Food processing facilities extensively make use of metal detectors. These detectors are generally used toward the end of the line. It is the last opportunity to ensure the quality and safety of foods before a packaged product is shipped to eventual consumers.
The central technology in metal detector has invariably had its compromises and limitations. Product effect that can confuse a wet product with metal or noise from inside the plant can disrupt detector signals.
Although metal detection technology has gradually evolved over the years, the needs of food processing have outpaced performance and business needs. There are growing productivity demands, retailer requirements and more stringent regulatory compliance stipulations.
The stakes are also higher: the possibility of an expensive recall and collateral damage through damage to brand reputation which can travel swiftly through social media.
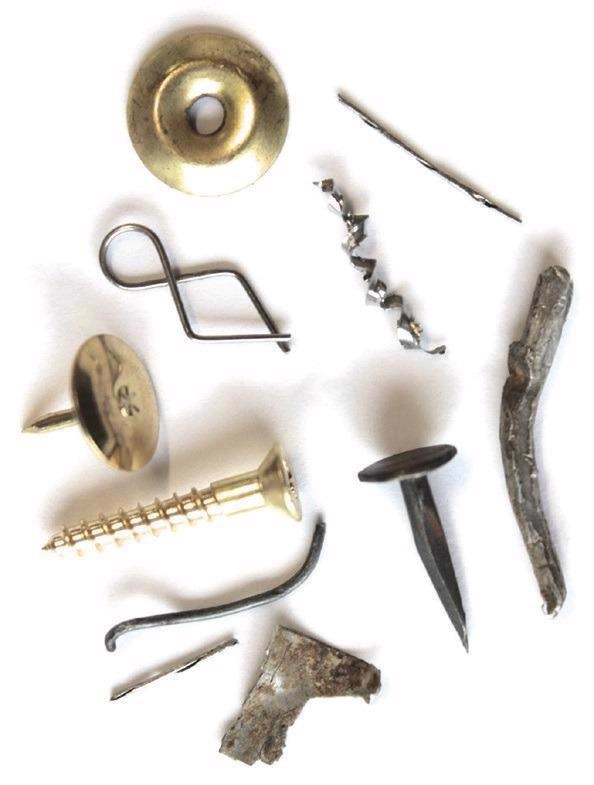
Figure 1. Image Credit: Thermo Fisher Scientific – Solutions for Industrial and Safety Applications
No organization is immune to these challenges. One can visit www.fda.gov and click on the 'recalls' section to peruse the range of food safety issues that are reported daily.
While food companies are migrating to X-ray inspection to detect a wider range foreign objects, not all applications need X-ray inspection if there is a minimal risk of non-metallic contaminants entering the process. The cost of X-ray inspection can be prohibitive for smaller processors, too.
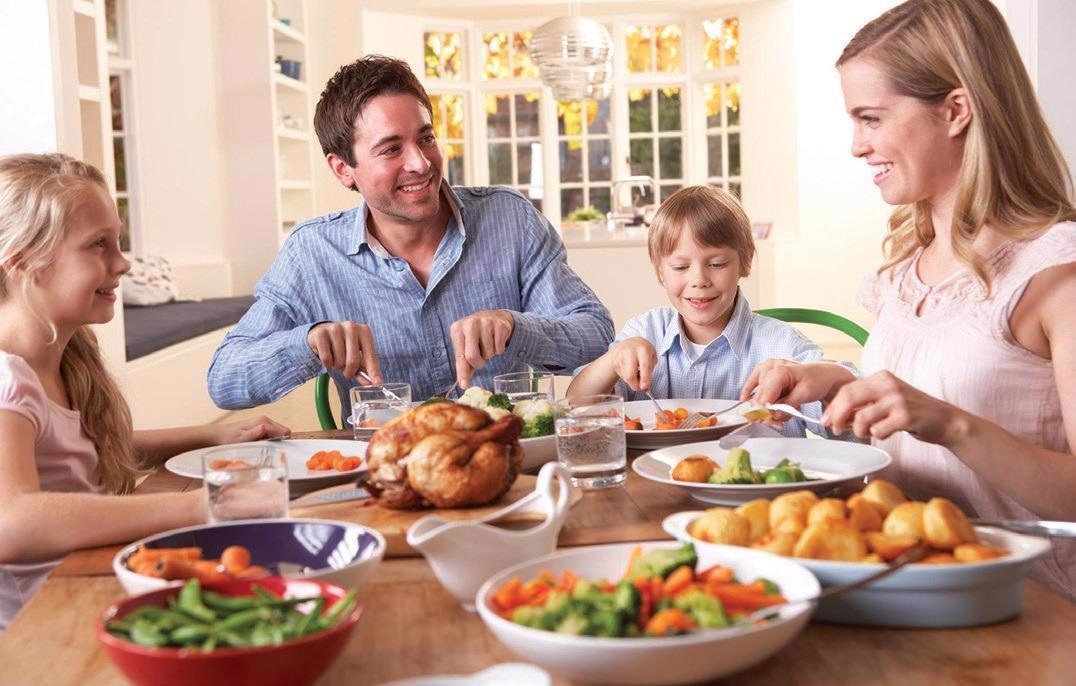
Figure 2. Image Credit: Thermo Fisher Scientific – Solutions for Industrial and Safety Applications
Why Metal Detection is Not Easy
What makes metal contaminant detection so difficult? A simple comparison may help here: why does a piece of jewelry or a coin activate a metal detector at airport security during an outbound flight but not during an inbound flight? What is the reason for the inconsistency?
