This article explores the fundamentals of pressure measurement, looking at different types of pressure measurement, available technologies, units of measurement, accuracy and common operational issues. It then moves on to outline the components that make up pressure transmitters before looking at a range of different applications.
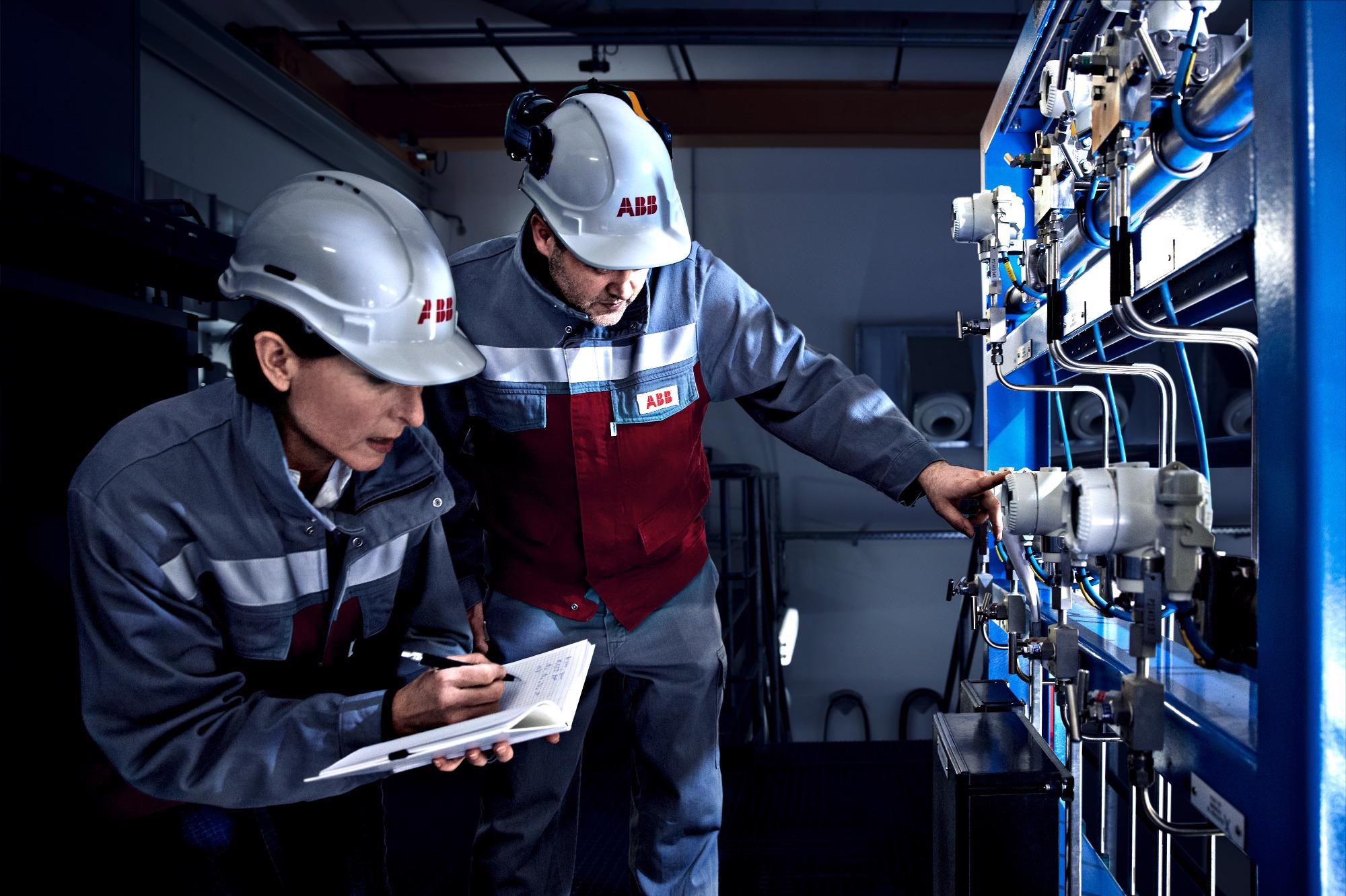
Image Credit: ABB
Types of Pressure Measurement Transmitter
There are essentially four different types of pressure measurement transmitters. Absolute pressure transmitters measure against a vacuum, meaning that if no pressure is applied, the reading would return a value for atmospheric pressure. This is what a barometer would measure, for example.
A gauge pressure instrument measures pressure against atmospheric pressure. For example, a common tire gauge could measure 32 psi of pressure, but measuring that same tire pressure with an absolute pressure transmitter would also include an additional 14.5 psi.
