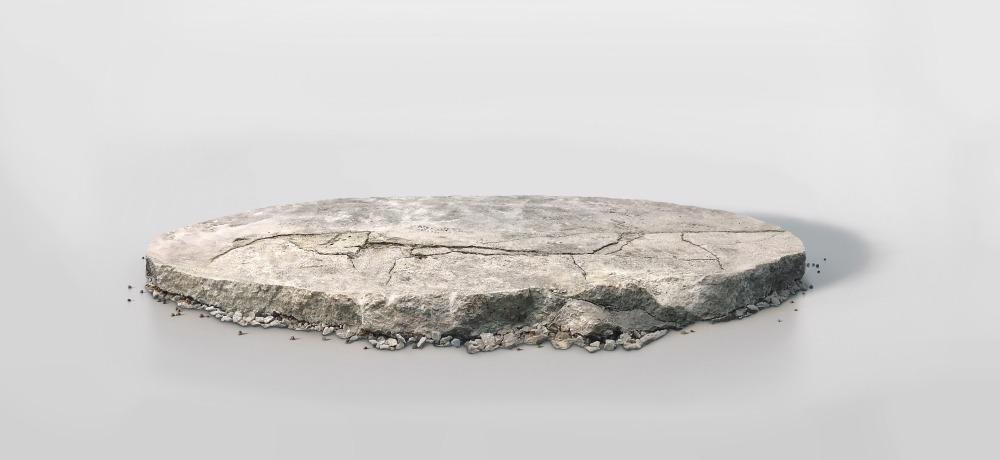
Image Credit: Red Tiger/Shutterstock.com
Elucidating the physical and chemical properties of a material is key to understanding how it interacts with other materials and performs in each application. One property of a material that affects its performance is the surface roughness (also known as surface finish.) This article will provide a brief overview of this property, analysis techniques, and why it is important to analyze.
What is Surface Roughness?
Surface roughness refers to the condition of processed surfaces. Irregularities present on the surface of the object determine the texture and appearance of the surface, which plays a significant role in that surface’s characteristics. The visual appearance and tactile feel of a surface are often described with terms such as matte-and-silver, mirror-finish, or smooth-and-shiny. Surface roughness is a numerical scale of the texture of a surface that is not dependent on tactile or visual sensation.
Surface irregularities on materials and parts can be created intentionally in the manufacturing process or be produced by various factors. These factors include vibrations caused by cutting tools, the bite of the edge used, or the physical properties of the material itself. Facial irregularities can show diversity, with different sizes and shapes that overlap in layers. The field which studies surface roughness amongst other small-scale features of a material is known as surface metrology.
Why is it Important to Measure Surface Roughness?
Irregularities tend to form nucleation sites, which cause breaks or corrosion in the material. This can cause rough surfaces to undergo more rapid wear and tear than smoother surfaces, but roughness can also encourage adhesion. The adverse or favorable influence of surface roughness is determined by the size and shape of the irregularities present. Surface roughness is a good predictor of mechanical part performance.
In engineering applications, there are tight quality parameters for surfaces and parts. Therefore, it is crucial that the roughness of a surface is measured accurately so it can adhere to the required standards in quality. Roughness is often undesirable, but it is difficult to control in manufacturing. Decreasing the roughness leads to the increased manufacturing cost of components, so there must be a trade-off between this cost and its performance application.
Characteristics of finished products that surface features affect include friction, durability, energy consumption, tightness, and operating noise. These are all important factors that govern the function and suitability of a component for industrial applications. Ink/pigment application and the varnish of panel materials are also affected by the surface features of a material.
All this can make the difference between a useable product and one that will be discarded and can affect project critical factors such as cost and material usage as well as safety for the operator of the finished product. Therefore, it is easy to see why the quantification of surface roughness, alongside other small-scale features of a material such as primary form and surface fractality, is such an important consideration in industries such as medical diagnostics and materials processing.
Defining Surface Roughness
There are three main ways to define surface roughness: statistical descriptors, extreme value descriptors, and texture descriptors.
Statistical descriptors include average roughness (Ra) and root mean square roughness (Rq). Extreme value descriptors include maximum peak height (Rp) and maximum valley height (Rv.) Texture descriptors include corrosion length. Ra is the most effective and commonly used measure of surface roughness.
Several techniques have been developed over the years to analyze these values and provide information on the finished product’s surface roughness and its suitability for the desired application.
Surface Roughness Analysis Techniques
Methods developed to measure surface roughness include direct measurement, non-contact, and comparison methods. These have been improved upon over the years to create the raft of analytical tools and methods available to scientists today.
- Direct methods – These use a stylus to evaluate the roughness of a surface, much like a vinyl record player. Roughness parameters are then established by the profile registered by the equipment. There is a drawback to direct methods, however, as they call for the disruption of the manufacturing process and the use of a physical stylus that must be in contact with the surface, which can cause damage to it.
- Non-contact methods – These use light or sound in place of a stylus. The reflected light or ultrasonic waves are measured to detect minute differences which are then used to measure the surface roughness features. Being non-destructive, they do not interfere with the manufacturing process and can be automated. Equipment used for non-contact techniques includes laser microscopes, coherence scanning interferometers, scanning probe microscopes, and digital microscopes.
- Comparison methods - These use samples of surface roughness that have been generated by the same material, process, and equipment being used. These pre-existing samples are then compared with a new sample, which determines if the surface roughness of the new material falls within the desired parameters. Due to the subjective nature of these techniques, they tend to be used for non-critical applications.
In Conclusion
Often, a gradual breakdown in surface quality or imperfections in the manufacturing process which leads to initially small issues can cause a component's breakdown. Proper surface feature analysis identifies the possible imperfections within the material which, if carried out to a high enough standard, avoids issues such as this and makes the manufacturing process more efficient and the end-product more suitable for its desired application.
References and Further Reading
Qualitymag.com (website), Measuring Surface Roughness [Accessed online 13 April 2021] https://www.qualitymag.com/ext/resources/files/white_papers/Olympus/LEXT-Surface-Roughness.pdf?1604073669
Septiadi, D and Nasution, A (2009) Determining Surface Roughness Level Based on Texture Analysis ResearchGate.net [Accessed online 13 April 2021] https://www.researchgate.net/publication/264542054_Determining_Surface_Roughness_Level_Based_on_Texture_Analysis
Keyence.com (Website), What is Surface Roughness? [Accessed online 13 April 2021] https://www.keyence.com/ss/products/microscope/roughness/line/
Disclaimer: The views expressed here are those of the author expressed in their private capacity and do not necessarily represent the views of AZoM.com Limited T/A AZoNetwork the owner and operator of this website. This disclaimer forms part of the Terms and conditions of use of this website.