Similar unpredicatable performance can exist when attempting to detect metals in food. Metal detection is simple when it works, but difficult when it does not. Detectable metal sizes and types may not be what the quality manager needs. Audits can fail. And, if a piece of metal escapes detection the consumer may be the first one to find it. Ensuring food safety demands a more predictable and consistent metal detection solution.
Key obstacles to achieving completely metal-free products:
- The metal detector should be able to detect anything and anywhere in any kind of product, at all the time. But this can be a daunting process considering the amount of production from just a single line in a day, and all the metal types and sizes that could be in the ingredients or come from equipment in the plant.
- Electromagnetic fields are used by metal detectors to identify things that are conductive and magnetic. Most food products are wet or contain minerals and salt, which upon exposure to electromagnetic fields also look conductive and magnetic. But identifying the metal and ignoring the product is not as easy as it sounds.
- Tiny metal foreign objects have very weak signals and the metal detector is working in a factory that has several potential noise sources that can confuse the software and electronics in the metal detector. For instance, at any given time:
- Electronics boxes are broadcasting broad spectrums of radiated noise
- Massive motors are switching on and off
- Temperatures fluctuate from boiling to freezing and vice versa
- Electrical power is fluctuating
- Production equipment is vibrating and causing the antenna present in the metal detector to shift
A New Solution: Multiscan Metal Detection
As one can see, it can be challenging to find the needle in the haystack -- or a piece of stainless steel in packaged meat.
Many of these formidible challenges are overcome through Multiscan metal detection technology. It is in the new Thermo Scientific™ Sentinel™ Multiscan Metal Detector. Sentinel metal detectors with Multiscan can considerably improve the probability of detection and reduce the chance of an escape to virtually zero.
There is No 'Best' Frequency for a Metal Detector
Among all metals, ferrous is the easiest to detect because of its magnetic properties. Iron is attracted by magnets. When a ferrous metal is present in the electromagnetic field, the latter will react the most, and the lower the frequency, the greater the reaction.
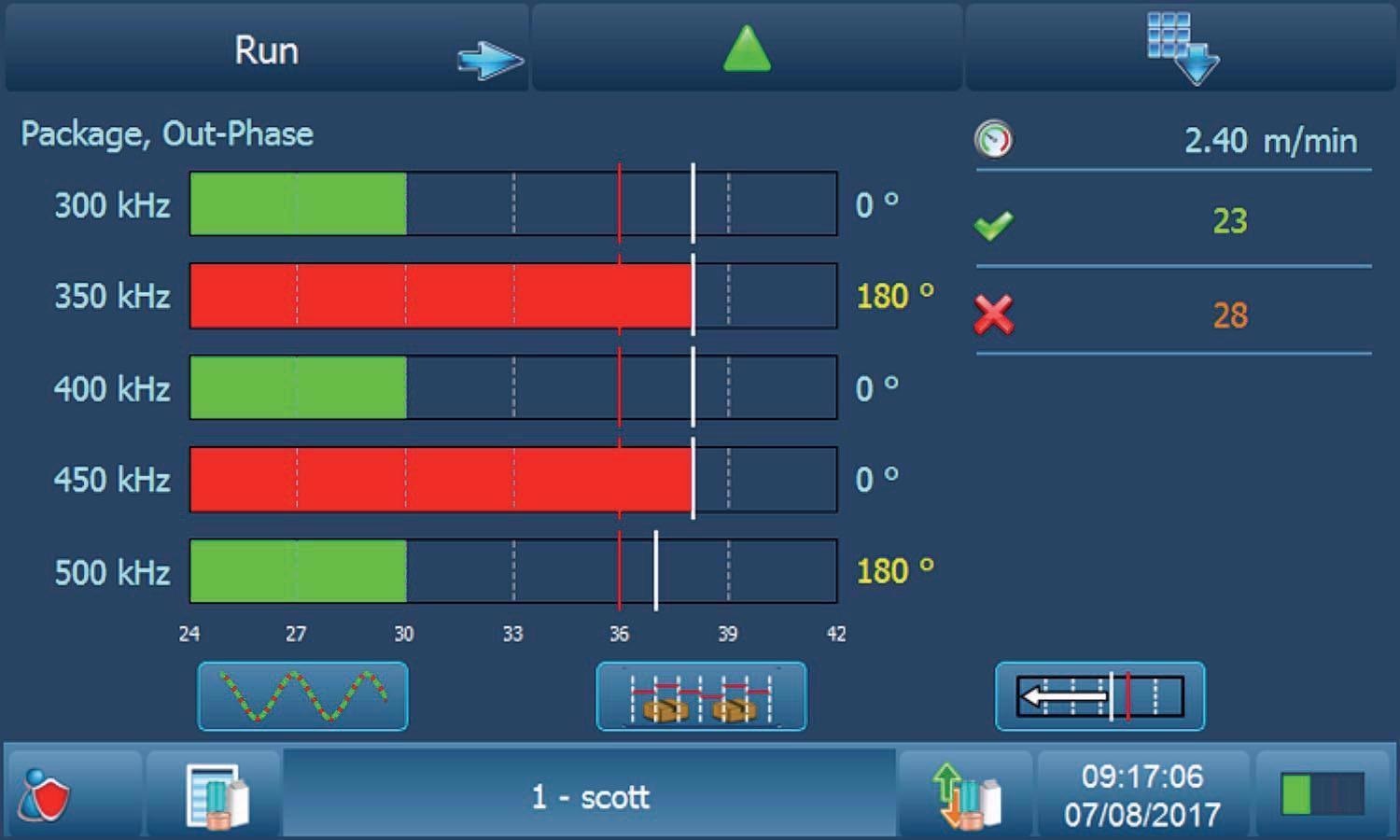
