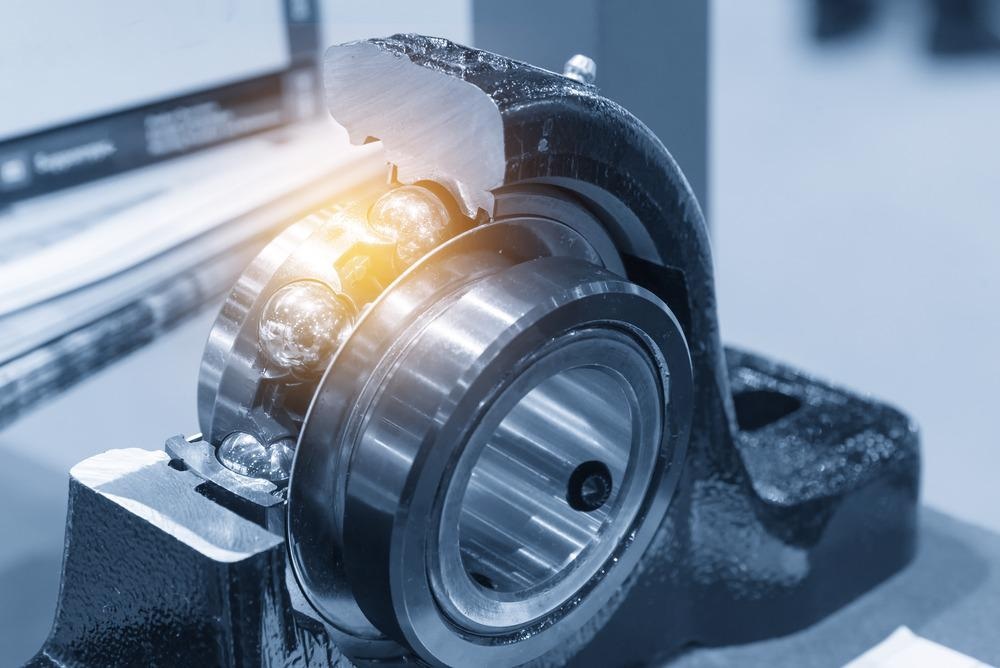
Image Credit: Pixel B/Shutterstock.com
Irregularities present on a surface are often described as surface roughness or texture. These surface textures such as grooves and dimples impart friction, which is the force between two sliding objects. Therefore, there is a relationship between surface roughness and friction. Researchers have recently found that the introduction of surface texture to an object can improve the tribological properties of its mechanical components.
Tribology is an interdisciplinary study that deals with the interaction of surfaces in relative motion. Tribological properties include friction, wear, and lubrication. A recent study has reported that surface texture with specific dimensions and patterns can effectively reduce friction. This property could be immensely beneficial in various sectors that use internal combustion engines and mechanical seals.
In several previous studies, while studying surface friction, surface roughness was neglected, and a smooth surface was assumed. It was much later that the importance of surface roughness in friction was realized.
Researchers conducted several experiments using textured polydimethylsiloxane (PDMS) disks which possessed varied roughness contours on its surface. In one such experiment, the PDMS disks were examined under a stationary GCr15 bearing steel ball using glycerol and deionized water lubricants. In this study, the best frictional property was attained at a particular or optimal surface roughness pattern using a mixed lubrication system. Another related study indicated that textured surfaces with traverse surface roughness exhibited superior frictional performance.
Relationship between Friction and Surface Roughness
A prior study proved that surface texture and surface roughness affect frictional behavior during sliding. This study was conducted using steel discs of varying roughness and texture. A similar result was also obtained in another study that had prepared steel specimens with different degrees of roughness by lapping, grinding, and polishing.
Scientists have also reported that the roughness parameter, i.e., specific patterns on an object’s surface, plays a crucial role in assessing friction. These parameters are used to quantify the surface roughness and texture.
A substantial amount of research had been conducted to determine the influence of various roughness parameters on the coefficient of friction. Previously, the conventional surface roughness parameters such as Ra, skewness, kurtosis, and peak density were thought to determine the friction between sliding objects. However, later researchers concluded that these are not the sole governing factors as they do not provide an apt functional characterization of the surface in terms of friction generation. They came up with a new surface roughness parameter called bearing length product which showed a functional relationship with the friction coefficient.
