Guided wave radar technology is highly suited to very difficult level measurement applications. A typical guided wave radar setup will involve a transmitter that is installed on top of a vessel or container and a probe that is attached to the transmitter via a cable.
The radar pulse is confined with the problem and cables, enabling a strong signal to be maintained and accurate measurements to be acquired, even when working in challenging environments.
This method is suitable for use in dusty environments, steam-filled spaces, or at high pressures, high temperatures, or otherwise harsh conditions. Guided wave radar technology is also able to accommodate different types of products, including both solids and liquids.

Image Credit: Shutterstock
Principles of Guided Wave Radar Technology
A radar pulse is sent from the transmitter through the cable or through the probe. The pulse reflects off the products being measured, returning to the transmitter. Time of flight analysis is used to calculate the level of the product.
When working with guided wave radar technology, it is important to consider the dielectric constant of the materials. Water-based products will present a very high dielectric constant, meaning that a strong signal is returned to the transmitter.
Dealing with low dielectric constants does result in some limitations, however. When working with some plastics or oils, it is prudent to verify dielectric of the materials prior to measuring because when working with low dielectric materials, the signal returned is weaker, and it may not be sufficient to properly measure the reflected signal.
ABB offers the LWT300 guided radar series. Introduced in the past year, the LWT300 series utilizes the same platforms as ABB’s range of other products such as pressure and temperature transmitters. Installation of all these products is straightforward via the standard software base and setup menu.
The LWT300 series uses the same coupler design as ABB’s previous model, the MT5000, but all the other parts have been completely redesigned and redeveloped, including the electronics.
The LWT300 series has an identical look and feel to ABB’s other products and the same streamlined approach to make transitioning from one product to another easy via a common menu layout.
The LWT300 series is available with aluminum or stainless-steel housing and touchscreen or push-button interface options. The head can be rotated, meaning it can be installed in more places while maintaining flexibility.
Threaded or flanged interfaces are available, as well as a range of different probes. The probes used in the LWT300 series can be manufactured from a range of different materials, depending on the type of products being measured. Connections are available via cable, rod, segmented rod or coaxial.
There are two specific models available: one for liquid measurements (LWT310) and one for solid measurements (LWT320). Each model offers similar specifications and can accommodate environments with temperatures up to 400 °F and pressures up to 200 bars or 2900 PSI.
The instruments can work dielectric constants up to 1.4 and offer an update rate of 5 Hz. Accuracy is within 2 mm.
The key difference between the two products is the coupler diameter. The coupler is installed between the transmitter and the cable or probes. The coupler must be more robust and often larger when working with solids because the pull force applied to cable or probes when working with solids is higher.
Some guided wave radar applications require the use of a flexible cable with a weight at the end because it is important to keep the cable straight within the vessel. This flexible cable must often cover long distances. The cable is cut to the length that is required based on the height of the vessel.
Rods will generally be made from stainless steel, but other types of materials are available. The rod can be continuous or segmented, with 1 m segments used to construct a rod that is a maximum of 6 m in length. If there are space constraints at the top of the vessel, segmented rods may provide an easier option in terms of installation.
Coaxial probe connections involve the use of a probe contained in a stainless steel tube. The signal is confined within the tube, making this method more suitable for working with very demanding applications and products with a dielectric constant of less than 2. With the coaxial option, there is no deadzone at the top of the probe.
When working with a small vessel that should be measured to the very top, the coaxial probe is often the best choice.
Over the years, guided wave radar has become increasingly popular, but it has historically had a reputation for being an expert-level device. ABB’s guided wave radar instruments offer a much more user-friendly experience, aiming to address these preconceptions.
The LevelExpert Application
The LWT300 series of instruments is operated via the LevelExpert algorithm. This algorithm prompts the user to provide information on the application that the guided wave radar will be used within, examines the waveform and automatically detects the correct level.
This approach is powerful and intuitive, and ABB expects that it will make commissioning guided wave radar instruments accessible to even inexperienced users.
Rather than setting technical parameters such as threshold, detector gain or filter shape, the user is prompted to describe the application itself.
For instance, is the guided wave instrument being placed on top of a nozzle? If so, how long is that nozzle? What are the process conditions? Is there a buildup? Is there foam? Is flashing expected in the application?
Most users will be aware of the answers to these questions, many of which are presented as a series of simple yes/no choices. Experienced users will find this process familiar, but for novice users, LevelExpert will ensure that everything is set up properly, ensuring accurate measurement from the very start.
After the measurement has been taken, LevelExpert will examine the waveform and qualify the different radar echoes. Users can view the waveform or echo shape on the unit itself or on a connected computer via a DTM or FDI package.
Because the application looks at and defines all the different echoes, false echoes are avoided, and measurements are generally more accurate. Users have the option of manually verifying the waveform to check its accuracy, but many users opt not to do this.
If users are looking for more specific information on a particular echo, this can be selected via the application’s menus.
Benefits of Guided Wave Radar Applications
The potential use of guided wave radar applications via long, remote cable offers a mix of convenience and safety. Many applications would involve the electronic head being directly integrated with the coupler, but this is split in two in the LWT300 series, which positions the probe inside the tank itself.
This allows the head to be kept at ground level, meaning there is no need to climb the tank to see it. This is also ideal when working with potentially hazardous products because the remote cable allows workers to take readings from a safe distance of up to 60 m.
The coupler, probe and electronic head are connected via a specific tool, ensuring this is tight enough to prevent any moisture from entering the connector. The cable and system are robust enough to work outside and in internally moist environments.
