Both wood and polyurethane foams are applied in the manufacture of radioactive material containers. As most of these radioactive material containers are typically certified for use over the course of decades, it is vital that the materials used in construction retain their physical properties over the lifetime of the application.
This study evaluates the characteristics of material aging and the fitness-for-use in long-term applications.
Back in 1997, a long-term continual aging test was initiated at Portland General Electric’s Trojan spent nuclear fuel dry storage facility, when the ISFSI impact limiter was first fabricated utilizing LAST-A-FOAM® FR-3708.
A subsequent long-term and ongoing aging study of LAST-A-FOAM® and multiple wood species exposed to the elements commenced in the December of 1999 by General Plastics Manufacturing Company.
General Plastics outlines the results of recent testing in these two long-term and ongoing aging studies of LAST-A-FOAM® polyurethane foam across a period of 20-years.
Experimental Conditions
Enclosed Storage
The encapsulated storage samples are held in a weather-tight, stainless steel enclosure kept at Portland General Electric’s Trojan Spent Nuclear Fuel dry storage facility. Additionally, each sample is packaged with polyvinyl film.
Figure 1 shows the enclosed storage condition with the door open; the foam in the exposed storage condition did not exhibit any water damage or biological contamination.
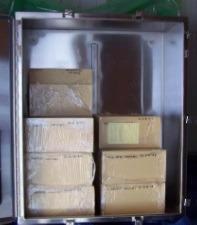
Figure 1. Enclosed Storage. Image Credit: General Plastics Manufacturing Company
Exposed Storage
The wood and PU foam materials were exposed year-round to the extreme environmental elements of the Pacific Northwest in the uncovered storage conditions. The specimens were stored in a subterranean concrete vault which had an open grate at the top.
The foam and wood were proportionately exposed to dust, dirt, insects, seasonal Pacific Northwest weather, and organic debris from plant life in the surrounding area (see Figure 2 and 3, below).
The expanded metal boxes were taken from the vault and transported indoors so that ambient conditioning could commence for a period of one week before handling. The accumulated debris was cleaned from the materials with light brushing, but they were not re-surfaced.
The specimens were placed in a conditioning chamber for a minimum of 40 hours at 70 +/- 5°F and 50 +/- 5% Relative Humidity after being cut to size prior to testing. Other than being subjected to the light cleaning, the 1.0” thick dimension was tested as it was found.
Some of the wood material showed considerable signs of decay and damage due to attacks by fungus and insects. Specimens were cut from the best areas of the stock, and these specimens received some light sanding to enhance the surface finish that comes into contact with the platens of the test machine.
Only the fresh-cut surfaces would be used as the test specimen, cut to meet the final specimen size. As the wood specimens demonstrate overall higher compressive strength, they were cut to 1” cubes to accommodate the capacities of the universal test machine.
The foam specimens were also 1.0” thick. However, due to the lower density, the tested surface area was 2”x2”.
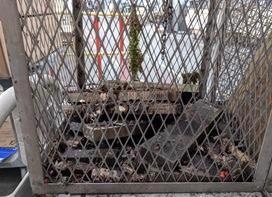
Figure 2. Exposed Wood Samples. Image Credit: General Plastics Manufacturing Company
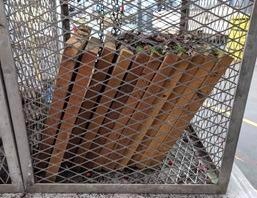
Figure 3. Exposed Foam Samples. Image Credit: General Plastics Manufacturing Company
Data
Density tests were carried out according to ASTM D-1622 while utilizing a digital caliper and scale. ASTM D-1621 was employed for compressive strength testing using a Shimadzu AG-X Plus 100 kN Universal Testing Machine. Five specimens of each material were tested at each condition.
FR-3708, Enclosed Storage |
Date |
Density (pcf) |
C/S (psi) |
Oct 1997 |
8.06 |
227.3 |
Jun 1999 |
8.04 |
251.0 |
Sept 2000 |
7.99 |
213.0 |
Jul 2004 |
8.06 |
210.4 |
Aug 2009 |
8.1 |
208.0 |
Aug 2019 |
8.11 |
216.4 |
Average |
8.06 |
221.0 |
Std. Dev. |
0.04 |
16.2 |
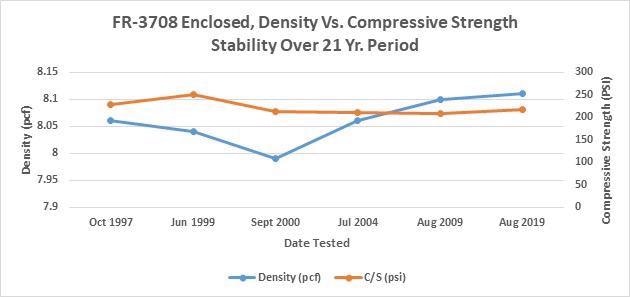
Image Credit: General Plastics Manufacturing Company
Exposed Storage (Foam and Wood)
Where all wood specimens were tested parallel to the vertical growth of the tree, all foam specimens were tested parallel to the rise of the foam when produced.
