In this interview, AZoM talks to Eddy Hill about the automated mineralogy solutions offered by ZEISS that enable optimization of mining practices.
Can you give us an introduction to geometallurgy (in particular, mineralogic)?
An introduction makes me think of compressing everything that geometallurgy is into a few words - that is a challenge, but I will try. The final aim of the geometallurgical process is to maximize the net present value of the mine whilst reducing technical and operational risks.
In practice, this means bringing together geological, mining, metallurgical, environmental, and economic disciplines to build a predictive model of process performance for today and tomorrow, and of environmental behavior that continues beyond mine closure.
It is a holistic approach that goes beyond the characterization of an ore by metallurgical testing and process mineralogy, although, it is in these two disciplines that our mining solutions are most impactful; in particular, ZEISS Mineralogic. Starting with feasibility and throughout the life of the mine, Mineralogic provides timely, high resolution chemical and mineralogical data vital to the geometallurgical method.
What are some of the main advantages of using a more holistic approach towards mining (such as its economic profitability and social benefits)?
Geometallurgy has evolved from its early origins as a bridge between the geologists and metallurgists. It now integrates all site stakeholders, across the entire mining value chain, increasing collaboration and knowledge sharing leading to business optimization. A parallel benefit is to staff morale as all staff become stakeholders and are invested in the process.
More broadly, Geometallurgy presents the opportunity to minimize mining’s social and environmental impact. Not just for current operations, but also by presenting a method for the re-evaluation of mining waste products.
More and more we are looking towards mine tailings as a potential resource and the application of geometallurgical programs to plan how best to rework the tailings and minimize the environmental impact is key to making these projects viable.
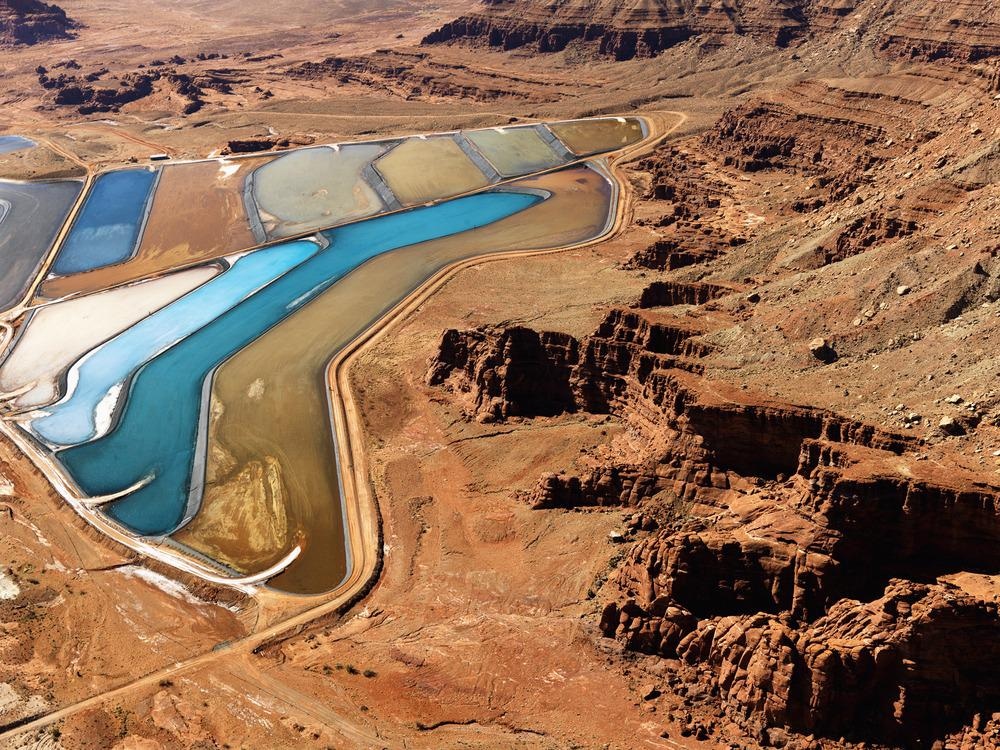
Image Credit: Shutterstock/iofoto
How do these types of programs benefit from gaining knowledge of the orebody before and during mining?
