The presence of water petroleum products, such as jet fuel, lubricating oils, or other similar products, can have damaging effects. Moisture is typically associated with corrosion and wear of an engine.
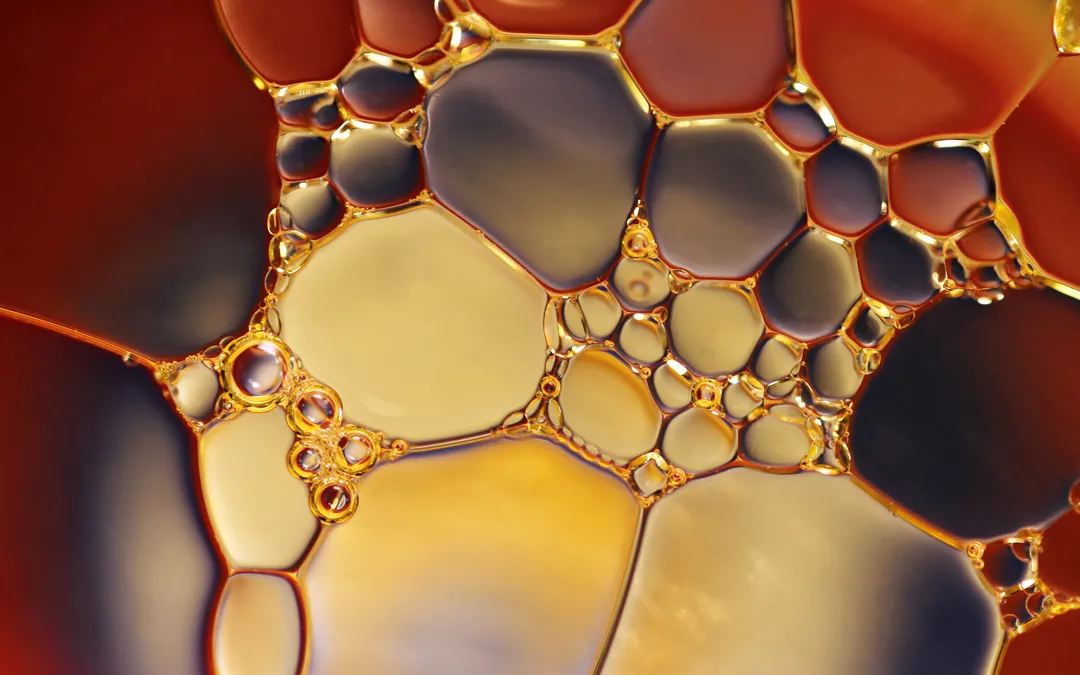
Image Credit: Metrohm AG
Determining the water content of petroleum products can avoid damage to expensive infrastructure and facilitate secure, safer operations.
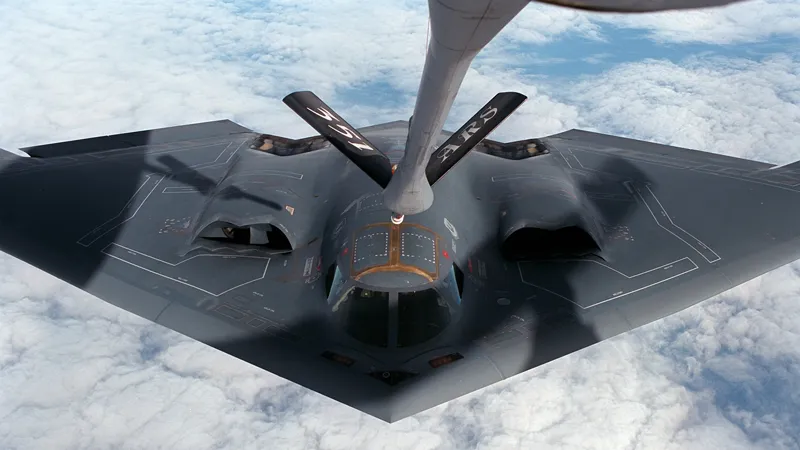
Image Credit: Metrohm AG
One standard that is generally cited for moisture determination in the specifications of various petroleum products is ASTM D6304: “Standard Test Method for Determination of Water in Petroleum Products, Lubricating Oils, and Additives by Coulometric Karl Fischer Titration.”
It has been updated recently – January 2021 – and now presents three procedures for the precise determination of moisture.
