesium iodide scintillators that can be used in surgery, and 3D scanners. They will be employed in vascular and orthopedic surgery, for example, knee or hip replacements. These procedures are all carried out with image guidance under X-ray.
Now, the security side of the business. We have upgraded our facilities here to make large quantities of phosphor screens that are used in X-ray backscatter imaging. These are also used in 3D scanners for baggage scanning in aviation.
An area we are moving into is scintillators for electron beam applications, in particular transmission electron microscopy, which is an interesting technology used in material science and life science research. Recent examples are seen in the media this year are images of SARS-CoV2 virus particles, which have been acquired with transmission electron microscopy. It is a technology that allows some of the smallest objects to be imaged, and we are becoming more involved in that market.
What features of the products have you been trying to optimize?
Martin Lewis: We have been working a lot recently trying to optimize the performance of CsI material by looking at the morphology, using various techniques. Running different processes, looking at different parameters, temperature, the position, rate, pressure, and trying to understand the impact of that on the morphology of the CsI and its X-ray performance, light output, and resolution, for example.
What would you say are your primary applications for Scintacor’s products?
Ed Bullard: We have a long history of involvement in dental X-ray and that remains one of our main focuses. We make a large percentage of the global production of scintillators for dental X-ray sensors used by dentists all around the world. We are also involved in security markets, whether for the checkpoint or baggage scanning security in airports or security at points of entry to countries, for example, ports or land borders. These security systems are preventing the smuggling of both drugs, people, guns, currency, and also radioactive materials.
An important part of our business is involved in detecting illicit trafficking of radioactive materials, such as plutonium, which of course is a risk to national security in this country and worldwide.
What's your favorite application for a Scintacor product?
Ed Bullard: We have such a wide range of applications and technologies and such a wide range of markets. I have always been very interested in medical X-ray and 3D imaging, as well as medical and industrial dental X-ray and that is an area that has a lot of opportunities for Scintacor to grow and expand its offerings.
What do you think makes Scintacor unique?
Ed Bullard: Not many people do what we do. It is quite a specialized niche. Certain groups have some of the capabilities we have in Japan or the US, but we are quite a unique company in the combination of skills and technologies we have here.
Martin Lewis: We can respond rapidly with new products, new methods, and we are keen to work with customers and meet their needs. You do not get that with the larger companies, we can respond and tailor things because our scintillation materials are infinitely variable. It is not a one-size-fits-all product. We can respond appropriately.
What do you think makes Scintacor different from its competitors?
Ed Bullard: What makes Scintacor unique is the scope of its offerings related to scintillation, and this exclusive focus on scintillation. Other companies are also involved in certain markets that we are involved in, but none are involved in all of them. These are the companies that are involved in a wide variety of activities, they may scan the whole of Photonics, whereas we have a very narrow focus on this specific area and it allows us to focus on that and help our customers with their product offerings without competing with them in their markets.
How does Scintacor like to operate with its clients or customers?
Ed Bullard: Our typical model of working with our customers is that we have a long-term, collaborative relationship, which is quite in-depth. For example, this afternoon, I had a regular call with clients in Massachusetts, USA, and we were talking with their commercial people, the buyers, but also their chief scientist and we have worked together over several years. We are involved directly in their product development process.
They have got a new product and we are part of that development, and we will develop the scintillation components of that. It is a very interactive process in which we are a strategic part of their supply chain and part of their team, and we are bringing the specific expertise that our engineers here have, as well as our tooling and our facility. We contribute to their product development efforts and ultimately their production.
Martin Lewis: We work closely with customers, and it is quite technical. We like to work with their technical people, discussing their problems, coming up with solutions, trying things, and always keeping them informed. We write a lot of reports that we share with customers, and that is very much appreciated. We try to understand what their problems are and try to improve product performance.
Can you give us some examples of the type of interesting projects that you have worked on with clients?
Ed Bullard: Scintacor recently worked on an exciting project collaborating with eXaminArt, on the Nasa funded PIXI (Planetary In-Situ X-ray Imager) project to develop an in-situ high-resolution X-ray computed tomography (microCT) instrument to analyze geological samples on the surface of Mars.
The PIXI system incorporates a new X-ray CMOS camera based on the Open Source Axiom Beta Camera developer’s kit. The sensor will be modified in-house with new CsI scintillators from Scintacor, optimized to provide the best trade-off of efficiency vs resolution. The method involves bonding a fiber optic plate (FOP) to the sensor and depositing a scintillator material on the surface of the FOP, to produce a very high-resolution detector.
Scintacor also participated in the Solid-State Neutron Detector – SoNDe – project to develop a high-resolution neutron detector technique that will enable the construction of position-sensitive neutron detectors for high-flux sources, such as the upcoming European Spallation Source (ESS) by avoiding the use of 3He in this detector the 3He-shortage, which might otherwise impede the construction of such large-scale facilities. Replacing 3He, Scintacor’s 6-lithium glass scintillators have been used in the SoNDe project to create a novel high-efficiency neutron detector with the capability to clearly distinguish between neutrons and gamma radiation.
How do you think Scintacor can help their customers with the challenges that they would be facing in the next couple of years?
Ed Bullard: Scintacor can help customers introduce new products more rapidly than if they undertook all the developments themselves internally. One big requirement from the customers is to reduce costs as well as improving quality. Our goals are to improve our efficiency, performance, and quality.
Can you tell us about Scintacor’s plan for the next five years?
Ed Bullard: We want to expand the range of products we offer. Moving beyond the specific dental X-ray market into medical and industrial X-ray applications and to do that, we need to have larger scintillators, and so we have acquired and installed a larger cesium iodide deposition chamber, which will allow us to make the larger CsI scintillators required particularly for surgery and also for some 3D imaging applications.
On the security side, we want to expand our reach geographically and to expand our market share in the screening of vehicles and people at international borders and airports.
The team, the facilities, and the processes we have developed offer a lot of opportunities for the future. And it is exciting to look forward to the next five years.
About Ed Bullard
Ed is a well-recognized leader in the X-ray detection industry. In 2003, Ed co-founded Dexela Limited to develop the 3D X-ray breast imaging technology. Ed was CEO of Dexela until the company was acquired by PerkinElmer in 2011. After the acquisition, Ed acted as General Manager of Dexela before being promoted first to Director of Global Sales for PerkinElmer Medical Imaging and then VP Global Marketing, Sales and Business Development in 2014.
About Martin Lewis
Martin Lewis – Has more than 30 years of experience in material science. Martin joined Scinacor in 2015 as Head of Process Improvement Group at Scintacor Ltd. Responsible for process engineering, yield improvement, manufacturing efficiency, technical problem solving, equipment design, failure analysis, optical inspection, process troubleshooting, process characterization.
Disclaimer: The views expressed here are those of the interviewee and do not necessarily represent the views of AZoM.com Limited (T/A) AZoNetwork, the owner and operator of this website. This disclaimer forms part of the Terms and Conditions of use of this website.