This article aims to break down a range of preconceptions about digitalization within the water industry. Within the water industry, there is a misconception that digitalization is complicated and expensive to implement within water systems.
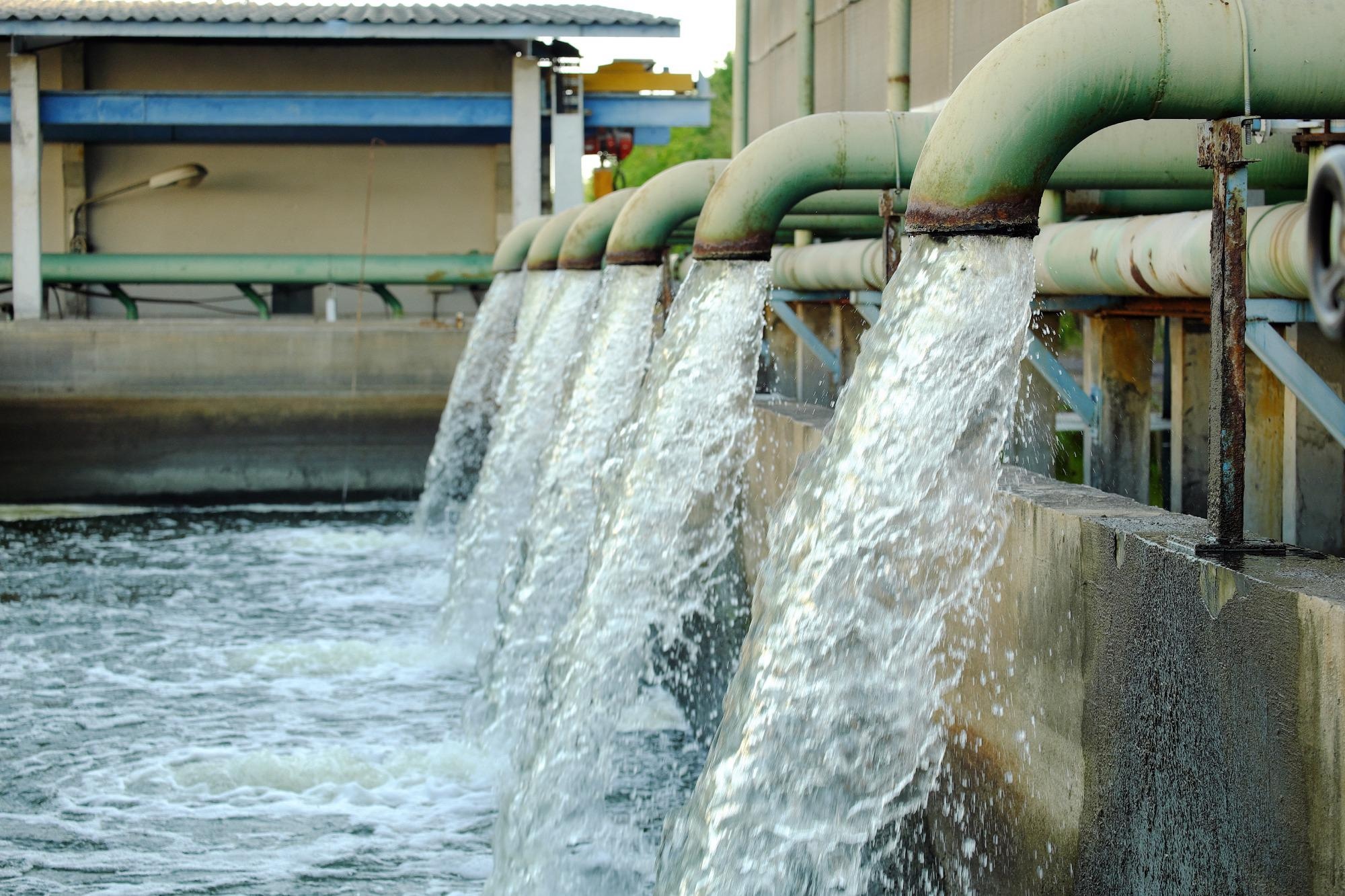
However, much of this technology is accessible, affordable and much easier to implement in existing systems than many users assume.