Direct sample injection into the titration cell (Procedure A) is advised for low viscosity samples without any anticipated interferences.
Alternatively, an oven (Procedure B) or water evaporator accessory (Procedure C) can be used to analyze samples that do not easily dissolve in Karl Fischer reagent, viscous samples and samples with components that are anticipated to interfere with the Karl Fischer reaction.
This article will highlight these three procedures and then establish when it is appropriate to use each one.
Establishing what the moisture content is in petroleum products doesn’t have to be convoluted or messy. Visit Metrohm’s website to discover more about the latest automated measurement capabilities facilitated by ASTM D6304.
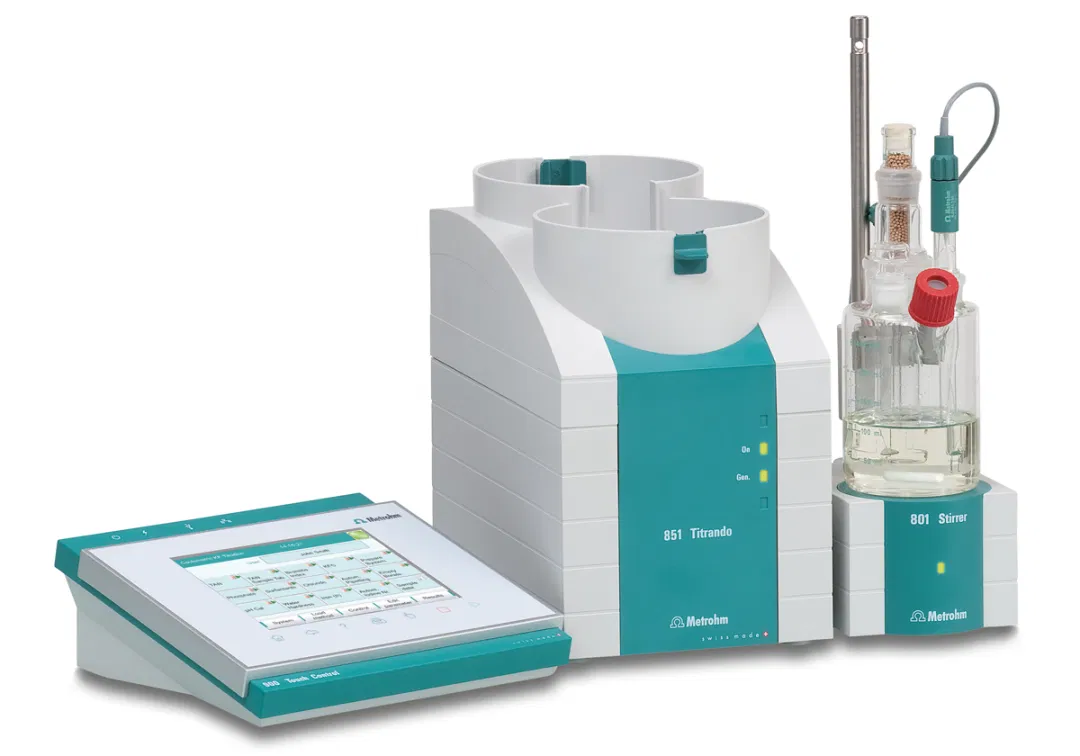
A coulometric Karl Fischer Titrator such as the 851 Titrando from Metrohm is the basis for all three procedures of ASTM D6304. Image Credit: Metrohm AG
Procedure A: Direct Injection
The direct sample injection into the titration cell is well-advised for low viscosity samples without any interferences anticipated. Injecting an aliquot of known mass or volume into the conditioned titration cell of a coulometric Karl Fischer apparatus, where it is automatically titrated, and the results are determined.
Method D6304 allows for the use of coulometric generator electrodes with and without a diaphragm. It is recommended to utilize the generator electrode with a diaphragm because of the sample’s low water content.
Phase separation can occur when using Procedure A as not all petroleum products are soluble in Karl Fischer reagent. If phase separation takes place, the reagents must be replaced.
The quantity which can be analyzed without phase separation is dependent on the volume and kind of sample, the volume of reagent and the solubility of the sample in the reagent.
