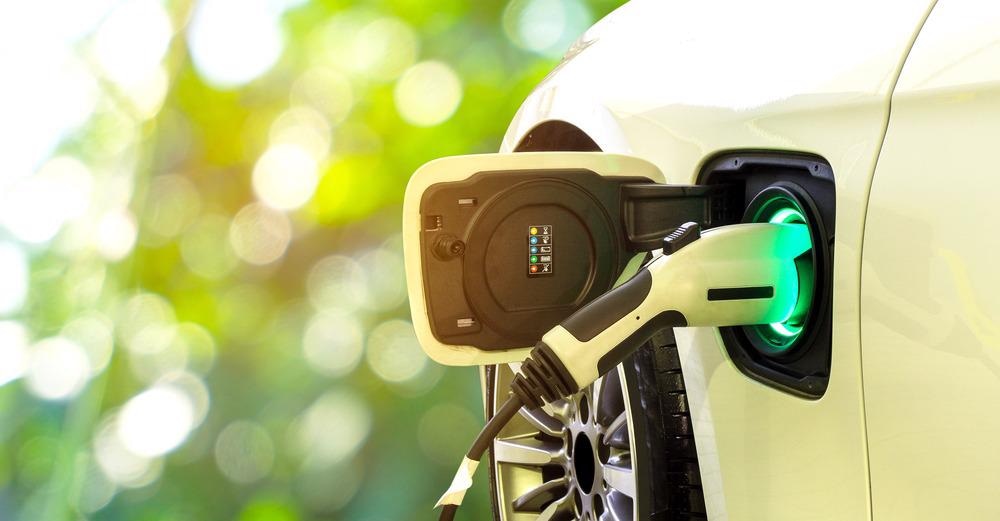
Image Credit: Smile Fight/Shutterstock.com
Found in every kind of modern vehicle, semiconductors make it possible for electric cars to be efficient, interactive and safe, which is critical when human life is at risk.
Why are Semiconductors Needed in Cars?
In the most visible sense, semiconductors are necessary for various interactivity features that could be accessed by a driver and passengers. They are also necessary for batteries and power trains in an electric vehicle and are key to the essential firmware found in most modern vehicles.
Modern electric cars require connectivity that enables a manufacturer to send essential software updates to the car’s firmware, including the brake system and power train, without the user having to lift a finger.
The more sophisticated the electric car, the more semiconductors it will require. The typical amount of semiconductor parts inside an electric car is increasing rapidly. As options such as blind-spot detectors and backup cameras come to be standard on all automobiles, these functions need semiconductors, and as a result, drive up the need for the valuable metals that comprise them.
The Drive for More Semiconductors
As autonomous driving becomes more common, the industry is likely to demand more semiconductors. Likewise, demand for semiconductors will grow as manufacturers add more electric vehicles to their fleets.
Potential developments in the semiconductor sector could provide longer battery life for these next-generation vehicles. While this specific technological development enhances the practical appeal of electric vehicles, giving them a range that competes with combustion engine cars, it would also translate to a large uptick in demand for semiconductors.
Current statistics show electric cars are becoming more accessible. In 2018, overall sales were 4 million, and 5 million electric vehicles were projected for 2019. However, sales in China and elsewhere were significantly affected by the COVID-19 pandemic.
Despite the pandemic, every top automaker continues to make electric cars more accessible. For instance, BMW is pushing for electric cars to make up 15-25% of overall sales by 2025, while Honda is striving for two-thirds of its overall sales to be electric cars by 2030. Obviously, those goals are a work in progress in light of the global pandemic.
Electric cars that are presently in the marketplace continue to be gradually embraced by the typical consumer. Experts credit the Toyota Prius with starting the widescale adoption of electric vehicle technology. In 2021, Tesla continues to be the subject of mass speculation, as seen in its wildly fluctuating stock price. While Tesla started as an ultra-luxury brand, the company debuted a more affordable Model 3 in 2017, with a $49,000 price tag.
As new models emerge, the semiconductor supply chain is expected to be placed under increasing and different stresses. For instance, cobalt is an essential element to create semiconductors, and over 50% of the world’s cobalt production originates in the turmoil-stricken Democratic Republic of Congo.
COVID-Related Semiconductor Shortages
In February 2021, US President Joseph Biden sat down with members of Congress to talk about a fundamental worldwide lack of semiconductors. The shortage can largely be traced back to production cutbacks of standard semiconductors at the beginning of the COVID-19 pandemic. Interestingly, the production of more sophisticated semiconductors has not been as severely affected.
The semiconductor shortage is a major concern as automakers shift to electric cars, pushing demand higher. In addition to being found in electric cars, semiconductors are also needed for smartphones, computers, and various smart devices.
In early 2021, the production of semiconductors started its return to pre-pandemic levels, but facilities understanding how to produce based on need is a highly complex issue. Supply issues are expected to lead to shortfalls of both common electronic items and vehicles of all kinds. While some electric cars require sophisticated microprocessors that were less affected by the pandemic, simple chips are vital to the manufacture of modern cars.
Shutdowns of semiconductor production facilities and greater demand for connectivity at the outset of the pandemic amplified the shortage, and facilities do have limitations to production. Most semiconductor facilities can only make so many “wafers per hour” due to limited throughput.
The automotive industry has been forced to deal with these limitations and shortages. In April 2021, both Ford and General Motors said they would be for the short-term shutting down production at several North American production facilities due to a lack of semiconductors.
The shortage has also hit every other automaker, with some non-US manufacturers announcing production cuts, including Honda, Toyota, and Volkswagen. Chinese electric vehicle manufacturer Nio also announced a stop to production in March 2021.
Resources and Further Reading
Cornell Media Relations Office. As EVs take off, semiconductor demand to rise amidst chip shortage. Cornell University. [Online] Available at: https://news.cornell.edu/media-relations/tip-sheets/evs-take-semiconductor-demand-rise-amidst-chip-shortage
Whalen, J. General Motors and Ford halt production at more factories as global semiconductor shortage worsens. The Washington Post. {Online} Available at: https://www.washingtonpost.com/technology/2021/04/08/gm-manufacturing-chip-shortage/
Manufacturing Business Technology. Semiconductors Are Key to the Future of Electric Vehicles. [Online] Available at: https://www.mbtmag.com/quality-control/article/13247783/semiconductors-are-key-to-the-future-of-electric-vehicles
Disclaimer: The views expressed here are those of the author expressed in their private capacity and do not necessarily represent the views of AZoM.com Limited T/A AZoNetwork the owner and operator of this website. This disclaimer forms part of the Terms and conditions of use of this website.