A foremost concern of food processors is the safety and quality of food. Cases of foreign material contamination are reported every year, leading to recalls and potentially compromising the safety of consumers. This fallout can prove to be costly and damage the reputation of a food processor’s brand.
Food manufacturers must keep their products safe, which takes proactive steps to inspect products for foreign objects and meet or even exceed food safety regulations.
Metal detectors can offer an effective defense by identifying stainless-steel, non-ferrous and ferrous metal contaminants in food products. Metal detection has been used by food processing facilities for many years and is a tried-and-true inspection solution. But this method comes with certain risks and challenges.
Metal detection can be a challenge when a food has product effect. This occurs when the metal detector's signal confuses a salty or wet product with a metal foreign object. It can be difficult to compensate for product effect and adjustments in settings to overcome it may require a service call.
New technologies are affording manufacturers a better ability to inspect for foreign objects more easily and in support of greater efficiency demands and changing consumption patterns and other market demands.
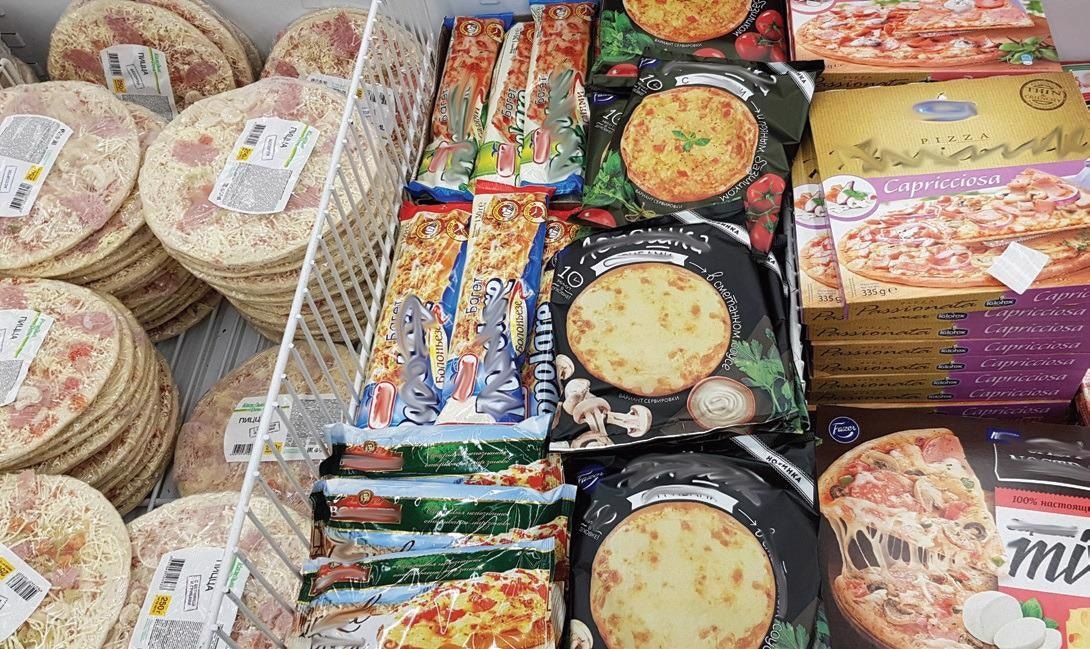
Figure 1. Image Credit: Thermo Fisher Scientific – Solutions for Industrial and Safety Applications
Changing Consumer Behavior
The COVID-19 pandemic swept in a rapid behavioral change in the way people bought and prepared food. Stay-at-home orders restricted or eliminated out-of-home meals. This trend is anticipated to persist even as constraints are lifted.
As per the American Frozen Food Institute,1 90% of consumers in the United States are eating more meals at home, and more numbers of people preferred frozen foods compared to the pre-pandemic period. With extended shelf-life, potential to stockpile in case of shortage of food and also the potential to restrict trips to grocery stores to avoid crowds, frozen foods offered a popular and convenient solution.