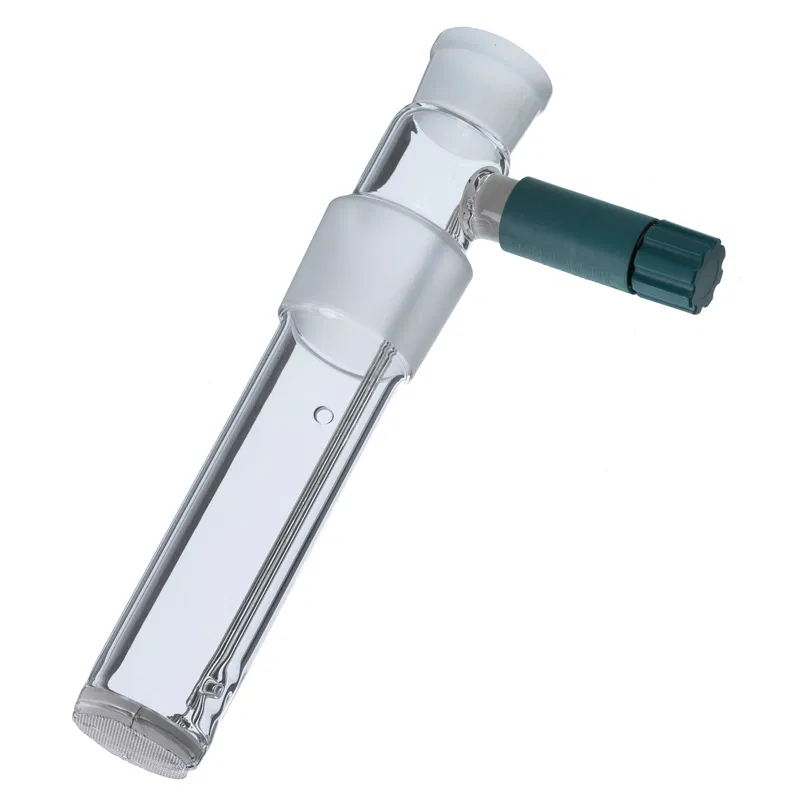
The generator electrode with diaphragm is recommended for water determination according to ASTM D6304 Procedure A. Image Credit: Metrohm AG
Procedure B: Water Extraction Using an Oven
For this procedure, an oven can be employed to analyze samples that do not dissolve easily in Karl Fischer reagent, viscous samples and samples where it is anticipated the components will interfere with the Karl Fischer reaction.
For the analysis, a typical sample is placed into a glass vial, which is then weighed and sealed immediately. The vial is then warmed in an oven to draw out any water. The vaporized water is transported into the Karl Fischer titration cell, which has been conditioned utilizing a dry carrier gas for titration.
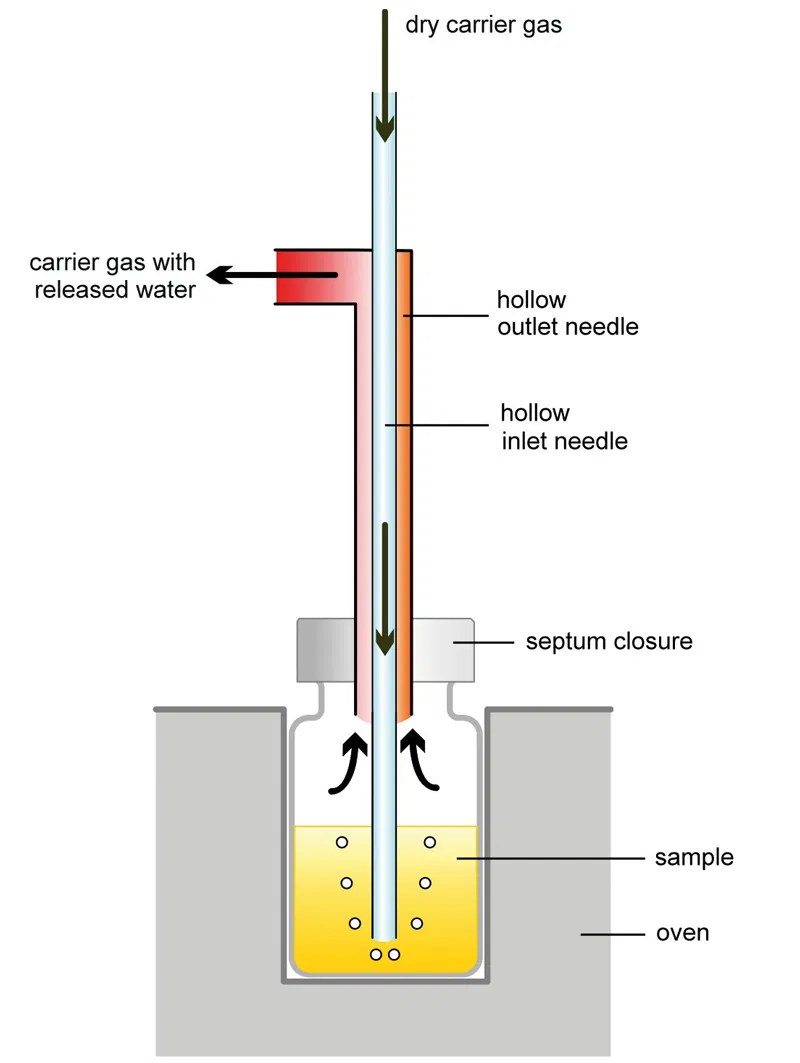
Schematic drawing of the Karl Fischer oven method. Image Credit: Metrohm AG
The optimal temperature used for the evaporation is dependent on the sample. The 874 Oven Sample Processor can conduct a temperature gradient test to establish the optimal temperature for extracting water without deterioration of the sample.