Detailed orebody knowledge is essential for the optimal recovery of the resource. Before any mineral processing takes place, there should be a clear understanding of what minerals will be of environmental concern and what minerals will exercise control over the process path.
This understanding must then be fed into the block model to predict behavior and highlight deleterious areas. Work to understand the deposit does not end once operation is underway. Instead, continuous monitoring of process performance and mineralogy data must feed back into the mine model as part of the continuous improvement loop.
What is the importance behind the practical application of mineralogical knowledge in the exploration and optimization of how an ore is mined and processed?
Mineralogical and geochemical knowledge is vital during the exploration phase and, later, key to the ongoing optimization of the beneficiation process. We mine for metals, we study minerals, but we recover particles – at least this is true for a flotation circuit. The value we seek resides in minerals but so do the deleterious aspects of the ore.
Detailed knowledge of the mineralogy, at every stage of the process, gives us control over the processing of the ore. It is the minerals, their composition, hardness, habit, size, etc that determine how the ore will fragment and how the value phases will be liberated.
It is the mineral constituents of a particle that determine how it will react to our recovery efforts. And so, providing detailed chemical and morphochemical information of the minerals and the particles they form is paramount in the 2D and 3D solutions we offer.
In terms of ZEISS’ current automated mineralogy solutions, how would you say these fit into the analytical part of the workflow?
ZEISS offers automated mineralogy solutions on its light microscopes (LM), scanning electron microscopes (SEM), and 3D X-Ray microscopes (XRM). On the mine, these solutions are optimized to work as part of a continuous improvement process, able to provide feed-forward information and performance information on the distinct stages of the beneficiation process.
In a more investigative or research-focused environment, they offer the high analytical resolution and accuracy you would expect from a ZEISS microscope.
When it comes to the development of Mineralogic mining analysis tools, what are some of the biggest problems you have come across so far, and how have these been overcome?
Any development program working on the edge of what technology can offer will encounter challenges; this has also been the case in the development of the Mineralogic tools. Being challenged, however, is a standard state of being for us.
We are constantly challenging ourselves, and being challenged by our customers, to find that extra detail, higher resolution, or new measurement type that adds value to the analysis. The toughest of all the challenges is overcoming the status quo but the Raw Materials Team consists of a dedicated team of experts in geoscience and the extractive industries capable of understanding your needs and keen to demonstrate the advantages offered by our solutions.
What is the importance behind high throughput mineral liberation investigations?
Mineral liberation studies are useful in assessing the liberation potential during comminution processes and the potential of pre-concentration stages. Traditionally, these studies may involve the use of SEM-based automated mineralogy techniques incurring a high cost due to the large number of sample analyses needed to attain statistical viability and minimize stereological effects.
Today, besides the 2D Mineralogic solution, ZEISS offers a 3D solution, for liberation investigations, which requires no special sample preparation, that does not suffer from stereological effects, and requires a smaller sample size to attain a statistically valid result. Overall, the time to results has been reduced and the data is a more accurate interpretation of reality.
How has the development of automated mineralogy affected the utilization of EDS mineral classification systems?
It could be argued that they have progressed hand in hand. The advent of SEM-based automated mineralogy brought to the fore the use of EDS detectors for mineral classification, offering a faster, if not initially as accurate, alternative to electron microprobe (EMP) analyses based on WDS.
Over the past 25 years, and accelerating over the past 10 years, the accuracy and speed of the EDS detectors have improved considerably. To the point where Mineralogic offers EDS based Automated Quantitative Mineralogy (AQM) with a resolution of 1000ppm. The Mineralogic classification system is based on the full deconvolution of the spectra acquired by EDS and the quantification of the chemical composition expressed as element weight% values.
