Primary concerns to food processors are product quality, food safety and brand protection. Fulfilling consumers’ demands in a fast-paced market with growing levels of uncertainty has underlined the significance of a safe supply and smooth running supply chain.
It starts with the potential to effectively and efficiently support the safety and quality of food products that enter the production line, such as inspection for foreign objects and microbiological contaminants.
Quick changes in supply needs have a major effect on processing lines in the short term and entail that food processors reconfigure or plan for more flexibility in their inspection processes going forward.
For instance, package sizes are changing to accommodate the shift in demand for big food service and institutional packages to single-serve and at-home packages.
The acceleration of shipping-friendly packaging for online orders was already underway and then accelerated during the global pandemic. It is anticipated the trend will continue and that there will be growth in lighter weight but strong packages for home delivery.
Consumers could be slow to retreat from a stock-up mindset, which could sustain the trend toward seeking out shelf-stable, 'middle-of-the-store,' low-cost food products.
Some manufacturers have reduced the number of stock-keeping units (SKUs) produced by them to decrease time-intensive product changeover and allow production of a greater volume of more popular sizes and varieties of packaged foods.
Pandemic-weary consumers and brands are beneficiaries of the proactive food safety measures put in place to comply with the Food Safety Modernization Act of 2011.
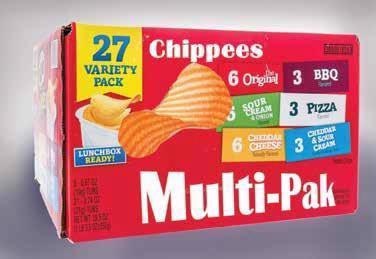
Figure 1. Image Credit: Thermo Fisher Scientific – Solutions for Industrial and Safety Applications
In the recent past, software-based traceability and recordkeeping have become essential to food safety programs. In addition, equipment manufacturers have tackled the requirement for modernized, easier and faster user interfaces as food manufacturers migrate to more automation, leading to fewer skilled workers.
It is believed that process enhancements intended to assure food safety will persist, with greater discipline and more innovations at each stage in the supply chain.
In response, manufacturers of food inspection technology have devised novel inspection solutions to more precisely detect metal foreign objects—the most common type of contaminant—to support food processors in meeting retailer codes of practice and regulation.
Food Metal Detection Challenges
In spite of its inherent drawbacks, metal detection technology has traditionally been a workhorse for the food sector. For food metal detectors, the central principle of operation is that a transmitter excites a signal as food contaminated with metal transverses the aperture, setting off a detection.
In reality, the signal produced by the food itself, called the product effect, can imitate a contaminant, requiring the detector to be able to differentiate the real metal from the product effect. Failure to differentiate them can lead to expensive false rejections or even product escapes.
The food plant environmental also has challenges, such as vibrations, moisture and other environmental factors that can interfere with the precise performance of metal detectors.
Besides this, the device should log set-up changes and save performance statistics for documentation purposes as part of a bigger, holistic view of an organization’s food safety program in the event of an issue.
The Selectscan Metal Detection Solution
Selectscan technology allows food processors to have a simple means to rapidly detect the single best frequency to use in a metal detector for a certain application. It can tune out product effect and adapt results to account for electromagnetic interference and temperature variations.
In parallel, it documents results from every production run. It is an entirely new and holistic metal detection solution.
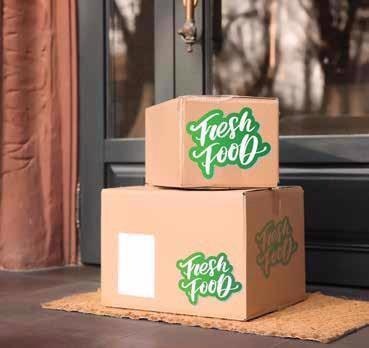
Figure 2. Home meal delivery is among the trends driving single-serve and at-home package sizes. Image Credit: Thermo Fisher Scientific – Solutions for Industrial and Safety Applications
Apart from fulfilling all the stated needs, the Selectscan technology can detect metal foreign objects up to 25% smaller in volume than the earlier single-frequency technology. Selectscan technology has many automated features that would otherwise need to be programmed by skilled personnel.