The majority of water companies’ needs can be grouped into one or more of these central categories.
- Efficiency is generally associated with utilities within the developed world that have well-established water networks. Water companies looking to improve efficiency are constantly investigating ways to do more with less.
- Environmental factors are important within the developed world and the developing world. Whether these factors are driven by regulation or a desire to address the impact of climate change, water companies must take this into account almost continuously.
- Expansion is primarily a driver in the developing world, as urbanization adds increasing pressure to already stretched utilities on a daily basis.
When considering the impact of digitalization in the water industry, goals, requirements and benefits will generally fall into one or more of these three categories.
Global Impacts of Digitalization
Digitalization has impacted the lives of people all over the world in a relatively short period of time. The advent and omnipresence of the mobile phone is a key example of this change. In 2005, hardly anyone used mobile phones, for example, and these were certainly not a central tool in many people’s lives.
By 2013 this had changed dramatically, with almost everyone owning a smartphone or even a tablet. A key factor in this change was the launch of the iPhone in 2007.
While touchscreens had existed since the 1970s and computers have had App Stores since the 1990s, the iPhone launched its App Store in 2008, combining all of that functionality into a single device.
This fundamentally altered the way that human beings interact with the world and this all took place within a relatively short period of time – an eight year period.
This rapid adoption of digitization has impacted the world of instrumentation - particularly the world of smart instrumentation - prompting a rapid evolution of the Human-Machine Interface (HMI).
Until recently, a lot of instrumentation was visual, with mechanical gauges still being used fairly extensively. The LCD display followed, meaning that users could view information to a higher level of granularity in the field.
Then, over the past five years, mobile telecommunication technology has begun to interact much more with instrumentation.
For example, flow meters can now be interrogated using a smartphone via near-field communication - effectively the same technology used when individuals pay for something wirelessly. QR codes can now be used to interrogate instruments in the field and extract diagnostic information from them with ease.
The future holds a great deal of potential in terms of HMI applications, with features such as voice control potentially being the next step in terms of the development of digital instrumentation.
The fundamental difference in all these HMI technologies is that the accuracy of instruments has remained largely the same. Digitalization has changed the way that workers interact with instruments, and because this has made measurement much easier, it has had a tangible impact on efficiency and accuracy in the field.
Industries such as ICT, media, finance and insurance lead the way in terms of digital maturity. As news and banking have moved to be largely online and digital, for example, these industries have been at the forefront of the digital revolution.
The water industry is comparatively behind other industries in terms of digitalization, despite its huge potential for improvement.
The Impact of Digitalization on the Water Industry
The consumer technology revolution has made computing, analytics, communication and storage technology available at a dramatically lower cost. This means that technology which was previously inaccessible to a range of industries is now much more affordable and available. As an industry, water is very much primed for rapid digitalization.
Improved connectivity is leading this potential for digitalization. Data is not useful if this is locked away in an instrument and users cannot easily access it. Unavailable data means it is not possible to derive insight from it or make any rapid changes to processes that may be required.
Smarter instrumentation has allowed easier connectivity onsite, and it is now possible to use smartphones and tablets to communicate with an instrument. Remote communication is also possible via wireless or Ethernet, meaning that retrieving data from an instrument is now considerably easier, even from some distance away.
Improved access to data alone is of limited use, however, because one of the other main challenges that water companies face globally is the issue of deskilling. Deskilling is a considerable barrier to water companies being able to deal with day-to-day challenges.
Newer technicians entering the water industry are trained fundamentally differently than many existing staff. They absorb information differently, but they are much more adept at using IT as they gather information in a very different way.
These newer technicians may not retain as much information as a traditionally trained technician with many years of experience. Digitalization enables instrumentation manufacturers to take some of that experiential skill and build it into devices.
Examples include a widely available QR code scanning function whereby if there is an instrument at fault on a site, workers can simply scan the QR code into a mobile phone to access a huge amount of diagnostic information about what may be happening, and instantly send this by email or instant message to a service technician working for the manufacturer who may even be based in a different time zone in a different country.
This allows communication around error reporting to be far more proactive, also removing any guesswork out of the fault-finding process. Another new development in digitalization is augmented reality. This technology offers an efficient means of training new operators.