Figure 3. Results from scanning five frequencies at a time using Multiscan metal detection technology. Image Credit: Thermo Fisher Scientific – Solutions for Industrial and Safety Applications
In contrast, stainless steel, containing a small amount of ferrous metal, has little to no magnetic property. It is similar to putting refrigerator magnets on a new stainless steel appliance. To find stainless steel with a metal detector, a high frequency is needed. This is because the high frequency field induces a current in the stainless steel which, in turn, generates a new field that interacts with the original field in the metal detector to create a signal.
Although a logical conclusion is that an ideal metal detector would run one high frequency and one low frequency, it is more complicated. Different conductive and magnetic reactions are exhibited by different sizes of the same metal. Metal alloys also have different reactions. The position, orientation and shape of the metal can alter the resulting signals in a metal detector.
So, which is the 'best' frequency for all metal detection applications? The solution is: as many as one can get at the same time.
This is the principle behind Multiscan technology. The operator selects up to five frequencies from 50 to 1000 kHz. The Multiscan detector rapidly scans through each, essentially providing the benefit of inspection by five metal detectors at a time.
The outcome is that the probability of detection goes up significantly and escapes are virtually eliminated. Sensitivity is also improved because users also have the optimal frequency running for all types of metals of concern.
By using Multiscan technology, the Sentinel Multiscan Metal Detector can detect metal spheres that are up to 50% smaller in volume than previous technology.
A simple graphical user interface and report enable users to easily see how the detector is performing at various frequencies.
Phasing Out Products and Metal Contaminants
Traditional metal detectors employ a method to ignore conductive and magnetic product effects, known as 'phasing.' Anything that passes through the metal detector with a known ratio of the magnetic-to-conductive signal below a certain threshold is overlooked because it is not a piece of metal but the product.
The issue is that the signals produced in a metal detector by random metal pieces can differ considerably. Ultimately, the phase angle of the signals precisely corresponds with the phase angle of the product. Since the metal signal is very small with respect to the product, the metal is not detectable.