90% of U.S. Consumers are Eating More Meals at Home
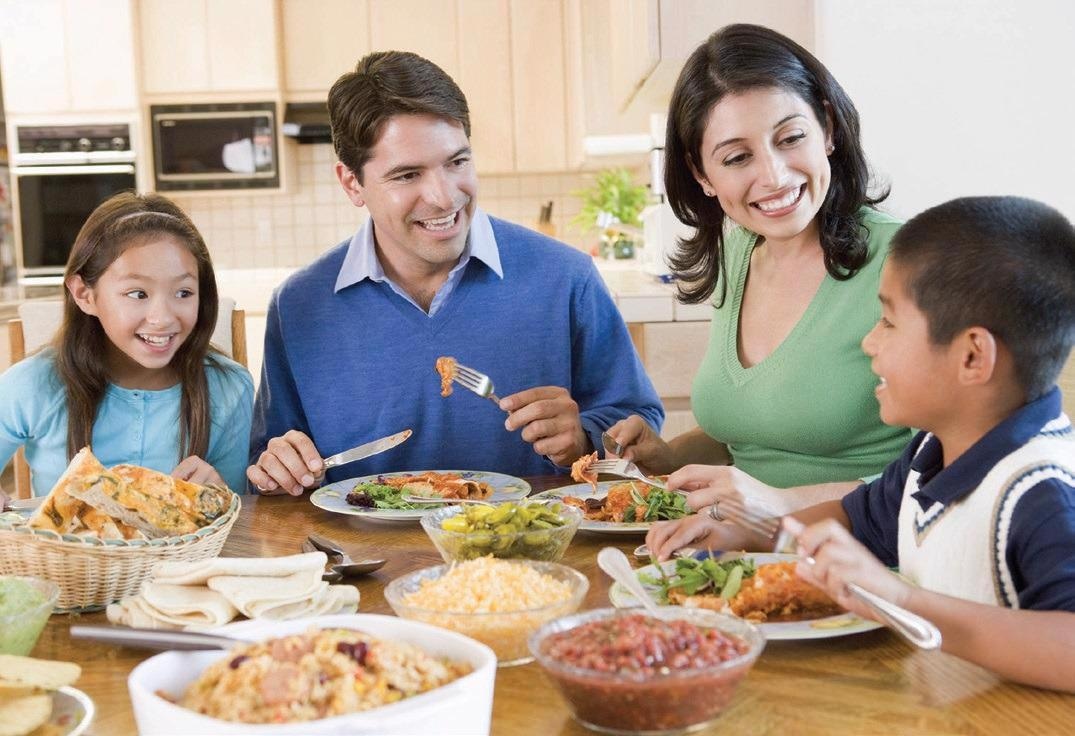
Figure 2. Image Credit: American Frozen Food Institute.1
Frozen food sales in the United States have almost doubled as a result. A similar trend was also seen beyond the United States, with frozen food sales growing 33% in the United Kingdom, 42% in France and 45% in Italy, according to IRI.2
After the initial surge in the purchase of frozen food, sales leveled out but continued to remain high.
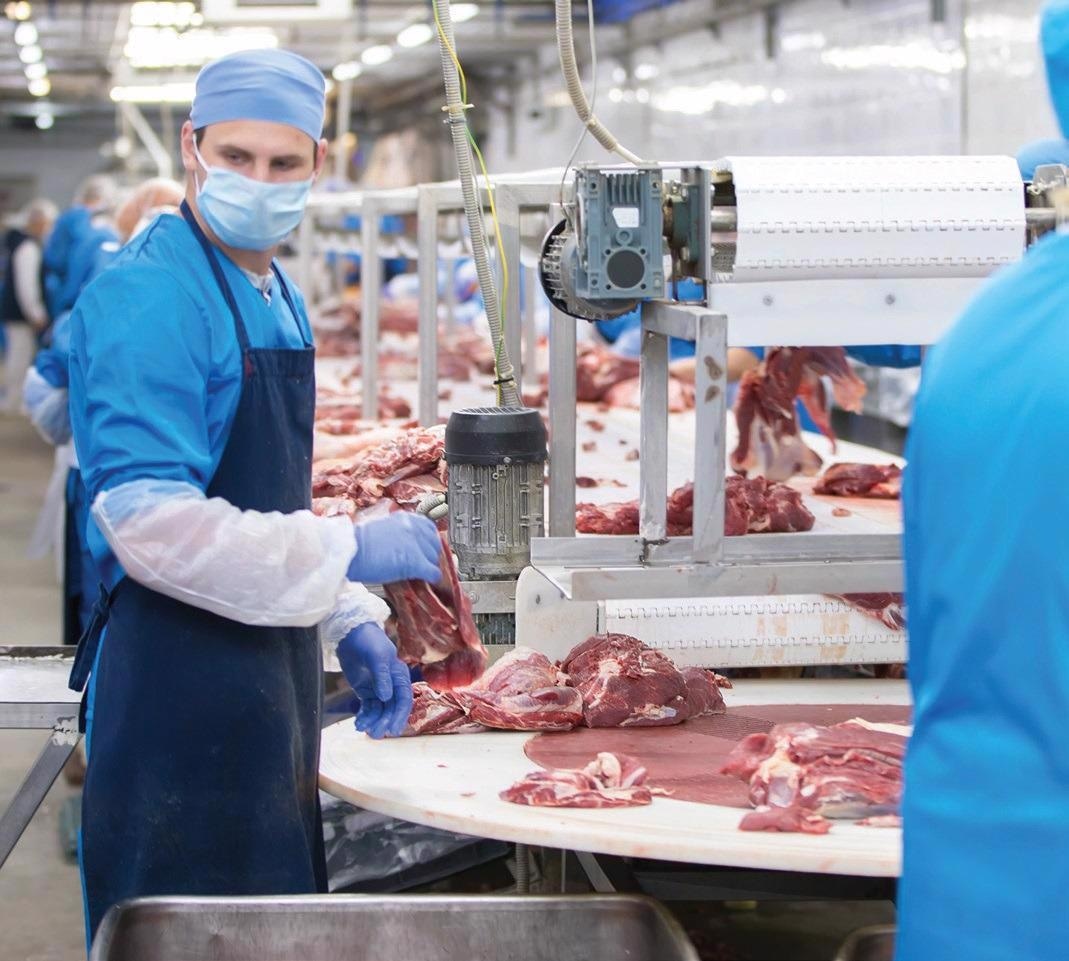
Figure 3. Image Credit: Thermo Fisher Scientific – Solutions for Industrial and Safety Applications
Adapting to Meet Challenges
While food processors have taken measures to protect against a viral outbreak, such changes can impact productivity. Even before the difficulties posed by the COVID-19 pandemic, the need was acute for higher throughput and more efficiency.
Therefore, automation is proving to be more important than ever. According to PMMI,4 52% of food processors prefer to install more automation. With it, food processing facilities can become more productive, and therefore, less time and labor are required to complete a given task.
Luckily, there are novel technologies to help ensure the safety of frozen foods and meet demand in rapidly evolving circumstances.
New Technology to Meet Inspection Challenges
The Thermo Scientific™ Sentinel™ 1000 Selectscan Metal Detector is one of the examples of these innovative technologies.
It is a flexible, high performing contaminant detection solution. Selectscan—the advanced metal detection technology— enables a user to select the ideal frequency for each application, from 50 to 1000 kHz for a higher level of food safety.
