Effective fabrication of complex, high performance semiconductor devices is highly dependent on the use of chemical mechanical planarization (CMP). This process is used to planarize the wafer surface before the next layer of metal or dielectric is deposited.
Current trends in lithography are adding increased pressure to CMP process steps. For example, reductions in line widths and the spacing of metal features are pushing the limits of 193 nm immersion lithography.
One means of circumventing this issue is the adoption of self-aligned double patterning (SADP) or quadruple patterning in order to reach the required dimensions. This approach sees wafers undergoing several CMP steps for each layer, however.
CMP is necessary, but this may also contribute to yield loss in applications where the process is not appropriately monitored and controlled. As more CMP steps are introduced into the process and the thickness of the material being removed decreases, it becomes increasingly difficult to manage CMP defect reduction.
Complex chip architectures with smaller critical feature sizes result in greater risk, allowing less room for error. Because of this, it is necessary to implement process optimization steps in CMP slurries in order to ensure that desired yields are maintained.
CMP slurries are generally comprised of silica, alumina, or ceria nanoparticles suspended in an aqueous solution. The material removal rate (MRR) of CMP slurries is dependent on the type of metal or oxide being removed, slurry properties and process parameters, for example, applied pressure or the speed of the polisher.
Maintaining strict control over slurry properties such as working particle size, chemistry and particle size distribution is important in ensuring the desired removal rate is achieved with minimal CMP-induced defects.
Reduced concentrations of oxidizing agents and polishing particles in a slurry will slow the material removal rate, thus enabling more precise control when working with nanoscale layers.
The working particle size in a CMP slurry working with leading-edge devices will typically fall between 30 and 200 nm, meaning that from a defect risk perspective, even sub-micron particles are considered large. CMP removes very thin layers of material, so slurry stability is essential in maintaining a sufficient removal rate.
Ensuring a proper balance of performance, process speed and cost tilts toward performance in cases where particles around 100 nm in diameter can cause considerable, potentially killer, defects.
Precisely controlling slurry chemistry and working particle size is essential if yields are to be enhanced. Slurries should have a narrow, uniform particle size distribution alongside a consistent and reliable balance of chemical components.
This article explores three types of process data analytics useful in ensuring high CMP yields: electrochemical analysis during blending, in-line process chemistry monitoring and particle size determination (Figure 1).
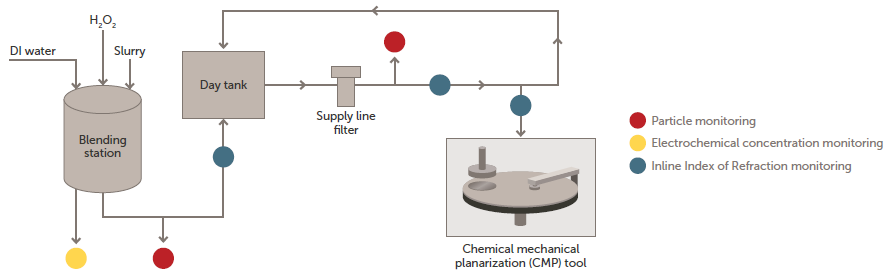
Figure 1. CMP process overview showing where chemical concentration monitoring and particle size analysis fit into the process flow. Image Credit: Entegris
Read the Full WhitePaper Here
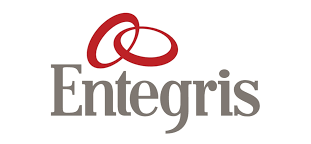
This information has been sourced, reviewed and adapted from materials provided by Entegris.
For more information on this source, please visit Entegris.