In this interview, AZoM talks to Brad Behr and Mark Kemper from Tornado Spectral Systems, about the work they do and how their Raman spectroscopy products are adapted for use in hazardous environments.
Please could you give an overview of Tornado Spectral Systems and the work you do?
My name is Brad Behr, and I’m the Chief Technology Officer at Tornado. I’m responsible for developing our IP portfolio for maximizing spectroscopic performance and turning our core technology into products that solve our customers’ process analytic problems.
My name is Mark Kemper, and I am the Director of Applications and Customer Success. I am primarily responsible for supporting global sales and enabling customer success.
Tornado creates high-performance Raman spectroscopy systems for process and laboratory monitoring. Our company was founded to commercialize some revolutionary optical engineering concepts that were invented by our academic research group at the University of Waterloo in Canada. Raman spectroscopy has been around for almost 100 years, but the Raman scattering signal is exceedingly weak, making Raman impractical for a lot of real-time process monitoring applications.
Our innovation, the High-Throughput Virtual Slit, brings an order of magnitude greater photon signal to the focal plane detector of a Raman spectrometer as compared to conventional systems, enabling measurements that were previously impossible for Raman.
Our analyzers are used in the pharmaceutical and biopharmaceutical sectors, fine chemical production, petrochemicals, and many other scenarios where you need fast, accurate, high-resolution measurements of molecular composition.
Why does Raman analysis sometimes need to be conducted in hazardous environments?
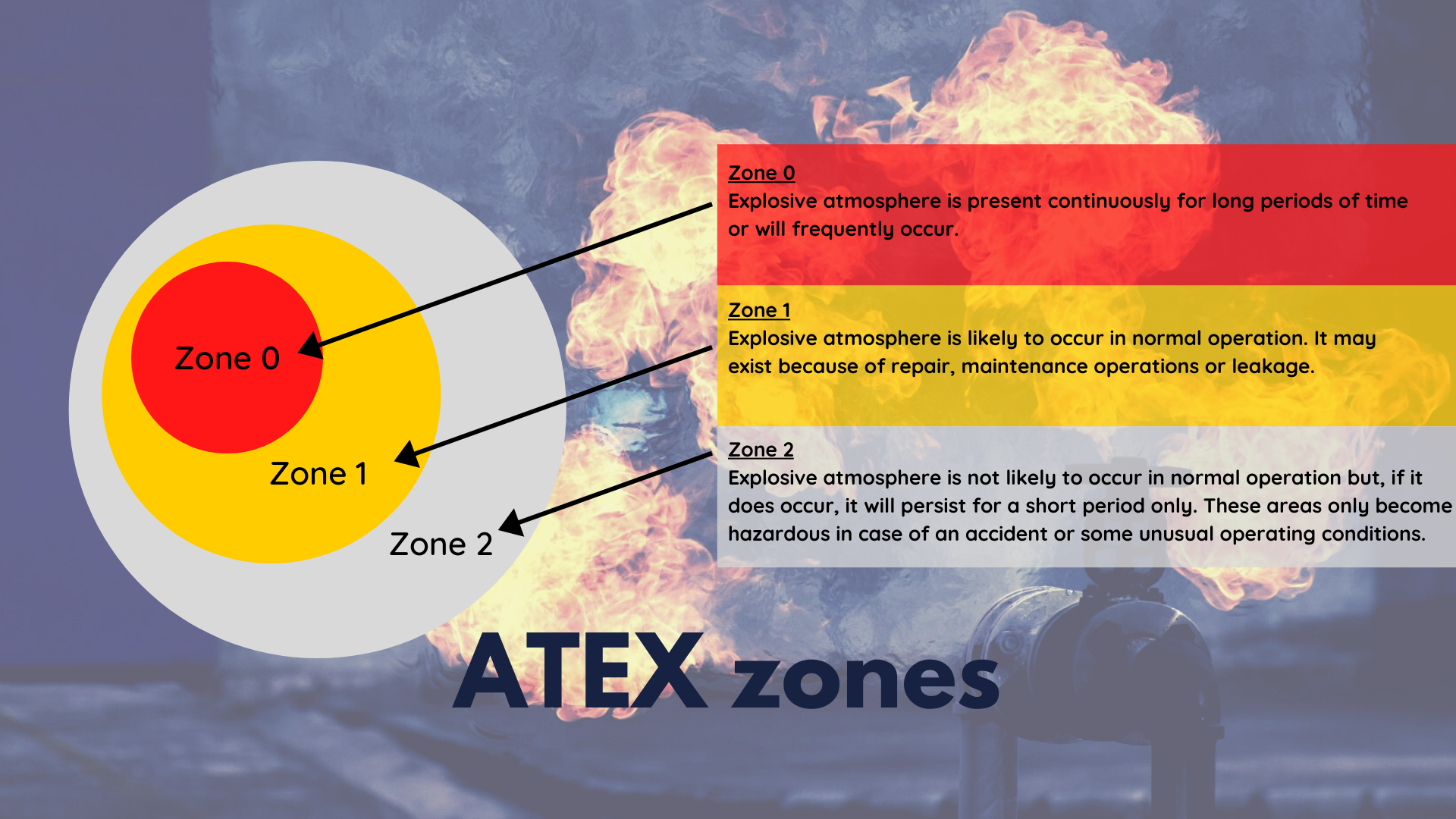
Classification of ATEX zones
Flammable vapors and gases are an unavoidable aspect of many manufacturing processes. Petrochemical refining, chemical production, and some types of pharmaceutical manufacturing are just a few of the situations where there is the potential (if not the certainty) of highly reactive gas species being present.
Dust and particulates also pose serious risk for creating catastrophic explosions or fires. As such, the IEC, the International Electrotechnical Commission, created a comprehensive set of standards for minimizing risk. The “IECEx” standards (where “Ex” refers to explosive atmospheres) laid out in their 60079 series of documents explain how to avoid creating an ignition source in many different industrial scenarios.