This proves not only advantageous when dealing with complex mineralogy and solid solutions, but also in that it provides a bulk chemistry for the sample comparable to that obtained by XRF, or EMP, with a spatial resolution of nm to cm.
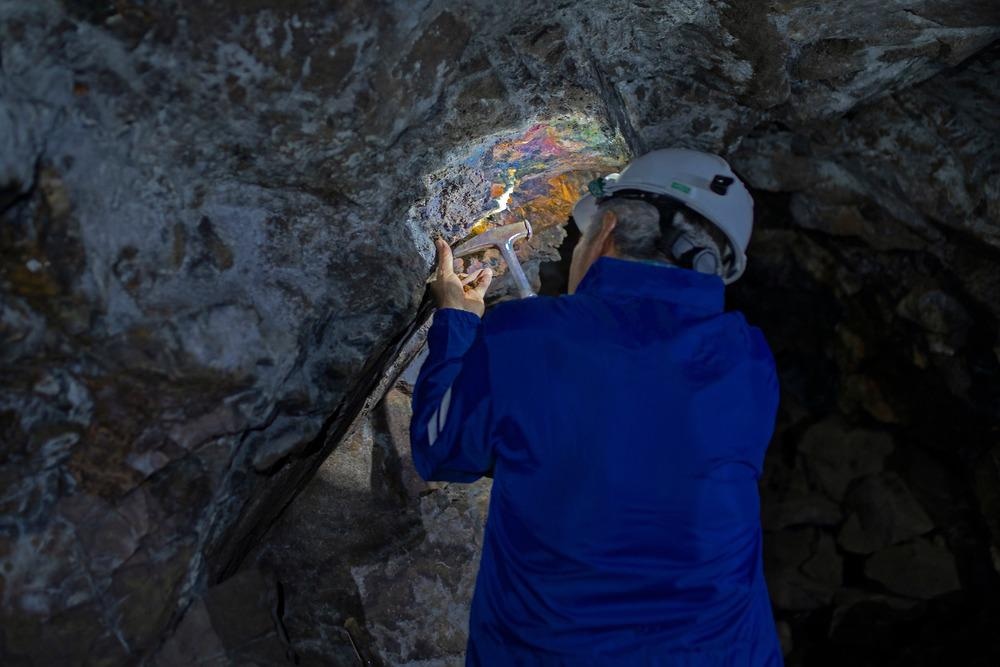
Image Credit: Shutterstock/Marlene Gracia
Looking towards the future, what do you hope for in terms of the development and dissemination of ZEISS automated mineralogy solutions?
Our drive is to provide the best, most accurate analyses to enable data-based decision making and we believe the connected laboratory, where LM, SEM, and XRM based Mineralogic speak to each other, seamlessly sharing data and enabling contextual interpretation is the best way to achieve this.
But we are not stopping there, there is other relevant information that should also be available and so we want to invite other techniques into the laboratory and integrate them, thus correlating Mineralogic to, fo
r example, laser ablation. With tools such as ZEN Connect and ZEN Data Storage at our disposal, I am pleased to say that we are very close to achieving our aim.
About Eddy Hill
Eddy Hill completed a Ph.D. in Experimental Petrology at the University of Bristol, which he followed with a move to UT to work on developing technologies for in-situ resource utilization with a view to building and supplying a Lunar Base. In time, he returned to more traditional research topics at the Lunar and Planetary Laboratory, Arizona, before moving to industry to work as a Consultant. In 2012, he joined ZEISS with a remit to develop automated analytical solutions for Geoscientists and the Mining Industry.
Disclaimer: The views expressed here are those of the interviewee and do not necessarily represent the views of AZoM.com Limited (T/A) AZoNetwork, the owner and operator of this website. This disclaimer forms part of the Terms and Conditions of use of this website.