Scientists studied the frictional response of four precisely conditioned finished surfaces (e.g., ground, hard turned, honed, and isotropic) using three-dimensional (3D) surface topographic analysis. The study revealed that the amplitude parameter, Sq (r.m.s. deviation of surface), spatial parameters, Sds (density of summits), and Std (texture direction) have a significant role in determining the frictional behavior of surfaces.
Numerical Study to Understand Frictional Characteristics of Surfaces
Numerical simulations, namely, the Navier–Stokes’s equations, could help study the frictional characteristics of micro-textures present on stainless steel surfaces. The simulation revealed that during hydrodynamically lubricated sliding, textured surfaces demonstrate 80% lower friction than untextured surfaces.
In another study, a step-wise numerical simulation was carried out to study the wearing of a cylindrical steel roller oscillating against a steel plate. This research used the special version of the finite element program NIKE2D. NIKE2D is an implicit, fully vectorized finite element code that is used to analyze the response of two-dimensional (2D) axisymmetric plane stress solids.
In this simulation, the pressure and sliding distance were recalculated with the change in the surface geometry. The result showed that an increase in time and speed had a significant impact on the wearing of the steel. Using numerical simulations, scientists have also increased the importance of dimple size and radius of the cylinder in determining the hydrodynamic effect. Various software such as Computational Fluid Dynamics (CFD) software, which is based on a physical model, has been developed to conduct the numerical simulation.
Physical Model to Understand Frictional Characteristics of Surfaces
The friction pairs can be described as two infinite parallel solid walls generating a film pressure when hydrodynamic lubrication is relatively low. Typically, the upper wall is static and smooth while the lower wall consisting of micro-dimples moves along the direction with a relative velocity. To calculate friction, a geometric model of the textured surface with roughness is developed. This considers the length of the solid wall, the depths and radius of the dimples, and the lubricating film thickness.
Importance of Friction Coefficient
It is important to understand the friction coefficient and friction force as they help to determine the exact dimensions and size of dimples to reduce the friction. Scientists have revealed that one of the most significant factors that influence the coefficient of friction during sliding is surface roughness.
Several numerical simulations are used to calculate the friction coefficient. For example, Reynolds’s equation is used to study the effect of different irregular patterns and shapes on hydrodynamic lubrication. Researchers have studied the role of surface roughness on piston rings and cylinder liners. They reported that surface roughness plays a critical role in the tribological properties. They further stated that the measure of friction reduction varied under different surface roughness with the same texture.
The Effect of Surface Roughness on Nanofriction
An extensive amount of research focuses on the understanding of the effect of surface roughness on nanofriction. Prior studies have shown that frictional force, between two laser-fabricated surfaces of nanoscale dimension with periodic grooves, is dependent on texture orientation. Nanowires are used as moving components in nanodevices. Therefore, to develop nanowire-based nanodevices, it is extremely important to foresee the friction between nanowires and the supporting substrate. The nanoscale friction is generally analyzed by the frictional force per unit contact area or frictional shear stress. Atomic force microscopy is typically used to study the friction between nanowires and the substrate.
Reference and Further Reading
Xie, H., Mead, J., Wang, S. et al. (2017). The effect of surface texture on the kinetic friction of a nanowire on a substrate. Scientific Report, 7, 44907. https://doi.org/10.1038/srep44907
Zhou, Y. et al. (2015). Influence of surface roughness on the friction property of textured surface. Advances in Mechanical Engineering, 7(2). https://doi.org/10.1177%2F1687814014568500
Menezes, P. et al. (2008). Influence of roughness parameters on coefficient of friction under lubricated conditions. Sadhana, 33(3), pp. 181–190.
Disclaimer: The views expressed here are those of the author expressed in their private capacity and do not necessarily represent the views of AZoM.com Limited T/A AZoNetwork the owner and operator of this website. This disclaimer forms part of the Terms and conditions of use of this website.