One key concept from this standards framework is the concept of zones. Zone 0 is the most hazardous because explosive or flammable gas is always or usually present. In Zone 1, these gases may be present occasionally. In Zone 2, the safest of the three hazardous zones, dangerous gases are rarely there. And then in a “safe zone”, there is never any hazardous atmosphere – this would be your control room or a separate building.
One of the great things about the Raman method is that most of your hardware like the main analyzer unit and control computer can reside in a safe zone, and the excitation laser and scattered Raman signal can be conveyed in and out of the hazardous zone by optical fibers.
If you want to make Raman measurements of your process, whether it’s quality control on raw materials, or reaction monitoring, or quantitative evaluation of the final chemical product, you have to be aware of the zone rating of the measurement point(s) and take appropriate steps to ensure that your measurement equipment in the hazardous zone adheres to the IECEx standards.
What are the main safety considerations when conducting Raman in a hazardous environment?
The biggest risk with doing Raman analysis in a potentially flammable or explosive atmosphere is that the concentrated laser beam may cause heating of a particle or surface and serve as an unintended ignition source. The IEC-60079 standards define three ways to prevent optical radiation (e.g. your Raman excitation laser) from triggering a fire or explosion.
- The IEC designation <op sh> refers to having some sort of sensor that will shut off the laser if explosive gases are near the Raman probe focal point. This could be an optical fiber break detection circuit for the case where the cable carrying the laser light is severed. Or, consider a situation where the Raman probe is measuring a liquid in a pipe or vessel. As long as the laser focal point is “underwater” and away from oxygen, combustion can’t take place, but a signal from a level sensor would be required to kill power to the laser if the liquid level falls too low and risks exposing the focal point to explosive vapor.
