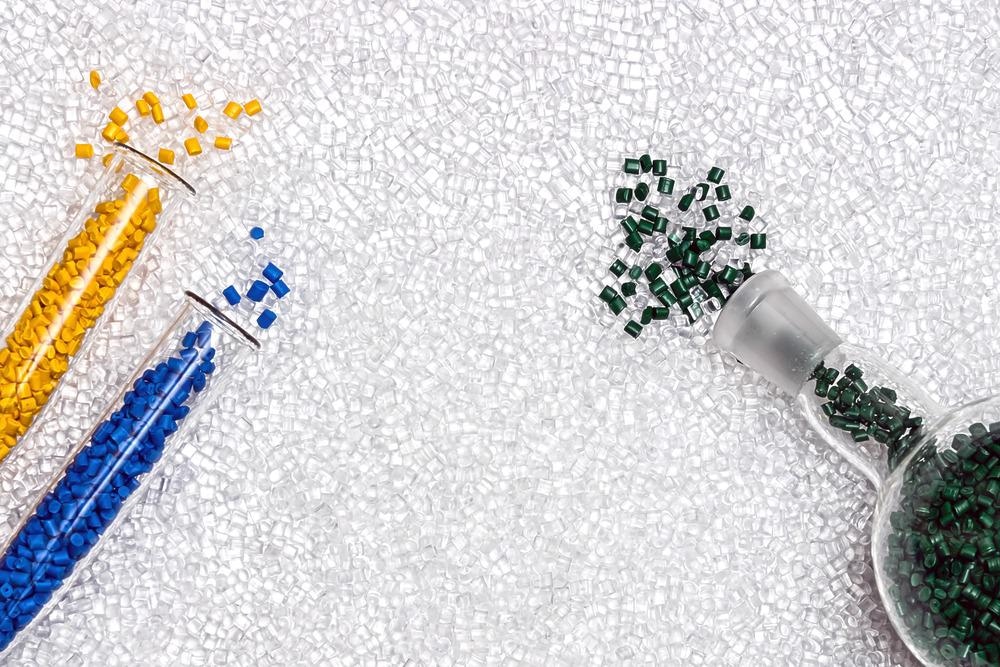
Image Credit: Mr_Mrs_Marcha/Shutterstock.com
Responding to the expanding demand for sustainable development and rising prices of raw materials, Royal DSM, a global advanced materials manufacturer based in the Netherlands, has made sustainability its strategic priority. In partnership with Neste, a leading producer of renewable fuels and feedstock for the chemical industry, Royal DSM aims to expand sustainable feedstock for polymer production and offer products that can support a more environment-friendly circular economy model.
Polymer materials have become an essential part of modern life and industrial development due to their versatile nature and superior material properties. However, many of today’s petrochemical-based polymers have concerning environmental impacts, including the greenhouse gases involved in raw material extraction and manufacturing and the waste plastic pollution of the environment.
The growing understanding of modern plastics' environmental impact allows some of the leading materials manufacturing companies to increase their efforts to develop innovative technologies that can mitigate ecological degradation by establishing circular economic models for plastic manufacturing, utilization, and end-of-life treatment and reuse.
Partnership for a Healthier Future
By partnering with Neste, DSM's Engineering Materials division moves towards establishing a comprehensive portfolio of high-performance, sustainable polymers and carbon footprint reduction.
By 2030, the company aims to offer a full alternative range of its high-performance materials manufactured from at least 25% recycled plastic waste and bio-based feedstock for polymer production.
Outstanding Performance and Less Damage to the Environment
In the first phase of the project, DSM Engineering Materials will gradually replace a substantial share of the fossil feedstock used in the manufacturing of its range of advanced polyamide and polyester materials, such as Akulon®, Stanyl®, and Arnitel®.
These materials are widely used in the packaging, automotive, electrical, and electronics industries.
Akulon® is a high-strength impact-resistant plastic, while Stanyl® is a heat-resistant polyamide with excellent strength and fatigue resistance, extremely suitable for high-temperature applications.
Arnitel® is an advanced thermoplastic copolyester offering a unique combination of flexibility, temperature resistance, and strength for a wide range of industrial applications.
Mass-Balanced Feedstock for Polymers
The range of sustainable alternatives will rely on many different technologies and approaches such as mechanical recycling, thermochemical recycling, and mass balance accounting of bio-based and recycled feedstock for polymers.
