The world is changing at a rapid pace, and so too is the focus on global emissions. The growing demand for Continuing Emission Monitoring Systems (CEMS) is largely decoupled from the general economy.
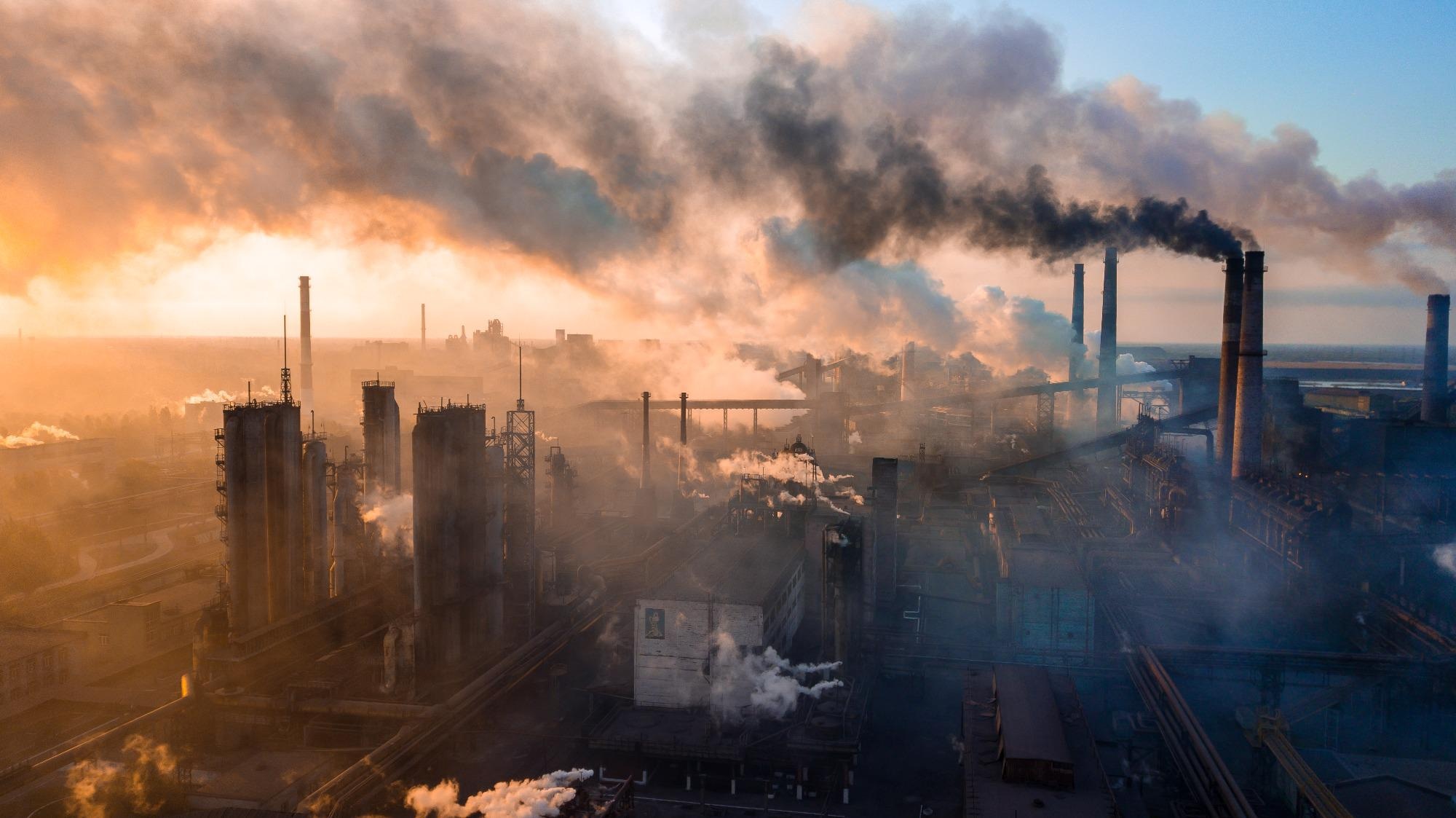
Image Credit: Shutterstock
This is driven by increasing regulation and stricter enforcement, as well as by growing public pressure on corporations to operate sustainably and protect their brand image.