Water companies in the vast majority of the world are working with limited resources and finances, meaning these companies are generally focused on doing more with less. Any solution that helps increase efficiencies and reduce downtime is therefore essential.
Apps on phones that enable e-manuals to be downloaded immediately rather than technicians having to carry around large documents or refer to video tutorials that guide them through commissioning processes will make a practical difference in terms of an instrument’s day-to-day use.
At a more advanced level, processes like institute verification devices take the guesswork out of the maintenance process by enabling users to address a problem before it becomes a serious issue, therefore reducing downtime. These are all practical ways in which digitalization makes a difference.
Every application example outlined thus far makes use of existing technology, meaning that water companies can get the most out of their assets without having to invest significant amounts of money.
Digitalization and Regulatory Compliance
Regulation is a central consideration in the water industry, with water quality being increasingly subjected to tight controls and stringent requirements all over the world. There is no room for mistakes when working to meet regulatory requirements, but digitalization can help remove the potential for error.
For example, digital data recorders make accessing real-time information and historical data much easier. An effluent discharge application, for example, would benefit from being able to have information stored securely and accessible immediately.
Digital recording applications also offer functionality, such as early warning notifications sent via email. If a limit is approaching, rather than having to rush out to site, staff can get an email alert well in advance, thus allowing them to address the problem before it arises and ensuring that the company does not fall foul of the regulatory authorities.
These applications tend to be comprised of a digital device surrounded by software and applications, which enhance the functionality of the device and make the measurement process easier.
This is largely possible without the need for significant capital expenditure because these systems essentially combine the company’s existing IT infrastructure (where email and resource planning systems are based) and the company’s operational technology (the instruments in the field).
Digitalization connects these two areas together, driving additional value.
Ensuring Drinking Water Quality via Digitalization
Consumers have a high level of expectancy from their drinking water. The final water should be clear, odorless, non-corrosive and most importantly, free of harmful bacteria and microbes.
Any unexpected deviation in quality could have a major impact, not only on the water treatment facility and distribution network but, more importantly, on the consumer. Many people take drinking water for granted, but a great deal of effort is required behind the scenes in order to deliver consistent quality and to meet regulatory requirements.
Delivering these results can be challenging, especially when faced with issues around poor connectivity, lack of skills, increased regulations, consumer demands and productivity challenges.
Even generic water treatment facilities will vary slightly in the approach they take to water treatment. In general, though, these facilities will maintain a common sequence of water treatment stages, starting with the water intake and ending with the final discharge stage.
A generic water treatment facility will tend to utilize five basic areas of treatment, each with its own demands from a measurement standpoint.
These are the water intake, the pre-treatment stage, coagulation/sedimentation, filtration and ultimately, the final water treatment process. Each of these stages plays an important part in the overall water treatment process.
Looking at these typical stages and combining all the analytical measurements in use can result in as many as 26 different parameters requiring monitoring and adjustment, all in a single facility.
This presents a sizeable challenge in terms of monitoring, maintaining and operating all of these measurement points during the facility’s day-to-day operation.
In addition, if there are no additional backups to the measuring points, any disruption to their operation can have a huge financial, regulatory and environmental impact.
Digitalization can play a significant role in helping water treatment companies improve operations without the need for complicated process adjustments or large financial expenditures.
Industrial Challenges and Digitalization: pH Monitoring
There are four common challenges in the drinking water industry, tied to productivity, connectivity, regulation and skill.
These industrial challenges can be addressed with digitalization and this process offers a range of benefits in relation to key analytical measurements in the water industry; for example, pH, fluoride, aluminum and iron monitoring.
pH monitoring is one of the most commonly utilized analytical measurements across a wide range of sectors.
It plays a key role in a number of industries, ranging from chemicals, carbon, paper, oil and gas and pharmaceuticals. pH sensors can be utilized in environmental monitoring, chemical dosing control, neutralization schemes and in ensuring water quality.
pH monitoring devices are relatively simple in terms of their design, but these can still present a complicated challenge as part of water treatment applications. Because they are so widely used, pH monitoring devices will take up a lot of analysis, maintenance and operational bandwidth within the facility.
