Sulfur is a natural element present in most hydrocarbon feed streams and contributes to a number of undesirable effects, including detrimental product quality, catalyst poisoning and ecosystem pollution.
Thus, it is necessary to quantify and monitor the sulfur content in almost every step of the industry´s operations or for regulatory control and final product specification.
Complete analysis of the sulfur content in hydrocarbons by combustion and UV fluorescence detection has been determined as the preferred method to identify feedstock, intermediate streams and finished hydrocarbon products. This is due to the sensitivity, linearity, dynamic range and ruggedness of this technique.
ASTM D5453 is a widely-accepted test method for identifying the total amount of sulfur in liquid hydrocarbons containing 1.0 to 8000 mg/kg total sulfur; boiling in the range from approximately 25°C to 400°C and with viscosities in the region between 0.2 and 20 cSt (mm2/S) at room temperature.
This test method is appropriate for determining total sulfur in liquid hydrocarbons comprised of 0.35% (m/m) halogen(s).
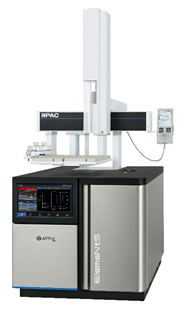
Image Credit: PAC L.P.
Measuring Principle
Using a fully automated liquid sampler, a hydrocarbon liquid sample is injected directly into a high temperature, dual temperature zone combustion tube in which the sulfur components are vaporized and combusted. The sulfur released is then oxidized to sulfur dioxide (SO2) in an oxygen-rich atmosphere.

After the water vapor generated has been extracted, a stream of inert gas (helium or argon) carries the reaction products into a reaction chamber. Here the SO2 molecules are transformed to excited SO2* using a UV lamp for the absorption of energy emitting light (fluorescence) while it relaxes to a stable state.
SO2 + hν → SO2*
SO2* → SO2 + hν
The emitted light signal is measured using a photomultiplier tube. The response signal is incorporated to determine the area, followed by the calculation of the sulfur concentration of an unknown product using the linear regression function of the concentration of conventional mixtures versus integrated area.
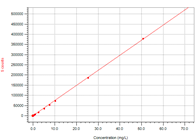
Image Credit: PAC L.P.
Validation
The methodology and system of the Antek ElemeNtS total sulfur analyzer is tested comprehensively for recovery and repeatability, response linearity and sample scope to verify its performance according to ASTM D5453.
Calibration
Calibration curves are controlled using tert-Butyl-di-Sulfide in o-Xylene standards. Each calibration solution and blank (o-Xylene) is evaluated on three occasions. The mean response of the blank injections is deducted from each calibration standard response conform method.
Table 1. Response values. Source: PAC L.P.
Concentration ng/µL |
Avg Area counts |
1.022.17 |
7073493 |
780.20 |
5420778 |
515.28 |
3587715 |
264.37 |
1844192 |
102.16 |
715151 |
78.00 |
543926 |
51.73 |
358257 |
25.88 |
182531 |
10.31 |
70464 |
7.81 |
53266 |
5.20 |
35585 |
2.60 |
18343 |
1.03 |
7599 |
0.52 |
4214 |
- |
834 |
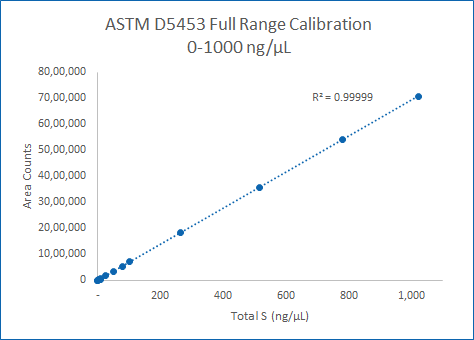
Figure 1. Full range Calibration curve covering typical range of ASTM D5453. Image Credit: PAC L.P.
Although in the range from 0 – 1000 ng/µL (figure 1), the ElemeNtS system demonstrates a linear response, individual calibration curves have been developed in line with the suggested ranges in ASTM D5453 (Figure 2,3,4).
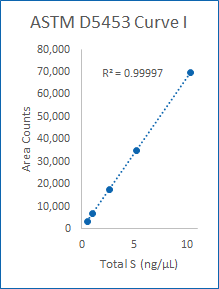
Figure 2. Curve I (0,5-10 ng/µL). Image Credit: PAC L.P.
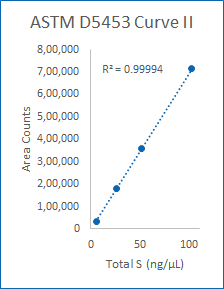
Figure 3. Curve II (5-100 ng/µL). Image Credit: PAC L.P.
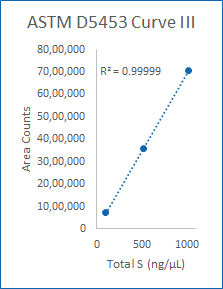
Figure 4. Curve III (100-1000 ng/µL). Image Credit: PAC L.P.
Sample Scope
Various types of samples (Gasoline BOB, Reformulated Gasoline, E85, Diesel B7, Jetfuel, heating oil) were chosen to offset the boiling point range of the method’s scope. To achieve one result, each sample is measure three times, and the mean detector response is determined.