At plant level, there has often been the tendency to focus on the initial cost of CEMS rather than total cost of ownership. This perspective is shifting, however, as organizations begin to realize that compliance or noncompliance can have a major impact on plant availability and profitability.
Plant maintenance resources are increasingly limited, while it is especially challenging to develop and retain good instrument technicians.
These emerging factors increase demand for contracted services and digital software solutions able to ease the burden on plant resources whilst helping organizations to better manage costs.
Emission monitoring and sustainability are the foundations of many successful businesses globally, with CEMS management impacting a diverse array of functions within any organization.
CEMS in Practice
The site manager requires complete compliance, ensuring that all costs are known and documented.
The environmental manager, however, needs to understand and trust the performance of the CEMS equipment, ensuring that data confirms operations are below emission regulations and effectively demonstrating the organization’s compliance with local government auditors.
Maintenance engineers are primarily concerned with resourcing and the need to avoid budget overruns. Meanwhile, operations managers often seek to continuously drive improvements, increasing cost-effectiveness and enhancing productivity.
Addressing all of these stakeholder interests in the most cost-effective way requires a holistic approach, taking into account conflicting and/or corresponding demands and addressing these in a robust, comprehensive way.
ABB supports organizations to do this by building on its firm foundation of 90 years of rich heritage in continuous gas analysis and emission monitoring. The company also boasts a global workforce of over 600 factory-certified service engineers and pioneering digital software solutions that are paving the way for true predictive maintenance.
ABB offers a unique combination of locally available market-leading products and highly skilled service professionals. These advantages are further enhanced by cyber-secure remote assistance and condition monitoring services, culminating in market-leading CEMS solutions delivering unrivaled value for money.
Hardware Solutions
ABB’s gas analyzers are the core measuring technologies of any hardware solution. These technologies have been developed and optimized over many decades in conjunction with a global network of partners.
Optical technologies, including infrared, UV, FTIR and lasers, cover the widest range of components, making these instruments ideal for the measurement of total hydrocarbons and oxygen measurement.
The company’s comprehensive portfolio of in-house technologies can be easily incorporated into scalable product lines, standardized system solutions, meaning that ABB is well equipped to tailor an emission monitoring solution to any measurement requirements.
Optimized Service via Digital Assets
Professional and efficient contract management forms the foundation of ABB’s measurement care service agreements. Speed of response is vitally important for CEMS applications because of the intense pressure that organizations face to remain in compliance and keep plants operational.
ABB offers guaranteed response times in terms of technical support and remote troubleshooting.
Dynamic QR codes embedded in the analyzer display allow rapid transfer of all relevant diagnostic information in a single communication. Factory-certified specialists are mobilized quickly, carrying any required parts to the site with them.
Proactively partnering with ABB throughout the entire equipment lifecycle ensures no unwelcome surprises, as well predictable costs, and extended equipment life. ABB is also able to recommend appropriate spare parts stock to be held on-site, while ensuring that critical parts are available when needed.
Preventative maintenance is a cornerstone of extended asset lifetimes. At the beginning of any partnership, ABB will visit the site to assess the overall condition of the installed base, providing a detailed report and recommendations to aid with future planning.
Asset performance is enhanced by embracing the latest digital technologies, while the wealth of experience available via ABB supports the organization to monitor the CEMS’ condition, better predicting and avoiding failures before they occur.
Assessing Total Cost of Ownership
A number of years ago, ABB conducted a study analyzing the cost breakdown between capital expenditure (CapEx) and operational expenditure (OPEX). The company also surveyed a selection of its customers to obtain their feedback and confirm its assessment.
ABB discovered that approximately one-third of the total cost of a CEMS program is comprised of the initial CapEx, with two-thirds of this total cost being made up of OPEX throughout the asset’s lifetime.
Operational expenditure was further broken down, revealing that this was comprised of approximately 27% for preventative maintenance activities, 25% for repairs, 24% for calibration, 20% for regular visual inspections and 4% for documentation.
This cost breakdown confirmed the vital importance of considering the total cost of ownership when selecting any CEMS solution.
Considering Calibration
Calibration is one of the most significant contributions to operating costs. Calibration is necessary for all types of gas analyzers, but the frequency at which this is required can be much higher depending on the quality of the instruments being used.
The effort and costs involved can also vary significantly based on the approach taken and the number of gas cylinders required for this process.