An Autolearn feature is key to the Selectscan technology. This feature takes the guesswork out of improving detection performance. Through an intuitive, on-screen wizard, users are guided through a simplified setup that can be achieved in a matter of minutes. The outcome is an operating frequency that can detect even the smallest metal contaminants for the particular application.
With Autolearn a food product that is not contaminated is first run through the aperture. Then, stainless-steel, ferrous and non-ferrous metal spheres of the specified sizes utilized for audits are added to the product and run through the detector. Based on the results, Autolearn will find out the best detection frequency and set all the sensitivity parameters automatically.
A proprietary visual graphic scoring algorithm also shows how every metal sphere can be found in a production run. As described in the next section, the metal size, best frequency and detectability score are demonstrated intuitively, so that users can more easily interpret results for their application.
By doing more test runs with metal foreign objects, the Autolearn algorithm will allow optimized set up and greater assurance that the product is safe.
On the other hand, setting up a conventional single fixed-frequency metal detector involves trial and error and is time-intensive. An experienced operator may take hours to adjust and test the metal detector at every new frequency to establish if detection specifications can be achieved. The operator will compromise on performance optimization for time.
Flexibility
Users know that different frequencies work best for different applications. Selectscan technology can work in an expansive range of frequencies from 50 to 1000 kHz for performance at the best frequency for each application.
For example, cheese or potato chip applications may need to detect at a low frequency to control the signal produced by the conductive salt content, whereas a high frequency may work best to identify stainless steel foreign bodies in a mineral-rich vegetable.
Selectscan technology can quickly and easily call up a saved product file for application changeovers.
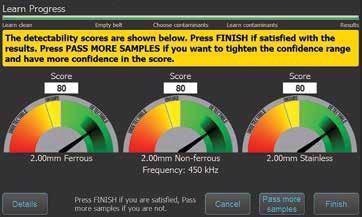
Figure 3. Autolearn rapidly guides a user through product set-up to maximize operational efficiencies and detection performance, supporting improved plant efficiency. Image Credit: Thermo Fisher Scientific – Solutions for Industrial and Safety Applications
Additional Benefits
The Selectscan metal detector includes other features required food companies that place a high priority on food safety. A sophisticated feature set allows independent modifications and traceability.
Phase tracking continually measures and modifies the product phase to sustain performance while the product composition changes. This is a challenge with a thawing frozen product that phrase tracking manages, removing the need for expensive line stoppages or intervention by users.
Likewise, Auto Phase Relearn will re-sync the product phase following a prolonged break or a big temperature variation to prevent a false reject without the need to push even one button.
The system collects data that can be easily read and organized by product including the overall numbers of rejected and accepted packs. This makes subsequent batch analysis easier and supports production efficiency.
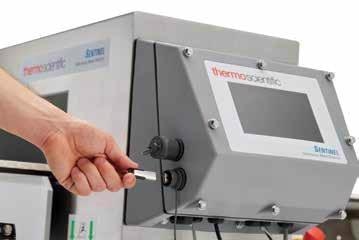
Figure 4. Image Credit: Thermo Fisher Scientific – Solutions for Industrial and Safety Applications
Since each application is distinct, the best practice is that the actual food product is tested in a laboratory setting to confirm system performance and detection capability before purchase.
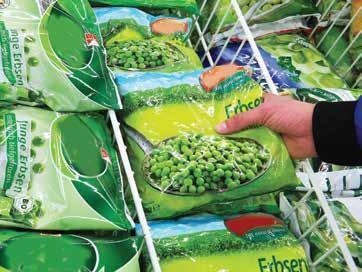
Figure 5. Selectscan’s phase tracking adapts to thawing frozen products without requiring user intervention. Image Credit: Thermo Fisher Scientific – Solutions for Industrial and Safety Applications
Conclusion
Developments in foreign object detection technology are pushing the limitations of detectable contaminant size and type in support of improved food safety. Manufacturers are also responding to food processor needs for ease of use, flexibility, documentation and efficient operation. Combined with a product test specific to the application, these solutions deliver better brand protection and peace of mind.
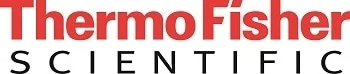
This information has been sourced, reviewed and adapted from materials provided by Thermo Fisher Scientific – Solutions for Industrial and Safety Applications.
For more information on this source, please visit Thermo Fisher Scientific – Solutions for Industrial and Safety Applications.