Differential pressure measurements involve determining the difference between two different pressures. Finally, multi-variable pressure measurements involve measuring the difference between static pressure and comparing this with a process temperature.
As well as these different types of transmitters, a range of other technologies exist. These include piezoelectric crystals that convert pressure into an electrical signal that can be measured.
Inductive type pressure sensors are generally better for use in harsh environments or applications prone to shock vibration. Strain gauge instruments are usually used for high pressure applications. ABB works with all of these different pressure transmitters.
Units of Measurement
Units of measurement may vary depending on the application in question, the country the user is operating within or whether they are specifically looking at high pressures, low pressures or a mix of both ranges. For example, 1500 psi is equal to 100 bar.
Depending on the model, most ABB pressure transmitters have direct application software loaded onto them, making determining pressure levels relatively straightforward.
The accuracy of the pressure transmitter can be affected by a number of factors, for example, temperature effects, the compressibility of the gas or the liquid being measured. The most significant factor affecting performance, however, is how the transducer is constructed.
The transducer is arguably the most essential part of the transmitter. The quality of the electronics used and the way that the manufacturer calibrates and characterizes the electronics within the transducer sensor can have a major impact on its overall performance.
Accuracy is listed in datasheets as a percentage of the calibrated span or occasionally as a percentage of the value that is read.
ABB produces the multi-variable 266JST pressure transmitter, which offers a percentage of span of 0.04% plus or minus 0.04% of the value. This is up to a 20 to 1 turn down, meaning that a 1000 inch transmitter turned down to perform smaller readings would still benefit from high levels of accuracy. Turn down range can affect accuracy.
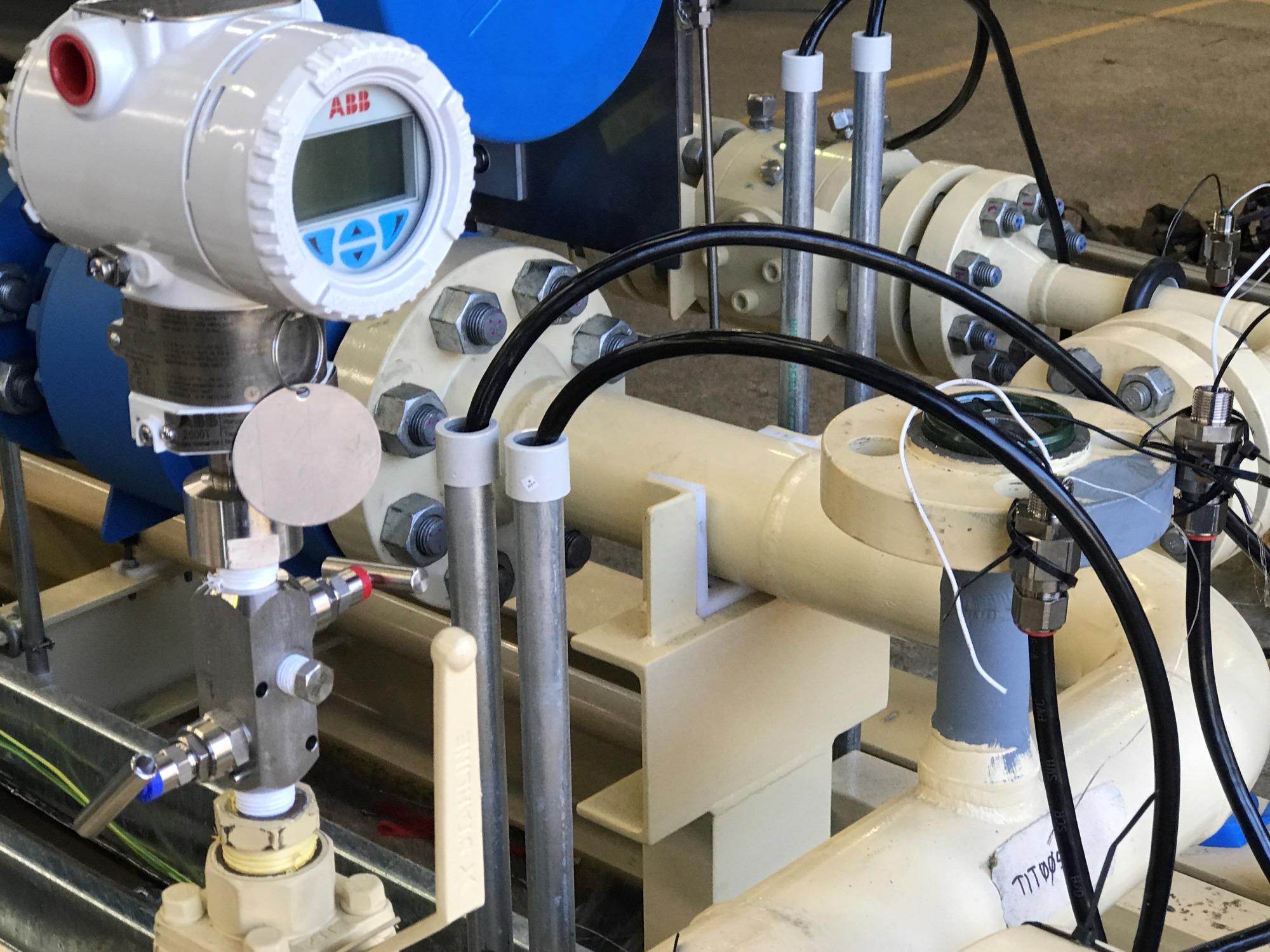
Image Credit: ABB.com
Pressure Transmitter Components
Pressure transmitter components typically include process connections that link the transmitter to the wider industry application process, transducers that regulate available signals and user interfaces.