See Table #1 for LAST-A-FOAM® test results and Table #2 for wood test results.
Table 1. Last-A-Foam® Test Samples and Testing Results. Source: General Plastics Manufacturing Company
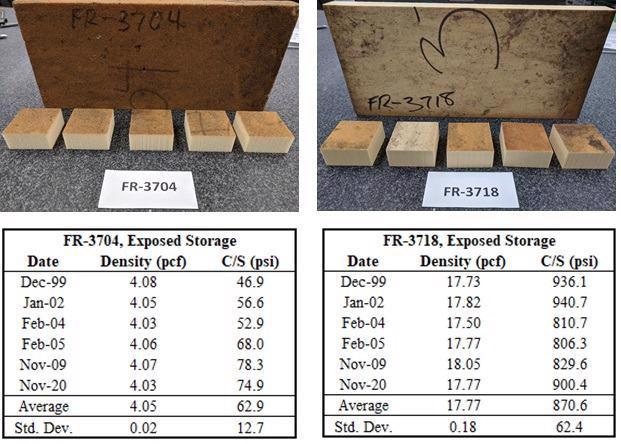
The Density and Compressive Strength of the LAST-A-FOAM® specimens under evaluation demonstrated results consistent with typical product variation, with no aging apparent or exposure-induced shifts in performance.
The graphs below demonstrate comparative test data for the two densities of LAST-A-FOAM, representing tests performed over a period of 21 years.
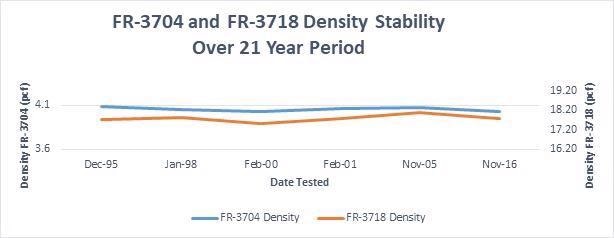
Image Credit: General Plastics Manufacturing Company
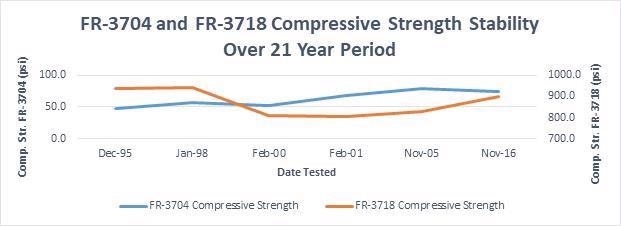
Image Credit: General Plastics Manufacturing Company
Table 2. Wood Samples And Testing Results. Source: General Plastics Manufacturing Company
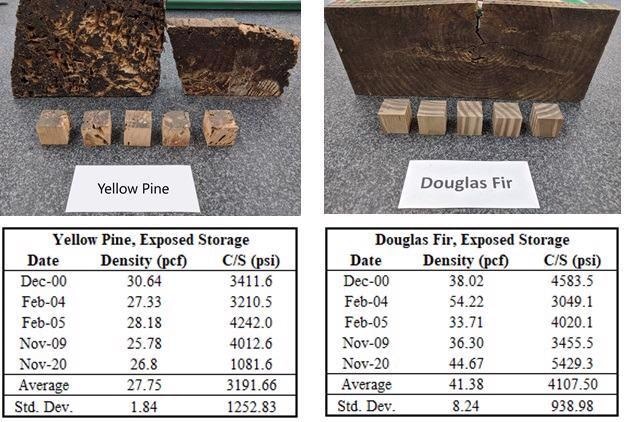
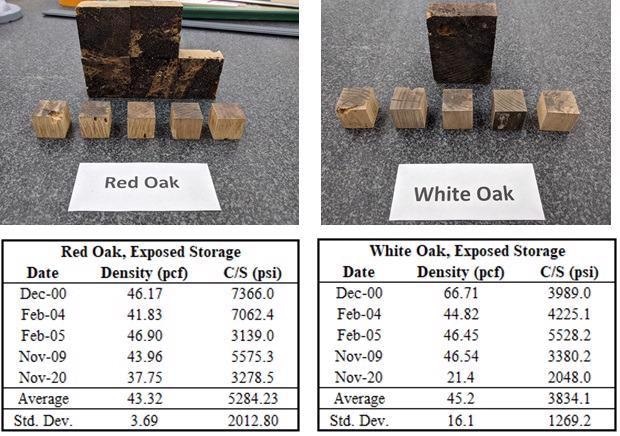
For the four species of wood, comparative test data is exhibited in the graphs below, representing tests carried out over the last 21 years.