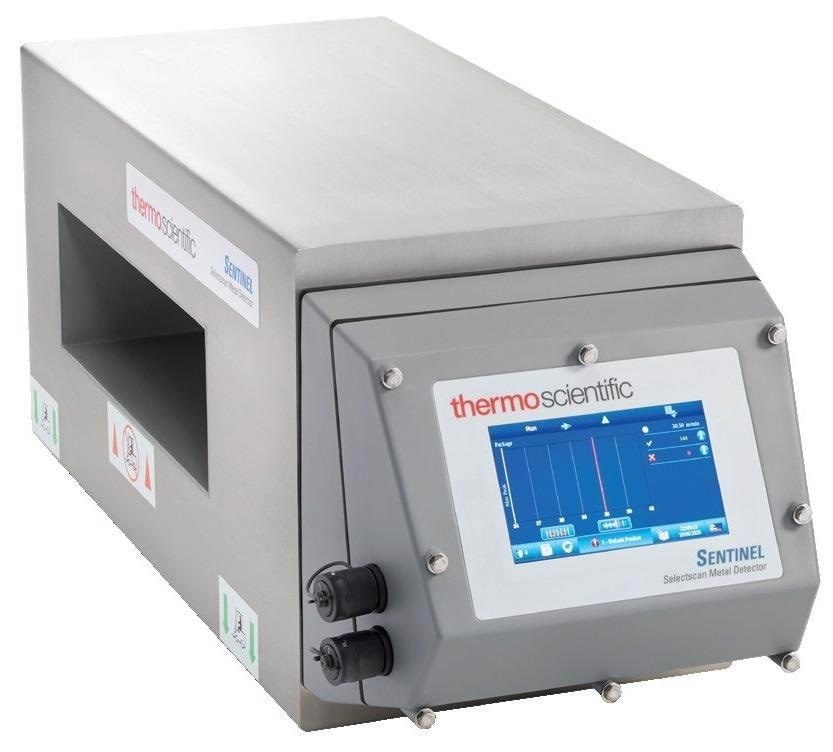
Figure 4. Image Credit: Thermo Fisher Scientific – Solutions for Industrial and Safety Applications
An Autolearn feature rapidly guides a user step-by-step through product set up to choose the right operating frequency and optimizes sensitivity and phase settings.
The combination of Autolearn and Selectscan technology also reduces the touch-time required for setup and product changeovers.
Workers at a range of skill levels can make adjustments; no specially trained staff need to always be available and no service call is needed to optimize detection or change from processing one product to another.
The Sentinel 1000 metal detector has a rich feature set, such as an advanced phase tracking feature that is valuable to frozen food processors as a product may thaw in a warmer environment.
The Sentinel 1000 metal detector can automatically compensate small, gradual changes over time. By using phase tracking, no manual intervention is required to re-adjust the device. The unit will correct on its own during a thaw without needing an operator to touch even a single button.
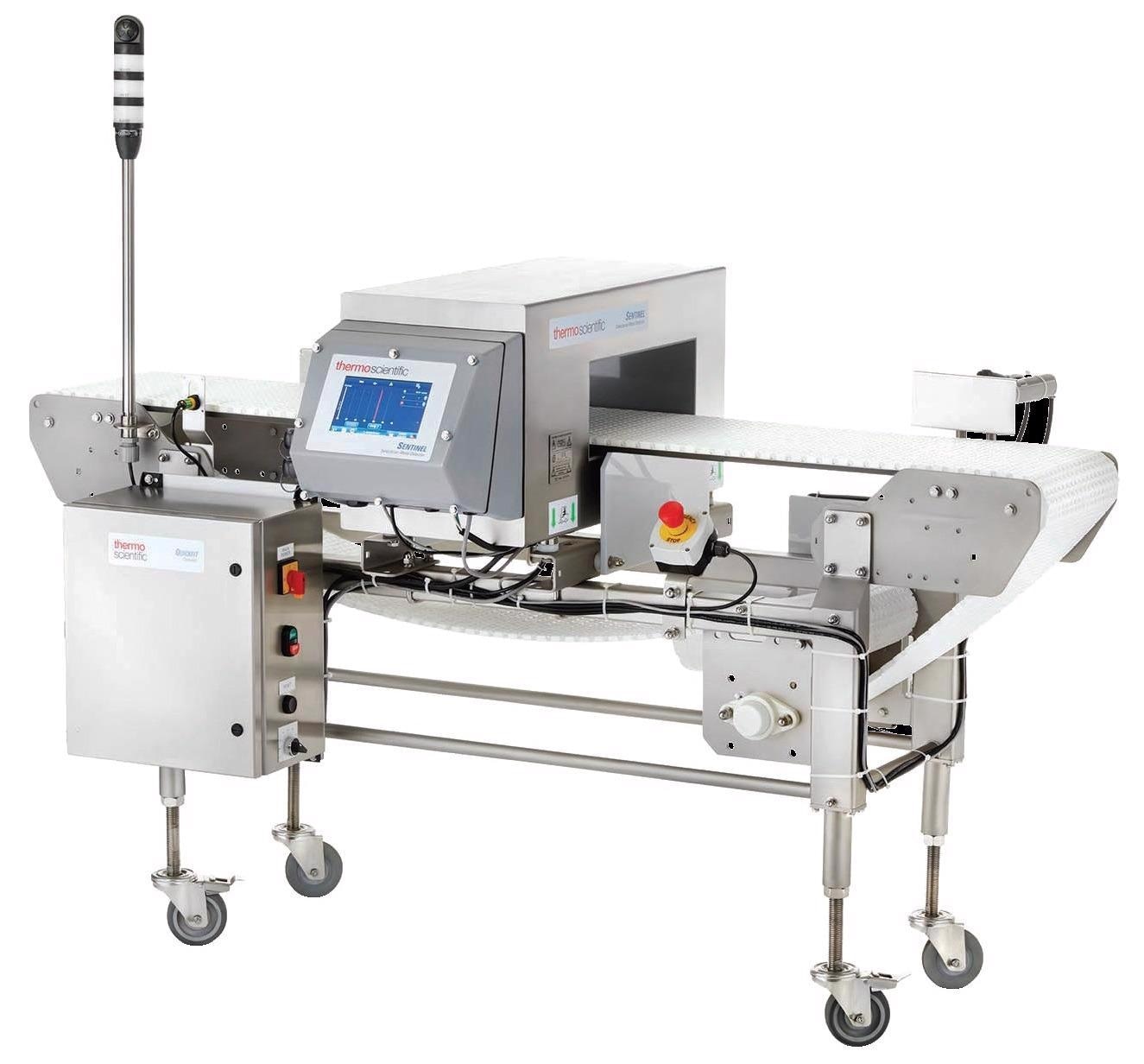
Figure 5. Image Credit: Thermo Fisher Scientific – Solutions for Industrial and Safety Applications
Moreover, the device itself can be cleaned and disinfected easily to avoid virus transmission through equipment contact. The system features a resilient stainless steel case, an epoxy aperture liner and a plastic front panel collectively rated to the IP69K ingress protection standard. The design allows repeated cleaning routines to reduce the risk of viral transmission while protecting the inner electronics and without compromising performance over time.
The Sentinel 1000 metal detector addresses product effect, arguably the most difficult and classic metal detection challenge. Frozen foods generally run as 'dry products' since they lack conductivity caused by moisture when frozen solid. Still, frozen foods will exhibit some product effect which needs to be overcome to ensure effective detection.
