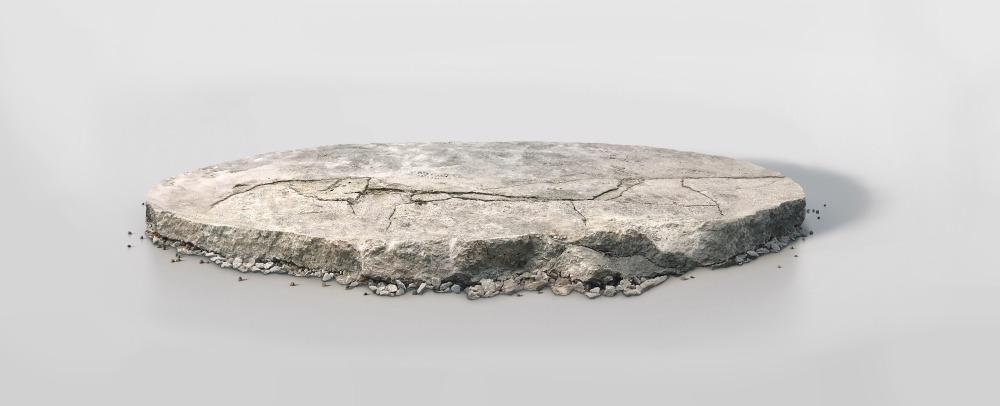
Image Credit: Red Tiger/Shutterstock.com
Irregularities on a surface determine how rough it is. Surface roughness can be evaluated by visual appearances and tactile sensation and can be measured using a numerical scale. A surface condition is often described based on its smoothness, shine, as well as matte and textured, or mirror-finish. These differences in appearance and tactile feel are due to the irregularities present on the surface of an object. Several mechanical and optical methods are used to measure the geometrical parameters of a surface.
Surface irregularities on objects or materials are either generated intentionally or are created by numerous factors such as the vibration of cutting tools and the physical properties of the material.
The functionality of various objects depends on surface texture which comes in diverse shapes and sizes. Surface irregularities may also occur as a result of the overlap in several layers. The concavities and convexities affect the quality and functionality of the object's surface. It also affects the performance of the resulting product, which includes friction, operating noise, durability, and energy consumption. Quantification of surface coarseness is associated with measuring them by their height, depth, and interval. This data is further analyzed by a standard method and calculated as per industrial quantities standards.
Recent Developments in Measuring Surface Roughness
In 1933, Abbott and Firestone first developed a profilometer technique to measure surface roughness. However, in 1939, Rank Taylor Hobson created a commercial instrument called Talysurf to measure surface irregularities.
The precision with which roughness is measured has increased immensely. Modern software computes around 300 parameters of roughness profile and includes various topography parameters. Irregularities of any surface can be measured up to 200 mm length and 100 mm width with the deviation of guide being equal to fractions of micrometers.
Physicists and engineers often require minute-scale, i.e., molecular roughness, details to analyze surface irregularities. These studies involve techniques such as low-energy electron diffraction, molecular-beam methods, field-emission, field-ion microscopy, scanning tunneling microscopy, and atomic force microscopy. Few measurement techniques are used to analyze geometric parameters of surfaces. The measurement techniques are broadly divided into two groups, namely, contact and non-contact type. These are discussed below:
Contact type
This type of surface measurement involves the actual contact with the equipment parts on the surface of the object to be measured. Currently, contact-type stylus instruments, using electronic amplification, are the most popularly used pieces of equipment.
Non-contact type
A contact-type instrument may damage surfaces when used with a sharp stylus tip, particularly soft surfaces, which enhances the importance of non-contact-type techniques. A non-contact optical profiler was first developed in 1983, based on the principle of two-beam optical interferometry. Currently, it is widely used in industries related to electronics and optics to measure smooth surfaces.
Different techniques are used, based on the physical principle, to assess the nanoscale, atomic scale, and microscale features of surface roughness. For example, some of the methods used are mechanical stylus, electrical, scanning probe microscopy (SPM), optical, fluid, and electron microscopy methods. Some of these techniques are briefly discussed as follows:
Geometric analysis
This method offers a qualitative assessment based on visual evaluation and subjective analysis of a material’s surface. This technique is subjective to the skill and experience of the professional involved. The main limitation of this method is the lack of a standardized method for evaluation.
Scanning probe microscopy methods
Techniques that include instruments based on scanning tunneling microscopy and atomic force microscopy are known as scanning probe microscopies (SPM).
Atomic force microscopy acts as a nano-profiler that can function at ultra-low sample size. This technique measures surface roughness with lateral resolution ranging from microscopic to atomic scales. This technique is mostly used for scaling roughness with an extremely high lateral resolution, in particular, nanoscale roughness.
SPM is the first instrument that can directly obtain three-dimensional images of solid surfaces with atomic resolution.
Fluid methods
This method is commonly used for continuous inspection required for quality control. This is a non-contact technique that provides numerical data that can be correlated empirically with the roughness. This is an extremely rapid method.
Electrical method
This technique utilizes the capacitance method which is based on the parallel capacitor principle.
The capacitance between two conducting objects is directly proportional to their area and the dielectric constant of the medium between them, and inversely proportional to the distance separating them. The capacitance method is commonly used for continuous inspection procedures that involve quality control.
Optical method
Optical interferometry is an invaluable technique used for measuring surface roughness at the macroscopic and microscopic scale. A recent optical technique offers measurement of the roughness of moving surfaces. The new technique which is known as the dark/bright ratio (DBR) method uses the collective effect of scattering and speckle phenomena.
In this method, the irregularities of a surface are determined from the difference in dimensions of the recorded dark and bright regions in the speckle pattern. This method is extremely useful for in-process measurement owing to its simplistic approach, both in terms of principle and optical equipment. It also offers a large measuring range with high accuracy.
Electron microscopy methods
This technique can reveal both macroscopic and microscopic surface features. The scanning electron microscope and stereomicroscope are used to profile a surface. The backscattered electron image is obtained via a scanning electron microscope and can provide three-dimensional measurements of roughness after several scans.
References and Further Reading
Tonietto, L., Gonzaga, L., Veronez, M.R. et al. (2019) New Method for Evaluating Surface Roughness Parameters Acquired by Laser Scanning. Scientific Report, 9, 15038. https://doi.org/10.1038/s41598-019-51545-7
Ali, H.R.S. (2012) Advanced Nanomeasuring Techniques for Surface Characterization. International Scholarly Research Network. Volume 2012, Article ID 859353, https://doi.org/10.5402/2012/859353
Wang, W. et al. (1998) A new optical technique for roughness measurement on moving surface. Tribology International. 31 (5), pp. 281-287, https://doi.org/10.1016/S0301-679X(98)00034-6
Butler, D. (2008) Surface Roughness Measurement. In: Li D. (eds) Encyclopedia of Microfluidics and Nanofluidics. Springer, Boston, MA. https://doi.org/10.1007/978-0-387-48998-8_1506
Disclaimer: The views expressed here are those of the author expressed in their private capacity and do not necessarily represent the views of AZoM.com Limited T/A AZoNetwork the owner and operator of this website. This disclaimer forms part of the Terms and conditions of use of this website.