Process connections in a simple pressure transmitter are often comprised of threaded types such as an NPT thread or direct mount connected to a type of manifold, such as a tank that has flange connections.
Where a process involves working with debris that users do not want to enter the bore diameter of the pressure transmitter, users may opt to use a flush mount.
Different bore sizes are available, and applications working with very high pressure may require the use of bores comprised of various thicknesses of metals, different machining or a protective chemical application.
The application may require the use of anti-abrasion coatings (for example, in pulp and paper applications) or hygienic connections (for example, in food, beverage or pharmaceutical applications). These are all different types of process connections.
Non-standard applications may necessitate the use of a remote seal, whereby the pressure reading is taken through a remote seal that is inserted into the application along with a capillary tube that runs to the actual transducer.
In ABB’s pressure transmitters, there are no gaskets or threads at all in the sensor capillary diaphragm seal as standard. The seal is welded all the way through and tested throughout all those welded connections, meaning there is no chance of any type of leak.
This all-welded technology is globally recognized as delivering performance and stability over time.
Remote seals are ideal for applications working with extreme temperatures. While a standard seal can withstand temperatures of -40°F to 250°F, some types of remote can withstand temperatures of 350°F up to 750°F.
There are many different types of remote seal coatings and metals that can be used if an application is working with a corrosive hazardous, solid-laden or dirty or viscous fluid.
Fluids with a tendency to crystallize may cause vibration, but this can be overcome with a remote seal. Users may also be working with food or beverages where they are required to meet FDA requirements. ABB provides a range of fill fluids, inert fill and oxygen services for these more specialized applications.
The transducer is the heart of the transmitter. Transmitters are designed to work with a wide range of pressure types, and these should be outlined on a specification sheet. The most common of these are process pressure, though an overpressure value may also be provided.
When in the overpressure range, no reading will be returned, but there will be no damage to the sensor, and this will be operational as normal when the pressure lowers. Burst pressure is also worth considering for safety purposes because it is important to make sure that nothing breaks and no leaking occurs during the process.
Transmitters can be manufactured from stainless steel, hastelloy, monel, or inconel, while fill fluid options include silicone, galden and halocarbons.
Connectivity Considerations
When selecting a pressure transmitter, it is also important to consider what kind of communication options are available for relaying the electrical signal, for example, into an RTU or skater system, analog inputs, or digital communications.
Common communication options include HART and 4-20 mA, with ABB offering standard and advanced options for these. When working with a simpler application, standard options offer an easy and quick setup, while advanced options allow users to develop more custom solutions to their application by configuring a range of options.
It is also possible to enhance existing systems or older applications with pressure transmitters, perhaps in order to meet a certification requirement or to replace a component with a more efficient alternative.
ABB pressure transmitters provide very clear graphical instructions on what wiring is needed for installation. Another analog signal option is the 1-5 volt low power signal, while remote applications running on batteries or solar panels may benefit from a wireless version that uses a gateway.
Upgrading existing systems to use wireless technology is recommended in many cases because it means there is no need to remove or uncover old wiring or trenching.
All of these communication options have the option of using the HART technology and are compatible with existing interfaces like Profilbus and Foundation Fieldbus.
The User Interface
The ABB user interface is common across all the company’s 266 pressure-related products, as well as many of ABB’s other products.
The user interface is based on a standard four button screen, which is intuitive and available in a range of languages. The system is easy to use, even for novice users with no prior experience of ABB’s systems.