The results are contrasted with the consensus values acquired during the Proficiency Testing Program (PTP). All sample results align with the range of the ASTM D5453 reproducibility limits (table 2).
Table 2. Overview of sample results, compared with consensus values of PTP. Source: PAC L.P.
AC part # |
Type |
PTP mean
(mg/kg) |
Result
(mg/kg) |
Delta |
D5453
R/√2 |
00.02.729 |
Diesel B7 |
9.4 |
10.2 |
0.8 |
2.2 |
00.02.730 |
E85 |
1.7 |
1.7 |
0 |
0.6 |
00.02.732 |
Jetfuel |
507 |
523 |
16 |
45 |
00.02.733 |
Gasoline Enhanced |
4.4 |
5.0 |
0.6 |
1.3 |
00.02.734 |
Gasoline BOB |
2.6 |
3.3 |
0.7 |
0.8 |
00.02.735 |
Diesel B7 |
9.6 |
10.5 |
0.9 |
2.2 |
00.02.736 |
Jetfuel |
168 |
181 |
13 |
19 |
00.02.737 |
Heating oil |
29 |
30 |
1 |
5.2 |
Recovery / Bias
Two NIST standard reference materials (SRM) were evaluated to identify any bias, such as what is detailed in ASTM D5453-16, chapter 15.2. The samples were gasoline SRM 2298 (4,7 mg/kg ± 1,3 mg/kg), and diesel SRM 2723a (11,0 mg/kg ± 1,1 mg/kg).
The differences observed between the values shown and the ARV (Accepted Reference Values) of the NIST standards meet NIST uncertainty limits (table 3). A representation of the injection signal of NIST SRM 2298 and 2723a is illustrated in Figure 5.
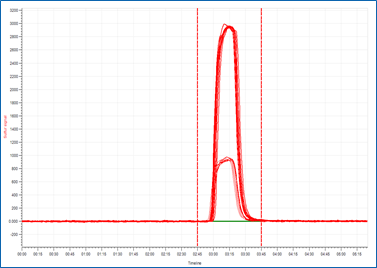
Figure 5. Overlay NIST SRM 2298 and SRM 2723a signal (n=10). Image Credit: PAC L.P.
Table 3. Comparison of NIST and analysis results. Source: PAC L.P.
NIST SRM |
2298 |
2723a |
Matrix |
Gasoline |
Diesel |
Sulfur mg/kg NIST |
4.7 (±1.3) |
11.0 (±1.1) |
Sulfur mg/kg Measured |
4.3 |
11.1 |
Observed Difference mg/kg |
0.4 |
0.1 |
Within NIST uncertainty limits |
Yes |
Yes |
Repeatability
The area is the principal measurement in total sulfur analysis. The measurement accuracy ultimately confirms the validity of the quantitative data generated. Area precision demands precise control of all operational conditions.
The inertness of the flow path can significantly influence area precision, particularly for sulfur components at low levels.
Utilizing two NIST reference samples, concentration repeatability for the ElemeNtS total sulfur analyzer is measured for ten consecutive runs. Repeatability standard deviation of total sulfur aligns with the precision statement of ASTM D5453.
Table 4. Repeatability values of NIST 2298 and 2723a reference material. Source: PAC L.P.
Run |
NIST 2298 |
NIST 2723a |
mg/kg S |
mg/kg S |
1 |
4.25 |
11.16 |
2 |
4.35 |
11.11 |
3 |
4.38 |
11.13 |
4 |
4.35 |
11.10 |
5 |
4.33 |
11.10 |
6 |
4.42 |
11.09 |
7 |
4.33 |
11.07 |
8 |
4.38 |
11.08 |
9 |
4.32 |
11.07 |
10 |
4.31 |
11.10 |
Average |
4.34 |
11.10 |
Standard deviation (SD) |
Measurement |
0.048 |
0.029 |
Method SD
(r D5453/2.77) |
0.21 |
0.39 |
Relative standard deviation (RSD) |
Measurement |
1.10% |
0.26% |
Method RSD
(r D5453/2.77)/mean |
4.36% |
3.54% |
Conclusion
These results show that the ElemeNtS analyzer is an efficient and effective tool for the identification of sulfur in Light Hydrocarbons, Diesel Engine Fuel, Spark Ignition Engine Fuel and Engine oil. This is based on the excellent calibration linearity, low limit of detection, exceptional repeatability and recovery.
The Antek ElemeNtS total Sulfur analyzer meets ASTM D5453 requirements.
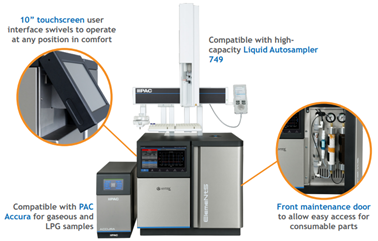
Antek's lab instruments provide reliable, precise elemental analysis for total nitrogen and sulfur, speciated nitrogen and sulfur, fluoride, chloride, and bromide. Antek products are recognized by global regulating bodies, leading scientific research institutions, and process laboratories as the instrument of choice for selective multi-element detection. Image Credit: PAC L.P.
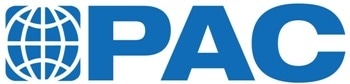
This information has been sourced, reviewed and adapted from materials provided by PAC L.P.
For more information on this source, please visit PAC L.P.