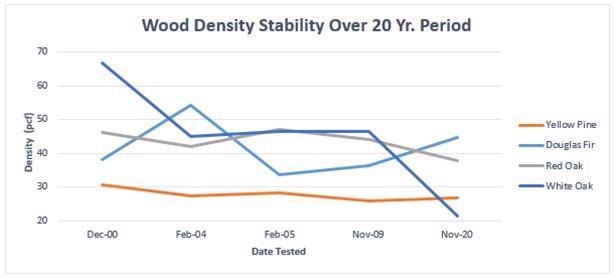
Image Credit: General Plastics Manufacturing Company
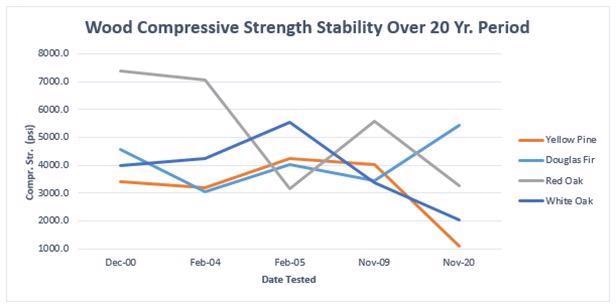
Image Credit: General Plastics Manufacturing Company
Discussion
For sample aging, two storage conditions were used. One set of samples was enclosure aged to simulate the ISFSI impact limiter condition, and the other to reproduce aging when materials experience prolonged exposure to the elements. Only the FR-3708 foam samples were aged in the enclosed storage condition.
Neither the enclosed nor exposed LAST-A-FOAM® material demonstrated considerable decreases in density or compression strength after a period of 20 years. The LAST-A-FOAM® products exposed exhibited the yellowing typically expected of polyurethane products due to UV exposure. The condition was restricted only to the surface.
When cut, the 21-year-old cut specimens showed virgin material typical of a newly produced material. Any moss found to be growing on the LAST-A-FOAM® material was a result of the underlying organic matter of leaves, dust and dirt, and not the foam material itself.
The foam demonstrated that LAST-A-FOAM® products do not support fungal growth conditions as results were consistent with previously conducted independent fungal tests. (Ref. ASTM G21 and MIL-STD-810G1 Method 508.7)
After 20 years of exposure, the wood samples exhibited various amounts of instability in both density and compression strengths.
Considerable amounts of organic matter were seen on the wood material, including but not limited to moss and mushrooms. Thus, due to its vulnerability to fungus and insects, the wood samples demonstrated signs of significant decay.
Of the four wood species included in this review, over time, the Douglas Fir performed better than other wood species. However, the Oak species may not last the next five years or even produce a specimen for testing planned in 2025.
As the graphed performances demonstrate, the PU foam demonstrates excellent resistance when exposed to severe environmental and biological conditions exhibiting better consistency in performance when in comparison to that of wood.
While some soiling and yellowing of the exterior LAST-A-FOAM® surfaces can occur, the closed-cell nature of the material guarantees that the environmental impacts do not extend beyond the surfaces exposed to the elements.
All foam samples showed virgin material when conducting sample examination below the surface, while no negative effect on mechanical performance was witnessed.
Conclusion
In applications where material stability is crucial over a prolonged period of time in various environmental conditions, it is vital to ensure material performance. General Plastics’ LAST-A-FOAM® products demonstrate the ability to withstand the test of time.
Whether within an enclosed steel casing or exposed to the elements, LAST-A-FOAM® will not decay, rot, or lose mechanical properties, ensuring that for the life of the nuclear packaging application, transport and storage conditions are safely maintained.

This information has been sourced, reviewed and adapted from materials provided by General Plastics Manufacturing.
For more information on this source, please visit General Plastics Manufacturing.