A refinery in continental Europe is operated by a major oil company. This refinery includes a total of three amine trains: one in the gas plant, one in the HDS unit and one in the FCC unit.
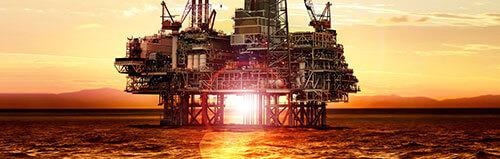
The initial plant design led to the amine unit in the FCCU only being fitted with a coarse filter on the lean side.
This amine unit had been facing ongoing foaming issues, and the refinery determined that these issues were being caused by a combination of liquid hydrocarbon ingress with sour fuel gas and the formation of fine particles of corrosion products present in the amine loop.
The refinery’s problems with foaming were leading to subsequent issues with the H2S spec in the treated gas, as well as the carry-over of heavier hydrocarbons alongside the fuel gas.
Because of this, the refinery in question was forced to restrict its amine unit capacity by 12.5%, from 40 tons per hour to 35 tons per hour. This reduction led to a reduction in fuel gas production, restricting FCCU output and resulting in considerable financial risk to the refinery.
A range of different filter technologies had been trialed unsuccessfully by the refinery; for example, self-cleaning, bags and pre-coat.
Working with Pall, a clean-up or ‘depollution’ of the amine solution was performed with a view to addressing the foaming issues by eradicating the solid and hydrocarbon contamination that was circulating in the amine.
A mobile unit was connected to the rich amine loop. This mobile unit included a liquid/liquid coalescer for the elimination of free and emulsified liquid hydrocarbons, a particulate filter for the elimination of solid particles and a carbon bed for the elimination of dissolved hydrocarbons.
Progress of the depollution was monitored, while the refinery’s laboratory was able to track the cleanliness of the amine solution using foam tests. The collapse time of the actual amine solution was 60 seconds, while the projected benchmark foam collapse time was 7 seconds for the new amine solution.
Foam collapse time was reduced to 20 seconds following the initial 24 hours of depollution, and after 72 hours, this had been reduced to 9 seconds. The use of a much cleaner amine solution allowed the refinery to return to operating this train at its designed capacity of 40 tons per hour.
The depollution also confirmed that the carbon bed placed downstream of the coalescer provided no additional improvement to the amine solution’s foaming. This illustrated that solid and hydrocarbon contaminants had been successfully removed using the particulate filter and the coalescer.
The refinery opted to install a particulate filter in the rich amine a few months later, ensuring that low levels of solid contamination could be maintained at all times. Pall provided the refinery with an Ultipleat® High Flow filter, complete with 10 micron absolute-rated filter cartridges.
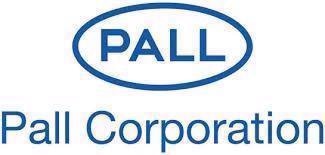
This information has been sourced, reviewed and adapted from materials provided by Pall Corporation.
For more information on this source, please visit Pall Corporation.