Dual-frequency resonance tracking (DFRT) is a technique that utilizes contact mode atomic force microscopy (AFM) to measure a sample’s weak electrical or mechanical responses.
Conventional resonance tracking techniques depend on a phase-locked loop (PLL) to ensure the phase runs persistently, but this approach breaks down with ferroelectric or other materials that, depending on the domain orientation, express a phase reversal.
The benefit of DFRT is fostered in its capacity to measure phase reversal while singly utilizing the resonant amplitude for feedback.
Applications associated with the DFRT technique include electrochemical strain microscopy (ESM), which is sensitive to the ionic-current-induced strain, scanning thermo-ionic microscopy (STIM) – which induces thermal oscillations to measure the strain, and piezoresponse force microscopy (PFM).
DFRT is of particular relevance for the thin-film characterization of ferroelectric and multiferroic materials, as the resonance-enhanced measurements facilitate the evaluation of weaker signals and avoids film breakdown via the use of lower polarization voltages.
While lock-in measurements set to a low frequency are standard for bulk materials, the nano-mechanical response to an electric or mechanical excitation can be significantly improved by turning to a contact resonance technique.
Measurement Strategies
The first step is establishing the contact resonance (CR) by probing the output frequency that is driven either electrically or mechanically when the AFM tip and sample come into contact.
It is then feasible to produce an amplitude-modulated signal (on the signal output) that induces two sideband amplitudes A1 and A2, on either side of the CR.
In the figure, the red curve exhibits the difference A2 - A1 as a function of the drive frequency: this demonstrates a monotonic behavior surrounding the resonance with excellent gain sensitivity and is subsequently applied for feedback.
A PID controller – built-in to Zurich Instruments lock-in amplifiers, further enhanced with the PID Advisor – modulates the difference A2' - A1' between the sideband amplitudes recorded at frequencies fc+/-fm. This difference in amplitude is used as the PID controller’s error signal and acts upon the center frequency fc.
If the resonance frequency varies due to tip-sample interactions, the amplitude difference as measured A2' - A1 may vary, leading to a shift in the drive frequency, as illustrated in the figure. At resonance, A1 and A2 collide and the setpoint is set to zero.
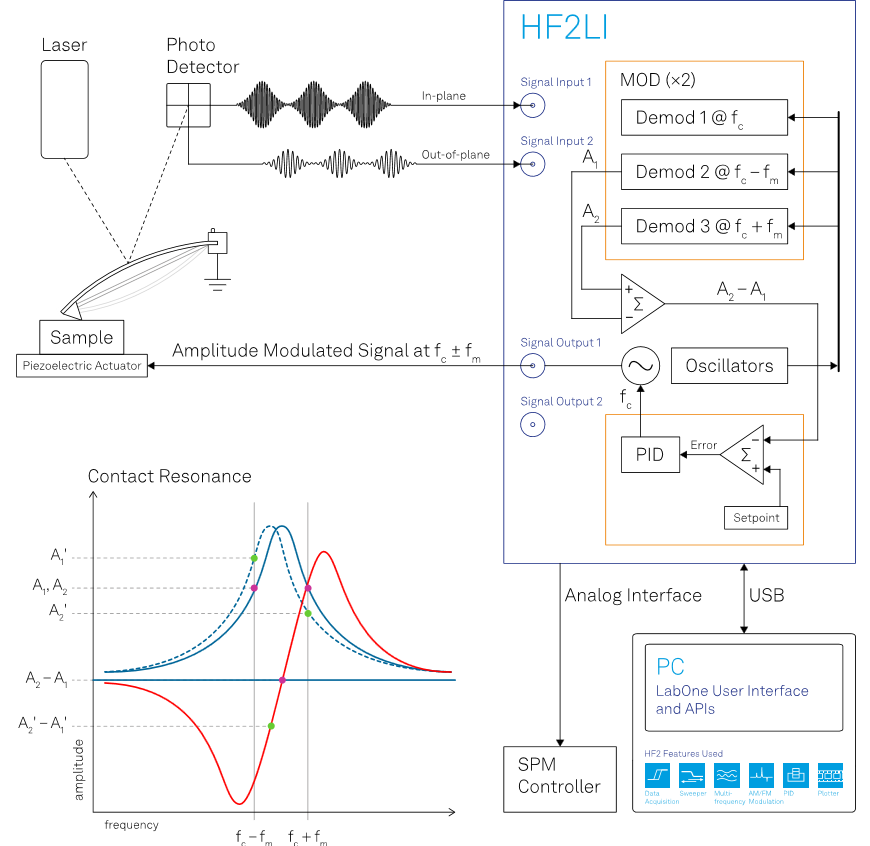
Image Credit: Zurich Instruments
Standard PFM versus DFRT-PFM
This table demonstrates how employing Zurich Instruments for DFRT-PFM measurements reaps numerous benefits in contrast to standard PFM measurements:
Source: Zurich Instruments
Criterion |
Standard PFM |
DFRT-PFM with HF2LI or UHFLI |
Bias modulation frequency |
100 Hz to few kHz |
Up to 50 / 600 MHz at CR |
Frequency
tracking |
None (static) |
Frequency tracking topography, used as a reference for lock-in measurements |
Frequency generation |
Up to 2 frequencies
(with 2 lock-ins or 1 HF2LI) |
Up to 6 frequencies or 2 CRs |
Lock-in measurements |
Single lock-in measurement
of amplitude and phase |
Center and sideband amplitudes and phases, PID error, frequency shift |
Feedback signal |
None (open loop) |
Difference of sideband amplitudes (A2-A1), PID Advisor |
Choice of drive frequency |
Manual tuning,
fixed frequency |
Always at CR, higher signal-to-noise ratio (SNR) |
The Benefits of Choosing Zurich Instruments
- Using the same Zurich Instruments lock-in amplifier, sideband detection, bimodal excitation and PID feedback on the amplitude difference are all easily accessible.
- Both inputs of the HF2LI Lock-in Amplifier can be utilized for measuring in-plane and out-of-plane components simultaneously, thus facilitating the study of the entire piezoelectric vector field (orientation, magnitude and polarity).
- Zurich Instruments offers a simple solution in the form of an add-on to any third-party AFM microscope: only the sensor deflection (vertical and lateral) and the bias voltage (drive) should be accessible.
- The use of higher harmonic components with DFRT leads to better sensitivity towards ionic current (e.g., ESM), thermally induced strain (e.g., STIM), or other harmonic-related phenomena.
- Sensitivity of measurements can be increased with resonance enhancement techniques – even when the use of a PLL is not possible. The same PID Advisor can enhance any linear feedback loop.
- By synchronizing the data acquisition (DAQ) module with an End-of-Line (EOL) trigger from the Scan Engine, all internal channels can be recorded as multiple images.
- Tracking the resonance frequency results in a reduction in topographical crosstalk, which is vital for samples with high surface roughness.
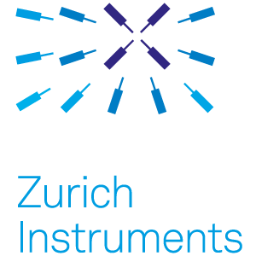
This information has been sourced, reviewed and adapted from materials provided by Zurich Instruments.
For more information on this source, please visit Zurich Instruments.