Digital solutions can help water treatment companies improve productivity and connectivity in terms of pH monitoring.
A common trend in the analytical world has been the introduction of digital pH sensors. The use of digital probes offers a number of benefits to consumers, including better accuracy and improved signal strength. Their main advantage over analog sensors is a dramatic improvement in productivity.
Digital pH sensors found as part of a pH measurement loop are fitted within the sensor body via an integrated PCB. This PCB helps process the pH signal internally, converting this to a more robust digital signal and substantially improving signal strength when compared to the vulnerabilities of an analog type sensor.
More importantly, digital pH sensors are capable of storing calibration and configuration data in the sensor itself. This feature allows for much easier sensor commissioning and true plug-and-play connectivity.
This highly beneficial feature means that users no longer have to conduct a calibration when they first commission a pH sensor. The sensor can be pre-calibrated in the lab at the user’s convenience, ready to use when they need it.
This feature alone helps reduce the average commission time of a pH sensor from approximately 20 minutes to around 2 minutes when using digital platforms.
Digitalization also provides benefits to other processes, which can greatly improve productivity within the industry. Digital pH sensors improve productivity by utilizing more advanced processing capabilities, such as sensor health monitoring.
In the past, analog sensors could only passively report issues with a sensor, such as broken glass or a plugged junction. When users received the notification, it was often too late because the probe would already be out of commission or behaving erratically.
These problems are usually unpredictable and can occur at any time, but with the introduction of digital probes, it is now possible to improve existing sensor health monitoring without the need for complicated wiring or hardware.
These advanced diagnostics can better predict end-of-life requirements, improving measurement confidence and minimizing process downtime by altering users’ maintenance or replacement requirements ahead of time.
Finally, the digitalization of pH monitoring instrumentation has greatly improved the communication between sensor and transmitter, eliminating some of the vulnerability and limitations of an analog sensor. Water treatment companies no longer need to manage table length limitations or fluctuations in readings due to cable movements.
Industrial Challenges and Digitalization: Connectivity
Some of the most challenging aspects of the water industry are tied to instrument connectivity. The ability to easily and quickly retrieve data from instruments offers huge benefits from an operational perspective.
Digitalization has opened up a number of pathways to improving connectivity between the operator and instrument, helping staff to stay connected when they are out in the field.
For example, newer platforms enabling wireless access via Bluetooth technology can help customers more easily extract the information required by their insurance providers.
Information such as process data, alarm logs and even maintenance schedules can all be viewed from the convenience of a personal cell phone or tablet, greatly improving the availability of vital information and helping users to better coordinate routine maintenance tasks; something that can be especially challenging with pH monitoring applications.
Another advantage of utilizing handheld devices with instrumentation is the ability to access cloud-based services, which can be tied to that specific instrument.
This feature allows users instant access to information specific to that product, for example, product documentation, technical support videos, instructional videos, software updates, product notifications or updates.
All this information is available via existing cell phone technology, without the need for any additional costly or complicated add-ons.
Industrial Challenges and Digitalization: Fluoride Monitoring
Fluoride monitoring is also a common parameter within the water industry. As an important aspect of the drinking water process, fluoridization requires careful monitoring and reporting to meet regulatory requirements.
Digital solutions can provide simple and effective benefits in terms of meeting these specific requirements, particularly when working with security and access to audit logs for recording purposes.
Fluoridization is a common tool used in the global water industry as a means of improving dental health, especially in children. Fluoride levels can be found naturally in some water sources waters, however, and this can interfere with accurate fluoride dosing.
Overdosing of fluoride can negatively impact human health, so accurate and continuous control of the fluoridization process is critical.
Strict regulations are often in place around the reporting of fluoride levels in the water industry, and digital solutions can help meet the increasing demands of regulators when dealing with online measurement of fluoride.
Before the advent of continuous online monitoring, water quality monitoring was generally completed via daily onsite log checks. While this approach is still utilized in some areas, it only provides a snapshot of process information.
In addition, the data collected must be manually logged for record-keeping to meet regulatory requirements. With increasing demands in the water market and calls for more accessible reporting, this manual approach can prove problematic and is prone to gaps and inaccuracies.