Setup is straightforward via an easy setup menu, which takes the user through the basic setup process in a streamlined manner. Additional menus are available, allowing the user to configure more advanced options as required.
The setup menu allows the user to set level limits, alarm options, calibration, overpressure options or access diagnostics that the user can drill down into.
ABB aims to offer as much ‘through the glass’ technology as possible, meaning that, for example, in an environment where the user does not want to open up the pressure transmitter, they do not need to. This is especially useful in working conditions that may involve a hot work permit or in an explosive environment.
Many users working in the field are already familiar with HART communications and different options for connecting a pressure transmitter or other field devices. ABB offers the Field Information Manager (FIM), a free to download software package that offers the DTMS for different products.
FIM uses a Windows-menu driven interface that is easy to navigate, is compatible with many different applications and continues to be developed.
Typical Applications
Pressure transmitters are used in a wide range of applications across a number of industries; for example, oil and gas, chemical, power, pulp and paper, water and wastewater, food and beverage and even marine applications.
The selection of pressure transmitters is largely dependent on the application in question and the sector. One of the primary reasons for using pressure transmitters is safety, ensuring that processes are effectively controlled and that risks such as explosions are minimized.
While pressure transmitters and their applications are highly variable, one commonality across all these areas is the use of valve controls. Pressure signals are passed to a unit which then performs a control action based on that signal; for example, opening or closing a valve.
One real-world example of this process sees a multi-variable transmitter used to collect precise data on expensive chemicals or expensive hydrocarbons, which are used for royalty exchange. This system uses high accuracy measurements, which are passed to an RTU before providing users with the right information.
A multi-variable pressure transmitter used in a hydrocarbon pipeline application uses an orifice plate, measuring the pressure on each side of the orifice plate and providing information on differential pressure as well as temperature.
As oil wells grow older, there may be a need to use a plunger to perform injections. ABB’s solutions allow users to perform measurements inside the casing, determining tubing pressure and line pressure, controlling the plunger and applying more pressure as required.
Safety systems are a primary concern in the chemical industry, with an array of alarms and shut down systems all working with pressure transmitters. Other key areas using pressure transmitters include controlling and monitoring applications, cooling towers and steam and natural gas storage, ethane production and ammonia production.
In the power industry, pressure transmitters are often used in the measurement of flue or burner gas, management of condensation pressure levels or combustion chambers and pulverized coal processing; all of these processes can benefit from high performance measurement.
Boilers require measurement of water feed and steam pressures, while turbines will require measurement of drafts. ABB’s instrumentation can accommodate the very low pressure ranges required to control differential pressure in these types of applications. This allows users to effectively adjust or cut off the flow where required.
The pulp and paper industry requires level measurements to be taken in terms of the pulp and paper itself, whether this is in terms of decomposition, levels in vats being used, levels of water tanks, or levels of the range of auxiliary products that are used in pulp and paper production.
Pressure measurement is performed on the disc filter, with differential pressure measurement performed on the drying cylinders.
The food and beverage industry often works with products that need to be FDA approved. Pressure measurement is used in a range of different processes such as heating, cooling and managing fill levels.
Sanitary connections are common in this industry, as are 3-A metal surfaces. Robust vacuum performance via ABB’s all-welded seals has proven essential in the food and beverage industry, where it is often essential that processes take place in sterile environments.
Pressure Transmitters from ABB
ABB operates factories in Bangalore, India; Shanghai, China; Ossuccio, Italy; Bartlesville; Oklahoma; and Warminster. The company ships between 150,000 and 200,000 pressure transmitters annually.
ABB offers a number of different product lines, offering users a lot of choices, model numbers, levels of certification and pressure ranges that can accommodate almost any application requirements.
ABB continues to develop and add products all the time; for example, a new product was released late in 2018, which is a mass measurement type of multi-variable, pressure transmitter able to communicates Modbus ideal for level measurement.
Customers are advised to speak to a local representative for advice or to discuss their needs. ABB will investigate the application in question, ascertain the customer’s needs and recommend a range of options that will be ideal for the application in question, regardless of the industry or size of the project.
Overall, ABB’s solutions are cost-effective, field-ready, certified and easy to use. The company provides quality, high end products at a competitive price, as well as a supportive team happy to take on any challenge.
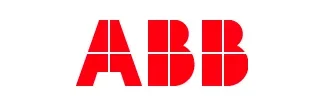
This information has been sourced, reviewed and adapted from materials provided by ABB Measurement & Analytics - Analytical Measurement Products.
For more information on this source, please visit ABB Measurement & Analytics - Analytical Measurement Products.