For further information regarding the oven method, its working principle and its benefits, check refer to the article: “Oven method for sample preparation in Karl Fischer titration.”
Water content determination in petrochemical products as per ASTM D6304
Video Credit: Metrohm AG
Water Extraction Using an Evaporator: Procedure C
Rather than using an oven, Procedure C demonstrates how a water evaporator can be employed for extracting the water of samples that do not easily dissolve in Karl Fischer reagent, viscous samples and samples with components where interference is expected with the Karl Fischer reaction.
During this process, an aliquot of sample is placed into a heated chamber incorporating a suitable solvent (most commonly, toluene). The heated chamber’s temperature is dependent on the solvent being used.
The water vaporizes together with the solvent in an azeotrope distillation. The azeotrope is then relayed, via a dry non-reactive carrier gas, into the conditioned Karl Fischer titration cell.
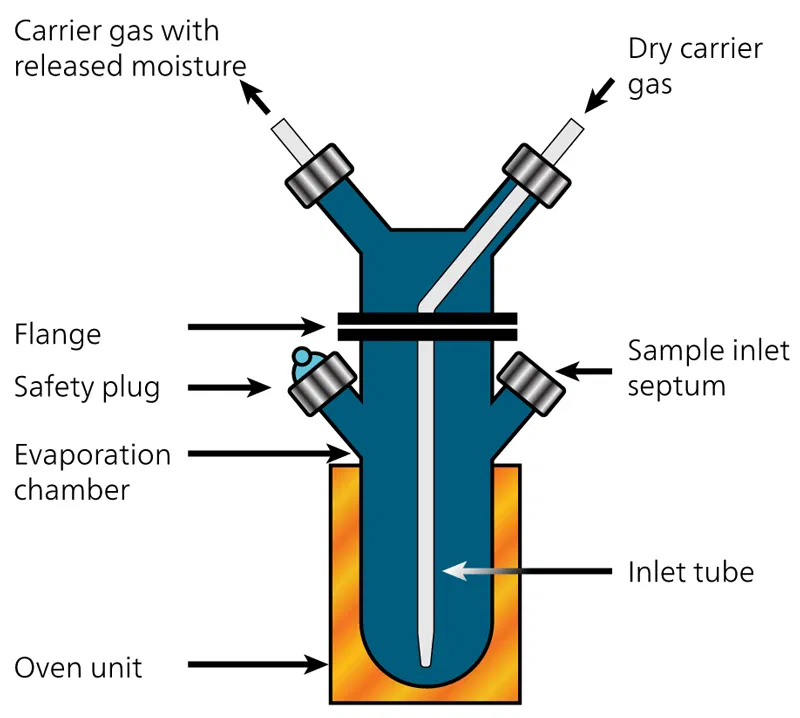
Schematic drawing of the evaporator method. Image Credit: Metrohm AG
When to Use Which Procedure
Procedure A is appropriate for liquid samples demonstrating a low viscosity, such as diesel fuel, jet fuel, or aromatics. Low viscosity is necessary in order to be able to easily add the sample into the Karl Fischer titration cell.
The samples demand excellent solubility in Karl Fischer reagent. Otherwise, phase separation will come to pass, which then necessitates replacing the Karl Fischer reagents.