- The <op pr> designation provides for a small region around the measurement point where active purging with inert gas or some other protective method will prevent explosive gases from leaking in. You’re essentially creating a small “safe zone” at your Raman measurement location.
- Tornado has designed its ATEX-safe Raman solution around <op is>, where the “is” stands for “inherently safe”. Extensive studies by IEC engineers have determined that by limiting the laser power coming into the hazardous zone to a certain level – either 15 mW, 35 mW, or 150 mW, depending on the specific types of gases present – then there is no risk of that laser light triggering an ignition, no matter how tightly focused the beam might get.
Two other important concerns are that an electrical signal going into a hazardous zone, such as a limit switch circuit or a laser safety indicator light, might create a spark, or that the materials that the Raman probe is made of could create a spark, such as from electrostatic discharge or metal surfaces banging together if the probe is dropped against a pipe, for instance. These factors also need to be considered in determining if a Raman system is safe for an ATEX deployment.
Following on from the previous question, the OPIS 35 has both ATEX and IECEx certification, could you elaborate a little on what this means?
ATEX, an abbreviation of “Atmosphères Explosibles”, is a European directive that defers to the IECEx standards. The IEC-60079 documents are extremely specific and comprehensive, but they do not have the force of law behind them.
The European ATEX directives make it a requirement, not just a best-practices guideline, to follow the IECEx standards.
Our OPIS 35 laser accessory has been certified with the IECEx mark “[Ex ia op is IIC T4 Ga]”, where each cluster of letters and numbers has a specific regulatory meaning:
- Ex refers to a potentially explosive atmosphere
- ia signifies that electrical output from the OPIS signaling and interlock circuits are intrinsically safe and can’t generate a spark
- op is tells us that the laser radiation is inherently safe under the following conditions:
- IIC defines an area with a gas atmosphere other than an underground mine
- T4 refers to potentially flammable gases with ignition temperatures of 135˚C or higher, which includes the vast majority of industrial gas types
- Ga means that OPIS 35 has the most stringent Equipment Protection Level
Tornado's OPIS 35 ATEX Certified Laser Accessory
The corresponding ATEX mark for OPIS 35 includes all the IECEx designations, plus the added indicators “II (1) G”, which translates to “suitable for installation on the Earth’s surface”, “suitable for connecting to equipment in a Zone 0”, and “suitable for gas atmosphere”. The ATEX mark also includes a yellow hexagon icon with script letters “Ex” inside, which is the most recognizable symbol of ATEX compliance. But you really should pay attention to the rest of the ATEX mark to determine if a specific device is safe for your ATEX situation.
So the ATEX and IECEx marks convey pretty much the same information, but it’s important to make the distinction that IECEx is a standard while ATEX is a regulation.
What would you consider to be the key features of the OPIS 35 and its integration with the HyperFlux PRO Plus?