To illustrate the efficacy of the Sentinel 1000 metal detector, a test was conducted utilizing frozen ready-to-eat meals that included rice, steak, spiced fruit and gravy. The trays were run through a 250 x 125 mm aperture.
Using Autolearn, the Sentinel 1000 metal detector chose a 450-kHz operating frequency in less than 10 minutes. Metals as small as 0.8 mm nonferrous and ferrous and 1.2 mm stainless steel diameter spheres were identified consistently, achieving a high level of food safety in a short time. Although the 450-kHz operating frequency worked well for this application, a different frequency may be the right one for other frozen foods.
By homing in on the optimal frequency for the application, small metal contaminants can be consistently detected that could not be using other single-frequency technology.
Arguably, the Sentinel 1000 metal detector is the most robust single-frequency metal detection solution available, with the flexibility and features required to keep frozen food safe in the new normal and beyond.
References and Further Reading
- AFFI (2020) https://affi.org/wp-content/uploads/2020/documents/Frozen%20Food%20Sales%20Amid%20COVID-19%20Consumer%20Research%20-%20FINAL.pdf
- IRI (2020) https://www.iriworldwide.com/en-us
- CDC.gov (2020) https://www.cdc.gov
- Food Engineering interview with PMMI VP Jorge Izquierdo (August 10, 2020)https://www.foodengineeringmag.com/articles/99054-food-processors-cope-withsupply-chains-pandemic-and-changing-customer-needs
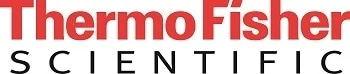
This information has been sourced, reviewed and adapted from materials provided by Thermo Fisher Scientific – Solutions for Industrial and Safety Applications.
For more information on this source, please visit Thermo Fisher Scientific – Solutions for Industrial and Safety Applications.