Regulatory requirements should also be considered, and it may be necessary to validate the CEMS more frequently due to stringent regulations; for example, where organizations are following US EPA requirements which mandate daily validation.
Optionally available in both the AO2000 and EL3000 series, internal gas-filled calibration cells have proven to be extremely popular with ABB’s customers. Glass windows within these instruments are welded to the gold-plated metal housing using a proprietary technique, guaranteeing that the gas cannot escape.
A real test gas with a known concentration is injected via the tubes on either end of the cell and filled inside.
Calibration cells are regarded as an acceptable alternative to flowing test gas in the vast majority of emission monitoring regulations, including the European EN14181 and the US EPA 40 CFR Part 60. These calibration cells will typically last for the lifetime of the analyzer.
ABB tested the cells used in the AO2000 and EL3000, assessing these side by side for over ten years, confirming that the cells’ stability was superior to many cylinder test gases, offering drift of less than 0.5% per year.
More recently, internal validation cells were introduced to ABB’s FTIR-based CEMS system - the ACF5000. This system uses wideband films to absorb infrared light at multiple frequencies, allowing them to be used to validate more than one instrument at a time.
These instruments are approved for the automated drift checks required in Europe while also being compliant with US standards and regulations in other parts of the world.
FTIR-based CEMS is more difficult to calibrate than conventional continuous gas analyzers. Because these instruments are typically used for measuring components such as hydrogen chloride, hydrogen fluoride, or ammonia, the gas is measured hot and wet.
ABB’s fully automated calibration processes will result in a substantial reduction in span gas cylinders required, simultaneously allowing anyone to trigger the validation without any formal training.
The process is also designed in a way that the validation has no influence on the availability of the CEMS measurements reported to the authorities while potentially saving the operator up to 95% in validation costs.
Digital Solutions
ABB is pioneering digital software solutions that are leading the shift towards true predictive maintenance and cyber-secure remote assistance.
Analyzed systems generate a substantial amount of data, and while a certain level of intelligence is often already built into analyzers and systems (for example, triggering warnings or alarms for the user when certain criteria are met), the ultimate goal is to be able to predict a failure before it occurs, allowing this to be prevented.
If something does go wrong, however, it is also important to be able to diagnose and fix this as soon as possible.
Increasing enforcement of environmental regulations around the world has meant that CEMS’ availability and performance are now more critical than ever before.
Digital solutions aim to address this challenge, harnessing the data that exists within analyzer systems and ensuring that data reaches the people who need it in a secure, easy, and fast way; delivering intelligent insights into what needs attention and how this should be addressed.
One such digital solution is the AnalyzeIT Explorer - an asset management software solution that monitors analyzer and sample handling system status to provide an early indication of a change in performance.
ABB delivers this software, with the basic license free of charge as part of its standard system solutions or available separately at cost. Remote monitoring and full control of the system allow the operator to trigger diagnostic or corrective actions without having to physically move to the analyzer, thereby saving time.
The AnalyzeIT Explorer also makes it possible to investigate logbooks for calibration and status messages along with trending temperatures, flows and pressures.
Each of these sets of data offers potential means of recognizing trends or identifying anomalies. Should an issue be detected, validation with test gases or calibration cells can be triggered remotely to further analyze the condition of the system.
ABB Ability is a unified cross-industry digital solution, extending from device to edge to cloud with devices, systems, solution services and a platform designed to empower users to better manage their assets.
ABB Measurement Analytics offers an ever-increasing suite of digital solutions within the ABB Ability Platform, each designed to help the company’s customers increase efficiency and lower operational costs.
These solutions are comprised of a suite of innovative state-of-the-art remote troubleshooting tools, including augmented reality, dynamic QR coding, and cloud-connected expert support.
All these solutions are closely tied to the myABB business portal, which users can access through the ABB website. This portal provides 24/7 access to the user’s install base and a gateway to a range of other online services.
Condition Monitoring
Condition Monitoring for measurement devices involves the use of a software solution that utilizes a robust industrial-grade micro PC.
Data is periodically gathered from ABB gas analyzers and either processed on-site or transmitted securely to ABB via email, where it is then compared against established performance benchmarks to identify any indication of a developing fault as early as possible.
This service is available for the ACF5000, ACF-NT, AO2000 and EL3000 series gas analyzers. Sessions can be scheduled at any frequency, for example, on a monthly basis or as part of a yearly plan.