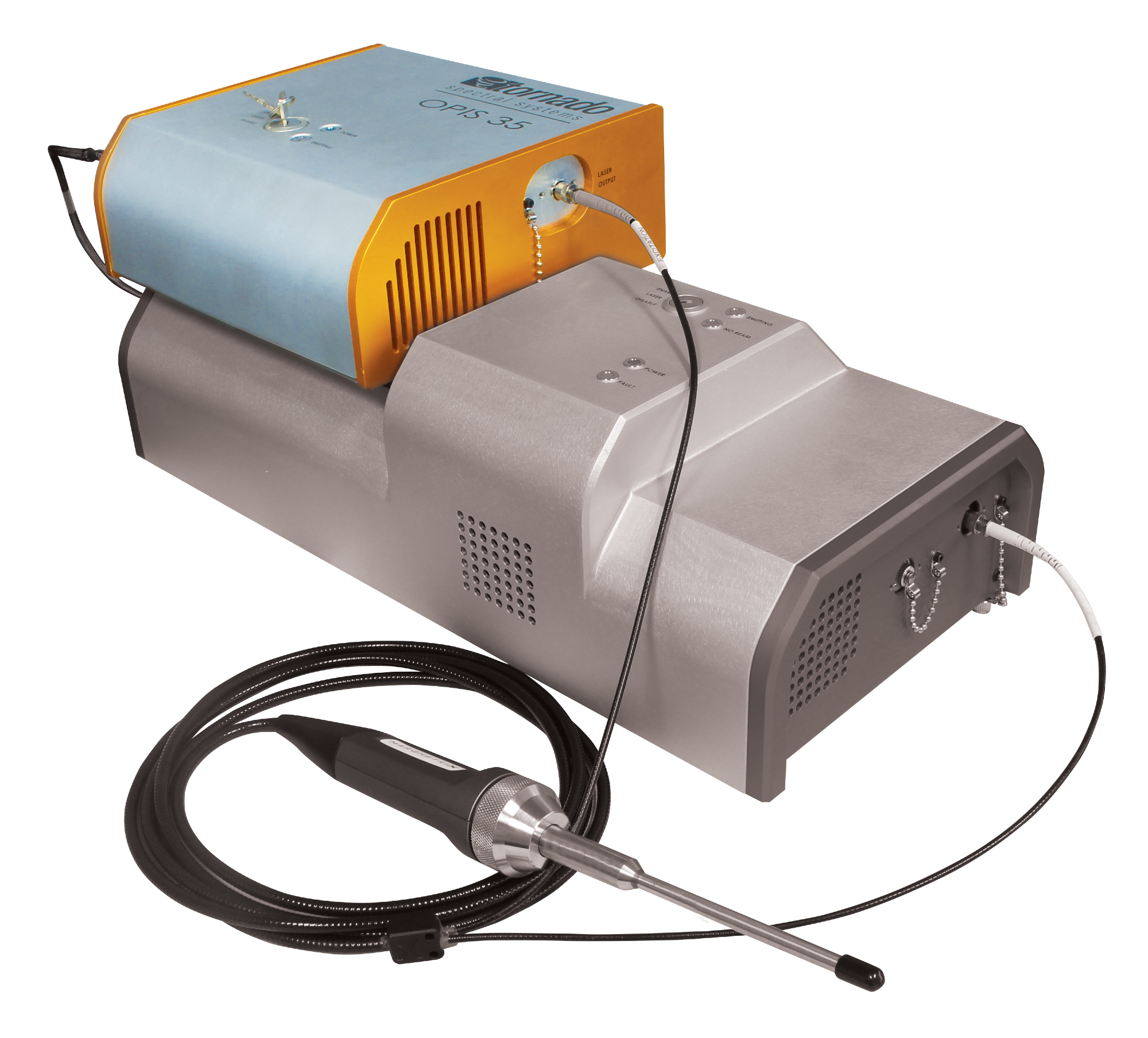
A 35mW HTVS-enabled HyperFlux™ PRO Plus delivers the same measurement precision as a conventional Raman analyzer running at 495mW
The key feature of the OPIS 35 device is the <op is> mark, that the device produces and transmits an inherently safe level of laser light which will never ignite any T4 gases. By design, any item (such as a Raman probe) connected to the OPIS 35 maintains compliance with ATEX Zone 0 optical safety without modification. To be clear, the OPIS 35 itself can’t be put in the hazardous zone, but it can send light into an optical fiber leading into the zone and this configuration is guaranteed to be safe.
You don’t need any auxiliary equipment like limit switches or purge systems, as you would with an <op pr> or <op sh> Raman system. The <op is> approach is so much simpler, less expensive, and arguably safer since there are fewer things that can go wrong.
And OPIS has internal current limiters which make it easy to send intrinsically safe electrical signals (that’s the 'ia' in the marks) into the hazardous zone, to light up a laser indicator light and/or enable an emergency stop button or door switch. Even though <op is> does not require any interlock shutoff circuits like <op sh>, eye safety regulations may specify these sorts of interlocks, and that capability is built into the OPIS 35.
