Verifying melt chemistry in order to control the melt process is crucial to ensure that the melt meets the specification limits of the grade to be cast. Within foundries, spark optical emission spectroscopy has been identified as the principal method for this task.
Today, foundries are under considerable amounts of pressure to cut costs. Therefore, simplifying the charging process – including the melt correction method – is a good way to reduce mounting costs. However, smart resource management and increased use of low-cost scrap and other casting sources can make charge correction complex, expensive and time-consuming.
Does Your Melt Make the Grade?
Manually comparing melt analysis results against a published grade table can extend time-scales and generate erroneous results.
Hitachi’s GRADE Database has the most comprehensive database in the world. Referencing the GRADE Database instantly provides all the information needed. If the melt corresponds to the specification, then you’re good to go. If it doesn't, the question that follows is how to determine what other materials should be added to the melt necessary to bring it in line with grade specifications?
There are numerous ways of doing this: Depending on previous experience, trial and error can be used, as well as using spreadsheets and diagrams to run through manual calculations. With both of these methods, it isn't possible to be 100% positive that the melt has been corrected without fault.
It can be expensive and delay the production line if it is necessary to run the whole test-correct-test process over. The most effective way to apply a charge correction process is to get it the right from the first melt run – and that is precisely what charge correction software delivers.
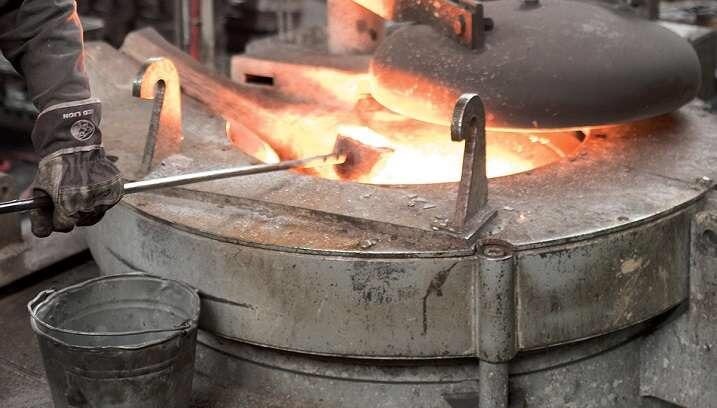
Image Credit: Hitachi High-Tech Analytical Science
Cost-Saving with Charge Correction Software Versus Manual Correction
Taking a look at an existing example, it is clear to see that the extra costs incurred when applying manual charge correction processes. The focus is set on a modest facility in order to keep numbers conservative.
Taking into consideration energy and labor costs alone, it may be surprising to learn that a small steel cast foundry with a single 1-ton capacity induction furnace can save over 20,000€ per year. Time saved will also be enough to run additional batches, making the financial picture even more captivating and desirable. Thus, large-scale facilities can expect greater cost savings and efficient use of resources.
These are the potential savings when using Hitachi’s GRADE Database in line with AdjCalc charge correction software. For a comprehensive demonstration of how these are utilized effectively to save time and reduce costs, watch the on-demand webinar.
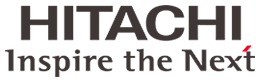
This information has been sourced, reviewed and adapted from materials provided by Hitachi High-Tech Analytical Science.
For more information on this source, please visit Hitachi High-Tech Analytical Science.