Mass balance accounting is based on the principle that the input feedstock's mass is equivalent to output product mass. A set of rules can be derived that allocates the bio-based and recycled content to different products manufactured from a mix of fossil-based and sustainably source feedstock.
The manufacturer can trace the flow of materials through the production value chain and highlight the amount of displaced fossil feedstock, allowing them to claim and market the content as ‘bio’-based or ‘recycled’-based.
Traceable and Sustainable Feedstock for Polymer Production
As the world’s largest producer of renewable fuels and raw materials for the polymer and chemical industries, the Finnish company Neste supports its partners with sustainability-oriented renewable and circular solutions.
Neste derives its sustainable feedstock for polymer production, called Neste RE, by combining renewable raw materials, including:
- Waste (and residue) oils and fats
- Sustainably produced vegetable oil and waste plastic that cannot be mechanically recycled, such as colored, multilayer, or multi-material packaging, and has previously been incinerated for energy recovery or landfilled.
The renewable component of Neste RE is produced from 100% bio-based, globally sourced raw materials such as cooking oil or sustainably sourced palm oil.
These are subjected to esterification in a biomass-to-liquid (BTL) process, branded NexBTL, which utilizes Neste's proprietary conversion method at refining Porvoo facilities Finland, Rotterdam in the Netherlands, and Singapore.
The renewable component may also contain renewable gaseous propane. Neste claims that it only includes sustainably produced renewable raw materials from carefully selected suppliers.
For the recycled component of Neste RE, non-reusable plastic waste is thermochemically liquefied, which turns the waste into a material similar to crude oil.
Straightforward Replacement of Fossil-Derived Raw Materials
Neste RE is a drop-in replacement of traditionally used fossil feedstock and is fully compatible with existing polymers production processes and infrastructure. This enables DSM to manufacture its range of sustainable engineering plastics consistently using its existing processes and facilities.
All of the recycled and bio-based feedstock for polymers within the product value chain has a globally recognized International Sustainability and Carbon Certification Plus (ISCC Plus) that covers all types of biological and non-biological renewables and recycled carbon raw materials.
Sustainable Opportunity for the Industry
The sustainability certified Akulon®, Stanyl®, and Arnitel® bio-based alternatives will deliver the same functional performance as DSM’s conventional portfolio of high-performance polymers, enabling customers to easily shift to a more sustainable solution without needing to requalify materials and processes. This would help to reduce the share of fossil-based feedstock used for plastics manufacturing, which is currently around 6% of the global oil production and is forecasted to increase to 20% by 2050, while at the same time maintaining a healthy and circular bio-based economy of high-performance polymers.
References and Further Reading
DSM (2020) DSM and Neste announce strategic partnership to create high performance materials made from sustainable feedstock. [Online] www.dsm.com Available at: https://www.dsm.com/corporate/news/news-archive/2020/2020-11-27-dsm-and-neste-announce-strategic-partnership-to-create-high-performance-materials-made-from-sustainable-feedstock.html (Accessed on 15 December 2020).
Neste (2020) Neste RE enables a future where all plastic products can be made of renewable and recycled materials – and the future starts today. [Online] www.neste.com Available at: https://www.neste.com/releases-and-news/plastics/neste-re-enables-future-where-all-plastic-products-can-be-made-renewable-and-recycled-materials-and (Accessed on 15 December 2020).
ISCC. The mass balance approach. [Online] https://www.iscc-system.org Available at: https://www.iscc-system.org/ (Accessed on 15 December 2020).
S. Moore (2019) DSM promises bio-based alternatives for entire engineering plastics portfolio. [Online] www.plasticstoday.com Available at: https://www.plasticstoday.com/k-show-dsm-promises-bio-based-alternatives-entire-engineering-plastics-portfolio (Accessed on 15 December 2020).
Ellen MacArthur Foundation (2016) The New Plastic Economy – Rethinking the Future of Plastics. [Online] www.ellenmacarthurfoundation.org Available at: https://www.ellenmacarthurfoundation.org/assets/downloads/EllenMacArthurFoundation_TheNewPlasticsEconomy_Pages.pdf (Accessed on 15 December 2020).
Disclaimer: The views expressed here are those of the author expressed in their private capacity and do not necessarily represent the views of AZoM.com Limited T/A AZoNetwork the owner and operator of this website. This disclaimer forms part of the Terms and conditions of use of this website.