While the exchange of the reagent can be automated, extra time is necessary for the reagents to reach dryness again. Even when samples are soluble in Karl Fischer reagents, there could still be obstacles with using Procedure A due to the sample matrix generating side reactions and consequently false results. In this case, Procedure B or C are the better options.
Procedure B is good for every type of sample, irrespective of their viscosity or matrix composition, as only the evaporated water is relayed into the titration cell. This leaves the sample, as well as interfering matrix components, caught the sealed vial, which can be easily disposed of post-analysis.
Thus, there is a great reduction in the reagent exchange frequency, which limits costs, as less reagent is needed. Depending on the lab’s workload, there is the real potential to fully automate the analysis, including exchange of the reagent using an automated Karl Fischer oven.
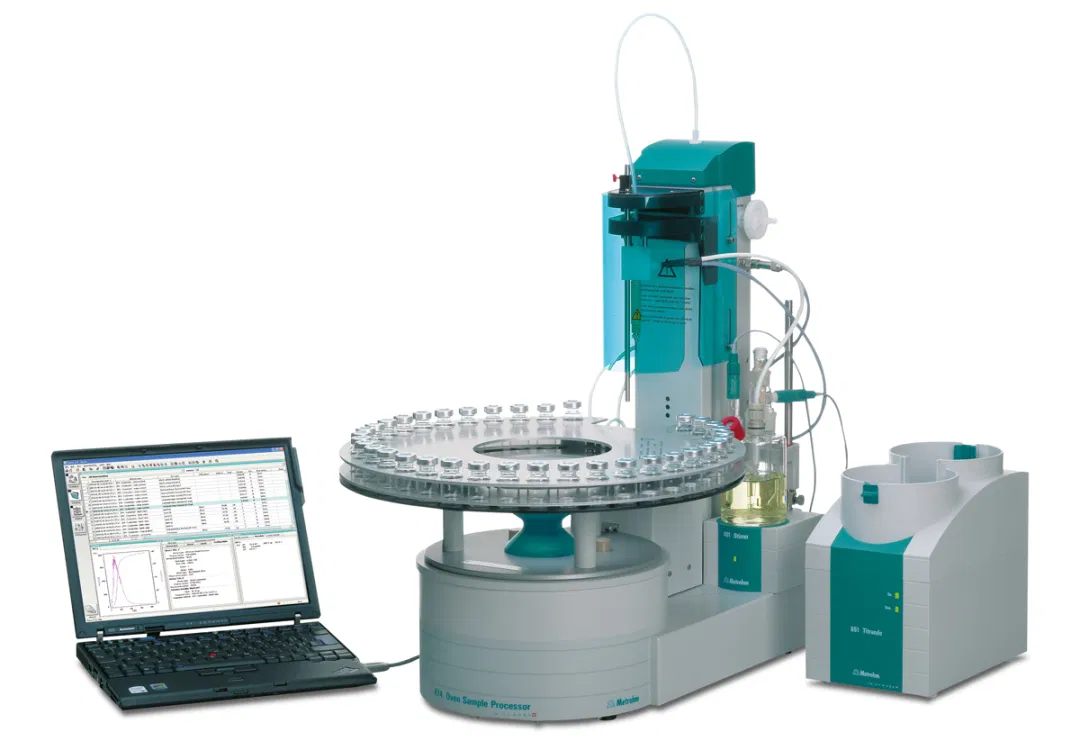
The 874 Karl Fischer Oven Processor with an 851 Titrando for a fully automated analysis according to ASTM D6304 Procedure B. Image Credit: Metrohm AG
Like Procedure B, Procedure C is appropriate for all kinds of samples. Regardless of their viscosity or matrix constitution, only the solvent and the evaporated water in an azeotrope are relayed into the titration cell.
The sample, as well as any matrix components that interfere, stay in the evaporation chamber. Yet, on occasion, it is still necessary to empty and refill the evaporation chamber manually, which can be painstaking, as the chamber must cool down prior to the exchange of content can take place.
In addition, complete automation is not possible with this method.
For a comprehensive detailing of the different factors for each procedure, download Metrohm’s free White Paper: “Moisture in petroleum products according to ASTM D6304.”
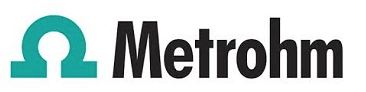
This information has been sourced, reviewed and adapted from materials provided by Metrohm AG.
For more information on this source, please visit Metrohm AG.