Beamline diagnostics are an essential part of any particle accelerator, used to measure and monitor the properties of the particle beam itself. Within these diagnostic systems, precise linear motion controllers enable sensors and measuring devices to be precisely positioned in or around the beam.
This article takes an in-depth look at the crucial role that high-performance linear motion controllers play in beamline diagnostics.
A ‘beamline’ in particle physics is the path along which a beam of particles or light passes. The term also encompasses the surrounding hardware, including guide tubes and diagnostic devices. The beam itself generally passes along the ultra-high vacuum interior of a metal tube known as the beam pipe.
Ensuring the beam pipe stays at ultra-high vacuum (UHV) pressure levels is critical to its functionality: by removing gas molecules from the beam pipe, the probability of unwanted collisions between these gas molecules and the beam is minimized.
The requirement for hard vacuum conditions means that beamlines are some of the most sophisticated vacuum systems in the world.1
All beamlines require beamline diagnostics: instrumentation which monitors the parameters beam itself, enabling beam properties to be corrected for specific applications.2
Beamline diagnostic equipment is essential to the everyday function of all particle accelerators: In fact, diagnostics hardware (including actuators, sensors and linear motion controllers) is estimated to account for 3% - 10% of the total cost of an accelerator facility.
Actuators and Linear Motion Controllers in Beamline Applications
Precision sensors (such as monitors for beam position, current or wavelength) deployed in beamline diagnostics must be very precisely positioned within the beamline.
This positioning is carried out by linear actuators, which are in turn controlled by linear motion controllers.
In beamline applications, the quality of the linear motion controllers used is just as important as the quality of the linear actuators themselves.
Linear motion controllers run the gamut from relatively simple handheld devices to software-controlled units. Handheld linear motion controllers are usually directly connected to motors, allowing the user to control both the speed and direction of a linear actuator.
Computerized linear motion controllers, on the other hand, enable more precise control via a software interface. Computerized linear motion controllers are perfect for industrial and scientific applications where system integration and high levels of precision are required.
The Multi-Axis Stepper Controller (MASC) from UHV Design provides single- or multiple-axis control of stepper motorized devices (such as linear actuators) for beamline diagnostic applications.
Featuring both analog and digital inputs, the MASC can be controlled either by integrated software, third party software (such as Applied Motion Q and Si programmer) or a touchscreen jog box.
UHV Design provides a range of other ultra-high vacuum grade components, including linear motion controllers and actuators for beamline diagnostics. To find out more about the range of linear motion controllers and other products from UHV Design, get in touch with them via their website today.
References
- A vacuum as empty as interstellar space | CERN.
- Forck, P. Lecture Notes on Beam Instrumentation and Diagnostics. 147.
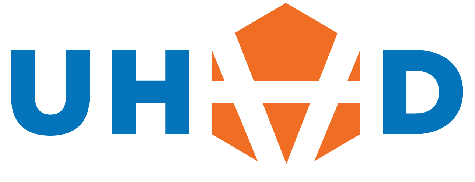
This information has been sourced, reviewed and adapted from materials provided by UHV DESIGN LTD.
For more information on this source, please visit UHV DESIGN LTD.