For example, searching for a small bit of stainless steel concealed in a small package of cheese, the operator could slightly vary the frequency (this distinguishes the product and the phase angles in the metal) and identify it, but this would also mean not being able to detect a different size of stainless steel because the phase angle of this contaminant lines up precisely with the cheese.
So, the issue is not resolved and simply moved somewhere else. It is kind of like patching a hole in a roof and later drilling a new hole in another location; water would still enter.
This is a nuanced but crucial real-world concern because perfect detection is not provided by any single-frequency metal detector. Adding another fixed frequency makes things slightly better but in the end, the roof still has holes.
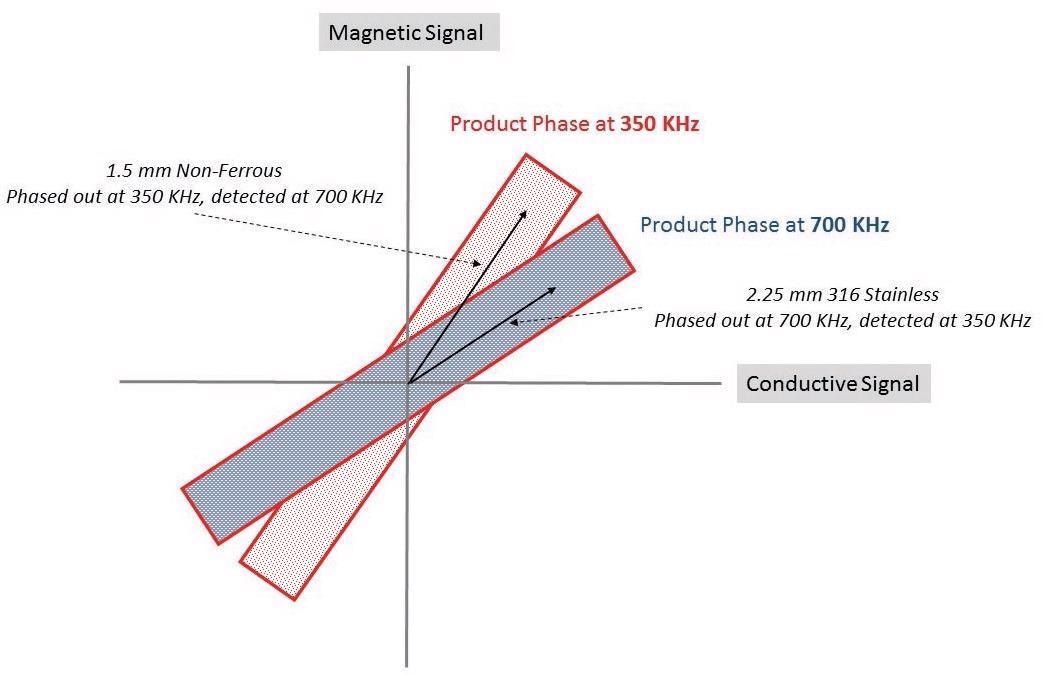
Figure 4. Stainless and non-ferrous phased out at one frequency but detected at another. Image Credit: Thermo Fisher Scientific – Solutions for Industrial and Safety Applications
This is where Multiscan technology resolves the problem. If a single frequency means a metal piece is phased out, another frequency identifies it and the other way round. Since five frequencies are running at a single time, there are more opportunities to find the containant.
Another analogy: If you're buying a used car, do you simply stand before the vehicle and peer at the bumper, windshield and hood? Of course not! You walk all around the vehicle and scan as many areas and angles as possible to see what kinds of issues the vehicle may have; you 'multiscan' before purchasing.
Overcoming Noise to Detect Small Metal Pieces
People experience audible noise in their daily lives: an airplane overhead when sitting on the patio, a person speaking on the telephone next to an office, or a washing machine running in the background when people are trying to watch television.
Noise gets in the way of the experiences above. Similarly, it impacts a metal detector trying to find a very subtle signal change such as finding a 1-mm diameter metal piece in a loaf of freshly baked bread.
The metal detector needs to have a 'quiet' background so that it can focus on finding the metal 'signal.' This is called a signal to noise ratio and the bigger the better.
Equipped with Multiscan technology, the Sentinel detector addresses this problem in numerous ways to improve performance. The metal detector antenna or coils are cast in a highly rigid material so they do not shift with respect to the stainless steel case. This prevents against small, false signals.
