When a natural gas or oil pipeline is under repair, it is absolutely necessary to check that the new weld is completely secure. On a fundamental level, the integrity of the weld depends on the total compatibility of the two pieces of pipe being fused together. If there any behavioral differences between the two pieces of pipe, or they become brittle during the welding process, the weld will malfunction – with potentially catastrophic consequences.
Therefore, it is vital to ensure the right grade of steel is being used. But being dependent on grade alone can be a risk because even within a grade, problems with weld integrity can occur due to variances in the exact composition. This means precise measurements of the exact composition of each individual piece is necessary to determine how the component will behave.
This is where the carbon equivalent concept comes in handy. This enables detailed material composition measurements and the ability to turn that information into something useful for the evaluation of the weldability of the material.
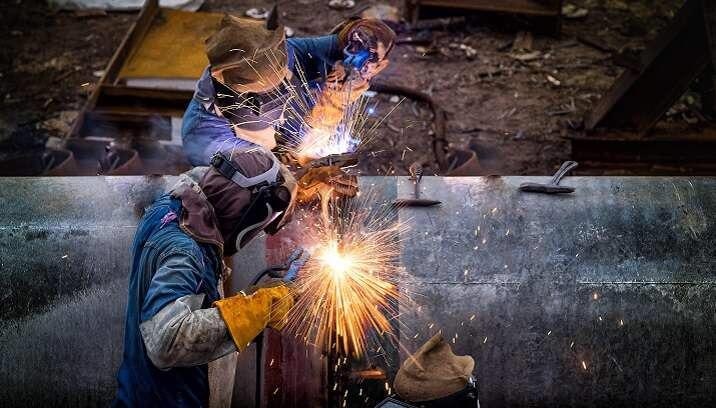
Image Credit: Hitachi High-Tech Analytical Science
Carbon Equivalent is the Key to Predicting Steel Behavior
Utilizing the equivalent carbon content concept is appropriate for ferrous materials, usually steel and cast iron, to identify different properties of the alloy when more than just carbon is present as an alloying element.
It’s generally accepted that the carbon levels present within iron or steel impact brittleness and strength and, therefore, how the material can be worked and welded. However, the presence of other elements means that carbon is not the only alloying element that contributes to the material properties.
Evaluating the impact of each individual element and how it interacts with all the others would be tough and laborious. Therefore, the carbon equivalent concept is utilized whereby all the alloying elements are put through a formula ‘converting’ them into an equivalent carbon percentage.
The concept is the conversion of the percentage of alloying elements other than carbon to the corresponding carbon percentage because there is an improved understanding of iron-carbon phases in contrast to other iron-alloy phases. This single number is then used to assess behavior, such as weldability, as exhibited in the table below:
Source: Hitachi High-Tech Analytical Science
Carbon equivalent (CE) |
Weldability |
Up to 0.35 |
Excellent |
0.36–0.40 |
Very good |
0.41–0.45 |
Good |
0.46–0.50 |
Fair |
Over 0.50 |
Poor |
Thus, it is clear from the table that the greater the CE number, the more likely the weldability will be under par. So, how is it possible to achieve this number? Enter the carbon equivalent equations:
- International institute for welding (IIW) CE:
CE = (%C)+((%Mn)/6)+(((%Cr)+(%Mo)+(%V))/5)+(((%Cu)+(%Ni))/15)
- Japanese welding institute PCM:
PCM = (%C)+((%Si)/30)+(((%Cr)+(%Cu)+(%Cr))/20)+((%Ni)/60)+((%Mo)/15)+((%V)/10)+((%B)*5)
- Düren CEM:
CEM = (%C)+((%Si)/25)+(((%Mn)+(%Cu))/20)+(((%Cr)+(%V))/10)+((%Mo)/15) +((%Ni)/40)
- Thyssen CET:
CET = (%C)+(((%Mn)+(%Mo))/10)+(((%Cr)+(%Cu))/20)+((%Ni)/40)
- EN 10025-1 CEV:
CEV = (%C)+((%Mn)/6)+(((%Cu)+(%Ni))/15)+(((%Cr)+(%Mo)+(%V))/5)
Here five equations are presented; in practice, the one that closely matches the type of steel being used is the one used to make calculations.
It is clear to see how each equation utilizes the percentage of carbon measured and then adds adapted percentages of the other elements. For example, (%Mn / 6), which is present in the first equation, utilizes the percentage of manganese but divides it by six, which reduces its effect.
Why are There Several Equations?
Over time, new equations were produced to enhance accuracy for various types of steel, such as low carbon. They were also expanded to approximate the hydrogen cracking vulnerability of steel.
Which One Should You Choose?
The most common equation, adopted by the International Institute for Welding, is the first equation. But if analysis of low carbon steel is being conducted, the PCM and CEM expressions are the most appropriate. However, where the carbon content is typically less than 0.11 wt.%, the second PCM equation is used for modern steels used in pipeline manufacture.
What Do I Actually Need to Measure in My Pipe?
To determine the weldability of the pipeline precisely, it is necessary to measure the elements within the PCM equation:
Boron, Carbon, Chromium, Copper, Molybdenum, Nickel, Silicon and Vanadium.
It may be necessary to also measure phosphorus and sulfur to generate a more detailed analysis and nitrogen will need to be measured if it is necessary to identify duplex steels.
Making CE Calculations Easy
Hitachi High-Tech’s range of spark OES instruments measure the elements essential for precise CE calculations and will go through the calculation and provide the CE number.
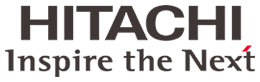
This information has been sourced, reviewed and adapted from materials provided by Hitachi High-Tech Analytical Science.
For more information on this source, please visit Hitachi High-Tech Analytical Science.