Each session involves the production of a detailed report, using a traffic light system for quick and easy identification of any issues that need to be addressed.
Condition Monitoring is a simple and effective tool to identify problems with CEMS equipment, often before a failure or loss of measurement accuracy occurs. When early indications of a problem are identified, corrective actions can be taken that are proven to reduce the time to repair.
This solution has been developed as a secure on-premise software application, providing users with the ability to email condition-based reports to ABB experts for remote assessment and predictive analysis, thereby reducing risks of unplanned downtime while enabling faster support and resolution when problems do occur.
CEMS in Practice
The considerations outlined above can be illustrated via a series of case studies. A power plant in Germany employed the AnalyzeIT Explorer asset management software in combination with internal calibration cells.
The plant in question uses more than 20 analyzers employed in a single plant, and by automating calibrations and documenting the drift, the plant was able to reduce maintenance efforts by 80%.
The plant also saved 95% of calibration costs by using calibration cells, reducing the number of test gas cylinders from 100 to 5. By proactively monitoring the analyzer systems remotely, the plant was also able to reduce downtime significantly.
This led the parent company to equip a sister plant in the same manner, with both plants now managed from a single location, further increasing these savings.
A Northern European waste energy company is based in an isolated location, prompting them to include Condition Monitoring in their contract with ABB. Within six months of establishing a measurement care agreement, ABB’s service team had a tangible use case for remote support.
Additional expert analysis was required, with a service engineer performing a regular maintenance program as part of the service contract, despite the client site being situated 300 kilometers from ABB’s office.
When a problem did occur, the expert was able to remotely diagnose the issue and assist the service technician in getting the back analyzer online with minimal delay cost. This remote support saved the customer at least €2000 from having an additional product technician travel to site, as well as avoiding delay and possible loss of production.
A Southern European utility company required assistance in meeting clean air regulations. The operator was a long-standing ABB customer, but the company had separate service agreements for each of its 13 facilities.
While these agreements were effective in meeting the company’s goal of 97.5% air emission monitoring uptime, managing, all these contracts were complex and time-consuming.
In August 2018, ABB combined all these separate service agreements into a comprehensive measurement care agreement.
ABB Ability Condition Monitoring for measurement devices was included in that agreement, ensuring the highest level of availability and reliability of equipment while preventing unplanned outages and downtime.
This helped the operator avoid serious potential costs and risks, ensuring that all equipment is kept in peak operating condition. This change also ensured a streamlined process, as one supplier is responsible for all equipment management and maintenance.
The solution allows ABB to optimize maintenance and enables immediate troubleshooting, which reduces travel expenses and on-site hours for ABB engineers, with all savings passed on to the customer.
Detailed remote health checks increase the data quality of the analytical systems and these improvements enhance overall maintenance efficiency conditions, potentially extending the life cycle of equipment.
The remote support capability of ABB's condition monitoring has enabled the customer’s Italian team to reduce the number of service engineer hours needed on some sites.
In a number of customer facilities, this remote support has resulted in savings for the client of up to €3000 per year when compared to remote support cases that would have required field service engineers to attend in person.
Cost Savings in Practice
The benefits of implementing automated calibration with internal cells, together with condition monitoring, can be demonstrated via an example of potential total life cycle cost reductions.
Taking €100,000 as an assumed initial equipment cost and assuming operating costs are double this amount (based on the research outlined earlier) would result in a total life cycle cost of €300,000.
Calibration and validation costs can be reduced by as much as 95%; for example, the power plant in Germany profiled above was able to reduce efforts for automated calibrations and documentation by 80%.
The proper approach to condition monitoring, in combination with a complimentary preventative maintenance program, has the potential to reduce other operating costs by half.
Continuing the example above, reducing the total life cycle cost by 40% (to around €180,000) and reducing operating costs by as much as 60%.
While each scenario will be different, the potential for overall cost savings via this proactive approach cannot be overstated. Giving proper consideration to the total life cycle cost of assets, coupled with the use of innovative hardware and software solutions, has the potential to drastically lower the overall cost of ownership.
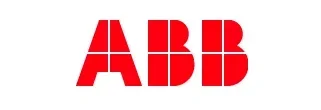
This information has been sourced, reviewed and adapted from materials provided by ABB Measurement & Analytics - Analytical Measurement Products.
For more information on this source, please visit ABB Measurement & Analytics - Analytical Measurement Products.