The internal electronics have the protection of multiple levels of shielding so that fields from the outside do not impact detection performance. The power supply design rejects noise in the electrical supply and an additional line filter is also added. A software filter is run on the detection signals to remove any noise that may enter the aperture that is not at the target frequencies.
Indeed, in extreme cases, some situations may still exist in which certain noise cannot be eliminated. In that case, users can simply adjust the frequency being effected and tune it out. And this can be effortlessly achieved through the graphical user interface.
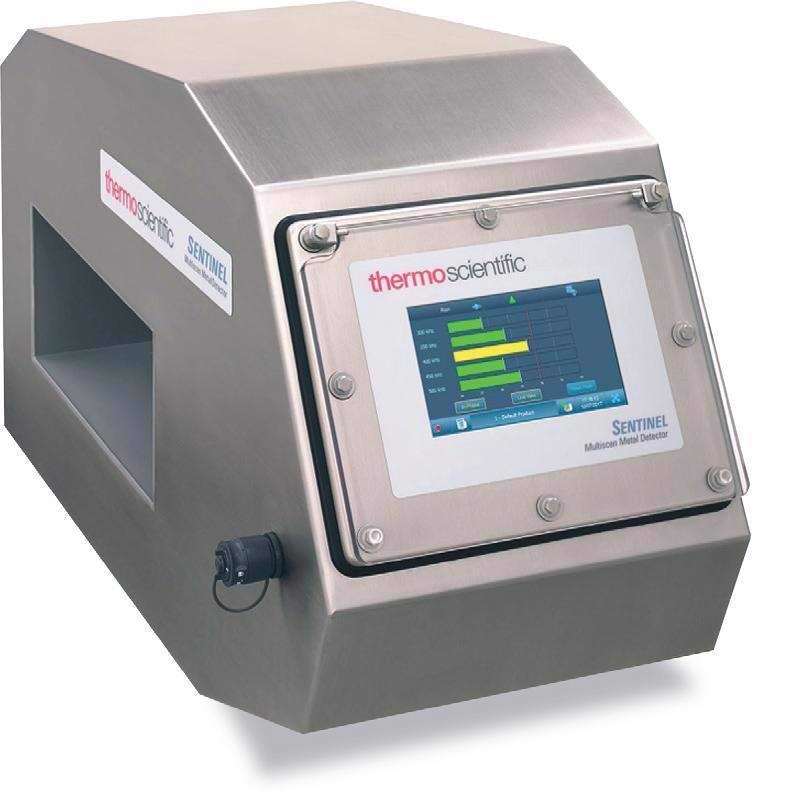
Figure 5. The Sentinel multiscan metal detector design tunes out noise for optimum detection performance. Image Credit: Thermo Fisher Scientific – Solutions for Industrial and Safety Applications
Other Important Benefits of Multiscan
Although metal detection has its challenges, evn five-frequency Sentinel metal detectors are easy to use. Scanning five frequencies at a time does not mean that a user will get five times the number of false rejections.
To make this technology user-friendly, the Sentinel metal detector has wizards, graphical displays and reports for ease of set up and adjustment. With auto-learn wizards, it is easy pick any set of frequencies, collect data from 1 to 10 packages and then automatically set gain, thresholds and phase, among others.
Users get instant feedback during and after the operations to see results.
During operation, users can view all the chosen frequencies in real-time and generate a report of the last 20 rejects to see what caused them. If any of these rejects were false, it's easy to make adjustments.