Many applications require high accuracy and low temperature drift, both of which are easily achievable using guided wave radar.
Temperature drift is an important consideration in terms of overall accuracy because accuracy is defined at a constant temperature (usually room temperature), meaning there is no guarantee that accuracy will be maintained as temperature changes. If accuracy is critical for an application, the temperature drift should certainly be considered.
For example, a very low temperature drift will ensure that accuracy is maintained as ambient temperature potentially changes throughout the day or due to a change in process temperature. A process could inject steam, heating up the transmitter and potentially leading to temperature oscillations during that time.
ABB uses a novel means of compensating for temperature drift, performing 15 to 50 times better than other instruments on the market - 0.2 mm per 10 °C with a maximum of 2.5 mm for the whole temperature range.
Redundant applications will also benefit from a low temperature drift. For example, an application may see two or three guided wave radars reporting the level, triggering an alarm if the level drifts over a given range between the three units.
If temperature changes do result in drift, not all units will drift the same way and there will be some spread in the measurement. If this spread is too large, the alarm will not trigger
Guided wave radar also offers a rapid measurement rate. Many level measurement applications do not require a fast level measurement rate because the levels involved do not change often, but this is critical in some more specialist applications.
The LWT300 series offers a 5 Hz update rate leading to a step response time of 400 ms. This is important in smaller tanks that often fill up quickly or in spherical or cylindrical tanks that are wide at the base but narrower at the top.
Rapid rates of measurement ensure less chance of overfilling, something especially important in many applications.
Guided wave radar instruments also allow users to change the probes without having to recalibrate the unit. This feature is beneficial in a number of scenarios; for example, where users keep a supply of varying length cables on-site for use with different tanks across various settings, or when switching between cable and rod setups or vice versa.
In this example, the user would simply need to enter the new cable length into the unit. Also, the user can change from a cable to a rod and vice versa. All the heads are calibrated in the factory and will work regardless of the type of probe they are used with.
Potential Applications of Guided Wave Radar
Guided wave radar is able to provide reliable, accurate measurements in a wide range of applications, even demanding applications that are subject to vapor, turbulence, flashing, limited foam, and some buildup on the probe, as well as changing temperature pressure and dielectric.
The LevelExpert software offers functions specifically designed to accommodate changes in dielectric constants.
In one straightforward application example, ABB installed guided wave radar on an external chamber as opposed to inside the vessel. This is one of the best solutions in terms of stability and is ideal when there are fluctuations, obstructions or agitations inside the vessel.
Stilling wells and applications using horizontal cylinders can also benefit from the use of guided wave radar. This application benefits from the use of traditional guided wave radar instruments or a coaxial probe, the latter being useful when dealing with low dielectric or long measurements.
In either application, false echoes are minimal, response time is rapid, and accuracy is ensured.
One customer based in Canada opted to use the LWT310 in an oil application to measure H2S. The challenge, in this case, involved obtaining reliable level measurements of crude oil stored in a fiberglass tank. The oil is very low dielectric, and there was interference from radio noise close to the installation.
ABB installed the LWT310 and used a 25 ft flexible cable, connecting this via a flange to a flat metal surface. This is very important to ensure an effective radar pulse launch. The probe was fitted into an external chamber via a segmented rod.
The customer in this example used the LevelExpert setup algorithms to complete the installations in-house with no support required, citing the LTW300 series’ reliability, affordability and robustness as key factors informing their choice to use these instruments.
Guided wave radar can be used in virtually all industries, and ABB offers a range of different applications to ensure reliable, precise measurements.
In another example, a company in Warsaw, Poland, working in the water industry, uses an LWT310 to accurately and rapidly measure water levels with a view to preventing floods. The customer was looking for reliable solutions that did not present false echoes, having previously had false echo issues with ultrasonic solutions.
This application required the solution to work in a narrow space of around 3.6 m, along with the option to use redundant measurements. This need for redundant measurements prompted the customer to use two guided wave radar instruments to help alleviate the risk of flooding between sections of the tunnel.
The customer performed the installations in-house using the LevelExpert algorithm. The commissioning had to be completed quickly, and since they installed the LTW310s, the customer has been much better equipped to monitor and prevent flooding.
Cooling towers are another popular use of the LWT310 instrument, with several customers using this to measure the water levels in a cooling tower system. Cooling towers are prominent across many industries, including power plants, petroleum refineries, petrochemical plants and even food manufacturers.
Typical installations are done using a long-distance pipe - around 25 ft in length. Cable probes are common, but it is important that the cable does not touch the side of the pipe because this leads to false echoes. The cable is kept in the middle of the pipe using spacers in this scenario.
Other applications may see the LWT300 series replacing bubblers or other non-contact devices because these applications are demanding, potentially dealing with foam, turbulence, or sludge in some cases.
Summary
One of the main advantages of guided wave radar is its high accuracy of up to 2 mm – much higher than any other instrument available on the market. Reliable measurement is possible even in harsh conditions, and because the pulse is confined by the probe and the probe touches the material, a lot of energy is available to analyze the signal.
The LevelExpert algorithm offers a new and improved means of interacting with the device, making this technology much more accessible to anyone who knows a lot more about their application than they do about how the device performs.
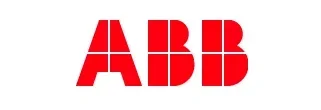
This information has been sourced, reviewed and adapted from materials provided by ABB Measurement & Analytics - Analytical Measurement Products.
For more information on this source, please visit ABB Measurement & Analytics - Analytical Measurement Products.