One additional feature of our ATEX solution is the flexibility of being able to add an OPIS device to an existing PRO Plus analyzer, and then being able to switch back to full-power (495 mW) excitation if the system is removed from the hazardous environment and moved back into a fully safe zone like a lab. It’s a simple matter of plugging or unplugging a couple of cables between the OPIS and the PRO Plus.
Our software recognizes when an OPIS is connected, modifies the user interface appropriately, and disables the PRO Plus internal laser. Furthermore, if the OPIS is not connected to a PRO Plus, then it won’t emit laser light.
Despite the lower power of the OPIS 35 laser, how have Tornado Spectral Systems managed to still provide the same quality of data that one would expect from a conventional Raman system?
Normally, limiting your laser to 35 mW would severely degrade the quality of the Raman spectrum, since the Raman signal is proportional to the excitation laser power. We make up for the loss in signal by pairing the inherently safe laser source with our HTVS-enhanced spectrometer, which has 10x to 20x better efficiency than a conventional spectrometer, thereby compensating for the lower Raman signal that you get from using the low-power laser. So we are able to achieve the same measurement precision quality -- be it speed, or limit of detection, or chemometric precision -- as a conventional analyzer that’s not <op is> compliant.
For Tornado Spectral Systems, what does the future of Raman analysis look like?
A complete solution for process analytics requires much more than a great analytical instrument. We’ve also put a lot of effort into developing powerful but easy-to-use instrument control software, offering flexible sample interfaces like different types of probes (immersion, flow cells, and non-contact), increasing capabilities for integration into industrial distributed control systems, and safety measures that are equal to the capabilities of our core instrument. All of these factors are critical for providing a comprehensive and fully deployable product for our customer base.
Where can readers find more information?
To learn more, please visit our website at https://tornado-spectral.com/
To view our webinar, Inherently Safe Raman Measurements for Hazardous Zones, please visit: https://tornado-spectral.com/resources/webinars/
About the Researchers
As Director of Applications Development and Customer Success at Tornado Spectral Systems, Mark is primarily responsible for supporting global sales and enabling customer success. Throughout his career, Mark has been extensively involved with spectroscopic technologies including Raman, FT-IR, Near-IR, Terahertz and NMR. Mark has worked on both the business and technical side and published 25 peer-reviewed papers in reputed journals and presented at 100+ international conferences and also contributed to one book chapter. Mark received his B.S. in chemistry from the University of Dayton (USA) and his M.S. in biological chemistry from the University of Minnesota (USA). He is currently pursuing his PhD under the guidance of Professor Toshiro Fukami at Meiji Pharmaceutical University in Tokyo.
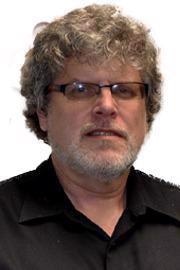
Brad started his career doing astrophysics research and developing advanced optical instrumentation for extracting the maximum amount of useful information from faint starlight. Much of this prior work translated directly into Tornado's advancement of the state-of-the-art for terrestrial spectroscopy applications such as real-time Raman monitoring and industrial process analytics.
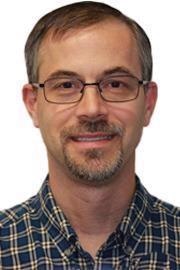
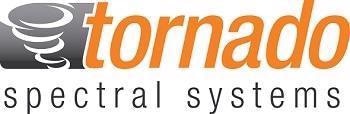
This information has been sourced, reviewed, and adapted from materials provided by Tornado Spectral Systems.
For more information on this source, please visit Tornado Spectral Systems .
Disclaimer: The views expressed here are those of the interviewee and do not necessarily represent the views of AZoM.com Limited (T/A) AZoNetwork, the owner and operator of this website. This disclaimer forms part of the Terms and Conditions of use of this website.