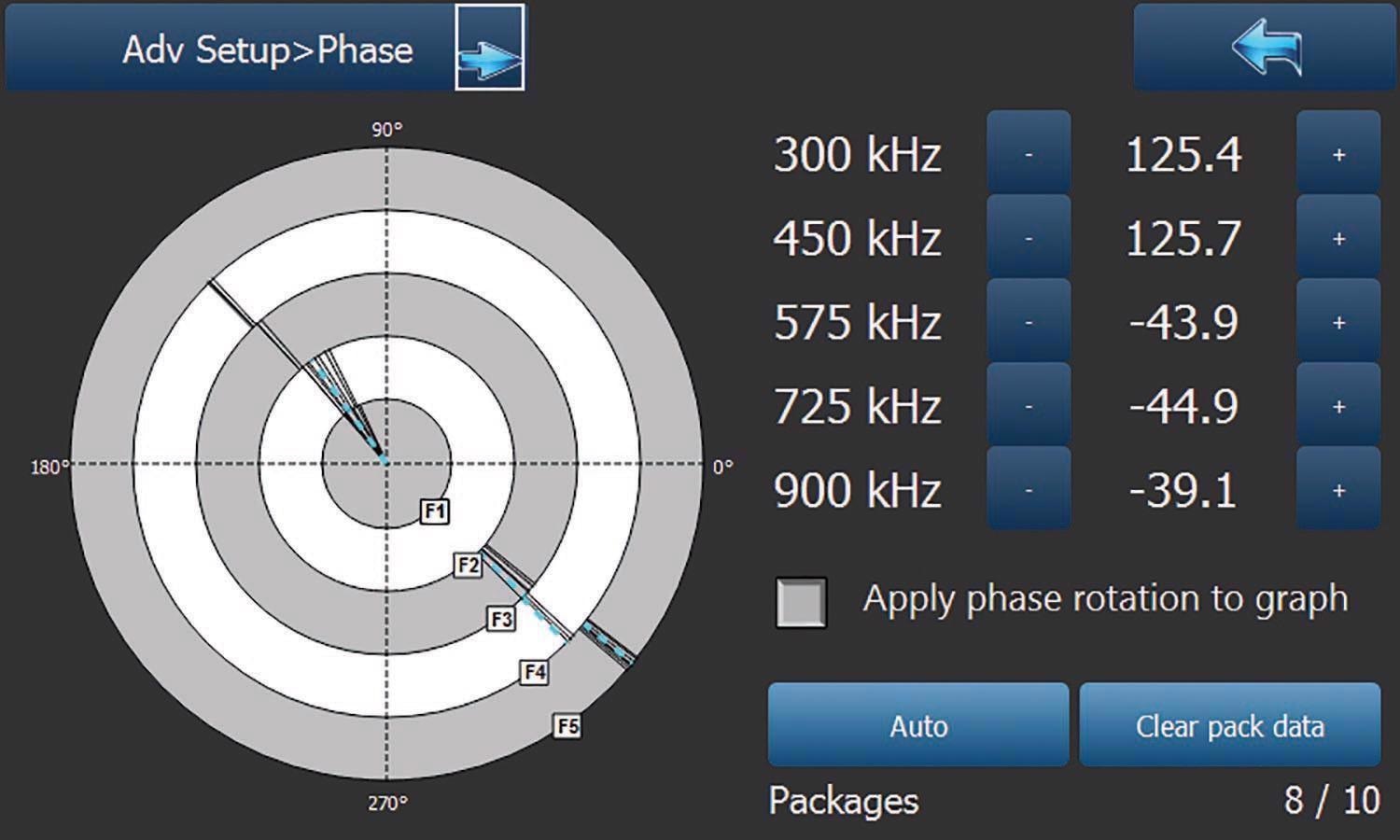
Figure 6. Phase learn for all five frequencies. Image Credit: Thermo Fisher Scientific – Solutions for Industrial and Safety Applications
If there are high levels of noise on any frequency, it can be easily changed in the software. It's also easy to disable a frequency if it is not detecting anything. There is no need for a service call to make such adjustments.
Metal detection veterans know that balance is also a major parameter for effective detection. There should not be any signal when a metal is not in the aperture. With Multiscan technology, all the frequencies that are being used should also be balanced.
To achieve this, the Sentinel detector automatically balances the frequencies. Although it takes a few minutes initially, it has a major effect on performance. The last balance data is used to save time unless users add a new frequency.
To eliminate subtle imbalances, the software runs an auto-balance process constantly. A balance diagnostic screen for advanced users allows them to ensure that balance is accurate and that there is no internal issue with the metal detector.
Conclusion
When it comes to food safety, how good is good enough? This is a complicated question to answer because everyone is hoping for complete safety. In this context, the cost of failure can be significant and can seriously damage the reputation of a company or brand, not to mention risking the health of consumers.
Until the development of Multiscan metal detection, dual- or single-frequency metal detectors had drawbacks and the risk of escape. But today, that is no longer the case.
The latest, innovative technology allows up to five times the protection with unrivaled, almost infinite, flexibility. It is now fast and simple to obtain the best real-world metal detection performance.
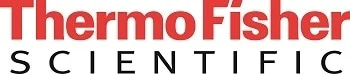
This information has been sourced, reviewed and adapted from materials provided by Thermo Fisher Scientific – Solutions for Industrial and Safety Applications.
For more information on this source, please visit Thermo Fisher Scientific – Solutions for Industrial and Safety Applications.