Online monitors help simplify these recording requirements by providing continuous updates on processes, therefore allowing abnormalities to be detected, alarms raised rapidly and corrective actions implemented at a much faster rate.
Online instruments can extend operations via regular, automated calibration, which helps ensure accurate monitoring of a process without the need for manual intervention.
One key benefit of digitalization with regards to regulatory requirements is that users, analysts and stakeholders have easy access to data within the instrument, rather than having to rely on external monitors or manually recording the information.
As well as offering the added security of password protected access, online instruments can provide additional features such as full graphical analysis, allowing users to easily visualize data trends in their applications.
Full audit logs also help record any abnormalities by tracking process alarms or diagnostic faults. Finally, the ability to transfer data via SD cards or USB drives allows for rapid information access while extending the internal memory capability of an instrument.
Industrial Challenges and Digitalization: Coagulant Management
A growing issue in industries across the world is the demand for instrumentation which is easier to operate, easier to support and easier to maintain. This issue can be highlighted by looking at another common process within the water industry: coagulation.
Digital solutions can greatly improve the monitoring of both aluminum and iron in the water treatment process from a skill perspective. Drinking water would not be as cheap and plentiful today if it was not for the use of chemical aides known as coagulants.
These chemicals help improve water quality, removing particulates present in water by altering their overall electrical charge.
Prior to treatment, these particulates would normally stay suspended in solution due to their mutual negative charge, which keeps them opposing one another and therefore separate. Particulates result in water that is colored and cloudy, so it is essential that they are removed prior to consumption by the consumer.
Coagulants change the overall charge of the particulates, helping them bond together so they can be easily removed by filtration.
The two most common forms of coagulant used in the industry today are either iron or aluminum-based. In both cases, residual monitoring of either iron or aluminum can help ensure proper dosing of the coagulant, and by doing so, facilities can ensure the highest level of purity while meeting regulatory requirements.
Like fluoride, overdosing of these coagulants can be problematic. This not only leads to chemical waste and cost implications but more importantly, it can cause increased coloration of the water and even contribute to a more corrosive sample. It is critical that accurate monitoring of residual coagulants is carried out during the water treatment process.
Carrying out any experiment is challenging but taking an experiment and making this automated and continuous can be extremely difficult. However, this is precisely what is taking place inside continuous water analyzers, often at the same time as tasks like routine maintenance, reagent replacement and commissioning set up.
This complicated analysis process, further combined with growing demand in the water market along with deskilling in the labor force, has led to huge increases in demand for products that offer simple and easy operation along with the ability to perform routine tasks quickly and with minimal training required.
Summary
Digitalization has the potential to change the water industry for the better. It offers the potential to eliminate guesswork from the water treatment process. Improved connectivity via digital technology makes data more accessible, allowing users to monitor processes remotely and in real-time effectively.
Digitalization also drives productivity, performance and operational efficiency by enabling water companies to better monitor, control and manage their instruments, processes and operations.
Everything outlined in this article is largely achievable using technology that is already readily available. This means there is no need for major capital expenditure or ongoing investment related to upgrades.
Digitalization can also provide a range of tools such as simulation, prediction and optimization through apps.
These tools enable companies to unlock hidden insights and enable greater analysis, allowing potential problems to be predicted prior to the problem becoming a major issue while ensuring that the company does not fall foul of any regulatory requirements.
Digitalization also enables companies to work together more easily, allowing manufacturers to assist customers more efficiently while working to address the deskilling that is so prevalent in the global water industry.
Digital technology enables water companies to virtually bring the expert to their site from anywhere in the world. This helps counter deskilling by incorporating the expertise of an expert engineer into the instrument itself, future-proofing the instrument and making diagnostic tools more accessible.
This potential to virtually bring an expert to a site from anywhere around the world without them needing to get on a plane or travel by car is particularly relevant in the current environment. Overall, the potential benefits of IT and OT coming together are proving to be a real game changer for customers.
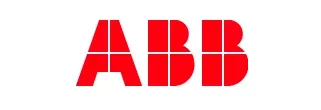
This information has been sourced, reviewed and adapted from materials provided by ABB Measurement & Analytics - Analytical Measurement Products.
For more information on this source, please visit ABB Measurement & Analytics - Analytical Measurement Products.